车削实习心得202(精选8篇)由网友“罗密欧与猪过夜”投稿提供,以下是小编给大家整理的车削实习心得202,欢迎大家前来参阅。
篇1:车削实习心得
经过为期5个星期的实训,到今天终于结束了。在这期间,我们从一无所知的新手,到现在基本上能够熟知机床,利用机床加工出合格的零件并取得中级技工证。这过程虽然遇到些困难,但有着老师的耐心指导,我们很快就掌握了其中的道理,也真正的学到了知识。所以对于这次的实训,我们都有着乐在其中的感受,感到很高兴。 由于我们这个专业是两个班的,实训便分为上下午进行。而我们班就在下午进行实训。带我们的龙老师是一位负责而又有耐心,亲切又随和的人。在龙老师的教授指导下,我们开始了解了数控车床的组成,操作方法,注意事项及加工零件时的对刀、设置刀补、编辑程序等事项。上课的时候龙老师总是不厌其烦的向我们讲解重点,实际操作时也经常在一旁指导,使得我们每一个人都能够真正的学到技术。在此说一声:谢谢龙老师。
数控车床主要由数控程序及存储介质、输入输出设备、计算机数控装置(CNC装置)、伺服系统、机床本体组成。在操作车床进行加工时,首先要检查机床是否正常工作,检查刀具。按照习惯,常把外圆刀装夹在1号刀位,车断刀装夹在2号刀位,螺纹刀装夹在3号刀位,端面刀则装夹在4号刀位。除了看刀具是否安装正确外,还要注意检查刀具是否有磨损或者崩刀。检查好刀具之后便可以在控制面板上输入程序指令来加工了。控制面板上提供了程序指令的输入、修改,车床的手动、自动控制,主轴的正反转等一系列的强大功能。这些功能使得机床操作起来变得更加简单,同时也更有利于我们加工零件。
在加工完工件的时候,一定要注意打扫车床,这也就是机床的保养工作。虽然数控车床比普车先进,其所消耗的润滑油也大于普车的用量,工厂中使用的980Tb系列新型车床甚至是“泡在润滑油”当中的。但这却并不能说明数控车床就不需要像普通车床那样及时的打扫保养。恰恰相反,数控车床更加需要进行日常的保养工作。因为数车的稳定性和精确度是十分重要的,一旦因保养不当而引起机床的故障要维修起来就会很麻烦了。
介绍完了机床的特点及注意事项,接下来就到了工件的加工了。在进行加工前,老师着中向我们讲述了将会用到的各种程序指令,包括M98、M99、M03、G70、G71、G72、G73、G75、G76、G92、G94、G00、G01、G02、G03等一系列指令的用法。在980TDb车床中一般都是默认使用M98的,而主轴一般都是用M03 正转,G70、G71、G72、G73则是加工程序的粗、精加工指令了。G70配合G71、G72、G73使用,用于工件的精加工;而G71、G72、G73则是用来粗加工。其中G71、G72加工较快速而G73则相对比较慢,但G71、G72只能加工单调递增或递减的程序而G73却没这个限制,而且G71指令后只能有X方向增量、G72指令后只能有Z方向增量而G币73却可以同时又X、Z方向增量。G75主要用于槽的加工,不过为了槽的光滑一般在G75之后使用G94循环加工指令。至于G76和G92则是用来加工螺纹的指令,另外还有G00快速定位指令、G01直线插补指令、G02/03圆弧插补指令等。能否熟悉这些指令对于编程出正确的加工程序可谓是十分关键的,因此老师讲的也十分的详细,这让我们在后面的加工中受益匪浅。
编辑好程序之后还要进行一个步骤才能进行加工,那就是对刀,也就是定位X、Z坐标轴的原点。对刀时首先用端面刀将工件的端面车平,按下控制面板的录入——程序——程序状态,然后按T0400——输入——运行,这样就能把端面刀旋转过来,接着切换到手动控制,主轴正转,将端面刀移动到距离工件不远处,然后摇动手轮使刀具刀尖轻碰工件端面,注意这个过程一定要慢慢移动刀具,以免崩刀。在确保刀具碰到工件端面之后,将刀具沿X方向移动到安全位置,向Z负方向进一个毫米,然后车削工件端面。车平工件端面后就可以对1号外圆刀了。按照先前的方法,将T0400改为T0100转换1号刀,然后移动刀具刀尖轻碰工件端面,按下刀补——将光标移到1号刀位,按Z0——输入,这样就确定了外圆刀的Z原点坐标,接着车一段零件的外圆,停止主轴,用游标卡尺量出外圆大小,在刀补那里键入X的大小——输入,这样就对好了1号外圆刀。其它的刀具则也是以此方法来对刀,对好刀之后设置刀补就可以进行工件的加工了。
这一次的实训可以说过得很充实,学到了许多课堂上没有的知识,扩充了自己的视野,提高了自己的动手能力,了解了数车的加工方法及原理,这一切都让我们受益匪浅。同时也非常感谢指导我们的老师们,正是因为老师的耐心指导才让我们学到了这么多的知识,这对于今后的工作是十分有帮助的,因此真心的说一句:谢谢老师,老师辛苦了!
篇2:车削实习心得
首先,理论知识与安全教育是必不可少的,在正式开车床车削零件之前,老师就用了整整一天的时间来为我们上理论方面的知识,虽然感觉第一天过得很乏味,但恰恰却是最重要的内容之一。比如:装夹工件的时候一定要用加力棒拧紧,以免零件飞出发生事故以及刀具的正确使用等等。练习摇车床,只有熟练的摇动大拖板与中拖板,才能为车削零件作好必要的准备,以免刀具与零件发生碰撞。因为这次我们实习的车床与在职中的时候实习的车床有所不同,在自动进给时有差别,另外还有转速的调节上也有出入。在了解了车床的一些理论知识后,第二天,我们就开始正式加工零件了。
车削第一个零件的时候,感觉还是很紧张,每一步都是那么的小心翼翼,以免出错。大拖板一小格代表1mm,中拖板和小拖板0.02mm。车削外圆时,在离尺寸2mm的地方也要停止自动进给改为手动,防止车削过头,零件损坏。第一、二个零件车削整理让我们的是台阶轴,掌握的是外圆的控制以及游标卡尺的使用与读数。精车的时候,定要先试切削测量一下,看尺寸是否在范围之内,这样加工出来的零件准确率就比较高。
第三个零件加工的是锥度,需要转动一定的刻度盘,车削的时候先将大拖板摇到规定的刻度,再用中拖板对刀,然后小拖板退出,大拖板不动,最后调好刻度以后再用小拖板手动进给,车出锥度。首先需要试切削一下,用万能角尺测量,在保证角度正确的情况下继续对刀车削。如测量出来发现小端有缝隙,则说明角度调大,反之则小,需要重新调整度数再试。在加工锥度之前一定不能将零件拿下卡盘,否则车削出来的锥度与圆的同心轴有偏差,导致锥度的线条成曲线形状。
在实习中老师还教了我们数控车床的操作与加工工件程序的编写,例如教我们何操作数控机床建立坐标系,调节进刀量、快速移动刀具、换刀;加工工件编程教了我们G0快速定位、G1直线插补、G2逆时针圆弧、G3顺时针圆弧、G80循环内(外)径切削循环、G83螺纹车削、G84弧面车削。让我们在学习普车时也了解了数控的加工方法与操作。
在实训的过程中遇到了不少问题,而犯的错误也不少,通过实训让我学会虚心求教,细心体察,大胆实践。任何能力都是在实践中积累起来的,都会有一个从不会到会,从不熟练到熟练的过程,人常说“生活是最好的老师”就是说只有在生活实践中不断磨练,才能提高独立思考和解决问题的能力;同时也培养了自己优良的学风、高尚的人生、团结和合作的精神;学会了勤奋、求实的学习态度。
做事要脚踏实地,求真务实,谦虚谨慎、戒骄戒躁、对知识的掌握要弄通弄懂,对技术的掌握要严守规范、严谨细致、精益求精,不懂的地方要问懂。一个人的力量是有限的,团结合作的力量是无穷的,通过对各个项目的加工让我明白:一粒沙虽小,但无数粒却能汇成无限的沙漠;水滴虽小,却你汇成辽阔的海洋;你的一个思想、一个方法,他的一个思想和方法,相互交流互换就有了两个思想和方法,当今社会竞争日益激烈,而我们现在就应该学会与他人合作。
当然,在实训过程中,我们也收获了快乐、与同学的快乐、与老师的快乐。因为每当自己或自己和同学完成了一个项目时,或多或少有些欣慰,会感到开心,我们会彼此之间相互比较谁做的工件好谁做的不好。虽然两周时间的实训时间很短,但对我今后的车工技能有很大帮助。这只是起点,终点离我们还有一定的距离,所以还是需要我们继续努力去走以后的路。而我们要把握好每一次的机会,错过了就再也找不回来了。
篇3:数控车削加工工艺
摘要:数控车床的使用的目的是加工出合格的零件,但合格零件的加工必须要依靠制定合理的加工工艺。本文针对当前数控车床使用者的工艺分析的不合理来进行对比,讲述合理的工艺分析的顺序问题。
关键词:数控车床 车削加工工艺 工艺分析
一、问题的提出
数控车削加工主要包括工艺分析、程序编制、装刀、装工件、对刀、粗加工、半精加工、精加工。而数控车削的工艺分析是数控车削加工顺利完成的保障。
数控车削加工工艺是采用数控车床加工零件时所运用的方法和技术手段的总和。主要内容包括以下几个方面:
(一)选择确定零件的数控车削加工内容;(二)对零件图进行数控车削加工工艺分析;(三)工具、夹具的选择和调整设计;(四)切削用量选择;(五)工序、工步的设计;(六)加工轨迹的计算和优化;(七)编制数控加工工艺技术文件。
但是分析了上述的顺序之后,发现有点不妥。因为整个零件的工序、工步的设计是工艺分析这一环节中最重要的一部分内容。工序、工步的设计直接关系到能否加工出符合零件形位公差要求的零件。设计不合理将直接导致零件的形位公差达不到要求,导致产生次品。
二、分析问题
数控车床的`使用者的操作水平较高,能够独立解决很多操作难题,但理论水平不是很高,这是造成工艺分析顺序不合理的主要原因, 造成工艺分析顺序不合理的另一个原因是企业的工量具设备不足。
三、解决问题
笔者认为合理的工艺分析步骤应该是:
(一)选择并确定零件的数控车削加工内容;(二)对零件图纸进行数控车削加工工艺分析;(三)工序、工步的设计;(四)工具、夹具的选择和调整设计;(五)切削用量选择; (六)加工轨迹的计算和优化;(七)编制数控加工工艺技术文件。 本文主要对二、三、四、五三个步骤进行详细的阐述。
(一)零件图分析
零件图分析是制定数控车削工艺的首要任务。主要进行尺寸标注方法分析、轮廓几何要素分析以及精度和技术要求分析。此外还应分析零件结构和加工要求的合理性,选择工艺基准。
1.选择基准
零件图上的尺寸标注方法应适应数控车床的加工特点,以同一基准标注尺寸或直接给出坐标尺寸。这种标注方法既便于编程,又有利于设计基准、工艺基准、测量基准和编程原点的统一。
2.节点坐标计算
在手工编程时,要计算每个节点坐标。在自动编程时要对零件轮廓的所有几何元素进行定义。
3.精度和技术要求分析
对被加工零件的精度和技术进行分析,是零件工艺性分析的重要内容,只有在分析零件尺寸精度和表面粗糙度的基础上,才能正确合理地选择加工方法、装夹方式、刀具及切削用量等。
(二)工序、工步的设计
1.工序划分的原则
(1)保持精度原则。工序一般要求尽可能地集中,粗、精加工通常会在一次装夹中全部完成。 为减少热变形和切削力变形对工件的形状、位置精度、尺寸精度和表面粗糙度的影响,则应将粗、精加工分开进行。
(2)提高生产效率原则。为减少换刀次数,节省换刀时间,提高生产效率,应将需要用同一把刀加工的加工部位都完成后,再换另一把刀来加工其他部位,同时应尽量减少空行程。
2.确定加工顺序
(1)先粗后精。按照粗车半精车精车的顺序进行,逐步提高加工精度。
(2)先近后远。离对刀点近的部位先加工,离对刀点远的部位后加工,以便缩短刀具移动距离,减少空行程时间。
(3)内外交叉。对既有内表面又有外表面需加工的零件,应先进行内外表面的粗加工,后进行内外表面的精加工。
(4)基面先行。作精基准的表面应优先加工出来,定位基准的表面越精确,装夹误差越小。
(三)夹具和刀具的选择
1.工件的装夹与定位
数控车削加工中尽可能一次装夹后能加工出全部或大部分代加工表面,尽量减少装夹次数,以保证加工精度。对于轴类零件,通常以零件自身的外圆柱面作定位基准;对于套类零件,则以内孔为定位基准。数控车床夹具除了使用通用的三爪自动定心卡盘、四爪卡盘、液压、电动及气动夹具外,还有多种通用性较好的专用夹具。操作时应合理选择 。
2.刀具选择
刀具的使用寿命除与刀具材料相关外,还与刀具的直径有很大的关系。刀具直径越大,能承受的切削用量也越大。所以在零件形状允许的情况下,采用尽可能大的刀具直径是延长刀具寿命,提高生产率的有效措施。数控车削常用的刀具一般分为3类。即尖形车刀、圆弧形车刀和成型车刀。
(四)切削用量选择
数控车削加工中的切削用量包括背吃刀量ap、主轴转速S(或切削速度υ)及进给速度F(或进给量f )。
切削用量的选择原则,合理选用切削用量对提高数控车床的加工质量至关重要。确定数控车床的切削用量时一定要根据机床说明书中规定的要求,以及刀具的耐用度去选择,也可结合实际经验采用类比法来确定。
一般的选择原则是:粗车时,首先考虑在机床刚度允许的情况下选择尽可能大的背吃刀量ap;其次选择较大的进给量f;最后再根据刀具允许的寿命确定一个合适的切削速度υ。增大背吃刀量可减少走刀次数,提高加工效率,增大进给量有利于断屑。
精车时,应着重考虑如何保证加工质量,并在此基础上尽量提高加工效率,因此宜选用较小的背吃刀量和进给量,尽可能地提高加工速度。主轴转速S(r/min )可根据切削速度υ(mm/min)由公式 S=υ1000/πD(D为工件或刀/具直径 mm)计算得出,也可以查表或根据实践经验确定。
三、结 语
数控机床作为一种高效率的设备,欲充分发挥其高性能、高精度和高自动化的特点,除了必须掌握机床的性能、特点及操作方法外,还应在编程前进行详细的工艺分析和确定合理的加工工艺,以得到最优的加工方案。
参考文献:
[1]《数控车削加工工艺性分析》.周鹏.《消费导刊·理论版》 第1期
篇4:车削加工通用工艺守则
一、前言
本守则规定了磨削加工应遵守的基本规则,适用于本企业的磨削加工。除另有相关特殊规定外,操作者必须严格执行本守则。
二、操作规则
1 加工前的准备
1.1 操作者必须首先检查加工所需的产品图样、工艺规程和有关技术资料是否齐全。
1.2 操作者要看懂看清工艺规程、产品图样及其技术要求,并按产品图样或(和)工艺规程复核工件毛坯或半成品是否符合要求,发现问题或有疑向应及时向有关人员反映,待问题解决后才能进行加工。
1.3 按工艺规程要求准备好加工所需的全部工艺装备,要熟悉其使用要求和操作方法,发现问题及时处理。
1.4 加工所用的工艺装备必须放在规定位置,不得乱放,更不准随意拆卸和更改。
1.5 检查加工所用的机床设备,准备好所需的各种附件。加工前机床要按规定进行润滑和空运转。
2 刀具的装夹
2.1 装夹刀具前应按不同类型刀具的安装特点将装夹表面擦试干净。
2.2 刀具装夹后要稳固可靠。
2.3 车刀刀杆伸出力架长度一般不应超过刀杆高度的1.5倍(车孔、槽等除外)。
2.4 车刀刀杆中心线应与走刀方向垂直或平行。
2.5 螺纹车刀刀尖的平分线应与工件的中心线垂直,
2.6 刀具装夹后,应用对刀装置或试切等检查其正确性。
2.7 车刀刀尖高度的调整
2.7.1 在车端面、车园锥面、车螺纹、成形车削、切断实心工件时,刀尖一般与工件中心线等高。
2.7.2 在粗车外园、精车孔时刀尖一般应比工件中心线稍高。
2.7.3 在粗车孔、精车细长轴、切断空心工件时,刀尖一般应比工件中心线稍低。
3 工件的'装夹
3.1 用三爪卡盘装夹工件进行粗车或精车时,若工件直径小于或等于30mm,其悬伸长度应不大于直径5倍,若工件直径大于30mm,其悬伸长度应不大于直径3倍。
3.2 用四爪卡盘、花盘、角铁(弯板)等装夹不规则偏重工件时,必须加配重。
3.3 在顶尖间加工轴类工件时,车削前要调整尾座顶尖中心与车床主轴中心线重合。
3.4 在顶尖间加工细长轴时,当使用中心架或跟刀架,要调整顶尖的顶紧力。死顶尖和中心架应注意润滑和调整顶紧力。
3.5 使用尾座时,套筒尽量伸出短些,以减少振动。
3.6 在机床工作台上安装夹具时,首先要擦净其定位基面,并要找正其与刀具的相对位置。
3.7 工件装夹前应将其定位面、夹紧面、垫铁和夹具的定位夹紧面擦试干净,并不得有毛刺。
3.8 工件装夹时,按工艺规程中规定的定位基准装夹,若未规定装夹方式,操作者可自选定位基准和装夹方法,选择定位基准应按以下原则。
3.8.1 尽可能使定位基准与设计基准重合。
3.8.2 尽可能使各加工面采用同一基准。
3.8.3 粗加工定位基准应尽量选择不加工或加工余量比较小的平整表面,而且只能使用一次。
3.8.4 精加工工序定位基准应是已加工表面。
3.8.5 选择的定位基准必须使工件定位夹紧方便,加工时稳定可靠。
3.9 对无专用夹具的工件,装夹时应按以下原则进行找正。
3.9.1 对划线工件按划线找正。
3.9.2 对不划线工件,在本工序后需继续加工的表面,找正精度应保证下工序有足够的加工余量。
3.9.3 对在本工序加工到成品尺寸并注有尺寸公差和位置公差的表面,其找正精度应小于其标注公差的三分之一。
3.9.4 对在本工序加工到成品尺寸的未注尺寸公差和位置公差的表面,其找正精度按ZBJ38001规定找正。
3.10 车削轮类、套类铸锻件时,应按不加工的表面找正,以保证加工后壁厚均匀。
3.11 装夹组合件时应注意检查结合面的定位情况。
3.12 夹紧工件时,夹紧力的作用点应通过支承点或支承面。对刚性较差的(或加工时有悬空部分的)工件,应在适当的位置增加辅助支承。
3.13 在立车上装夹支在面小,高度高的工件时,应使用加高卡爪,并在适当的部位加拉杆或压板压紧工件。
3.14 用压板压紧工件时,压板支承点应略高于被压工件表面,压紧螺栓应尽量靠近工件。
3.15 夹持精加工表面和软材质工件时,应垫以紫铜皮等软垫。
篇5:车削加工通用工艺守则
4.1 根据工件材料、精度要求和机床、刀具、夹具等情况,合理选择切削用量。
4.2 在轴类工件上切槽时,应在精车之前进行,以防止工件变形。
4.3 粗车带螺纹的轴时,一般应在螺纹加工之后,再精车无螺纹部分。
4.4 车削台阶轴时,为保证车削的刚性,一般应先车直径较大的部分,后车直径较小的部分。
4.5 钻孔前应先车平工件端面。必要时可先打中心孔。钻深孔时,一般先钻导向孔。
4.6 对有公差要求的尺寸应尽量按其中间公差加工。
4.7 工艺规程中未规定表面粗糙度要求的粗加工工序,加工后的表面粗糙度Ra值应不大于 0.025 mm。
4.8 铰孔前的表面粗糙度Ra值应不大于0.0125 mm。
4.9 凡下工序需进行表面淬火,超声波探伤或滚压加工的工件表面,在本工序加工的表面粗糙度Ra值应不大地0.0063 mm。
4.10 在本工序后为无法去毛刺的工序时,本工序加工所产生的毛刺在本工序去除。
4.11 车削φ10~φ20mm的孔时,刀杆直径应为被加工孔径的0.6~0.7倍;车削大于φ20mm的孔时,一般应采用装夹刀头的刀杆。
挂轮后要进行试切。
4.13 4.13 使用自动车床时,要按机床调整卡片进行刀具与工件相对位置的调整,调好后要进行试切,首件合格后方可加工;加工过程中要随时注意刀具的磨损及工件尺与表面粗糙度。
4.14 在立车上车削时,当刀架调整好后,不得随意移动横梁。
4.15 当工件的有关表面有位置公差要求时,尽量在一次装夹中完成车削。
4.16 车削圆柱齿轮齿坯时,孔与基准端面必须在一次装夹中加工。必要时应在该端面的齿轮分度圆附近车出标记线。
4.17 在大件的加工过程中应经常检查工件是否松动,以防影响加工质量或发生意外事故。
4.18 当粗、精加工在同一台机床上进行时,粗加工后一般应松开工件,待其冷却后重新装夹。
4.19 在切削过程中,若机床━━刀具━━工件系统发出不正常声音或加工表面粗糙度突然变坏,应立即退刀停车检查。
4.20 粗加工时的倒圆、倒角、槽深等都应按精加工余量加大或加深,以保证精加工后达到设计要求。
4.21 图样和工艺规程中未规定的倒角、倒圆、尺寸和公差要求应按ZBJ38001的规定。
4.22 在批量生产中,必须进行首件检查,合格后才能继续加工。
4.23 加工过程中,操作者必须对工件进行自检。
4.24 操作者应正确使用测量器具,用时先调零位,使用动作要轻。
4.25 粗加工后的配合面、摩擦面和定位面等工作表面不允许在其上打印标记。
5 加工后的处理
5.1 工件在本工序完成后,应做到无屑、无水、无脏物,并在规定的工位器具上摆放整齐。
5.2 暂不进行下道工序加工的或精加工后的表面应进行防锈处理。
5.3 凡配对加工的零件,加工后需做标记(或编号)。
5.4 本工序加工完的工件应经专职检查员检查合格后方能转往下道工序。
6 其它要求
6.1 工艺装备用完后要擦拭干净,涂好防锈油,放到规定位置或交还工具库。
6.2 产品图样、工艺规程和所使用的其它技术文件要保持整洁,严禁涂改。
篇6:UGNC6.0车削加工实例
1. 打开模型文件14,
2. 初始化加工环境。选择【开始】→【加工】进入初始化加工环境,系统弹出【加工环境】对话框,选择turning单击初始化,进入加工环境。结果如下图所示:3. 创建中心孔刀,单击菜单栏中的按钮,系统弹出【创建刀具】对话框,刀具子类型选择【DRILLING_TOOL】创建D15的钻头,单击确定更改直径值为15,单击确定完成这把刀的创建。4. 选择菜单栏【工具】下拉菜单中的【车加工横截面】,系统弹出【车加工横截面】对话框,单击部件,再单击按钮其它数值采用默认,单击确定,结果如下图所示:5.双击操作导航器中采用默认,单击确定,双击,单击按钮,选择如下图所示的轮廓线,单击确定,再单击按钮,系统弹出【毛坯几何体】对话框,单击选择,选择原点为毛坯点位置,在长度和直径文本框中分别输入205、105单击确定,结果如下图所示:6.单击按钮,系统弹出创建操作对话框,选择类型为【CENTERLINE_SPOTDRILL】,四个父结点组如下图所示:7.在上一步弹出的对话框中设置参数,【循环】选择钻,深、进刀距离文本框中输入2、恒定增量文本框输入2、入口直径为15、深度选择端点,指定如下图所示的终点,驻留时间为2秒,单击显示起点和终点,结果如下图所示:8.单击按钮,生成刀轨,结果如下图所示:9.单击菜单栏中的按钮,系统弹出【创建刀具】对话框,刀具子类型选择【OD_80_L】,单击确定,在刀尖半径和方向角度文本框中分别输入0.3、5。结果如下图所示:10.单击按钮,系统弹出创建操作对话框,选择类型为【ROUGH_TURN_OD】,四个父结点组如下图所示:11.单击切削区域后按钮,系统弹出【切削区域】对话框,径向修剪平面1中的限制选项选择距离,轴向修剪平面1中的限制选项也选择距离,其它参数设置如下图,结果如下图所示:12.单击按钮,生成刀轨,结果如下图所示:
13.单击菜单栏中的按钮,系统弹出【创建刀具】对话框,刀具子类型选择【OD_55_L】,单击确定,在刀尖半径和方向角度文本框中分别输入0.2、18。结果如下图所示:14.单击按钮,系统弹出创建操作对话框,选择类型为【FINISH_TURN_OD】,四个父结点组如下图所示:1. 打开模型文件14。
2. 初始化加工环境。选择【开始】→【加工】进入初始化加工环境,系统弹出【加工环境】对话框,选择turning单击初始化,进入加工环境。结果如下图所示:3. 创建中心孔刀,单击菜单栏中的按钮,系统弹出【创建刀具】对话框,刀具子类型选择【DRILLING_TOOL】创建D15的钻头,单击确定更改直径值为15,单击确定完成这把刀的创建。4. 选择菜单栏【工具】下拉菜单中的【车加工横截面】,系统弹出【车加工横截面】对话框,单击部件,再单击按钮其它数值采用默认,单击确定,结果如下图所示:5.双击操作导航器中采用默认,单击确定,双击,单击按钮,选择如下图所示的轮廓线,单击确定,再单击按钮,系统弹出【毛坯几何体】对话框,单击选择,选择原点为毛坯点位置,在长度和直径文本框中分别输入205、105单击确定,结果如下图所示:6.单击按钮,系统弹出创建操作对话框,选择类型为【CENTERLINE_SPOTDRILL】,四个父结点组如下图所示:7.在上一步弹出的对话框中设置参数,【循环】选择钻,深、进刀距离文本框中输入2、恒定增量文本框输入2、入口直径为15、深度选择端点,指定如下图所示的终点,驻留时间为2秒,单击显示起点和终点,结果如下图所示:8.单击按钮,生成刀轨,结果如下图所示:9.单击菜单栏中的按钮,系统弹出【创建刀具】对话框,刀具子类型选择【OD_80_L】,单击确定,在刀尖半径和方向角度文本框中分别输入0.3、5,结果如下图所示:10.单击按钮,系统弹出创建操作对话框,选择类型为【ROUGH_TURN_OD】,四个父结点组如下图所示:11.单击切削区域后按钮,系统弹出【切削区域】对话框,径向修剪平面1中的限制选项选择距离,轴向修剪平面1中的限制选项也选择距离,其它参数设置如下图,结果如下图所示:12.单击按钮,生成刀轨,结果如下图所示:
13.单击菜单栏中的按钮,系统弹出【创建刀具】对话框,刀具子类型选择【OD_55_L】,单击确定,在刀尖半径和方向角度文本框中分别输入0.2、18。结果如下图所示:14.单击按钮,系统弹出创建操作对话框,选择类型为【FINISH_TURN_OD】,四个父结点组如下图所示:15.单击切削区域后按钮,系统弹出【切削区域】对话框,径向修剪平面1中的限制选项选择距离,轴向修剪平面1中的限制选项也选择距离,其它参数设置如下图,结果如下图所示:16.单击按钮,生成刀轨,结果如下图所示:
17.单击菜单栏中的按钮,系统弹出【创建刀具】对话框,刀具子类型选择【OD_GROOVE_L】,单击确定,在刀片宽度文本框中分别输入4。结果如下图所示:18. 单击按钮,系统弹出创建操作对话框,选择类型为【GROOVE_OD】,四个父结点组如下图所示:
19.单击切削区域后按钮,系统弹出【切削区域】对话框,径向修剪平面1中的限制选项选择距离,轴向修剪平面1中的限制选项也选择距离,轴向修剪平面2中的限制选项选择点,选择槽的右端面点,其它参数设置如下图,结果如下图所示:20.单击按钮,生成刀轨,结果如下图所示:21.单击按钮,系统弹出创建操作对话框,选择类型为【FACING】,四个父结点组如下图所示:22.单击切削区域后按钮,系统弹出【切削区域】对话框,径向修剪平面1中的限制选项选择距离,轴向修剪平面1中的限制选项也选择距离,其它参数设置如下图,结果如下图所示:23.单击按钮,生成刀轨,结果如下图所示:24.单击菜单栏中的按钮,系统弹出【创建刀具】对话框,刀具子类型选择【OD_THREAD_L】,单击确定,结果如下图所示:25.单击按钮,系统弹出创建操作对话框,选择类型为,四个父结点组如下图所示:26.单击【select crest line】后的按钮,随便选择螺纹的上表面线作为顶线,再单击【select end line】后的按钮,选择螺纹的右端面,即可确定螺纹的形状,单击选择根线后面的按钮,选择根线,即螺纹的底线,起始偏置的文本框中输入相应的数值,其它参数的设置如下图所示:27.单击按钮,生成刀轨,结果如下图所示:篇7:细长轴数控车削方法
细长轴数控车削方法
在数控加工中,车细长轴工件是一种难度较大的加工工艺。
但该工作也有一定的规律性,存在三个关键技术,即中心架和跟刀架的使用、解决工件热变形伸长以及如何合理选择车刀几何形状等方面,下面以一个实际工件为长800mm直径40mm的细长轴,在中心架和跟刀架的辅助的前提下,来对细长轴进行合理的阐述加工。
一、零件图的分析
该工件表面由内外椭圆面、内孔及内外螺纹等表面组成,其中多个直径尺寸与轴向尺寸有较高的尺寸精度和表面粗糙度要求。
零件图尺寸标柱完整,符合数控加工尺寸标柱要求;轮廓描述清楚完整;零件材料为45钢,切削加工性能较好,无热处理和硬度要求。
1、结构工艺性分析
零件的公艺性是指零件对加工方法的适应性,即所设计的零件结构便于加工成型。
在数控车床上加工零件时,应该根据数控车削的特点,认真审视零件结构的合理性。
本次研究课题就应该使用多把车刀,以及其它辅助装置来完成零件的车削加工。
2、尺寸标注方法分析
零件图上尺寸标注方法应适应车床加工的特点。
本零件图的尺寸标注能够直观的分析出各部分的尺寸,尺寸标注没有不合理的部分。
3、精度及技术要求分析
对被加工零件的精度及技术要求进行分析,是零件工艺分析的重要内容,只有在分析零件尺寸精度和表面粗糙度的基础上,才能正确合理地选择加工方法、装夹方式、刀具及切削用量等。
精度及技术要求分析的主要内容如下:
(1)分析精度及各项技术要求是否齐全、是否合理。
(2)分析本工序的数控车削加工精度能否达到图样要求,若答不到,需要采取其它措施弥补时,则应给后续工序留有余量。
(3)找出图样上有位置精度要求的表面,这些表面应在一次安装下完成。
(4)对表面粗糙度要求较高的表面,应确定用恒线速度切削。
4、轮廓几何要素分析
在分析零件图时,要分析几何要素的给定条件是否充分。
本零件图几何要素充分,圆弧与圆弧相切,内外螺纹紧密配合,总长度等于各段长度,符合轮廓几何要素要求。
二、车削过程要注意的问题:
1、工件受切削力、自重和旋转时离心力的作用,会产生弯曲、振动,严重影响其圆柱度和表面粗糙度。
2、在切削过程中,工件受热伸长产生弯曲变形,;车削就很难进行,严重时会使工件在支持尖间卡住。
因此,车细长轴是一种难度较大的加工工艺。
虽然车细长轴的难度较大,但它也有一定的规律性,主要抓住中心架和跟刀架的使用、解决工件热变形伸长以及合理选择车刀几何形状等三个关键技术,问题就迎刃而解了。
三、中心架支撑细轴使用过程:
在车削细长轴时,可使用中心架来增加工件刚性。
一般车削细长轴使用中心架的方法有:1、中心架直接支承在工件中间 当工件可以分段车削时,中心架支承在工件中间,这样支承,L/d值减少了一半,细长轴车削时的刚性可增加好几倍。
在工件装上中心架之前,必须在毛坯中部车出一段支承中心架支承爪的沟槽,表面粗糙度及圆柱度误差要小,否则会影响工件的精度。
车削时,中心架的支承爪与工件接触处应经常加润滑油。
为了使支承爪与工件保持良好的接触,也可以在中心架支承爪与工件之间加一层砂布或研磨剂,进行研磨抱合。
2、用过渡套筒支承车细长轴用上述方法车削支承承中心架的沟槽是比较困难的。
为了解决这个问题,可加用过渡套筒的处表面接触,过渡套筒的'两端各装有四个螺钉,用这些螺钉夹住毛坯工件,并调整套筒外圆的轴线与主轴旋转轴线相重合,即可车削。
四、使用跟刀架支撑细长轴的方法:
跟刀架固定在床鞍上,一般有两个支承爪,跟刀架可以跟随车刀移动,抵消径向切削时可以增加工件的刚度,减少变形。
从而提高细长轴的形状精度和减小表面粗糙度。
从跟刀架的设计原理来看,只需两只支承爪就可以了,因车刀给工件的切削抗力F`r,使工件贴住在跟刀架的两个支承爪上。
但是实际使用时,工件本身有一个向下重力,以及工件不可避免的弯曲,因此,当车削时,工件往往因离心力瞬时离开支承爪、接触支承爪而产生振动。
如果采用三只支承爪的跟刀架支承工件一面由车刀抵住,使工件上下、左右都不能移动,车削时稳定,不易产生振动。
因此车细找轴时一个非常关键的问题是要应用三个爪跟刀架。
五、车削细长轴的车刀的选择:
1、刀片材料为YT15硬质合金。
2、切削用量:粗车时,切削速度vc=50~60m/min;进给量f=0..3~0.4mm/r;切削深度ap=1.5~2mm。
精车时,切削速度vc=60~100m/min;进给量 f=0.08~0.12mm/r ;切削深度ap=0.5~1mm.。
3、采用乳化液作切削液。
4、适用范围:适用于车削光杠、丝杆等细长轴。
六、合理选择车刀的几何形状:
车削细长轴时,由于工件刚性差,车刀的几何形状对工件的振动有明显的影响。
选择时主要考虑以下几点:
1、由于细长轴刚生差,为减少细长轴弯曲,要求径向切削力越小越好,而刀具的主偏角是影响径向切削力的主要因素,在不影响刀具强度情况下,应尽量增大车刀主偏角。
车刀的主偏角取kr=80°~93°。
2、为减少切削烟力和切削热,应该选择较大的前角,取r0=15°~30°。
3、车刀前面应该磨有R11.5~3的断屑槽,使切削顺利卷曲折断。
4、选择正刃倾角,取入=3°使切削屑流向待加工表面,并使卷屑效果良好。
5、切削刃表面粗糙度要求在Ra0.4以下,并要经常保持锋利。
6、为了减少径向切削力,应选择较小的刀尖圆弧半径(re<0.3mm)。
倒棱的宽度也应选得较小,取倒棱宽br1=0.5f。
篇8:数控加工中车削工艺
数控加工中车削工艺
【摘 要】数控机床的加工工艺与普通机床的加工艺虽有诸多相同之处,但也有许多不同之处。
为此,分析了数控车削的加工工艺。
数控机床产生20世纪40年代,随着科学技术和社会生产的发展,机械产品的形状和结构不断改进,对零件的加工质量要求越来越高,零件的形状越来越复杂,传统的机械加工方法已无法达到零件加工的要求,迫切需要新的加工方法。
数控车床又称为CNC(computer numerical control)车床,即用计算机数字控制的车床,是国内使用量最大、覆盖面最广的一种数控机床。
CNC车床能加工各种形状不同的轴类、盘类即其它回转体零件。
【关键词】数控车床;车削加工;工艺分析
0.前言
数控机床作为一种使用广泛、典型的机电一体化产品,综合应用了微电子技术、计算机技术、自动控制、精密测量和机床结构等方面的最新成就,是一种高效的自动化机床。
随着科学技术的不断发展,迄今,国际上又出现了以一台或多台加工中心、车削中心为主体,再配以工件自动装卸和监控检查装置的柔韧性制造系统FMS、计算机集成制造系统CIMS和无人化工厂FA。
由于数控机床极高效率、高精度和高柔韧性于一身,很好的代表了机床的主要发展方向。
时代和社会生产力的不断发展,要求数控系统与数控机床向更高的水平与层次迈进(高精度化、运动高速化、高柔韧性化、智能化)。
1.零件图纸分析
1.1零件的特征
拿到图纸首先了解零件的材料;然后从图纸中看出该零件轮廓是由哪些部分构成的,最后分析这些部分包括哪些加工。
1.2数值计算
生活中,我们对几何信息的认知有多种方法,常用的有数形结合法(解析法)。
但有时面对复杂的图形,解析法会带来繁重的数学计算。
CAD作为一套专业的绘图软件,它强大的信息处理功能为图形中繁杂点的计算带来了可能。
我们在操作界面中绘制图形后就可以打开状态栏中的捕捉、对象捕捉按钮,在绘图区捕捉相关的点。
同时,在状态栏中就可以看到这些点的坐标。
2.工件定位与装夹的分析
2.1加工精度要求
明确加工图纸上数值所示的加工精度要求。
2.2定位基准的选择
定位基准选择原则有以下4种:
(1)基准重合原则(2)基准统一原则(3)便于装夹原则(4)便于对刀原则。
根据定位基准选择原则,避免不重合误差,便于编程,以工序的设计基准作为定位基准。
2.3装夹方式
夹具的作用是保证工件在机床上的正确位置和牢固的安装,即定位和夹紧,从而使数控加工顺序进行,保证工件的位置精度,同时也保证工件坐标系能够建立在正确的位置上。
车削加工的工件一般是回转体,对于回转体零件,一般选择三爪自定心卡盘。
2.4工艺过程制定
由于每个零件结构形状不同,各表面的技术要求也有所不同,故加工时,其定位方式则各有差异。
一般加工外形时,以内形定位;加工内形时又以外形定位。
因而可根据定位方式的不同来划分工序。
3.切削用量分析
3.1切削用量
切削用量包括切削速度,背吃刀量和进给量.对于不同的加工方法需要选择不同的切削用量。
粗加工时一般以加工效率为主通常选择较大的背吃刀量和进给量,采用较小的切削速度 。
精加工时通常选择较小的背吃刀量和进给量采用较高的切削速度。
3.2主轴转速的确定
主轴的转速是由切削刃上选定点相对于工件的`主运动的线速度。
主运动速度:n=1000Vc/πd 单位为r/min
4.数控车床对刀分析
4.1刀位点
在进行数控加工的编程时,往往将整个刀具浓缩视为一个点,那就是刀位点,它是在刀具上用于表现刀具位置的参照点。
对刀操作就是要测定出程序起点处刀具刀位点相对机床原点以及工件原点的坐标位置。
在对刀时,常用的仪器有:对刀测头、千分表或对刀瞄准仪等。
对刀点可以设置在零件、夹具上或机床上面(尽可能设置在零件的设计基准或工艺基准上)。
4.2 待加工毛坯的对刀
试切端面:将两端面已经加工好的待加工毛坯装夹到主轴上,在工件的伸出端安装Z 轴向设定器。
快移刀具接近到Z 轴向设定器,改用增量方式控制刀具工进,至到指示灯亮时停止动作,保持 Z轴 向不动,取出轴向设定器。
然后在机床操作面板上调出刀具补偿菜单栏中刀偏表,在相关的试切长度填空栏中键入有关数值(当前刀具刀位点相对于程序原点的距离)。
试切外圆:快速将刀具刀位点移动刀毛坯端面角附近,然后用增量方式调节X、Z 轴向进给至刀位点刚好切到毛坯外表面,再用MDI方式运行进行外圆车削。
同时保持X轴轴向坐标不变,退出刀具。
用游标卡尺测量出试切外圆直径。
然后在刀偏表中键入试切直径。
4.3刀偏值的测定
刀偏值就是各刀具相对于基准刀具的几何补偿。
用点动或步进方式操作移动刀具,使基准刀具刀位点对准工件的基准点,然后进行X轴 Z轴坐标清零,退刀。
换置刀具,再用点动或步进方式使该刀具刀位点对准工件上的同以一基准点,此时屏幕上显示的坐标既是该刀号刀具的几何偏置△Xj,△Zj。
同理,可依次测定出其它刀具相对于基准刀具的几何偏置。
在相应的刀偏表中依次键入选用刀具刀位点的几何补偿。
5.总结
近年来,在国外的数控系统与伺服系统制造技术突飞猛进的大背景下,通过大量的技术引进,我国现代制造工业在飞速发展(数控技术得到广泛的应用)。
同时,我们还要看清现阶段中国数控业与世界先进水平的差距。
我国只有拥有完全自主知识产权上的数控核心技术,才能实现真正意义上的“世界工厂”和“制造大国”乃至“工业强国”。
这使国人不得不开始重新思索中国数控在未来的发展之路。
【参考文献】
[1]赵长明.数控加工工艺及设备.北京:高等教育出版社.2003.
[2]夏凤芳.数控机床.北京:高等教育出版社.2005.
[3]袁哲俊.金属切削刀具.上海:上海科学技术出版社.1993.
[4]蔡兰,王霄.数控加工工艺学.化学工业出版社.2005.
[5]王爱玲.数控机床加工工艺.北京:机械工业出版社.2006.
[6]刘靖华.数控加工技术.高等教育出版社.2003.
[7]徐宏海.数控加工工艺.化学工业出版社.2004.
★ 车工实习报告
★ 普车工实习报告
★ 车工的实习报告
★ 车工实习心得体会
★ 车工实训心得体会
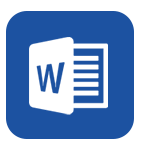
【车削实习心得202(精选8篇)】相关文章:
车工实习报告总结汇报2023-09-01
金工实习心得体会2022-10-13
金工实习心得体会精选2024-03-15
关于金工实习心得1000字2023-05-13
车工专业学生金工个人实习总结2023-04-30
金工实习制作小铁锤心得体会2022-08-18
金工实习心得体会一周2022-09-19
车工实习报告2024-05-16
工程训练实习总结2022-11-08
金工实习报告车工2022-12-17