UG等高切削在模具上的应用(精选10篇)由网友“北师大”投稿提供,下面是小编收集整理的UG等高切削在模具上的应用,供大家参考借鉴,希望可以帮助到有需要的朋友。
篇1:UG等高切削在模具上的应用
模具是目前应用CAD/CAM最普遍和最先进的行业之一,在模具加工中,为了使数据能够在数控加工机床上应用,必然要用到CAM编程。目前比较流行的CAM软件有UG,Cimatron,MasterCAM,DELCAM powerMILL,EDGECAM,HZS space-E等。
在UG的发展过程中,CAM一直是加工业者最可靠的工作伙伴。它不仅提供可靠、精确的刀具路径,更让NC程序设计师可以随心所欲地设计出心目中最有效的加工程序。CIMdata的调查报告指出,EDS UG被视为所有CAM软体供应商中最强大的竞争者。
UG CAM有下列几个特点:
(1)提供可靠、精确的刀具路径。
(2)能直接在曲面及实体上加工。
(3)良好的使用者界面,允许使用者能依工作上的需要,定制使用者界面,不仅能提高作业效率,同时能有效使用及保存公司的Know-How。
(4)提供多样性的加工方式,方便NC程序设计师设计各种高效率的刀具路径。
(5)提供完整的刀具库及加工参数库管理功能,使新进人员能充分利用资深人员的经验,设计优良的刀具路径。
(6)提供泛用型后处理功能,产生各NC加工机床适用的NC程式。
UG CAM包含二轴到五轴铣削、线切割、大型刀具库管理、实体模拟切削及泛用型后处理器等功能。本文将介绍三轴铣削中等高切削在模具加工上的应用。
等高切削
等高切削在模具加工上,主要用于需要刀具受力均匀的加工条件下。应用等高切削可以完成数控加工中80%的工作量。例如粗加工时,一般刀具受力极大,因此等高切削能以控制切深的方式,将刀具受力限制在一个范围内。此外,在中加工或精加工时,如果加工部位太陡、太深、需要延长加长刀刃的情形,由于刀具太长,加工时偏摆太大,往往也需要用等高切削的方式来减少刀具受力。目前最流行的高速切削机床,也是等高切削的使用者。
UG的等高切削功能不仅提供多样化的加工方式,同时允许刀具在整个加工过程中能在均匀的受力状态下实现最快、最好的切削。以下是UG等高切削的特性。
(1)刀具使用没有限制
NC程序设计师可以依照加工机床的性能、毛坯材质、夹持方式以及对切削效率的考虑,自由选用平刀、球刀、圆鼻刀、T型刀等刀具进行等高切削,
在计算上,UG利用所选用的刀具,分层沿等加工面计算,所以能产生准确的刀具路径。
(2)自动探测undercut区域
UG能自动探测加工范围内的undercut区域,并自动计算出最佳的刀具路径。用T型刀铣切时,若刀柄与加工面不发生干涉,UG尽可能作最完整的切削。由于用平刀切削,因此在undercut区域,UG产生的刀具路径以刀具不碰到加工面为原则。
(3)提供多样化的刀具路径型式
UG等高切削提供住复式切削、单向切削、螺旋切削、沿边切削及多层沿边切削。其中多层沿边切削可提供高效率的粗毛坯加工路径,也是深陡加工面精加工的良好选择。高速切削机床可利用此功能生成良好的加工路径。多层沿边切削的刀具路径的每一深度上产生3道刀具路径,第一道离成品面3mm,第二道离成品面1mm,第三道则加工在成品面上。
(4)产生刀具受力均匀的加工路径
模具加工时,NC程序设计师或机床操作员往往为了避免NC程序中刀具局部受力过大而造成刀具严重损耗的情形,不得不降低整体路径的进给速率,从而影响了整个加工效率。UG提供多样的进给速率设定方式来解决这个问题。使用者可以设定刀具局部受力的进给率(如第一刀切削,刀具路径往复时刀具路径转角时)。
(5)在不同高度区域设定不同切削深度
为了在加工后能留下均匀的毛坯,同时又不耗费不必要的加工时间,UG可提供使用者按加工工件的形状特性,在不同的高度区域中设定不同的切削深度。在完成多层沿面中加工时,在陡峭区域可设定较大的切削深度,在平缓区域设定较小切削深度。
(6)具有加工素材及成品体的观念
加工素材及成品体的运作,让使用者在不修改CAD模型的情形下,能便利地进行等高粗加工及精加工的计算。对于模具电极及滑块的NC程序制作非常方便。
(7)具有允差切削功能
模具业者所接收的CAD资料,经常是上游所提供的IGES档案。因此加工用的CAD模型的曲面之间常会有间隙及重叠的情形。UG提供允差切削功能,在使用者设定的公差范围内能自动处理曲面间的间隙及重叠,从而产生良好的刀具路径。
(8)在个别加工曲面上,可以设定不同的加工预留量
在模具设计中,由于成品几何形状的规范,往往需要定义不同的壁厚、合模面、靠破面及一般成品面。为了方便NC程序设计师在单一CAD模型上设定NC程序,UG让NC设计师在个别加工曲面上设定不同的预留量(正值及负值),以提高NC程式的设计效率。
(9)提供多种进/退刀方式
UG等高切削提供直线、折线、圆弧等多种进/退刀方式,来满足实际加工的需要。使用者同时能在不同深度区域或加工区域设定不同的预钻孔位置及钻孔深度。UG在进刀时亦能依加工几何形状及刀具定义,自动决定由预钻孔进刀或斜向进刀,以符合实际加工要求。(
篇2:UG CAD/CAM在模具中应用的研究
UG CAD/CAM在模具中应用的研究
介绍了UG软件的CAD/CAM功能.以一瓶体为研究对象,通过UG CAD对其进行造型设计,进而设计出加工该瓶体的模具;然后将高速切削应用于模具加工中,分析了模具加工方式以及加工参数,使用UG CAM对整个制造过程进行设计仿真,并通过后置处理输出NC(数控)代码.最后通过VERICUT仿真软件证实了CAM的有效性.
作 者:苏建民 Su Jianmin 作者单位:潍坊科技学院,山东,寿光,262700 刊 名:铸造工程 英文刊名:FOUNDRY ENGINEERING 年,卷(期): 33(2) 分类号:P391.7 关键词:模具 计算机辅助设计/制造 高速切削篇3:UG在模具设计中的应用
UG在级进模设计中的应用,模具设计(Mold Design and Manufacturing),
以前,模具供应者和原始设备制造商一直很难解决模具设计中存在的问题。因为资深的工程师正在逐渐减少,而培养一个合格的模具工程师,对一个公司来说,既需要大量的时间,也需要大量的精力。UG为您提供业界最为强大的模具设计和制造功能,它的过程向导捕捉了业界特有的过程知识,融合了工业界专门的知识与经验,创立了最有效率的工作流程。生产率可以提高2~3倍,有时甚至更高。能让经验很少的设计人员同样能够设计出高质量的模具的先进工具,如注塑模具向导、级进模具向导、冲压模向导等。
UG还为您提供当前模具加工的最前沿技术——High Speed Machining (HSM)。高速铣削走刀快、转速快、切削量少、变形小、不需冷,它简化加工工艺、减少加工时间、提高加工质量、Nurbs 插补能极大地缩短程序、加工出高质量的薄壁件。UG提供高速铣削下的3轴NURBS 插补、5轴 NURBS 插补、刀轴光顺控制、刀轨光顺等功能,保持最大和稳定的切削速度,避免不连续和突然加速度变化,保持恒定的主轴转速,等体积切削,在保证插值公差的前提下,尽可能减少程序段数,提供高度连续的光顺刀位数据。
多工位级进模设计向导
级进模具设计和加工始在计算机、汽车、电子和电器工业领域内的支柱产业,
级进模设计是一个相对复杂和高度叠代的过程。传统的设计方法需要人工得重复全部设计过程,需要大量的时间和金钱,而且还需要大量的设计知识和经验。UG提供的级进模具向导通过特定工业过程的智能自动化大大的提高了生产率。
UG提供了一个完整的级进模设计环境,封装了模具设计的专家知识,而且还具有足够的灵活性去融合客户专门的知识,满足用户的不同需要。用户通过这个模块能自动的提取钣金特征并且将它们映像到过程特征上和自动的满足公司标准的功能,以捕捉一系列的设计。高效、简便易用的毛坯排样设计工具能够使设计人员有效的安排出每个工位的过程特征,尽可能得减少废料。客户化的模架库、标准零件库和镶件库加快了模具结构设计的速度,确保了用户的整个过程都能高效进行。
UG的级进模具向导,大大的缩短整个级进模的设计周期;充分利用人力资源,从而把成本减少到最低;把人为错误减少到最低,从而提高模具设计的质量;轻而易举地适应设计更改;极大的缩短您产品的投放周期、提高产品质量和更多的革新设计和扩展应用;让您的产品在竞争日益激烈的市场环境中脱颖而出,让您获得空前的竞争优势!
一个完整的冲压模具设计向导
UG冲压模工程向导可以通过过程自动化来辅助产品设计人员和制造工程师。冲压模向导为制定冲压工艺规程、模具布局和模具分析提供了一系列的工具。冲压模向导提供了辅助定义过程的功能,指导工程师制定用来加工特殊钣金零件的加工工艺。UG18版本新增了模具结构设计模块,这个模块与模具工程集成,能够提供从一个工序到下一个工序的无缝的数据流;还能够创建加工零件的工装模型。
篇4:UG在玩具设计中的应用
摘要:工业产品设计是一门古老而又年轻的学科,近年,计算机辅助技术飞速发展,计算机辅助工业产品造型设计就是这两个学科的结合、统一,我们在该论文中用两个案例阐述了使用UG软件做工业产品——玩具结构及外形设计的设计流程和技巧。
关键词:UG 玩具设计 结构设计 外形设计 人机工程1 引言 UG软件是由美国著名航空公司麦道开发的CAD/CAM/CAE/PDM应用系统,它覆盖产品的整个开发过程,包括概念设计、详细设计、工程分析、模拟仿真以及制造等,而玩具在工业产品中占有相当比重,尤其是在泛珠三角地区,中国现有8000多家玩具企业,其中广东占有5000多家,占到全国市场的一半以上,但大部分以出口为主。在去年,国家劳动和社会保障部正式向社会发布了玩具设计师的个新职业,这是我们中国玩具设计行业的一个新的开端。因此,对于中国的玩具设计师这一新兴行业,要求在玩具设计过程中设计师们的专业技能越来越高,新的技术给我们的设计带来了方便,同时也要求设计师们的计算机辅助技术的专业技能要更加熟练。2 UG在玩具结构设计中的应用 在玩具结构设计中,牙箱的设计是非常重要的,玩具的各种动作依靠牙箱来完成,因此掌握牙箱的设计是进行玩具结构设计的基础。牙箱的构成主要是由各种齿轮、凸轮、曲轴、马达等组合,在进行牙箱设计的具体工作前,有必要完成齿轮这个最基本零件的设计。玩具结构中的齿轮一般选用模数为0.4~1的小模数齿轮,其材料多选用赛钢(POM)、尼龙、合金等。 下面我们来看看使用UG来进行玩具结构设计中最常用的标准直齿圆柱齿轮的创建方法。 我们新建一个文件,进入相应的应用模块Modeling三维建模模块。 现在,我们来看看在UG中建立圆柱直齿轮的过程: 首先,我们要建立圆柱齿轮齿形渐开线表达式。大家知道,齿轮零件有几个基本的参数:模数(m)、齿数(z)、压力角(α),我们要通过齿轮的这些参数来确定齿形渐开线方程,这个过程我们需要通过UG的表达式菜单来建立,在主菜单选择Tools→Expressions创建以下表达式:a =0b =360m =0.75 (模数)z =36 (齿数)a =20(压力角)r =m*z*cos(α)/2s =(1-t)*a+ t*bt =1xt =r*cos(s)+r*rad(s)*sin(s)yt =r*sin(s)+r*rad(s)*cos(s)Zt =0注:d=m*z=工作节圆( 分度圆)齿顶圆d1=d+2*m齿底圆d2=d-2.5*m(hh)齿厚 (pi*m)/2 pi齿高=2.25*m啮合间隙=0.25*m接下来,使用UG的法则曲线建立齿轮齿形渐开线。在主菜单选择Insert→Curve→Law Curve→By Equation,生成渐开线如下图(1)所示:图(1)最后,生成齿轮实体,并阵列如图(2)、图(3)图(2) 图(3)3 UG在玩具外形设计中的应用 下面,我们再来看一个UG在玩具外形设计中的应用实例: 这款儿童娱乐休闲椅如图(4)所示:这款儿童休闲座椅是我们为在公共场所休闲娱乐的7~12岁儿童所设计的产品,图(4) 它的外观设计构思来自鲜花的花辨,此椅颜色设计方面运用多种颜色配搭,犹如鲜花盛开的形状,寓意花儿一样幸福的童年。 首先,在做这款儿童休闲椅的设计过程中,我们需要综合考虑外观的造型与人机工程的因素,另外,就是增强它的功能性。 设计座椅在某种意义上来说就是设计一种新的生活方式、工作方式、休闲方式、娱乐方式,对“座椅的功能不仅是物质的,也是精神的”有更多、更深的理解。 座椅设计会更重视“保护式”设计,不仅环保,而且更体贴,更加照顾人的情感。 在人们休闲时,座椅舒适程度成为人们首先考虑的因素,科技因素在座椅设计和制造中的含量越来越高 。 我们来看一组设计的人机数据:图(5)为人站立时的脊椎形态:其中腰部脊椎形状为向内凸起的。图(6)为人坐着时的脊椎形态:腰部脊椎形状为向外的弓型。 其中两图中的阴影区域为脊椎承力部位,也是脊椎最容易劳损的部位,所以对于现在长时间呆在办公室坐班的白领来说都或多或少患有腰部病痛。图(5) 图(6)坐姿情况下,支持人体的主要结构是脊柱、骨盆、腿和脚。良好坐姿情况下,压力适当地分布在各椎间盘间。座椅对人有以下益处:1、减轻腿部肌肉的负担;2、可以防止不自然的躯体姿势;3、降低人的耗能量;4、减轻血液循环系统的负担。 由于椎间盘内压力和肌肉疲劳是引起不舒服感觉的主要原因,因此,座椅的侧面轮廓若能降低椎间盘内压力和肌肉负荷,并且使之降到尽可能小的程度,就能产生舒服的感觉。当靠背倾角达到110°时,人体的肌电图的波动明显减少,被试有舒服的感觉。 基于以上人机数据,我们来设计者款座椅的时候,利用UG的草图功能,做椅背设计的初始草图,如图(7)所示:图(7) 然后,我们再来考虑它的功能设计部分: 顶部及底部为固定在中轴上不动的,中间部分能转动,可供小孩娱乐,座椅高度已经考虑到小孩摔倒的安全因素,另外座椅可以往上收拢防尘。上面采用透明材质,设计为自动售货机。底部为自动储物柜,在人们休闲时无须担心随身携带的财务损失。如图(8)、图(9)所示:图(8) 图(9)4 结束语 本文只是结合两个较简单的设计说明了UG的工业产品设计的流程及操作技巧等,对于玩具设计本身而言,它是一个复杂而难以掌握的过程,还需要设计者对于玩具行业的安全规范及ISO标准一些设计规则十分熟练,很值得深入研究。参考文献:《人机界面设计》罗仕鉴 朱上上 孙守迁编著 机械工业出版社《UG NX2 工业设计培训教程》李开林 李维 邝芸编著 清华大学出版社篇5:高速切削技术和高速切削刀具在模具制造中的应用研究
高速切削技术和高速切削刀具在模具制造中的应用研究
高速切削技术是对传统金属切削加工技术革命性的变化,而高速切削刀具为高速切削提供了硬件基础.随着模具制造业的不断发展,高速切削技术和高速切削刀具已经在模具加工制造中得到越来越广泛的`应用.
作 者:刘长灵 黄翊之 林七七 作者单位:河源职业技术学院 刊 名:科技信息 英文刊名:SCIENCE & TECHNOLOGY INFORMATION 年,卷(期): “”(12) 分类号:G71 关键词:高速切削 高速切削刀具 模具制造篇6:UG在钣金技术中的应用
在钣金件设计与制造过程中,为提高钣金设计、制造的质量和效率,UG 软件在钣金CAD,CAM/CAE方面的研究和应用,
随着机械设计自动化的不断发展,CAD/CAE/CAM 一体化软件层出不穷,UG软件便是其中之一。UG软件能将机械设计与生产的全过程集成在一起,它通过一种独特的参数化的以及面向零件的3D实体模型的设计制造技术,改变了传统的设计理念,为我们提供了一条更直观、更有效、更快捷的设计途径。在机械制造中,利用UG软件可以创建实体零件模型及组装造型,它具有运动模拟功能、虚拟装配功能、产生工程图功能、高级数控功能等,在设计过程中可进行有限元分析、机构运动分析、动力学分析和仿真模拟,提高设计的可靠性。在此,仅就UG软件在钣金设计制造中的应用,作一个初步探讨。
1 钣金件制造业概况
钣金零件是通过冲压工艺方法获得的具有一定形状、尺寸和性能的零件。由于冷冲压工艺具有生成率高、适合大批量生产等优点,所以钣金零件在航空航天、汽车、船舶、机械、化工、粮食加工机械等工业中应用十分广泛,在目前的零件加工行业中逐渐成为一个重要的组成部分。钣金零件传统的设计方法是钣金工程师在大脑里构思三维的产品,再通过大脑的几何投影,把产品表现在二维图样上,工程师有一大半的工作量是在三维实体和二维工程图的相互转化和繁琐的查表、计算中。而制造工人又要把二维的图样在大脑中反映出三维的实体然后进行加工—— 划线(放样展开)、裁料、成形、联接和装配,费时费事费力。若将计算机辅助设计、制造应用到钣金零件制造业中,尤其是将UG软件应用到钣金零件的设计制造中,则可以使钣金零件的设计非常快捷,制造装配效率得以显著提高。
2 UG软件应用到钣金零件设计制造中的主要步骤
2.1钣金零件的设计
人在设计零件时的原始冲动是三维的,设计实施的结果是有颜色、材料、硬度、形状、尺寸、位置、相关零件、制造工艺等关联概念的三维实体。但是在传统的设计中,在这两者之间的信息传递竟然全是二维的图形表达。由于以前的手段有限,人们不得不共同约定了在第一象限(美国是第三象限)平行正投影的二维视图表达规则,用有限个相关联的二维投影图表达自己的三维设想。这种信息表达是极不完整的,而且绘图、读图都要经过专门训练的人进行。
如果能直接以三维概念开始设计,尤其在UG软件的支持下,可以更直观、准确地表达出设计构思的全部几何参数,整个设计过程就可以完全在三维模型上讨论。UG软件提供了专供钣金设的钣金设计模块UG/Sheet Metal Design,它能帮助钣金工程师利用设计与制造相关联的观点来合理化设计过程,从板料的生成、各道工序的完成来逐步创建钣金零件。它可以看作是一个加工钣金零件的虚拟环境,工程师可以直接在计算机屏幕上进行零件设计和装配,产品的制作过程与真实的产品制造过程几乎没有差别,计算机屏幕上的产品就是未来产品的三维图像。
单个钣金零件设计完成后,可将多个零件的三维立体模型进行模拟装配,装配模型中的各零件相关:如果装配模型中的某一零件作了修改,其它零件也随之自动地作相应修改,从而大大缩短产品的设计和加工周期,提高产品设计的准确性,
2.2钣金零件的展开
在钣金零件设计完成后,为便于加工,都要将其转化为展开图,以确定所需板料大小以及板料的形状等。在传统的钣金零件展开时,都通过人工凭经验计算获得。这样做有3个缺点: (1)工作量大,展开过程繁琐。(2)效率低,在展开时对于一般工程师而言易产生错误。(3)精度低,大部分展开凭经验获得,造成物料和人工的大量粮费。
在UG 中利用其钣金模块UG/Sheet Metal Design的自动展开功能,可完成钣金零件的自动展开。对于展开后板料的形状和大小,均可通过自动计算获得,因此拥有高速、高精度、零错误率以及操作简捷的优点。
2.3钣金零件加工过程的模拟
利用UG/Sheet Metal Design模块中的自动展开功能及任意变换角度功能,可对钣金零件的加工过程进行模拟,以确定零件的最佳制作路线,完成零件的工艺性分析。在对加工过程进行模拟的过程中完成折弯刀具的选择。
2.4钣金零件加工工艺的输出
利用UG/Drafting模块强大的绘制二维视图功能可以方便、快捷、准确地绘制出各种需要的工序图,方便后续工序的制作和检验。由于UG的单一数据库,二维工程图与三维实体模型是完全关联的,如钣金造型有改动,二维视图也自动发生相应的变化,因此大大提高了二维图纸的准确性和出图效率。
2.5钣金零件排样
利用UG/Sheet Metal Nesting模块可在一块毛坯料上对若干品种的零件进行多种优化排样。用户只需提供零件的种类、每种零件的数量以及所用板料的规格,系统即可进行“自动排样”,并对不同的组合布局进行择优选择。该模块还能优化冲压工序,减少刀具更换,使冲压零件时板材重定位最少。用户还可以在交互式图形方式下直接在板材上进行排样。
2.6钣金零件数控加工程序的编制与输出
UG/Manufacturing模块提供了完备的编程手段供编程人员选用。其中包括二轴至五轴数控铣削、二轴至四轴数控线切割、三轴数控电火花加工、转塔式多工位冲压等多种加工手段。编程人员可以根据需要进行数控编程,利用UG的加工仿真模块可以对编制的程序进行加工仿真,若加工效果不理想,可以及时纠正,从而获得最理想的加工效果。
2.7钣金零件的数控加工
利用相应的后置处理文件,把刀位文件转化成机床能够识别的NC代码程序,通过串行接口输入到相应的数控机床,进行钣金零件的数控加工。
3 结束语
(1)采用UG软件进行钣金零件的辅助设计,可彻底地将工程师从零件图和展开图绘制的烦恼中解脱出来,与传统的设计过程相比更直观、更高效;
(2)利用CAE模块进行分析,最大限度地减少了设计缺陷;
(3)利用CAM 模块,提高了加工能力和效率;
(4)UG软件还提供了针对AutoCAD等其它软件的数据接口,使这些软件能与UG相互交换数据。
篇7:UG标准件制作及其在模具设计中的应用
7. 单击“插入-基准/点-基准平面”菜单,选择“自动判断”选项,相在关点“ORIGIN”上依次选择建立平行于XY、XZ、ZY平面的三个相关基准面,在部件导航器中将这三个相关基准面特征依次重命名为“ORIGIN_XY”、“ORIGIN_XZ”、“ORIGIN_YZ”,8. 单击“插入-基准/点-基准平面”菜单,建立约束斜顶头顶部位置的相关基准面。单击“插入-基准/点-基准平面”菜单,在弹出的对话框中选择“自动判断”选项,确保对话框左下角“Associative”前面的勾要打上,选择前面建立的“ORIGIN_XY”基准面,出现预览的基准面,确保法向箭头矢量方向是+ZC向,在“距离”文本框中输入“head_level”,点击确定完成这个基准面的建立,在部件导航器中将这个基准面特征重命名为“head_bot”。 步骤5和步骤6中所建立的相关点,是用于定位斜顶组件的原点位置;相关基准面是用于建立草图的放置面或用作约束基准;基准轴用作约束基准或草图的水平定位参。9. 点击“插入-基准/点-基准CSYS”,弹出“基准CSYS”对话框,在对话框中选择“绝对 CSYS”选项,在绝对坐标原点(0,0,0)建立基准坐标系统。MOLDWIZARD状态下调用的装配模架的插入点都是以UG的绝对座标为基准的,所以,下面步骤我们要根据“绝对 CSYS”来建立动模板底面,上顶针板顶面、底面,下顶针底面、下底板顶面、底面的基准平面,以实现斜顶组件能自动安装到模架的各个板中相应位置。10. 单击“插入-基准/点-基准平面”菜单,选择“自动判断”选项,确保左下角“设置”前的小勾打上,在绘图区选择“绝对 CSYS”的“XY”平面,确保预览状态的基准面法向矢量为-ZX向,在偏置文本框中输入“CP_off”,单击“确定”,动模底面的基准面已经建立了。在部件导航器中将这个基准面特征重命名为“CP_off”。11. 单击“插入-基准/点-基准平面”菜单,选择“自动判断”选项,确保左下角“设置”前的小勾打上,在绘图区选择“绝对 CSYS”的“XY”平面,确保预览状态的基准面法向矢量为-ZX向,在偏置文本框中输入“EJA_off”,单击“确定”,上顶针板顶面的基准面已经建立了。在部件导航器中将这个基准面特征重命名为“EJA_off”。12. 单击“插入-基准/点-基准平面”菜单,选择“自动判断”选项,确保左下角“设置”前的小勾打上,在绘图区选择“绝对 CSYS”的“XY”平面,确保预览状态的基准面法向矢量为-ZX向,在偏置文本框中输入“EJB_off”,单击“确定”,下顶针板顶面的基准面已经建立了。在部件导航器中将这个基准面特征重命名为“EJB_off”。13. 单击“插入-基准/点-基准平面”菜单,选择“自动判断”选项,确保左下角“设置”前的小勾打上,在绘图区选择“绝对 CSYS”的“XY”平面,确保预览状态的基准面法向矢量为-ZX向,在偏置文本框中输入“EJB_bot”,单击“确定”,下顶针板底面的基准面已经建立了。在部件导航器中将这个基准面特征重命名为“EJB_bot”。14. 单击“插入-基准/点-基准平面”菜单,选择“自动判断”选项,确保左下角“设置”前的小勾打上,在绘图区选择“绝对 CSYS”的“XY”平面,确保预览状态的基准面法向矢量为-ZX向,在偏置文本框中输入“BCP_off”,单击“确定”,底板顶面的基准面已经建立了。在部件导航器中将这个基准面特征重命名为“BCP_off”。15. 单击“插入-基准/点-基准平面”菜单,选择“自动判断”选项,确保左下角“设置”前的小勾打上,在绘图区选择“绝对 CSYS”的“XY”平面,确保预览状态的基准面法向矢量为-ZX向,在偏置文本框中输入“BCP_bot”,单击“确定”,底板底面的基准面已经建立了。在部件导航器中将这个基准面特征重命名为“BCP_bot”。16. 单击“插入-基准/点-基准平面”菜单,选择“自动判断”选项,确保左下角“设置”前的小勾打上,在绘图区选择“EJB_bot”平面,确保预览状态的基准面法向矢量为+ZX向,在偏置文本框中输入“lift base”,单击“确定”。在部件导航器中将这个基准面特征重命名为“lift base”。这个基准面位置比下顶针板底面高10MM,也就是斜顶座的顶面。
17. 创建斜顶标准组件的lift.prt的子组件。单击“装配-组件-新建组件”,文件夹路径要确保和“lift.prt”一样,名称为“lift_a.prt”点击“确定”,出现“新建组件”对话框,引用集选择“模型”,其它不变,点击“确定”。以同样的方法依次建立其它各子组件的部件文件“lift_a.prt”、“lift_b.prt”、“lift_c.prt”、“lift_d.prt”、“lift_e.prt”、“lift_f.prt”、“lift_g.prt”。29. 打开“装配导航器”,点击“lift_b”,再点右键,选择“设为显示部件”,弹出一个新的窗口。点击“插入-设计特征-旋转”命令,弹出“旋转”对话框,在“曲线规则”中选择“单条曲线”,依次选择链接的斜顶主体草图中斜顶杆的四条曲线;旋转轴为草图中杆的中心线,点击“确定”,完成斜顶杆本体特征的建立,30. 打开“装配导航器”,点击“lift_c”,再点右键,选择“设为显示部件”,弹出一个新的窗口。点击“插入-设计特征-拉伸”命令,弹出“拉伸”对话框,在“曲线规则”中选择“单条曲线”,依次选择链接的斜顶主体草图中滑座轮廓的四条曲线,拉伸矢量方向设置为“+Y”,开始距离为““lift”::W2/2”,结束距离为““lift”::W/2”,点击“应用”;再选择导向块的四条曲线,拉伸矢量方向设置为“+Y”,开始距离为““lift”::W2/2”,结束距离为““lift”::W/2+5”,“布尔运算”类型中选择“求差”,点击“应用”;再选择螺丝销钉草图中的二个销钉孔二个螺丝过孔,“值”对话框选择“贯通”,“布尔运算”类型中选择“求差”,点击“应用”;再选择螺丝沉头的二条曲线,矢量方向为“-ZC”,“值”为““lift”::ch”,“布尔运算”类型中选择“求差”,点击“应用”;点击“插入-细节特征-倒斜角”命令,选择二条棱角,倒角半径输入““lift”::C”,点击“确定”;完成斜顶座本体特征的建立。点击“插入-关联复制-生成实例几何体”命令,弹出“实例几何体”对话框,在“类型”中选择“镜像”,选择前面已经做好的实体特征,以草图的中心为基准面关联复制另一半滑座主体。31. 按照上面相同的方法完成其它子部件实体的建立。32. 在装配导航器中双击“lift”,利用上面的方法制作斜顶头、斜顶杆、导套、滑座、深孔钻定位面面的假体,以实现斜顶组件与各板之间的工艺避空。点击“编辑-对象显示”,选择刚才建立的所有假体,点击鼠标“中键”,在“颜色”栏选择6号黄色,“线型”栏选择“虚线”,“透明度”选择80,局部着色打勾,点击“确定”,完成假体的显示编辑。33. 点击“格式-引用集”,弹出“引用集”对话框,点击“添加新的引用集”,命名为“FALSE”,选择刚才所建立的一些假体,点击鼠标中键;用相同的方法建立引用集名字为“TRUE”实体为各个子组件的引用集。点击“文件-属性”,在弹出的“属性”对话框中,“属性”栏“标题”中输入“UM_STANDARD_PART”,“值”中输入“1”,以上引用集和属性中输入的英文字符不能出现错误。34. 将各个子组件中的真体放在第1层,草图和基准面放在250层,假体放在245层,关掉250、245层,保持图面清爽。35. 建立斜顶组件的bitmap位图文件,名称为 “lift.bmp”,位图文件要反映斜顶组件的主控参数,形状,结构,图面要做到清晰不乱。将“lift.bmp” 放在…\standard\metric\liutailong\lift 文件夹下面。36. 建立斜顶组件的数据库。复制一个UG自带的标准件EXCEL电子表格,存放于…\standard\metric\liutailong\lift中,将其命名为“lift.exl”。UG标准件电子表格有固定的格式。下面我们根据这个斜顶组件来简单的介绍一下电子表格中必填的内容。POSITION项:这个是设置标准件定位方法的项目。这个斜顶组件我们采用“WCS_XY”的方法定位。
PARENT项:这个是用来设置斜顶组件装配在哪个父部件下面的。笔者已经自己建立了一套模具设计装配构架,所有的斜顶组件都装配在“lift_asm”下面。模块初始化后,所有的装配主构架会自动建立,当调用标准件后,所有的标准件都会自动归类到相应的已经分好类的文件下面,条理清晰。
ATTRIBUTES项:该选项是用来定义标准件的属性的。当调用标准件时,系统会自动把这些属性克隆到所生成的标准件部件中。这些属性可以是标准件识别属性、BOM属性、及其它的属性。这里我们就简单填写二个属性“CATALOG=
BITMAP项:该选项是用来定义标准件位图路径的。这里我们输入“…\standard\metric\liutailong\lift\bitmap\lift.map”。
PARAMETERS项:此选项是电子表格中的大脑,必须有的。它用于管理标准件的主控参数名称和参数取值。这里我们把前面建立的lift.exp文件里所有的参数都输入。如(九)所示:(由于表格太长,仅示一小部分)
图(九)主控参数表格
37. 在标准件注册电子表格中注册斜顶组件标准件,即我们常说的报户口。在“…\standard\metric\liutailong”中建立文件名为“liutailong_reg_mm.xls”文件,建立“DD成型系统DD”分类,所有的滑块和斜顶标准件都放在这个分类下。如图(十)所示:图(十)标准件注册表38. 验证和调试。一般来说,一个标准件要验证的内容有:定位方法是否方便,放置原点和方位是否正确;各子组件是否能实现开发目标中确定的自动的定位到各块模板相应的位置和高度;各草图自由度是否已经完全约束;主控参数取值是否合理;标准件规格各参数是否正确,假体避空等是否符合工艺要求等等。
四.应用范例
调用一个斜顶组件,参数设置如下图(十一)所示,其中M值表示斜顶座相对斜顶杆位置的微调变量。
篇8:高速切削刀具在数控加工中的应用论文
摘要:
随着科学技术水平的不断提高,作为先进制造技术的重要组成部分高速切削技术在模具加工制造中已得到越来越广泛的应用。本文结合高速切削技术的发展现状,阐述了高速切削技术的应用及其未来趋势。
关键词:
篇9:高速切削刀具在数控加工中的应用论文
一、高速切削技术和高速切削刀具
目前,切削加工仍是机械制造行业应用广泛的一种加工方法。其中,集高效、高精度和低成本于一身的高速切削加工技术已经成为机械制造领域的新秀和主要加工手段。
“高速切削”的概念首先是由德国的C.S~omom博士提出的,并于1931年4月发表了著名的切削速度与切削温度的理论。该理论的核心是:在常规的切削速度范围内,切削温度随着切削速度的增大而提高,当到达某一速度极限后,切削温度随着切削速度的提高反而降低。此后,高速切削技术的发展经历了以下4个阶段:高速切削的设想与理论探索阶段(193l—l971年),高速切削的应用探索阶段(1972-1978年),高速切削实用阶段(1979--1984年),高速切削成熟阶段(20世纪90年代至今)。高速切削加工与常规的切削加工相比具有以下优点:第一,生产效率提高3~1O倍。第二,切削力降低30%以上,尤其是径向切削分力大幅度减少,特别有利于提高薄壁件、细长件等刚性差的零件的加工精度。第三,切削热95%被切屑带走,特别适合加工容易热变形的零件。第四,高速切削时,机床的激振频率远离工艺系统的固有频率,工作平稳,振动较小,适合加工精密零件。
高速切削刀具是实现高速加工技术的关键。刀具技术是实现高速切削加工的关键技术之一,不合适的刀具会使复杂、昂贵的机床或加工系统形同虚设,完全不起作用。由于高速切削的切削速度快,而高速加工线速度主要受刀具限制,因为在目前机床所能达到的高速范围内,速度越高,刀具的磨损越快。因此,高速切削对刀具材料提出了更高的要求,除了具备普通刀具材料的一些基本性能之外,还应突出要求高速切削刀具具备高的耐热性、抗热冲击性、良好的高温力学性能及高的可靠性。高速切削技术的发展在很大程度上得益于超硬刀具材料的出现及发展。目前常用的高速切削刀具材料有:聚晶金刚石(PCD)、立方氮化硼(CBN)、陶瓷、Ti(C,N)基金属陶瓷、涂层刀具fCVD)~超细晶粒硬质合金等刀具材料。
二、高速切削刀具的发展情况
金刚石刀具材料。金刚石刀具具有硬度高、抗压强度高、导热性及耐磨性好等特性,可在高速切削中获得很高的加工精度和加工效率。金刚石刀具分为天然金刚石和人造金刚石刀具。然而,由于天然金刚石价格昂贵,加工焊接非常困难,除少数特殊用途外,很少作为切削工具应用在工业中。近年来开发了多种化学机理研磨金刚石刀具的方法和保护气钎焊金刚石技术,使天然金刚石刀具的制造过程变得比较简单,因此在超精密镜面切削的高技术应用领域,天然金刚石起到了重要作用。
立方氮化硼刀具材料。立方氮化硼(CBN)是纯人工合成的材料,是20世纪50年代末用制造金刚石相似的方法合成的第二种超材料——CBN 微粉。立方氮化硼(CBN)是硬度仅次于金刚石的超硬材料。虽然CBN的硬度低于金刚石,但其氧化温度高达1360℃ ,且与铁磁类材料具有较低的亲和性。因此,虽然目前CBN还是以烧结体形式进行制备,但仍是适合钢类材料切削,具有高耐磨性的.优良刀具材料。CBN具有高硬度、高热稳定性、高化学稳定性等优异性能,因此特别适合加工高硬度、高韧性的难加工金属材料。PCBN刀具是能够满足先进切削要求的主要刀具材料,也是国内外公认的用于硬态切削,高速切削以及干式切削加工的理想刀具材料。PCBN刀具主要用于加工淬硬钢、铸铁、高温合金以及表面喷涂材料等。国外的汽车制造业大量使用PCBN刀具切削铸铁材料。PCBN刀具已为国外主要汽车制造厂家各条生产线上使用的新一代刀具。
陶瓷刀具。与硬质合金相比,陶瓷材料具有更高的硬度、红硬性和耐磨性。因此,加工钢材时,陶瓷刀具的耐用度为硬质合金刀具的10~20倍,其红硬性比硬质合金高2~6倍,且化学稳定性、抗氧化能力等均优于硬质合金。陶瓷刀具材料的强度低、韧性差,制约了它的应用推广,而超微粉技术的发展和纳米复合材料的研究为其发展增添了新的活力。陶瓷刀具是最有发展潜力的高速切削刀具,在生产中有美好的应用前景,目前已引起世界各国的重视。在德国约70%加工铸件的工序是用陶瓷刀具完成的,而日本陶瓷刀具的年消耗量已占刀具总量的8%~l0%。
涂层刀具。涂层材料的发展,已由最初的单一TiN涂层、TiC涂层,经历了TiC-112o3-TiN 复合涂层和TiCN、TiA1N等多元复合涂层的发展阶段,现在最新发展了TiN/NbN、TiN/CN,等多元复合薄膜材料,使刀具涂层的性能有了很大提高。硬质涂层材料中,工艺最成熟、应用最广泛的是TiN。(氮)化钛基硬质合金(金属陶瓷)金属陶瓷与由WC构成的硬质合金不同,主要由陶瓷颗粒、TiC和TiN、粘结剂Ni、Co、Mo等构成。金属陶瓷的硬度和红硬性高于硬质合金而低于陶瓷材料,横向断裂强度大于陶瓷材料而小于硬质合金,化学稳定性和抗氧化性好,耐剥离磨损,耐氧化和扩散,具有较低的粘结倾向和较高的刀刃强度。
三、高速切削刀具的具体应用情况
理想的刀具材料应具有较高的硬度和耐磨性,与工件有较小的化学亲和力,高的热传导系数,良好的机械性能和热稳定性能。理想的刀具使得高速硬切削能够作为代替磨削的最后成型工艺,达到工件表面粗糙度、表面完整性和工件精度的加工要求。硬质合金刀具具有良好的抗拉强度和断裂韧性,但由于较低的硬度和较差的高温稳定性,使其在高速硬切削中的应用受到一定限制。但细晶粒和超细晶粒的硬质合金由于晶粒细化后,硬质相尺寸变小,粘结相更均匀地分布在硬质相的周围,提高了硬质合金的硬度与耐磨性,在硬切削中获得较广泛应用。
陶瓷刀具和CBN刀具是在高速硬车削和端面铣削中最常用的刀具。它们所具有的高硬度和良好的高温稳定性,使其能够承受在硬切削过程中高的机械应力和热应力负荷。与陶瓷刀具相比,CBN刀具拥有更高的断裂韧性,因此更适合断续切削加工。为保证工件较高的尺寸精度和形状精度,高的热传导率和低的热膨胀系数也应是刀具材料所应具有的重要性质。因此,具有优良综合性能的CBN刀具是最适合用于高速硬切削的刀具。聚晶金刚石刀具的硬度虽然超过立方氮化硼刀具,但即使在低温下,其对黑色金属中铁的亲和力也很强,易引起化学反应,因此不能用于钢的硬切削。
一般而言,PCD刀具适合于对铝、镁、铜等有色金属材料及其合金和非金属材料的高速加工;而CBN、陶瓷刀具、涂层硬质合金刀具适合于钢铁等黑色金属的高速加工。故在模具加工中,特别是针对淬硬性模具钢等高硬度钢材的加工,CBN刀具性能最好,其次为陶瓷刀具和涂层硬质合金。
结论
高速切削技术的问世改变了人对传统切削加工的思维和方式,极大提高了加工效率和加工质量。而高速切削与模具加工的结合,改变了传统模具加工的工序流程。高速切削刀具作为高速切削技术的关键,随着技术的不断完善,将为模具制造带来一次全新的技术革新。
参考文献
[1] 韩福庆 高速切削刀具材料的开发与选择[J] 化学工程与装备
[2] 周纯江 叶红朝 高速切削刀具相关关键技术的研究[J] 机械制造2008
[3]范炳良 林朝平基于高速切削刀具锥柄系统的分析与研究[J] 机械设计与制造 2008
[4]马向阳 李长河 高速切削刀具材料[J] 现代零部件2008
[5]李鹏南 张厚安 张永忠 胡忠举 高速切削刀具材料及其与工件匹配研究[J] 工具技术2008
[6]肖寿仁 高鸣智 邓晓春 高速切削刀具材料应用进展[J] 有色金属2008
篇10:管理信息化在模具制造业的应用和实践
管理信息化在模具制造业的应用和实践
摘要本文讨论分析了模具企业管理信息化的重要性和必要性,指出了信息化在提高模具企业生产率、降低成本以及提高品质等方面所起的作用,并结合案例分析,进一步提出基于专业化管理系统iM3的模具企业信息化解决方案。
引言
一般说来,模具企业都是中小企业,大都是从作坊式的企业成长起来,甚至目前仍有许多模具企业是作坊式的的管理,在模具交货期、成本、质量的控制方面问题层出不断。面对激烈的市场竞争,落后的管理手段和水平,使模具企业中的管理和技术人员只有疲于奔命,企业投巨资引进的CAD/CAM系统和高档数控加工设备也难以发挥出应有的效率和水平,企业缺乏活力和竞争力。这些问题已经引起了许多有志向国际先进水平看齐的模具企业经营者的高度重视,如何提高企业管理水平,增强企业的竞争力已成为我国模具制造行业参与国际市场竞争迫切需要解决的问题。
因此,模具制造企业要提高管理水平,具备快速反应和及时调整的能力,没有一套先进的管理系统实现管理的信息化是很难做到的。通过信息化建设,实现模具制造企业的集成化管理,是促进企业提高经营管理水平的一个有效途径。
本文通过模具企业实际的案例,讨论分析了信息化对提高模具企业管理水平的重要性和必要性,并结合深圳市伟博思网络技术开发有限公司开发的专业化模具企业管理系统iM3(inteMoldMakingManagement),给出了信息化解决方案。
一、信息化是企业与客户信息交流沟通的桥梁
模具是典型的按定单单件生产的行业,每一个定单都要与客户进行详细的业务和技术方面的沟通,否则将会产生严重的后果。下面是模具企业与客户信息沟通不充分的两个实例:
案例1.某大型模具厂承接了一个日本新客户的模具定单,这个日本客户习惯定单下达后,就与模具厂的设计人员进行详细的技术沟通,对模具提出很细致的设计要求,模具厂按此要求进行设计就可以了,不需要再确认设计图纸。而模具厂设计人员完成设计后,却仍按以往接美国客户定单的习惯,等待客户确认设计后再订购模架和材料,一直等了10天,才知道客户不需要确认图纸。结果,该套模具延期10天,客户很不满意,从此不再下定单,为此失去了一个非常有潜力的客户。
案例2.某模具工厂承接了一个新客户的模具定单,该客户的注塑工厂有一套严格的生产安全标准――多少吨的模具必须使用多大的吊环。由于缺乏详细的技术沟通,这个问题被忽略了。模具设计人员按照本工厂的习惯选用吊环,结果比客户的标准小了一个规格,致使模具交付客户后,才发现不符合要求,只能把模具运回,重新加工吊环孔,整个过程的费用就超过万元,同时还影响了客户的生产。
由此可见,在与客户及企业内部的信息沟通方面即便是一个小小纰漏,都会对企业造成巨大损失。因此,解决好沟通问题,具有如下重要意义:
尽量一次把客户业务与技术方面的要求了解全面,避免多次反复,从而节省费用和时间。
详细了解客户的模具技术要求,避免在试模后修改和返工。
对每一次沟通的内容进行记录和总结,针对每个客户逐步建立客户业务和技术资料知识库,在公司内部共享,以便提高客户服务水平,减少错误。
信息化的管理系统将能够帮助模具企业更好地与客户进行信息沟通。例如,在iM3系统中,提供了详细的模具技术沟通模板,模板整合了国内外多家优秀模具企业的经验,完全与国际模具行业接轨。通过该模板,方便与客户进行详细的技术沟通,减少模具的修改工作。而且通过系统记录的与客户沟通信息,可以总结客户业务和技术方面的习惯,分享给公司内部相关人员,避免犯重复的错误。
二、信息化系统可以帮助企业监控模具进度
客户非常关注模具的试模及交付日期,往往根据模具的试模时间安排试产及生产计划,尤其是海外客户,往往把模具的交付期的重要性放在首位。因此,控制模具的生产制作工期是企业在市场竞争中取胜的一个重要指标。下面的案例可能是许多模具厂都出现过的问题。
案例.某大型模具工厂承接了美国客户的模具定单,由于缺乏有效的模具生产进度监控和管理手段,不能按期试模。生产部门也把这一情况反馈给海外的市场人员,但市场人员由于不能了解生产的实际情况,担心不按期试模客户会不高兴,于是抱着侥幸的心态,认为生产部门能够加班加点抢回时间,仍然承诺客户的既定试模日期。当客户从万里之外来看试模时,发现模具在一周内根本不能试模。客户非常失望,从此不再下定单。
对模具进程监控不力的根源在于:
缺乏有效的模具生产进度监控手段,不能及时发现模具生产过程中出现的问题,及早发现、及早解决。
模具生产过程的状况不能得到有效反馈和记录,往往凭感觉来判断模具的进程,习惯用“差不多、差很远、很快做完”等模糊概念来说明进度,数据不准确及时,往往产生侥幸心理。
公司内部缺乏信息共享的环境与平台。由于每个人的工作性质的不同,对每套模具的实际生产进程的了解程度有很大的差异,而且,通过台阶式的层层信息反馈往往会造成信息失真,再加上人为的因素,问题就出来了。
人们往往比较注意重要和难的问题,忽视小问题,尤其是当企业同时有数十或上百套处于不同阶段的在制模具时,管理人员很难坚持每天不厌其烦地检查每一套模具的每一个任务进程是否在计划之内。
信息化的管理系统将为企业提供共享的、一致的、忠实的进程监控平台。例如,在iM3系统中,通过项目计划与进程控制,可以对模具的整个生命周期(定单确定―设计―采购―生产―首次试模―模具修改―交付)进行管理。生产一线管理人员直接在系统中反馈模具实际进度,系统忠实地监控项目进程的每一个任务,当某一控制点出现延期时,系统会自动发出报警邮件给相关人员,以便及早发现、及早解决。而且,对于一些关键任务,还可以让系统提前预警,以使有关人员及早准备和安排 。
&n
bsp; 三、有效的模具成本控制利不开信息化
成本控制是模具企业管理上的一个难点,模具企业的成本控制能力越来越突出地体现了企业的核心竞争力。目前,模具行业面临着模具价格越来越低的沉重压力,模具增加几次修改,模具利润就消耗干净,甚至要赔本。企业如果不能从根本上解决这个问题,将面临淘汰出局的危险。
在专业化的模具企业管理系统iM3中,将通过如下途径帮助企业控制成本:
在公司内部下达定单时,以报价的成本估算为基础,为模具制定计划成本;系统中设置成本预警,对模具生产中的`成本要素进行监控,从而有效控制各项费用,确保利润目标的顺利达成。
在模具BOM下达时,比较设计物料总成本与计划材料成本的差异,决定是否下达。在采购材料收货时,比较交货价格与计划价格的差异,决定是否收货,从而有效控制采购成本。
系统记录和统计每一工件在每个加工工序中产生的加工工时,自动比较实际加工费用与计划费用的差异,监控制造费用。当实际费用超过计划费用时,系统会自动报警,通知相关管理人员。
案例.某模具厂在设计某客户的电视机前壳模具时,采用四块价格昂贵的铍铜。供应商供货时,将四块铍铜的边角料也一起计价,送货价格超出计划价格6000多元,仓库管理人员在为该物料收货入库时,模具公司采用的iM3管理系统警告此物料入库价格严重超出计划费用,拒绝入库。经过采购主管与供应商交涉后,剔除不合理的6000元费用后,才收货。
四、信息化有助于车间监控和管理
实时车间监控可以帮助生产主管监控每台设备的生产情况及模具的加工进程,提高设备的利用率,控制工件的生产进度。
例如,当公司管理人员需要检查生产车间情况时,可以通过iM3系统查看各加工设备和工作组的的实时生产情况,系统通过不同的颜色标记,清晰反映各设备及加工组正在加工的工件和待加工工件的状态,包括每台机床正在干什么,机床目前的负荷情况,正在加工的工件是否延期,待加工工件是否已移交本工序,上道工序是否延期,物料是否到位等,大大减轻了管理人员的工作强度。
当管理人员需要检查某套模具的生产情况时,可以查看以甘特图形式展示出来的模具加工进度,并通过各工序的计划时间和实际的进程的对比,帮助管理人员跟踪模具的生产进度。
而以往生产管理人员在检查模具进度时,要到车间一个工位一个工位去看,而且只能看到主要的部件,小零件完成情况可能根本无法了解,甚至连车间的班组长也不知道小零件在哪里。或者召开生产会议,把各班组长全部召集起来,花费很长的时间一一汇报模具的进度。由于班组长还不是第一线的加工人员,只能以自己的感觉和经验来判断模具的进度,具有很大误差。对于经验丰富的工人来说,可能判断准确点,但一个工厂没有办法保证每个工人都是很有经验、每时每刻都很有责任心。而只要一个定单中有一套模具不能按期完成,整个定单的交付就有问题,这也是许多模具厂在试模前经常要加班加点,甚至通宵加班赶制模具的一个主要原因。
五、信息化管理系统促进CAD工程数据在企业内部共享
由于工期短,模具企业的设计图纸很难象批量生产模式的企业一样做得很精细,而且由于更改频繁、图纸量大,也不可能把图纸发给许多非生产部门,这为企业内部的设计信息共享带来了障碍。生产或其他业务部门有时希望能够测量一下图纸中未标注的尺寸,有时需要查看一下3D模型以便对复杂的结构有更清楚地了解,这些需求都没必要为此购买昂贵的CAD设计软件,而且对非设计部门的人员来说,使用专业化的CAD软件在操作和查找相关文件方面也很不方便。如果把管理系统与CAD工程数据链接,则会极大地方便生产或其他业务部门,使设计信息真正在全企业共享。
在iM3系统中,根据模具企业的运作特点,集成了设计模型浏览工具,可以在系统中方便浏览2D/3D文档(包括AutoCAD、Pro/E、UG等)。这样,可以在公司内部任何一台电脑中查看CAD模型。例如,工艺人员制订某个工件的生产工艺路线时,可以直接点击查看3D图形按钮,借助浏览工具可以旋转、检查尺寸、做各种剖切面等操作,方便工艺人员制订合理完整的工艺流程;车间工人在加工某一工件时,借助车间生产终端,可以方便浏览正在加工零件的3D图形,通过对比加工工件与3D图形,检查是否加工正确,判断加工是否完全,避免返工和报废。而以往数控和电火花加工操作人员只看2D图形,很难判别工件的最终形状,经常由于CNC程序遗漏或电极漏做而造成工件的返工,既浪费资源,又影响模具工期。此外,这一功能对于市场报价、采购等部门的工作人员也都是非常有用的。
六、信息化在促进信息共享方面的其他作用
通过信息化管理系统提供的信息共享平台,将为企业内部的管理工作提供前所未有的便利,减轻管理人员的工作压力,避免出错,有效的保证模具质量和工期。
案例1.某厂模具装配前,装配钳工经常因外购顶针到货不及时,需要电话询问仓库和采购部门,甚至打电话给供应商,才能确认交付时间,非常麻烦。如果中间某个环节信息出现断路,就无法确定准确的交付日期,那么模具试模时间则因此不能确定。
案例2.某大型模具企业,每天晚上7:30―9:00要召开生产管理骨干人员会议,会议的主要议题是检讨模具的生产情况(进度、质量),当某套模具出现问题时,再研讨如何改进。管理规范的模具企业都会定期组织类似的会议,但这需要很多人员花费大量的精力和时间去了解模具的生产状况,查询和记录全部模具的生产信息,从中筛选出非正常的模具。这样做,无疑将增加管理人员的压力,把宝贵的时间和精力浪费在信息的统计和收集方面,且往往因收集的信息不准确而影响决策。
在一个具有信息化管理系统的模具企业,通过系统与管理流程密切结合,将会为企业的各级管理和工作人员带来信息查询和统计的方便,使其准确的掌握最及时、最准确的各种信息。例如,在iM3系统中,生产管理人员可以通过系统查询生产或采购物料目前所处的实际状态,不必一个一个部门电话查询;当需要了解模具的进度时,除了系统可以自动为异常发出警告外,管理人员也可以主动进入系统,统计其关注
的异常问题,如,统计截止目前设计拖期的模具或采购拖期的物料、统计计划下周试模的模具、统计尚未按期付款的客户、统计本月某供应商的应付帐等,这不但可以极大地减轻模具管理人员的工作压力,而且能够帮助管理者正确决策。
当然,管理信息化还可以在更多的方面帮助模具企业改进管理,因篇幅所限,这里不再一一列举了。
结束语
通过管理信息化与管理改进紧密结合,可以促进企业的管理规范化,提高企业的运作效率和市场竞争力,把企业的管理人员从繁杂的、重复性的劳动中解放出来,使高层管理人员可以有更多的时间关注企业的发展方向,加强与客户的沟通,开拓更广泛的市场,市场人员也可以进一步加强客户关系的管理,寻找新的客户资源,技术主管可以有时间关注模具新技术的发展,加强行业内技术的交流,不断提升企业的技术水平,生产主管可以有更多的时间考虑如何进一步提高工效,提升质量和降低成本,做到不断改善。因此,模具企业应该把握住信息化时代带来的机遇,为企业的长远可持续性发展打好坚实的基础。 相关性:毕业论文,免费毕业论文,大学
★ 机电专业实习总结
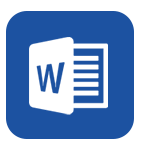
【UG等高切削在模具上的应用(精选10篇)】相关文章:
机电一体化顶岗实习个人总结2022-11-05
金工实习总结2022-11-05
个人简历:机械自动化2022-05-06
复杂网络理论下计算机网络拓扑研究论文2022-04-29
机电专业顶岗实习心得总结2022-08-12
冷冲压技术在模具设计中的应用开题报告2023-08-28
浅谈基于数字化设计制造能力培养的课程群规划论文2024-04-19
数控技术毕业论文2022-12-01
模具设计cad自荐信2023-01-25
机械设计制造及其自动化专业自荐信2022-04-30