锅炉毕业论文(精选13篇)由网友“抹茶拿铁”投稿提供,下面就是小编整理过的锅炉毕业论文,希望大家喜欢。
篇1:锅炉毕业论文
锅炉毕业论文
基于组态软件的供暖锅炉监控系统设计
摘 要
工业锅炉是采暖供热系统的核心设备,它的主要任务是安全可靠、经济有效地把燃料的化学能转化为热能,进而将热能传递给水,生产出满足需要的蒸汽或热水。
本文主要介绍的是通过组态软件(MCGS)做成的一套锅炉监控系统。大家都知道我们可以把锅炉分为三个相对独立的环节去控制:燃烧系统的控制,汽包液位的控制,过热蒸汽温度的控制。本文也采用了这样的分环节控制的方法。首先,用炉膛内的压力与饱和蒸汽的压力组成串级控制系统去控制燃料的供给量,继而控制了燃烧系统。当然为了安全起见我们还必须用一个压力传感器去测量炉膛内的压力。其次,用饱和蒸汽的温度和汽包的水位组成串级控制去控制给水量,继而控制汽包的水位。最后,用过了减温器的蒸汽的温度与过热后的蒸汽的温度组成串级控制去控制减温水的供给量,继而控制过热蒸汽的温度。该系统具有数据采集,实时控制,在线查询等功能,同时能够通过一些简单的传统控制(PID控制)对其进行相对稳定的控制。
本文针对过路系统三个环节中的每个环节的单独控制(燃烧系统控制,汽包液位控制,过热蒸汽温度控制),得到了比较稳定的锅炉系统,同事又对其进行了较为良好的监控。
关键词:组态软件;锅炉;串级控制;安全
目 录
摘 要 ............................................................... I
第1章 引 言 ........................................................ 1
1.1锅炉研究的背景和意义 ............................................ 1
1.2 锅炉研究的现状和存在的问题...................................... 1
第3章 锅炉工艺流程 .................................................. 4
3.1锅炉工艺流程简介 ................................................ 4
3.2锅炉控制中的控制参数 ............................................ 5
3.2.1锅炉中的主要控制参数 ........................................ 5
3.2.2锅炉参数之间的内在关系 ...................................... 5
3.3锅炉设备的控制系统 .............................................. 6
3.3.1锅炉汽包水位控制 ............................................ 6
3.3.2锅炉燃烧系统的控制 .......................................... 6
3.3.3过热蒸汽系统的控制 .......................................... 7
3.4相关对象的动态特性 .............................................. 8
3.4.1汽包水位的动态特性 .......................................... 8
3.4.2压力的动态特性 ............................................. 10
第4章 锅炉监控系统设计 ............................................. 13
4.1设计方案 ....................................................... 13
4.1.1汽包水位控制系统设计 ....................................... 13
4.1.2燃烧控制系统的设计 ......................................... 14
4.1.3过热蒸汽温度控制 ........................................... 15
第7章 结束语 ...................................................... 16
致 谢 ............................................................... 20
第1章 引 言
1.1锅炉研究的背景和意义
工业锅炉是采暖供热系统的核心设备,它的主要任务是安全可靠、经济有效地把燃料的化学能转化为热能,进而将热能传递给水,生产出满足需要的蒸汽或热水。 我国目前在役运行的工业锅炉共约有52万台,多为燃煤链条炉,它们的特点是应用广,容量小(绝大多数都是 10 t/h以下的分散锅炉),设备陈旧,耗煤(或油、气)量大(年耗煤量占全国总耗煤量的三分之一),效率低(平均约为60%),自动化程度不高。另外由燃料燃烧产生的烟尘、SOX,NOX等对环境造成了严重污染。
随着对生产自动化要求渐高的趋势,改变工业锅炉运行中传统的手动、半自动操作方式已势在必行尤其是近年来我国北方各大城市承受着持续低温天气和煤炭价格大幅度上涨的压力,还要面对供热标准。
工业供暖锅炉的安全运行显的越来越是重要,那么这就要我们用一些方法来监控锅炉的运行。并且在出现异常的情况下能够马上显示出来,这样以便于我们进行整修。所以为了供暖锅炉能够安全有效的运行,我们必须对它进行监控,这就是我们经常说的供暖锅炉监控控制系统[1]。
1.2 锅炉研究的现状和存在的问题
随着信息技术的发展,远程教育中的重要组成部分――远程实验系统获得了越来越多的关注。作为控制类学科的典型实验对象――锅炉控制系统也成了远程实验研究的焦点。现在,绝大多数高校都是购买现成的工控机和成套的实验控制对象以及相应的控制软件(多为组态软件),成本很高,而且产品功能也不十分完善,灵活性差,实验结果不理想。例如:学生们做 PID锅炉水位定值调节实验时,
只能设定 P、I、D的参数值,然后看下实验的运行结果就行了,这样学生们就不容易深刻理解实验背后较深的控制理论知识,不利于专业素养的培养,也不能适应现代高校控制类相关专业的教学需要和实验教学的发展趋势。因此,开发一种功能完善 、灵活性好,且能够进行自主设计型实验的远程实验监控软件就很有必要。我们选用组态软件(MCGS)作为锅炉控制系统远程实验监控软件的开发工具。锅炉微计算机控制,是近年来开发的一项新技术,它是微型计算机软、硬件自动控制、锅炉节能等几项技术紧密结合的产物,我国现有中、小型锅炉30多万台,每年耗煤量占我国原煤产量的 1/3,目前大多数工业锅炉仍处于能耗高、浪费大、环境污染等严重的生产状态。提高热效率,降低耗煤量,用微机进行控制是一件具有深远意义的工作[2] 。
作为锅炉控制装置,其主要任务是保证锅炉的安全、稳定、经济运行,减轻操作人员的劳动强度。采用微计算机控制,能对锅炉进行过程的自动检测、自动控制等多项功能。
锅炉微机控制系统,一般由以下几部分组成,即由锅炉本体、一次仪表、微机、手自动切换操作、执行机构及阀、滑差电机等部分组成,一次仪表将锅炉的温度、压力、流量、氧量、转速等量转换成电压、电流等送入微机,手自动切换操作部分,手动时由操作人员手动控制,用操作器控制滑差电机以及阀等,自动时对微机发出控制信号经执行部分进行自动操作。微机对整个锅炉的运行进行监测、报警、控制以保证锅炉正常、可靠地运行,除此以外为保证锅炉运行的安全,在进行微机系统设计时,对锅炉水位、锅炉汽包压力等重要参数应设置常规仪表及报警装置,以保证水位和汽包压力有双重甚至三重报警装置,这是必不可少的,
以免锅炉发生重大事故[3]。
随着计算机控制系统的发展和成熟,国外发达国家的工业锅炉已经应用了成熟的DCS或FCS产品,如霍尼威尔9000、西门子Teleperm-D、SMAR Sytem302等系统,并取得了良好的效果。我国工业锅炉平均单机容量只有2.4t/h,远低于国外水平(日本为5t/h,美国为14t/h),容量还不足以大到使用国外成套昂贵设备的程度。近十年来,国内中小型工业锅炉计算机控制系统多采用两级方式,即监管级和控制级,监管级进行监视和管理,控制级完成数据采集和控制功能[4]。
第3章 锅炉工艺流程
3.1锅炉工艺流程简介
锅炉是化工,炼油,发电等工业生产工程中必不可少的动力设备。常见的锅炉设备的主要工艺流程如图3.1所示。燃料和空气按照一定的比例送入燃烧室燃烧,生产的热量送给蒸汽发生系统,产生饱和蒸汽。然后经过过热器,形成一定气温的过热蒸汽,汇集至蒸汽母管。具有一定压力的过热蒸汽,经负荷设备控制供给负荷设备用,与此同时,燃烧过程中产生的烟气,除将饱和蒸汽变为过热蒸汽外,还经省煤器预热锅炉给水和空气预热器预热空气,最后经引风机送往烟囱,排入大气 [5]。
3.1 锅炉设备主要工艺流程图
图3.1 锅炉设备主要工艺流程图
3.2锅炉控制中的控制参数
3.2.1锅炉中的主要控制参数
锅炉是全厂的重要动力设备,其要求是供给合格的蒸汽,使锅炉发汽量适应负荷的需要。为此,生产过程的各个主要工艺参数必须严格控制[5]。锅炉设备是一个复杂的被控对象,主要输入变量是负荷,锅炉给水,减温水,送风和引风等。主要的输出变量是汽包水位,蒸汽压力,过热蒸汽温度,炉膛负压,过剩空气等。锅炉对象简图如图3.2所示:
3.2.2锅炉参数之间的内在关系
锅炉的这些输入变量和输出变量之间相互关联。如果蒸汽负荷发生变化,必
将会引起汽包水位,蒸汽压力和过热蒸汽温度等的变化。燃料量的变化不仅影响蒸汽压力,同时还会影响汽包水位,过热蒸汽温度,过热空气和炉膛负压;给水量的变化不仅影响汽包水位,而且对蒸汽压力,过热蒸汽温度也有影响;减温水的变化会导致过热蒸汽温度,蒸汽压力,汽包水位等的变化。所以锅炉设备是一个多输入多输出且相互关联的被控对象[6]。
3.3锅炉设备的控制系统
由于锅炉设备是一个多输入,多输出的且相互关联的被控对象,目前工程处理上做了一些假设后,将锅炉设备控制划为若干控制系统,主要的控制系统可分为锅炉汽包水位控制,锅炉燃烧系统控制,过热蒸汽温度的控制。
3.3.1锅炉汽包水位控制
被控变量是汽包水位,操纵变量是给水量。它主要考虑的是汽包内部的物料平衡,使给水量适应锅炉的蒸汽量,维持汽包中水位在工艺允许范围内。维持汽包水位在给定范围内室保证锅炉安全运行的重要条件之一,是锅炉运行的重要指标。
如果水位过低,则由于汽包内的水量较少,而且负荷却很大,水的汽化速度又快,如不及时控制,就会使汽包内的水全部汽化,导致锅炉烧坏和爆炸;水位过高会影响汽包汽水分离,产生蒸汽带液现象,会使过热器管壁结垢导致破坏,同时过热蒸汽温度急剧下降,该蒸汽作为汽轮机动力的话,还会损坏汽轮机叶片,影响运行的安全与经济性。汽包水位过高过低的后果极为严重,所以必须严格加以控制。
3.3.2锅炉燃烧系统的控制
锅炉燃烧控制系统的控制的目的是使燃烧所产生的热量适应蒸汽负荷的需要(常以蒸汽压力为被控变量);使燃料与空气量之间保持一定的比值,以保证经济燃烧(常以烟气成分为被控变量),提高锅炉的燃烧效率;要让引风量和送风量相适应,以保持炉膛负压在一定范围内。为了达到上述三个控制目的,控制手段也有三个,即燃料量,送风量和引风量。
锅炉燃烧控制系统的基本任务是使燃料所产生的热量能够适应锅炉的需要,同时还要保证锅炉安全经济的运行。燃烧控制的具体内容及控制系统设计因燃料种类,制粉系统,燃烧设备以及锅炉的运行方式不同而有所区别,但是大体上看来都要完成以下几个方面的任务:
(1) 主蒸汽压力的变化反映了锅炉生产的蒸汽量和汽机消耗的蒸汽量相适应的
程度。为此必须设置蒸汽压力控制系统。当负荷变化时,通过控制燃料量使蒸汽压力稳定。
(2) 当燃料量改变时,必须相应地控制送风量,以保证燃烧过程的经济性。
(3) 炉膛压力的高低关系着锅炉的安全经济运行。燃烧控制系统必须要让引风
量(烟气量)与送风量相配合以保证炉膛压力为一定值。
3.3.3过热蒸汽系统的控制
维持过热器出口温度在允许范围内,并保证管壁温度不超过允许的工作温度。被控变量一般是过热器出口温度,操纵变量是减温水的喷水量。
现代锅炉的`过热器在高温高压条件下工作。过热器出口温度是全厂工质温度的最高点,也是金属壁温的最高点,在过热器正常运行时已接近材料允许的最高温度。如果过热蒸汽温度过高,容易烧坏过热器,也会引起汽轮机内部零件过热,
影响安全运行;温度过低则会降低全厂的热效率,所以电厂锅炉一般要求过热蒸汽温度偏差保持在?50C以内。
过热蒸汽温度自动控制系统是锅炉控制中的难点。目前,很多实际系统并没有达到控制指标的要求。其主要原因有下述的两个方面:
(1) 扰动因素多变化大。各种扰动因素对过热蒸汽温度的静态影响的关系我们
要弄清楚。
(2) 控制通道滞后大。控制过热蒸汽温度的手段是调节减温水量。控制通道的
动态特性与减温器的安装位置有关。假若能将减温器安装在过热器的出口,显然控制通道的滞后小的多。但是这样的工艺流程安排对过热器的安全是不利的。为了保证过热器不超温,工艺上总是将减温器安装在过热器的入口,这将带来控制对象较大的滞后[7]。
3.4相关对象的动态特性
3.4.1汽包水位的动态特性
(1)蒸汽负荷对水位的影响即干扰通道的动态特性
在燃料不变的情况下,蒸汽用量突然增加,瞬时必然导致汽包压力下降,汽包内的沸腾突然加剧,水中气泡迅速增加,将整个水位抬高,形成虚假的水位上升现象即所谓的假水位现象。
在蒸汽量的扰动下,水位变化的阶跃响应曲线如图3.3所示。当蒸汽流量突然增加时,由于假水位现象,在开始阶段水位不仅不会下降反而会上升,而后下降(反之,当蒸汽流量突然减小时,则水位先下降后上升)。蒸汽突然增加时,实际的水位变化H,是不考虑水面下气泡容积变化时的水位变化H1,与只考虑水面
图3.3 水位变化的阶跃响应曲线
下气泡容积变化所引起水位变化H2的叠加,即
H = H1 + H2 (3.1)
假水位变化的大小与锅炉的工作压力和蒸发量等有关,例如一般100-300t/h的中高压锅炉,当负荷突然变化10%时,假水位可达30-40mm。对于这种假水位现象,在设-*计方案时必须注意[8]。
(2) 给水量对水位的影响,即控制通道的动态特性
在给水流量作用下,水位的阶跃响应如图3.4所示。把汽包和给水看作单容自衡对象,水位响应曲线如图3.4中的H1线。但是由于给水温度比汽包内饱和水
的温度低,所以给水量变化后,使汽包中的气泡减少,导致水位下降。因此使劲的响应曲线是图3.4中的H线,即当突然加大给水量后,汽包水位不是立即增加,而是要呈现出一段起始惯性段。
图3.4 给水流量作用下水位的阶跃响应曲线
3.4.2压力的动态特性
(1)气压的动态特性
气压对象由一系列装置组成,它包括给煤机,炉膛,汽水系统,过热器,汽轮机进气阀和汽轮机。在燃料量和风量同时变化时对发气量基本上是一个纯滞后环节。汽包的压力对象,反映过热器的过热蒸汽压力对象都是一个积分环节。其它的都可以看做是一个比例环节。但是需要指出的是气压的动态特性是与汽轮机调速运行系统的运行情况有关的。当然主蒸汽压力的变化反映了锅炉生产的蒸汽量和汽轮机消耗的蒸汽量相适应的程度,为此我们要设置蒸汽压力控制系统,这也是有气压的动态特性决定的。这里所指的气压是燃料量扰动下的气压和负荷扰动下的气压[9]。
(2)炉膛压力对象特性
为了保证炉膛安全,一般要求炉膛压力略小于大气压力,所以炉膛压力一般
称之为炉膛负压。炉膛负压放映了引风量与送风量之间的平衡关系。当送风量或
引风量单独改变时,炉膛负压惯性变化很小,故可以将炉膛负压对象近似看成是一个时间常数很小的一阶惯性环节。
(3)关于经济燃烧
众所周知,对于燃烧过程应保持燃料量与空气量成比例。但是假若配置的是燃料量与空气量固定的比值控制系统,却因为以下原因,并不能保证在整个生产过程中始终保持经济燃烧。因为其一,在不同的负荷下,两流量的最优比值是不相同的;其二,燃料成分(如含水分,灰分的量)有可能变化;其三,流量测量的不准确。这些因素都不同程度的影响到燃料的不完全燃烧或空气的过量,造成炉子热效率下降。为了改进这一情况,最好有一个指标来闭环修正两流量的比值。目前常用的是烟气中的含氧量。
烟气中的各种成分,如O2,CO2,CO和未燃烧烃的含量,基本可以反映燃料燃烧
的情况,最简便的方法是用烟气中的氧量A0来表示。根据燃烧反应方程式,可以
计算出使燃料完全燃烧时所需要的氧量,从而可以得到所需的空气量,称为理想空气QT。但是实际上完全燃烧所需的空气量QP,要超过理论计算的量,即要有一定的过剩空气量。由于烟气的热损失占锅炉热损失的绝大部分,当过剩空气增多时,一方面使炉膛温度降低;另一方面使烟气热损失增多。因此过剩空气量对不同的燃料都有一个最优值,以满足经济燃烧的要求[10]。
过剩空气量常用过剩空气系数?来表示,即实际空气量QP与理论空气量QT之比为:
? = QP/QT (3.2) 因此,?是衡量经济燃烧的一种指标。保证锅炉热效率最高的?值称为最佳?值,
最佳?值与锅炉负荷有关,一般?在1.2-1.4之间。
?很难直接测量,但是可用烟气氧含量百分数A0来衡量。在完全燃烧情况下,
存在以下近似式
? = 21/(21-A0) (3.3)
当?=1.2-1.4时,相应A0为3.5-6(O2%).最佳的氧量值与负荷关系为
A0 = 6-D/50 (3.4)
式中,D为负荷百分数。
第4章 锅炉监控系统设计
4.1设计方案
由于锅炉是一个复杂的控制对象,所以我们要想对其进行全面的监控是很难做到的,在前面我们也都讲过锅炉可以分成为若干个控制环节进行控制,所以我们设计的时候也要这么考虑。在本文中我们是将锅炉控制分为三个环节,但是这三个环节并不是孤立的,它们之间也是相互关联的。下面我们就将三个环节的设计方案一一介绍。
4.1.1汽包水位控制系统设计
前面我们已经说过液位对于整个系统的重要性,这里我们就不做叙述了。汽包水位的控制手段主要是控制给水量,基于这一原理我们可以用汽包的液位去控制给水量,这样构成的是单回路控制系统。但是由于这样控制下,控制效果并不理想,所以我们可以再引入饱和蒸汽温度这个量,蒸汽的温度越高说明炉膛内的压力越大,这样产生的热量就越多,所以自然而然需要的水量就要增加,所以我们可以用汽包液位与饱和蒸汽温度组成串级控制系统这样可以满足汽包液位在一定的稳定状态下。如图4.1所示:
图4.1 汽包水位控制简图
4.1.2燃烧控制系统的设计
现代锅炉中可以分为燃油锅炉和燃煤锅炉。本文所采用的是燃油锅炉。对于现代大型的燃油锅炉,多采用微正压燃烧。这样可以减少漏风,实现低氧燃烧,从而防止锅炉受热面积的腐蚀和污染等。由于低氧燃烧时过剩空气系数很小,在符合变动时更应该注意燃料量与空气量的配合恰当,否则会产生不完全燃烧,引起炉膛爆炸,受热面污染,尾部再燃等事故。因此燃烧系统对于压力的稳定要求很高,所以我们可以考虑用压力去控制燃烧,在本文中我们采用的是炉膛负压与饱和蒸汽压力组成串级控制去控制燃烧系统。前面我们也介绍过主蒸汽(饱和蒸汽)和炉膛压力对整个燃烧系统的重要性这里就不做叙述。但是用这两个量去控
制燃烧系统安全是没有问题,但是要做到经济燃烧却是很难。基于这一点我们还
要控制送风量,在这里我们选用主蒸汽(饱和蒸汽)的压力去控制送风量。如图
4.2所示是锅炉燃烧控制的简图。
图4.2 锅炉燃烧系统简图
4.1.3过热蒸汽温度控制
过热蒸汽的温度是锅炉生产过程的重要参数,一般由锅炉和汽轮机生产的工艺确定。从安全生产和经济技术指标上看,必须控制过热蒸汽温度在允许范围之内。需要指出的是,由于不同的工艺情况,过热蒸汽温度被控过程的控制难度具有极大的差异,假若减温器采用混合器,而且在减温器出口有允许安装测温元件,对于这种情况我们就采用如图4.3的控制方案,这样能得到满意的控制效果。这个方案是两个温度的串级控制,但是该方案设计的前提是减温器到过热器之间有
预留孔,允许安装测温元件去测量温度[11]。
图4.3 过热蒸汽温度控制简图
第7章 结束语
基于组态软件(MCGS)的锅炉监控系统具有以下几个特点:
1 控制功能完善,系统不仅能完成更加复杂的计算,逻辑控制,还加入了锅炉控制信息控制系统,保留了锅炉运行的历史曲线,实时曲线,报警显示,数据存贮,为锅炉的安全运行以及维修技术改造提供了依据。
2 集中显示操作,微机显示屏取代了庞大的现实操作盘,过程信号以多种画面或数据形式显示,运行员利用键盘操作,实现集中管理大大提高了锅炉系统的效率,减少了错误操作。
3 系统拓展灵活,应用微机技术,各种功能主要依靠软件通过公用软件完成,修改控制方案时只需要改软接线即可,系统升级更加灵活。综上所述,基于组态软件的锅炉监控控制系统是现在很实用经济的控制实施方式。
参考文献
[1] 赵钦新. 工业锅炉安全经济运行[M]. 北京:中国标准出版社, .
[2] 张占龙, 文代刚. 工业锅炉计算机网络化自动监测与控制技术[J]. 渝州大学学报, ,16(2): 8-10.
[3] 王洪国. 自动控制技术在工业锅炉上的应用[J]. 云南冶金, 1999,28(3): 50-54.
[4] 谭绍勇. STD工控机工业锅炉控制系统[J]. 计算机术与自动化,1995,14(2): 46-50.
[5] 王树青,王新民,田学民. 工业过程控制工程[M]. 北京:化学工业出版社,.
[6] 敖晨虹,胡海兰,周丽君. 先进控制与优化控制在过程工业应用中若干问题探讨[J]. 石油化工自动化,, 2(5): 28-30.
[7] 姜铁源,张来仁,王伟. 多台工业锅炉微机控制系统[J]. 黑龙江自动化技术与应用,1999,18(4): 26-28.
[8] 郭顺京. PC总线实验锅炉控制系统的研究[D]. 焦作: 河南理工大学化学,.
[9] 徐志良,宋志强,吴晓蓓.过程控制实验监控软件的开发[J]. 计算机工程,2002, 6: 263-266.
[10]Lennartson, Betal. Hybrid systems in process control[J]. IEEE Control Systems Magazine, , 16(5): 45C56.
[11]Li H. X, Guan S. Hybrid intelligent control strategy[J]. IEEE Control Systems Magazine, , 21(3): 36C48.
[12]Lu Y Z, He M, Xu C W. Fuzzy modeling and expert optimization control for industrial process[J]. IEEE Transactions on Control System Technology, , 5(1):44C50.
[13]陈曾汉. 工业PC及测控系统[M]. 北京: 机械工业出版社,.
致 谢
在论文工作即将结束之际,在此向我的导师苏成利老师表示深深地感谢。在学习期间,能遇到这样学识渊博的好导师,我感到非常的幸运。在我做论文期间,苏成利老师给予了悉心指导,从论文的整体方向确定到具体步骤的实施,他都给予我细心的帮助,经常在百忙之中抽出时间为我指导,在理论上给我指明方向,在实践中为我解答疑问。尤其在平时的学习和工作中,苏成利老师严谨的治学态度,实事求是的工作作风,甘于奉献的高尚品德给我留下了深刻的印象,成为我终生学习的楷模。
篇2:锅炉毕业论文
引 言
随着科学技术的发展,自动控制在现代工业中起着主要的作用,目前已广泛应用于工农业生产及其他建设方面。生产过程自动化是保持生产稳定、降低成本、改善劳动成本、促进文明生产、保证生产安全和提高劳动生产率的重要手段,是20世纪科学与技术进步的特征,是工业现代化的标志之一。可以说,自动化水平是衡量一个国家的生产技术和科学水平先进与否的一项重要标志。电力工业中电厂热工生产过程自动化技术相对于其他民用工业部门有较长的历史和较高的自动化水平,电厂热工自动化水平的高低是衡量电厂生产技术的先进与否和企业现代化的重要标志。
本次毕业设计的主要是针对单元机组汽温控制系统的设计。锅炉汽温控制系统主要包括过热蒸汽和再热蒸汽温度的调节。主蒸汽温度与再热蒸汽温度的稳定对机组的安全经济运行是非常重要的。过热蒸汽温度控制的任务是维持过热器出口蒸汽温度在允许的范围之内,并保护过热器,使其管壁温度不超过允许的工作温度。过热蒸汽温度是锅炉汽水系统中的温度最高点,蒸汽温度过高会使过热器管壁金属强度下降,以至烧坏过热器的高温段,严重影响安全。一般规定过热器的温度与规定值的暂时偏差不超过±10℃,长期偏差不超过±5℃。
如果过热蒸汽温度偏低,则会降低电厂的工作效率,据估计,温度每降低5℃,热经济性将下降约1%;且汽温偏低会使汽轮机尾部蒸汽温度升高,甚至使之带水,严重影响汽轮机的安全运行。一般规定过热汽温下限不低于其额定值10℃。通常,高参数电厂都要求保持过热汽温在540℃的范围内。
由于汽温对象的复杂性,给汽温控制带来许多的困难,其主要难点表现在以下几个方面:
(1)影响汽温变化的因素很多,例如,蒸汽负荷、减温水
量、烟气侧的过剩空气系数和火焰中心位置、燃料成分等都可能引起汽温变化。
(2)汽温对象具有大延迟、大惯性的特点,尤其随着机组容量和参数的增加,蒸汽的过热受热面的比例加大,使其延迟和惯性更大,从而进一步加大了汽温控制的难度。
(3)汽温对象在各种扰动作用下(如负荷、工况变化等)反映出非线性、时变等特性,使其控制的难度加大。
第一章 汽温控制系统的组成与对象动态特性
本章将以330MW的单元机组锅炉为例,通过研究其高温、亚临界压力、中间再热、自然循环、单炉膛前后对冲燃烧、燃煤粉汽包炉,且汽轮机为单轴、三缸、两排汽、再热、凝汽冲动式,说明过热器与再热器在锅炉中的位置及布置情况,从而全面掌握研究对象的生产过程,并熟悉其动态特性及分析影响汽温变化的各种因素。
1.1 过热器的分类及基本结构
1.1.1 过热器的分类
过热器可以根据它所采用的传热方式分为对流过热器、半辐射过热器及辐射过热器三种。对流过热器是放在炉膛外面对流烟道里的过热器,它主要以对流传热方式吸收流过它的烟气的热量。半辐射过热器也称屏式过热器,一般放在炉膛上部出口附近,它既吸收炉膛火焰的辐射热,又以对流方式吸收流过它的烟气的热量。辐射过热器是放在炉顶或炉墙上的过热器,它基本上只吸收炉膛内火焰和烟气的辐射热。
现代大容量高参数锅炉的过热器主要由对流过热器,屏式过热器,包覆过热器,顶棚过热器,联箱及减温器构成。制造它们的材料一般都是合金钢,有的还需用特种钢来制造。
(1)对流过热器:布置在烟道内,依靠热烟气对流传热的过热器,称为对流式过热器。对流过热器是由联箱和很多细长
的蛇形管束所组成。蛇形管可作立式或卧式布置。过热器的进出口联箱放在炉墙外部,起着分配和汇集蒸汽的作用。蛇形管与联箱上的管接头焊接在一起。
大容量锅炉的对流过热器布置在烟温很高的区域内,其蒸汽温度和管壁的热负荷都很高。而蒸汽侧放热系数比省煤器中的水或蒸发受热面中的汽水混合物的放热系数都低的多,因此过热器受热面必须用具有良好的高温强度特性的优质碳素钢或含有铬、钼、钒的耐热合金钢制造。过热器管子用什么材料制造,取决于它所处的工作条件。现代锅炉对流过热器多采用立式布置,因为这样可以采用简单可靠的悬吊固定方法,而卧式过热器的固定比较困难。立式布置的主要缺点,是停炉时积存在管内的凝结水不易排出,容易引起蛇形管下部弯头腐蚀。
(2)辐射过热器:辐射过热器可布置在燃烧室四壁,也称墙式或壁式过热器,或布置在炉顶,称顶棚过热器,直接吸收辐射热。在做墙式布置时辐射过热器的管子可以布置在燃烧室四壁的任一面墙上,可以仅布置在燃烧室上部,也可以沿燃烧室高度全部布置;它可以集中布置在某一区域,也可以与蒸发受热面管子间隔布置。
在自然循环锅炉中,辐射过热器管子布置在燃烧室上部,能使管子避开热负荷最高的火焰中心区域。但是这种布置会使水冷壁管的吸热高度降低,可能影响水循环的安全性。如果辐射过热器沿燃烧室全部高度布置,则处于火焰中心区的管子容易过热烧坏。特别是升火过程中,为保证管子的冷却必须采取从外界引进蒸汽等专门措施。在直流锅炉中,情况有所不同,水冷壁上部都有一定的过热度,相当于辐射过热器,由于上部炉温较低,所以可保证安全。
在国产自然循环锅炉中,未采用墙式布置的辐射过热器,而多采用布置在炉顶的顶棚过热器,受热面为紧靠炉顶的直管,称为顶棚管。这种过热器的辐射传热作用较墙式过热器为弱,但因处于较低的烟气温度场,工作比较安全可靠,与屏式过热器和包覆过热器配合使用,效果较好。
(3)屏式过热器和包覆过热器
除了上述两种过热器外,还有一种介于两者之间的半辐射过热器。最常用的半辐射过热器是布置在燃烧室上部或出口处的高温烟区内的屏式过热器。其结构特征为几排拉稀的管屏。屏式过热器沿炉宽平行布置,管屏数目一般为8―16片,屏片间距为0.5―2米,各跟管子之间的相对间距S2/d在1.1左右,屏中并联管子的数目为15―30跟。管屏悬挂在炉顶的钢梁上,受热后能自由的向下膨胀。为了保持各屏间的节距,可将相临两屏中的若干对管子弯绕出来互相夹持在一起,而各屏本身的管子也应夹持在同一平面上。屏式过热器布置在对流过热器前面,以降低对流过热器入口烟温,避免对流过热器结渣。屏式过热器的汽温变化特性介于辐射与对流过热器之间,所以变化也比较平稳。
图1-1是布置在不同烟温区域内的过热器的汽温特性示意图。从图中可以看出,当锅炉负荷从33%增加到满负荷时,曲线1所示的屏式过热器的汽温变化非常平稳,仅上升了10℃;曲线2和3所示的对流过热器的汽温上升了42℃和50℃;而曲线4代表的辐射过热器的汽温却大幅下降了。由于屏式过热器具有过热汽温平稳的特点,在现代大型锅炉上广泛地采用了这种过热器。
为了得到较好的传热效果,最好把屏式过热器布置在烟温为950―1050℃的烟道中。屏式过热器进口烟温的选择,应保证燃料进入屏式过热器前已燃尽,否则在屏区再燃烧会严重影响管屏的工作安全。根据已采用屏式过热器的许多锅炉运行实践证明,它能够在1000―1300℃烟温区内可靠工作,并具有良好的汽温变化特性。
1.1.2 过热器的基本结构
图1-1 布置在不同烟温区域内的过热器气温特性
1-布置在烟温1200℃区域的屏式过热器;2、3-布置在烟温为
1000℃
和900℃区域内的对流过热器;4-布置在燃烧室内的辐射过热器
300MW单元机组是现在是我国火力发电机组的主力型号,多采用亚临界参数及中间再热。330MW机组锅炉的过热器,具体结构见图1-4所示。此过热器具有以下特点:由于过热蒸汽参数高,需要布置更多受热面,因此炉膛内布置大量屏式过热器。采用辐射式、半辐射式和对流过热器联合过热系统,以获得良好的过热蒸汽温度变化特性。低温过热器采用逆流布置,以便获得较大的传热温差,从而节约钢材。
采用两级喷水减温,这样做的目的有两个,一是为了使汽温调节更灵敏,减小热惯性,二是为了保护过热器。第一级喷水减温器布置在前屏过热器之后,调节量较大且调节惰性大,用来调节因负荷、给水温度和燃料性质变化而引起的汽温变化,为粗调。另外它还有保护屏式过热器和对流过热器受热面的作用。第二级喷水减温器布置在高温对流过热器(末级过热器)之前,这一级热惯性小,可保证出口汽温能得到迅速调节。减温器共有四只,每级安装两只,每只喷水量为每级喷水量的一
半。减温水源为自制冷凝水。
蒸汽流程为:饱和蒸汽由汽包引出后经一部分顶棚过热器进入侧墙和后墙包覆过热器,流出后在联箱内混合,进入低温对流过热器,出来后再经过另一部分顶棚过热器进入前屏过热器,流出后经过第一级喷水减温器减温,再进入后屏过热器,流出后经过第二级减温器减温,进入高温对流过热器完成最后一次过热后,送往汽轮机。
图1-2 300MW机组过热器系统图
1-汽包;2-前屏过热器;3-后屏过热器;4-顶棚过热器; 5-侧墙包覆过热器;6-后墙包覆过热器;7-低温对流过热器; 8-第一级减温器;9-第二级减温器;10-高温对流过热器
1.2 过热蒸汽温度控制的意义与任务
锅炉过热蒸汽温度是影响机组生产过程安全性和经济性的重要参数。现代锅炉的过热器是在高温、高压的条件下工作的,过热器出口的过热蒸汽温度是机组整个汽水行程中工质温度的最高点,也是金属壁温的最高处。过热器采用的是耐高温高压的合金刚材料,过热器正常运行的温度已接近材料所允许的最
高温度。如果过热蒸汽温度过高,容易损坏过热器,也会使蒸汽管道、汽轮机内某些零部件产生过大的热膨胀而毁坏,影响机组的安全运行。如果过热蒸汽温度过低,将会降低机组的热效率,一般蒸汽温度降低5-10℃,热效率约降低1%,不仅增加燃料的消耗量,浪费能源,而且还将使汽轮机最后几级的蒸汽湿度增加,加速汽轮机叶片的水蚀。另外,过热汽温的降低还会导致汽轮机高压级部分蒸汽的焓值减小,引起反动度增大,轴向推力增大,也对汽轮机安全运行带来不利的影响。所以,过热蒸汽温度过高或过低都是生产过程所不允许的。
1.3 过热蒸汽温度控制对象的动静态特性
1.3.1 静态特性
1、锅炉负荷与过热汽温的关系
锅炉负荷增加时,炉膛燃烧的燃料增加,但是,炉膛中的最高的温度没有多大的变化,炉膛辐射放热量相对变化不大,因此炉膛温度增高不大。这就是说负荷增加时每千克燃料的辐射放热百分率减少,而在炉膛后的对流热区中,由于烟温和烟速的提高,每千克燃料的对流放热百分率将增大。因此,对于对流式过热器来说,当锅炉的负荷增加时,会使出口汽温的稳态值升高;辐射式过热器则具有相反的汽温特性,即当锅炉的负荷增加时,会使出口汽温的稳态值降低。如果两种过热器串联配合,可以取得较平坦的汽温特性,但一般在采用这两种过热器串联的锅炉中,过热器出口蒸汽温度在某个负荷范围内,仍随锅炉负荷的增加有所升高。
2、过剩空气系数与过热汽温的静态关系
过剩空气量改变时,燃烧生成的烟气量改变,因而所有对流受热面吸热随之改变,而且对离炉膛出口较远的受热面影响显著。因此,当增大过剩空气量时将使过热汽温上升。
3、给水温度与汽温关系
提高给水的温度,将使过热汽温下降,这是因为产生每千克蒸汽所需的燃料量减少了,流过过热器烟气也就减少了。也可以认为:提高给水温度后,在相同燃料下,锅炉的蒸发量增
加了,因此过热汽温将下降。则是否投入高压给水加热器将使给水温度相差很大,这对过热汽温有显著的影响。
4、燃烧器的运行方式与过热汽温的静态关系
在炉膛内投入高度不同的燃烧器或改变燃烧器的摆角会影响炉内温度分布和炉膛出口烟温,因而也会影响过热汽温,火焰中心相对提高时,过热汽温将升高。
1.3.2 动态特性
目前,火电机组厂广泛采用喷水减温方式来控制过热蒸汽温度。影响汽温变化的因素很多,但主要有蒸汽流量、烟气传热量和减温水量等。在各种扰动下,汽温控制对象是有烟池、惯性和自平衡能力的。
1、蒸汽流量扰动下的蒸汽温度对象的动态特性
大型锅炉都采用复合式过热器,当锅炉负荷增加时,锅炉燃烧率增加,通过对流式过热器的烟气量增加,而且烟气温度也随负荷的增大而升高。这两个因素都使对流式过热器的气温升高。然而,当负荷增加时,炉膛温度升高的并不明显,由炉膛辐射传给过热器的热量比锅炉蒸汽量增加所需热量少,因此使辐射式过热器出口温度下降。可见,这两种型式的过热器对蒸汽流量的扰动的反映恰好相反,只要设计上配合得当,就能使过热其出口汽温随蒸汽流量变化的影响减小。因此在生产实践中,通常把对流式过热器与辐射式过热器结合使用,还增设屏式过热器,且对流方式下吸收的热量比辐射方式下吸收的热量多,综合而言,过热器出口汽温是随流量D的增加而升高的。动态特性曲线如图1-3(a)所示。
蒸汽流量扰动时,沿过热器长度上各点的温度几乎是同时变化的,延迟时间较小,约为15s左右。
图1-3 在扰动下温度的变化曲线
2、烟气侧热量扰动下蒸汽温度对象的动态特性
当燃料量、送风量或煤种等发生变化时,都会引起烟气流速和烟气温度的变化,从而改变了传热情况,导致过热器出口温度的变化。由于烟气传热量的改变是沿着整个过热器长度方向上同时发生的,因此汽温变化的迟延很小,一般在15-25s之间。烟气侧扰动的汽温响应曲线如图1-3(a)所示。它与蒸汽量扰动下的情况类似。
3、蒸汽温度在减温水量扰动下的动态特性
当减温水量发生扰动时,虽然减温器出口处汽温已发生变化,但要经过较长的过热器管道才能使出口汽温发生变化,其扰动地点(过热器入口)与测量蒸汽温度的地点(过热器出口)之间有着较大的距离,此时过热器是一个有纯滞后的多容对象。.动态曲线图如图1-3(b)所示。当扰动发生后,要隔较长时间才能是蒸汽温度发生变化,滞后时间比较大,滞后时间约为30-60s。
综上所述,可归纳出以下几点:
(1)过热器出口蒸汽温度对象不管在哪一种扰动下都有延迟和惯性,有自平衡能力。而且改变任何一个输入参数(扰动),
其他的输入参数都可能直接或间接的影响出口蒸汽温度,这使得控制对象的动态过程十分复杂。
(2)在减温水流量扰动下,过热器出口蒸汽温度对象具有较大的传递滞后和容量滞后,缩减减温器与蒸汽温度控制点之间的距离,可以改善其动态特性。
(3)在烟气侧热量和蒸汽流量扰动下,蒸汽温度控制对象的动态特性比较好。
1.4 过热蒸汽温度控制系统的基本结构与工作原理
这里以330MW机组分散控制系统的过热蒸汽温度控制系统为例,对其系统结构和工作原理进行介绍。
该330MW机组的过热蒸汽温度控制采用二级喷水减温控制方式。过热器设计成两级喷水减温方式,除可以有效减小过热蒸汽温度在基本扰动下的延迟,改善过热蒸汽温度的调节品质外,第一级喷水减温还具有防止屏式过热器超温、确保机组安全运行的作用。
本机组过热器一、二级喷水减温器的控制目标就是在机组不同负荷下维持锅炉二级减温器入口和二级减温器出口的蒸汽温度为设定值。
1.4.1 过热器一级减温控制系统
过热器一级减温控制系统的原理简图如图1-4所示。该系统是在一个串级双回路控制系统的基础上,引入前馈信号和防超温保护回路而形成喷水减温控制系统。主回路的被控量为二级减温器入口的蒸汽温度,其实测值送入主回路与其给定值进行比较,形成二级减温器入口蒸汽温度的偏差信号。主回路的给定值由代表机组负荷的主蒸汽流量信号(代表机组负荷信号)经函数器f(x)产生,其含义为给定值是负荷的函数。运行人员在操作员站上可对此给定值给予正负偏置。主回路的控制由
PID1来完成。主回路控制器接受二级减温器入口蒸汽温度偏差信号,经控制运算后其输出送至副回路。
副回路的被控量为一级减温器出口的蒸汽温度。其温度的测量值送入副回路与其给定值进行比较,形成一级减温器出口蒸汽温度的偏差信号。副回路的给定值是由主回路控制器的输出与前馈信号叠加形成。副回路采用PID2调节器,它接受一级减温器出口蒸汽温度的偏差信号。
图1-4 过热器一级减温控制系统
由于机组的负荷会改变,控制对象的动态特性也随之而变,为了在较大的负荷变化范围内都具备较高的控制品质,在大型机组的蒸汽温度控制中,可充分利用计算机分散控制的优点,
将主、副调节器设计成自动随着负荷的变化不断地修改整定参数的调节器,上述蒸汽温度控制系统就是如此。
1.4.2 二级减温控制系统
过热器二级减温控制系统的原理简图如图1-5所示。该系统与一级减温控制系统的结构基本相同,也是一个串级双回路控制系统,不同之处在于:主、副调节器输入的偏差信号不同,采用的前馈信号也不同。
二级减温控制系统的主回路的被控量为二级过热器的出口蒸汽温度,该蒸汽温度与主回路的给定值进行比较,形成二级过热器出口蒸汽温度偏差信号,主回路的给定值由运行人员手动设定,对于300MW机组在正常负荷时,给定值一般为540℃。
图1-5 过热器二级减温控制系统
副回路的被控量为二级减温器出口蒸汽温度,其温度的测量值送入副回路与其给定值比较,形成二级减温器出口蒸汽温度的偏差信号。副回路给定值是上主回路控制器的输出与前馈信号叠加而形成的。
二级过热器蒸汽温度控制是锅炉出口蒸汽温度的最后一道控制手段,为了保证汽轮机的安全运行,要求尽可能提高锅炉出口蒸汽温度的调节品质。因此,二级减温控制的主回路前馈信号采用了基于焓值计算的较为完善的方案。其前馈信号有主蒸汽温度和压力的给定值的函数,还有主蒸汽流量代表机组负荷以及送风量、燃烧器火嘴摆动倾角等。
除了以上内容外,二级减温控制系统的其他部分以及工作原理与一级减温控制系统完全相同。
1.5 再热汽温控制系统
1.5.1 再热汽温控制的任务
为了提高大容量、高参数机组的循环效率,并防止汽轮机末级蒸汽带水,需采用中间再热系统。提高再热汽温对于提高循环热效率是十分重要的,但受金属材料的限制,目前一般机组的再热蒸汽温度都控制在560℃以下。另一方面,在锅炉运行中,再热器出口温度更容易受到负荷和燃烧工况等因素的影响而发生变化,而且变化的幅度也较大,如果不进行控制,可能造成中压缸转子与汽缸较大的热变形,引起汽轮机振动。
再热蒸汽温度控制系统的任务是将再热蒸汽温度稳定在设定之上。此外,在低负荷、机组甩负荷或汽轮机跳闸时,保护再热器不超温,以保证机组的安全运行。
1.5.2 再热汽温的控制方法
再热蒸汽温度调节采用摆动火嘴加喷水减温的控制方式。 按设计,再热蒸汽温度正常情况下由喷燃器火嘴倾角的摆动来控制。也就是说,再热器汽温控制的减温水阀门平常是全关的,它对再热汽温只起一种辅助的或保护性质的调节作用。
1、摆动火嘴:
摆动燃烧器火嘴倾角是设计用来调节再热汽温的正常手段,它是一个带前馈信号的单回路调节系统。在锅炉A,B侧末级再热器出口联箱上各装有两个出口蒸汽温度测点,可由运行人员在OIS上手动选择每侧的某一测点或两个测点的平均值作为本次再热汽温控制使用。
根据主蒸汽流量经函数发生器给出的随机组负荷变化的再热汽温设定值,与运行人员手动设定值经小值选择器后与再热蒸汽测量值进行比较,偏差进入控制器。控制器设计为SMITH预估器和PID调节器互相切换的方式,两者只能由一个起控制作用,可由热控工程师通过软件调节。为了提高再热汽温在外扰下的调节品质,控制回路设计了机组负荷和送风量经函数发生器给出的前馈信号。根据再热汽温的偏差经控制器的控制运算后在加上前馈信号,形成了对燃烧器火嘴倾角的控制指令,这个指令信号分四路并列输出去驱动炉膛四角的燃烧器火嘴倾角。当进行炉膛吹扫时,火嘴倾角将被自动连锁到水平位置。
2、喷水减温:
喷水减温只起辅助或保护性质的减温作用。每侧的再热汽温有两个测量信号,当摆动火嘴在自动控制状态时,喷水减温的再热汽温设定在摆动火嘴控制系统设定值的基础上加上根据摆动火嘴控制指令经函数发生器给出的偏置量,意在当摆动火嘴有调节与低时抬高喷水减温控制系统设定值以确保喷水减温阀门关死。当摆动火嘴控制指令接近下限而将失去调节余地时,该偏置量应该减小到零以便再热汽温偏高时喷水阀门接替摆动火嘴的减温手段。
由于喷水减温系统只是设计用作辅助调节手段,故系统设计比较简单,再热汽温设定值与测量值的偏差经PID调节器后直接作为喷水减温阀门开度指令,控制器未设计SMITH预估器,也未设计任何前馈信号。
图1-6 再热汽温控制SAMA图
1.6 汽温调节的概念和方法
维持稳定的汽温是保证机组安全和经济运行所必须的。汽温过高会使金属应力下降,将影响机组的安全运行;汽温降低则会机组的循环的效率。据计算,过热器在超温10℃到20℃下长期运行,其寿命会缩短一半;而汽温降低10℃会使循环若效应降低0.5%,运行中一般规定汽温额定值的波动不能超过-10℃~+5℃。因此,要求锅炉设置适当的调温手段,以修正运
行因素对汽温波动的影响。
对汽温调节方法的基本要求是:调节惯性或延迟时间小,调节范围大,对热循环热效率影响小,结构简单可靠及附加设备消耗少。
汽温的调节可归结为两大类:蒸汽侧的调节和烟气侧的调节。所谓蒸汽侧的调节,是指通过改变蒸汽的热焓来调节温度。例如喷水式减温器向过热器中喷水,喷入的水的加热和蒸发要消耗过热蒸汽的一部分热量,从而使汽温下降,调节喷入的水量,可以达到调节汽温的目的。烟气侧的调节,使通过改变锅炉内辐射受热面和对流受热面的吸热量分配比例的方法(例如调节燃烧器的倾角,采用烟气再循环等)或改变流经过热器的烟气量的方法(如调节烟气挡板)来调节过热蒸汽温度。
1.6.1 从蒸汽侧调节汽温
汽温调节通常采用喷水减温作为主要调节手段。由于锅炉给水品质较高,所以减温器通常采用给水作为冷却工质。喷水减温的方法是将水呈雾状直接喷射到被调过热蒸汽中去与之混合,吸收过热蒸汽的热量使本身加热,蒸发,过热,最后也成为过热蒸汽的一部分。被调温的过热蒸汽由于放热,所以汽温降低,达到了调温的目的。
喷水减温调节操作简单,只要根据汽温的变化适当的变更相应的减温水调节阀门开度,改变进入减温器的减温水量即可达到调节过热汽温的目的。当汽温偏高时,开大调节门增加减温水量;当汽温偏低时,关小调节阀门减少减温水量,或者根据需要将减温器撤出运行。
单元机组的锅炉对汽温要求较高,故通常装置两级以上的喷水减温器,在进行汽温调节时必须明确每级减温器所担负的任务。第一级布置在分隔屏过热器之前,被调参数是屏式过热器出口汽温,其主要任务是保护屏式过热器,防止壁管超温。由于该减温器距末级过热器的出口尚有较长距离,相对来说,它对出口汽温的调节时滞较大,而且由于蒸汽流经后几级过热器后,汽温的变化幅度较大,误差也大,所以很难保证出口蒸
汽温度在规定的范围内。因此,这级减温器只能作为主蒸汽温度的粗调节。该锅炉第二级喷水减温器设在末级对流过热器进口,被调参数是主蒸汽出口温度,由于此处距主蒸汽出口距离近,且此后蒸汽温度变化幅度也不大,所以第二级喷水减温的灵敏度高,调节时滞也小,能有效的保证主蒸汽出口温度符合要求,因而该级喷水调节是主蒸汽的细调节。第二级喷水减温器往往分两侧布置,以减小过热汽温热偏差。正常工况时,一、二级喷水量的比例为总喷水量的75%和25%,在高加全部切除时,其比例为95%和5%。
喷水减温器调节汽温的特点是,只能使蒸汽减温而不能升温。因此,锅炉按锅炉额定负荷设计时,过热器受热面的面积是超过需要的,也就是说,锅炉在额定负荷下运行时过热器吸收的热量将大于蒸汽所需要的过热热量,这时就必须用减温水来降低蒸汽的温度使之保持额定值。由于一般组合过热器汽温特性都呈对流特性,所以当锅炉负荷降低时,汽温也下降,这时减温水就应减小,对于定压运行的单元机组,由于蒸汽失去汽温调节手段,因而主汽温就不能保持规定值,故锅炉不宜在此情况下做定压运行,而应采用滑压运行,以保证过热蒸汽有足够的过热度。喷水减温调节主蒸汽温度在经济上是有一定损失的。一方面由于在额定负荷时过热器受热面积比实际需要值大,增加了投资成本;另一方面因一部分给水用作减温水,使进入生煤器的水流量减少,因而锅炉排烟温度升高。增加了排烟损失。同时喷水减温的过程,也是一个熵增的过程。故而有可用能的损失。但是,由于喷水减温设备简单,操作方便,调节又灵敏,所以仍得到广泛应用。
再热器不宜采用喷水减温调节汽温。因为喷水减温器将增加再热蒸汽的数量,从而增加了汽轮机中,低压缸的蒸汽流量,即增加了中低压缸的出力。如果机组的负荷一定,将使高压缸出力减小,减少高压缸的蒸汽流量。这就等于部分的用低压蒸汽循环代替高压蒸汽循环做功,因而必然导致整个机组热经济性的降低。再热器喷水减温器的主要目的是当出现事故工况,
再热器入口汽温超过允许值,可能出现超温损坏时,喷水减温器投入运行,借以保护再热器。在正常运行情况下,只有当采用其他温度调节方法尚不能完全满足要求时,再热器喷水减温器才投入微量喷水,作为再热汽温的辅助调节。
1.6.2 从烟气侧调节汽温
1、改变火焰中心位置。改变火焰的中心位置可以改变炉内辐射吸热量和进入过热器的烟气速度,因而可以调节过热汽温。当火焰中心位置抬高时,火焰离过热器较近,炉内辐射吸热量减少,炉膛出口烟温升高,则过热汽温将升高。火焰中心位置降低时,则过热汽温降低。改变火焰中心位置的方法有:
(1)调整喷燃器的倾角。采用摆动式燃烧器时,可以用改变其倾角的办法来改变火焰中心沿炉膛高度的位置,从而达到调节汽温的目的。在高负荷时,将喷燃器向下倾斜某一角度,可以使火焰中心位置下移,使进入过热器区的烟气温度下降,减小过热器的传热温差,使汽温降低。而在低负荷时,将喷燃器向上倾斜适当角度,则可以使火焰中心位置提高,使汽温升高。摆动式燃烧器的调温幅度较大,调节灵敏,设备简单,投资费用少,并且没有功率损耗。目前使用的摆动式燃烧器上下摆动的转角为±20°,一般用10°~20°器的倾角的调节范围不可过大,否则可能会增大不完全燃烧损失或造成结渣等。如果向下的倾角过大时,可能会造成水冷壁下部或冷灰斗结渣。若向上的倾角过大时,会增加不完全燃烧损失并可能引起炉膛出口的屏式过热器或凝渣管结渣。同时在低负荷时若向上的倾角过大,还可能发生炉膛灭火。摆动式燃烧器可用于过热蒸汽的调温,也可用于再热蒸汽的调温。当摆动式燃烧器作为再热汽温的主调方式时,它将以再热汽温为信号,改变燃烧器的倾角。 为了保持炉膛火焰的均匀分布,此时四组燃烧器的倾角应一致并同时动作。当燃烧器倾角已达到最低极限值时,再热汽温仍然高于额定值时,再热器事故喷水减温器将自动投入运行,以保持汽温和保护再热器。
(2)改变喷燃器的运行方式。当沿炉膛高度布置有多排喷
燃器时,可以将不同高度的喷燃器组投入或停止工作,即通过上、下排喷燃器的切换,来改变火焰中心位置。当汽温高时应尽量先投用下排的燃烧器,汽温低时可切换成上排喷燃器运行,也可以采取对距过热器位置不同的喷燃器进行切换的方法,当投用靠近炉膛后墙的喷燃器时,由于这时火焰中心位置离过热器近火焰行程短,将使炉膛出口的烟温相对的高些。而切换成前墙或靠近前墙的喷燃器运行时,则火焰中心位置离过热器相对的远些,炉膛出口烟温就相对的低些。
(3)变化配风工况。对于四角布置切圆燃烧方式,在总风量不变的情况下,可以用改变上、下排二次风分配比例的办法来改变火焰中心位置。当汽温高时,一般可开大上排二次风,关小下排二次风,以压低火焰中心。当汽温低时,一般则关小上排二次风,开大下排二次风,以抬高火焰中心。进行调整时,应根据实际设备的具体特性灵活掌握。
2、改变烟气量。若改变流经过热器的烟气量,则烟气流速必然改变,使对流传热系数变化,从而改变了烟气对过热器的放热量。烟气量增多时,烟气流速大,使汽温升高;烟气量减少时,烟气流速小,使汽温降低。改变烟气量即改变烟气流速的方法有:
(1)采用烟气再循环。采用烟气再循环调节汽温的原理是从尾部烟道(通常是从省煤器后)抽出一部分低温烟气,用再循环风机送回炉膛,并通过对再循环烟气量的调节来改变流经过热器的烟气流量,改变烟气流速。此外,当送入炉膛的低温再循环烟气量改变时,还使炉膛温度发生变化,炉内辐射吸热与对流吸热的比例将改变,从而使汽温发生变化。由此,改变再循环烟气量,可以同时改变流过过热器的烟气流量和烟气含热量,因而可以调节汽温。
(2)烟气旁路调节。采用这种方法是将过热器处的对流烟道分隔成主烟道和旁路烟道两部分。在旁路烟道中的受热面之后装有烟气挡板,调节烟气挡板的开度,即可改变通过主烟道的烟气流速,从而改变主烟道中受热面的吸热量。由于高温对
流烟道中烟气的温度很高,烟气挡板极易变形或烧坏,故这一方法只用于布置在锅炉尾部对流烟道中的低温过热器或低温再热区段,而在我国目前的超高压机组中,则仅用于低温再热器区段。采用烟气旁路来调节再热汽温时,还会影响到过热汽温。为了增加再热汽温的调节幅度并减小对过热汽温的影响,应使主烟道中的再热器有较大的受热面,而旁路烟道中的过热器受热面则应小些。
(3)调节送风量。调节送风量可以改变流经过热器的烟气量,即改变烟气流速,达到调节过热汽温的目的。调节送风量首先必须满足燃烧工况的要求,以保证锅炉机组运行的安全性和经济性。而用以调节汽温,一般知识作为辅助手段。当汽温问题成为运行中的主要矛盾时,才用燃烧调节来配合调节汽温。利用送风量调节汽温是有限度的,超过了范围将造成不良后果。因为过多的送风量不但增加了送、吸风机是耗电量,降低了电厂的经济性,而且增大了排烟热损失,降低锅炉热效率。特别是燃油锅炉对过剩空气量的控制就更为重要。过剩空气量的增加,不但加速空气预热器的腐蚀,还有可能引起可燃物在尾部受热面的堆积,导致尾部受热面再燃烧。
第二章 过热汽温控制系统的基本方案
目前,过热汽温的控制方案很多,而且随着自动控制技术和计算机技术的不断发展,新的控制方法不断出现,汽温控制的质量也不断提高。传统的汽温控制系统有两种:串级汽温控制系统和采用导前微分信号的汽温控制系统。由于过热汽温控制通道的迟延和惯性很大,被调量信号反应慢,因此选择减温器后的汽温作为局部反馈信号,形成了上述的两种双回路控制系统。下面将分别加以介绍。
2.1 串级汽温控制系统
单回路控制系统是各种复杂控制系统的基础,由于其控制简单而得到广泛应用。但随着工业技术的不断更新,生产不断强化,工业生产过程对工业参数提出了越来越严格的要求,并且由于生产过程中各参数间的关系复杂化及控制对象迟延和惯性的增大,都使得单回路控制系统显得无能为力,因而产生了许多新的.、较复杂的控制系统,如串级控制、导前微分控制、复合控制、分段控制、多变量控制等。串级控制系统对改善控制品质有独到之处,本节将对其组成、特点及整定进行讨论
2.1.1 串级汽温控制系统的基本结构及原理
火电厂过热汽温串级控制系统的结构图2-1所示:
图2-1 过热汽温串级控制系统
该汽温串级控制系统中,有主、副两个调节器。由于汽温对象具有较大的延迟和惯性,主调节器多采用PID控制规律,其输入偏差信号为I?2-I?0,输出信号为IT1,副调节器采用PI或P控制
规律,接受导前汽温信号I?1和主调节器输出信号IT1,输出为IT2。当过热汽温升高时,I?2增加,主调节器输出IT1减小,副调节器
输出IT2增加,减温水量增加,过热汽温下降。在主、副调节器
均具有PI控制规律的情况下,当系统达到稳定时,主、副调节器的输入偏差均为零,即:
I?2=I?0;I?1=IT1
由此也可以认为主调节器的输出IT1是导前汽温I?1的给定
值。
过热汽温串级控制系统的原理方框图如图2-2所示,具有内外两个回路。内回路由导前汽温变送器、副调节器、执行器、减温水调节阀及减温器组成;外回路由主汽温对象、汽温变送器、主调节器及整个内回路组成。系统中以减温器的喷水作为控制手段,因为减温器离过热器出口较远,且过热器管壁热容
较大,主汽温对象的滞后和惯性较大。若采用单回路控制主汽温q1(即将q1作为主信号反馈到调节器PI1,PI1直接去控阀门开
度)无法取得满意的控制品质。为此再取一个对减温水量变化反映快的中间温度信号q2作为导前信号,增加一个调节器PI2组成
如图2-2所示的串级控制系统。调节器PI2根据q2信号控制减温
水阀,如果有某种扰动使汽温q2比q1提早反映(例如:内扰为喷
水量W的自发性变化),那么由于PI2的提前动作,扰动引起的q2波动很快消除,从而使主汽温q1基本不受影响。另外,PI2的
给定值受调节器PI1的影响,后者根据q1改变q2的给定值,从而
保证负荷扰动时,仍能保持X满足要求。可见,串级系统中采用了两级调节器,各有其特殊任务。
图2-2 过热汽温串级控制系统的原理方框图
2.1.2 串级汽温控制系统的设计
为充分发挥串级控制系统的优点,在设计实施控制系统时,还应适当合理的设计主、副回路及选择主、副调节器的控制规律。
1、主、副回路的设计原则
(1)副参数的选择,应使副回路的时间常数小,控制通道短,反应灵敏。通常串级控制系统是被用来克服对象的容积迟延和惯性。副回路应该把生产系统的主要干扰包括在内,应力
求把变化幅度最大、最剧烈和最频繁的干扰包括在副回路内,以充分发挥副回路改善系统动态特性的作用,保证主参数的稳定。因此,在设计串级控制系统时,应设法找到一个反应灵敏的副参数,使得干扰在影响主参数之前就得到克服,副回路的这种超前控制作用,必然使控制质量有很大的提高。
(2)副回路应包含被控对象所受到的主要干扰。串级控制系统对进入副回路的扰动有很强的克服能力,为发挥这一特殊作用,在系统设计时,副参数的选择应使得副回路尽可能多的包括一些扰动。但这将与要求副回路控制通道短,反应快相矛盾,应在设计中加以协调。在具体情况下,副回路的范围应当多大,取决于整个对象的容积分布情况以及各种扰动影响的大小。副回路的范围也不是愈大愈好。太大了,副回路本身的控制性能就差,同时还可能使主回路的控制性能恶化。一般应使副回路的频率比主回路的频率高的多,当副回路的时间常数加在一起超过了主回路时,采用串级控制就没有什么效果了。
(3)主、副对象的时间常数应适当匹配。由于串级系统中主、副回路是两个相互独立又密切相关的回路。如果在某种干扰作用下,主参数的变化进入副回路时,会引起副回路中参数振幅增加,而副参数的变化传到主回路后,又迫使主参数变化幅度增大,如此循环往复,就会使主、副参数长时间大幅度波动,这就是所谓串级系统的“共振现象”。一旦发生了共振系统就失去控制,不仅使系统控制品质恶化,如不及时处理,甚至可能导致生产事故,引起严重后果。为确保串级系统不受共振现象的威胁,一般取
Td1??3~10?Td2
(2-1)
式子中:Td1为主回路的振荡周期;Td2为副回路振荡周期,要满
足式子(2-1),除了在副回路设计中加以考虑之外,还与主、副调节器的整定参数有关。
2、主、副调节器的选型
串级控制系统中,主调节器和副调节器的任务不同,对于
它们的选型即控制规律的选择也有不同考虑。
(1)副调节器的选型
副调节器的任务是要快速动作以迅速消除进入副回路内的扰动,而且副参数并不要求无差,所以一般都选P调节器,也可采用PD调节器,但这增加了系统的复杂性,在一般情况下,采用P调节器就足够了,如果主、副回路频率相差很大,也可以考虑采用PI调节器。
(2)主调节器的选型
主调节器的任务是准确保持被调量符合生产要求。凡是需采用串级控制的生产过程,对控制的品质都是很高的,不允许被调量存在静差。因此主调节器必须具有积分作用,一般都采用PI调节器。如果控制对象惰性区的容积数目较多,同时又有主要扰动落在副回路以外的话,就可以考虑采用PID调节器。
3、主、副回路调节器调节规律的选择原则
(1)主参数控制质量要求不十分严格,同时在对副参数的要求也不高的情况下,为使两者兼顾而采用串级控制方式时,主、副调节器均可以采用比例控制。
(2)要求主参数波动范围很小,且不允许有余差,此时副调节器可以采用比例控制,主调节器采用比例积分控制。
(3)主参数要求高,副参数亦有一定要求这时主、副调节器均采用比例积分形式。
2.1.3 串级汽温控制系统的整定
在如图2-3所示的串级系统中,因为两个调节器串在一起,在一个系统中工作,相互之间或多或少的有些影响,因此在串级系统的整定要比简单系统复杂些。
图2-3 串级控制系统方框图
1、两部整定法
当串级系统中副回路的控制过程比主回路快的多时,可按下述步骤分别独立整定主、副调节器参数。
(1)先整定副调节器
当副回路受到阶跃扰动时,在较短时间内副回路控制过程就告结束。在此期间,主回路基本上不参加动作,由图2-3得整定副回路时的方框图,如图2-4 (a)所示。可按单回路系统的整定方法整定副调节器WT2?s?。
(2)整定主调节器
当主回路进行控制时,副回路几乎起理想随动作用,由图2-3可得
R2(s)?Y2(s)Wm2(s)
从而求得副回路的闭和传递函数
Y2(s)1?R2(s)Wm2(s)
(2-2)
图2-4 主副调节器分别独立整定时的方框图
即在主回路中副回路可看作一个比例环节,由此画出整定主回路时的方框图,如图2-4(b)所示。可按单回路系统的整定方法整定主调节器WT1?s?的参数。
按上述步骤整定系统后,通常应满足?2?3?1(?1、?2分别为
主、副回路主导衰减振荡成分的频率)。要达到此要求整定时应考虑以下几个问题:
① 对象的动态特性。控制对象前区动态特性W02(s)与整个控制对象的动态特性W0(s)?W01(s)W02(s)相比,应有较小的迟延和惯性。
② 调节器类型的选择。副调节器WT2(s)可选用P(或PD)调节器,主调节器应选用PI调节器,以使副回路有较高的衰减振荡频率。
③ 整定指标的选择。副回路可取较低的稳定性裕量(例如
。 ??0.75)而主回路则取较高的稳定性裕度(例如??0.9)
另外,按此方法整定串级系统时还应考虑控制对象惰性区动态特性的求取。在图2-4中,控制对象导前区的特性W02(s)可直接由实验测得,而惰性区的特性W01(s)不一定能直接由实验获得,但整个控制对象的动态特性W0(s)?W01(s)W02(s)总是可以由实验测得,因此对象惰性区的动态特性W01(s)原则上可以由W0(s)和W02(s)算出:
W01(s)?W0(s)
W02(s)
(2-3)
例如:锅炉过热蒸汽温度控制对象及其导前区的动态特性常
可表示为W0(s)?W01(s)W02(s)?K0?1(s)??(s)(1?T0s)n0
(2-4)
W02(s)??2(s)K2??(s)(1?T2s)n2
(2-5)
式中:?为减温水阀门的开度。利用级数展开和低阶近似,惰性区的动态特征可表示为: W01(s)??1(s)??2(s)K1
(1?T1s)n1
(2-6)
式中 K1?K0;T1?nT
K2??nT;n1?n0T0?n2T2n0T02?n2T22200222?n0T0?n2T22
如果控制对象及其导前区动态特性可以用式(2-4)、(2-5)来表示,而且有n2?2和n0?3,那么当 n0T0?3n2T2时(n0T0和n2T2分别为W0(s)和W02(s)分母中s项的系数),可以满足主、副调节器按图2-4分别整定的条件,而惰性区对象表示为
W01(s)?K12?(1?T0s)n0(1?T0s)n0K0
(2-7)
这样避免了由W0(s)和W02(s)计算出W01(s)的麻烦,尤其用阶跃响应实验曲线整定主调节器时更为简便。因此在式(2-7)假定下
????????????Tc?0?Tc?1
(2-8)
式中:??/Tc?0为控制对性W0(s)阶跃响应实验曲线上?与Tc的比值,
它实际往往无法由实验曲线上直接获得(如在过汽温对象中)。
2、逐次逼近法
(1)先整定副调节器WT2(s)。在第一次整定副调节器时,断开主环,即按副回路单独工作时的单回路系统来整定副调节器WT2(s)的参数,记作?WT2(s)?1。
(2)根据?WT2(s)?1整定主调节器WT1(s)。由图2-5可以写出串级控制系统的特征方程为
1?WT1(s)WT2(s)W02(s)W01(s)Wm1(s)?01?WT2(s)W02(s)Wm2(s)
(2-9)
可得此时等效控制对象的传递函数为
*W01(s)?WT2(s)W02(s)W01(s)Wm1(s)
1?WT2(s)W02(s)Wm2(s)
(2-10)
按照单回路系统整定方法求出主调节器参数,记作?WT1(s)?1。
(3)据(2)得到的?WT1(s)?1,再整定副调节器WT2(s),由图2-5写出串级控制系统的特征方程为
1?WT2(s)?W02(s)Wm2(s)?WT1(s)W02(s)W01(s)Wm1(s)??0 (2-11)
可得此时等效控制对象为
* W02(s)?W02(s)Wm2(s)?WT1(s)W02(s)W01(s)Wm1(s) (2-12)
然后根据单回路系统的整定方法求出副调节器的参数,记为?WT2(s)?2。
(4)如果?WT2(s)?2的参数值与第(1)步得到?WT2(s)?1的参数值
基本相同,那么整定就告完成。两个调节器的整定参数步骤分别为(1)和(2)中求得的参数,否则应根据?WT2(s)?2重复步骤(2)、
(3),直到出现两次整定结果基本相同为止。
3、补偿法
当控制对象导前区的动态特性与整个控制对象的动态特性相比,迟延和惯性不够小时,控制系统经整定后主、副回路的振荡频率差别不够大,这时就不能 用“两步整定法”整定,可以采用“补偿法”整定调节器参数。
图2-3所示的串级控制系统,在保持系统特征方程式不变的条件下,可把它的闭和回路等效的变换成图2-5所示:
图2-5 串级控制系统方框图的等效变换
从等效变换后方框图形式可以看出,如果为了分析串级系统的稳定性,可以把它看作一个单回路系统。在这个等效单回路系统中,调节器为?WT1(s)WT2(s)?控制对象为 W0*(s)?W02(s)?W01(s)?Wm2(s)
??1?? Wm1(s)WT1(s)?
(2-13)
因此,串级系统可按下述步骤进行整定:
(1)适当选择主调节器WT1(s)的参数,以造成一个动态特性较好的等效控制对象W0*(s)。从图2-5或式(2-13)的关系中可知,所造成的等效控制对象W0*(s)只能在控制对象原有的基础上?W01(s)、W02(s)?,通过选择WT2(s)WT1(s)的参数使它比较有利于控制。这就是“补偿法”整定的概念。
(2)选择好WT1(s)的参数得到了等效控制对象W0*(s)后,就可以按单回路系统整定调节器?WT1(s)WT2(s)?,从而得出副调节器WT2(s)的参数。用“补偿法”的概念整定串级控制系统时,不必考虑主、副回路之间相互影响的程度。虽然整定的结果并不能保证串级系统在最佳的条件下工作,但是它可以使系统具有足够的稳定性裕度,因而使整定后的串级系统具有正常运行的基本条件,在主、副调节器不能分别独立整定时,这可以作为整定串级控制系统的一种使用方法。
2.2 导前微分控制系统
在温度控制系统中,常用的一种便是导前微分控制系统。这种控制系统的结构特点是:只用了一个调节器,调节器的输入取了两个信号。一个信号是主汽温经变送器直接进入调节器的信号,另一个信号则是减温器后的温度经微分器后送入调节器的信号。在时间和相位上,后一个信号超前于主信号(主汽温信号),因此把这种系统称为导前微分控制系统。又因为它有两个信号直接送入到调节器,所以也称这样的系统为具有导前微分信号的双冲量控制系统。微分作用能反映输出量的变化趋势,因而能提前反映输出量的变化,把这种作用用于控制系统,能改善控制性能。
2.2.1 导前微分控制系统的组成及原理
采用导前微分信号的过热汽温控制系统如图2-6所示。这个系统引入了导前汽温?2的微分信号作为调节器的补充信号,以改
善控制质量。因为?2和主汽温?1的变化趋势是一致的,切?2的变化比?1快的多,因此它能迅速反映?1的变化趋势。引入了?2的微
分信号后。将有助于调节器的动作快速性。在动态时,调节器将根据?2的微分信号和?1与?1的给定值之间的偏差而动作;但在
静态时,?2的微分信号消失,过热汽温?1必然等于给定值。如果
不采用导前信号?2的微分信号,则在静态时,调节器将保持(?1??2)等于给定值,而不能保持?1等于给定值。
由图2-6所示的系统结构图我们可以画出导前汽温微分信号控制系统的原理方框图,如图2-7所示。它包括两个闭合的控制回路:
1、由控制对象的导前区W02(s),导前汽温变送器r?2、微分器Wd(s)、调节器WT(s)、执行器KZ和减温水调节阀K?组成的副回路
(导前补偿回路);
2、由控制对象的惰性区W01(s)、主汽温变送器r?1和副回路组成的主回路。
图2-6 导前汽温微分信号的双回路汽温控制系统
2.2.2 导前微分控制系统的分析
对于如图2-7所示的控制系统,当去掉导前汽温的微分信号时,系统就成为单回路控制系统,如图2-8(a)所示,控制对象W0(s)??W01(s)W02(s)?的迟延、惯性较大。当系统加入导前汽温微分信号后,调节器将同时接受两个输入信号,系统也成了双回路结构。但对于这个双回路系统作适当的等效变换后,发现仍可把它当作一个单回路系统来处理,如图2-8(b)所示。只是由于微分信号的引入改变了控制对象的动态特性。这个新的控制对象的输入仍然是减温水流量信号WB,但输出信号为?1*,等效控
制对象的传递函数可以根据方框图求得。其中:
?1*??1?d?2??2
dt??1
W(s)?*
0????W02(s)?W01(s)?Wd(s)?2?WB(s)??1???1*(s)
(2-14)
图2-7 采用导前汽温微分信号的双回路汽温控制系统原理框图
图2-8 采用微分信号改变控制对象特性的方框图
a――单回路系统方框图;b――双回路系统的等效方框图
在静态时,微分器输出为零,所以等效控制对象的输出在动态过程中,等效控制对象的输出中除了主汽温信号?1?1*??1;
外,还叠加了导前汽温?2的微分信号。由于?2的惯性迟延比?1小得多,因而等效对象的输出?1*的惯性迟延比?1小得多。因此加入
导前汽温微分信号的作用可以理解为改变了控制对象的动态特性,可见,等效控制对象是输出?1*比主汽温?1的响应有很大的改
善。所以,在控制对象惯性迟延较大的情况下导前汽温微分信号的双回路汽温控制系统是控制品质远比单回路控制系统好。
2.2.3 导前微分控制系统的整定
1、按补偿法进行整定
根据前面对系统的分析方法,我们可以得出补偿法的整定规则:整定微分器Wd?s?的参数(KD、TD)以形成一个等效对象,
这个等效对象的动态特性等于(或近似等于)在动态时为导前区的特性,在静态时为主汽温的特性,而调节器WT(S)的参数(?,
Ti)则按等效对象的特性整定(按一般单回路控制系统得到整定
方法)。
下面分析如何通过调整微分器的参数来获取等效对象的特性。
设主汽温对象的传递函数为
W0(s)?W02(s)W01(s)?K0
(1?T0s)n0
(2-15)
导前区汽温对象的传递函数为
W02(s)?K2
(1?T2s)n2
(2-16)
则等效对象的传递函数为
???K0K0W0*(s)?W02(s)?W01(s)?Wd(s)?2???Ws02??n2?(1?Ts)K2?1?2?
(2-17)
由上式可得
?K?Wd(s)??0?W01(s)??K2???1
??2
(2-18)
可见微分器的参数时根据控制对象的惰性区来整定的,用控制对象惰性区传递函数的求法,可得:
W01(s)?K1
(1?T1s)n1
且
则式(2-18)可写为
Wd(s)?K1?K0/K2 ????1KDTDs1?K1?1?n1?1?TDs(1?Ts)?1???2
(2-19)
假设汽温对象惰性区得传递函数时一阶的(即n1?1),则有
KDTDsTs??1K1T1s??1?K11?1?TDs1?T1s??21?T1s??2
比较等式两边的对应项可得
TD=T1
KD=K1??1??2
微分器按此组参数整定,则等效对象的传递函数为
W0*(s)?K0
(1?T2s)n2
则实现了完全补偿的预定目的。但是汽温对象的惰性区传递函数的阶次都是高于一阶的(通常n1?2),那么,式(2-19)等号两边就只能作到近似相等,而不能实现完全补偿。下面推导n1?2时,微分器参数的确定方法。
将式(2-19)等号的两边展开为幂级数的形式:
等式左边为
KDTDs2233?KDTDs?1?TDs?TDs?TDs?…? 1?TDs
等式右边为
?????11?1K1?1??K1n1????21?Ts?????21??n1?n1?1?22??nTs?T1s? ?112!??
令等式两边s的低阶项(二阶以下项)的系数相等
s项
s2项 KDTD?K1??1nT ??2112KDTD?K1??1n1?n1?1?2T1 ??22
由此可以确定微分器的整定参数
KD?K1??12n1 ??2n1?1
TD?n1?1T12
(2-20)
按式(2-20)求得的Wd?s?参数仅能实现对象的近似补偿,即使
W0*(s)?W02(s)K0
K2
在确定了等效对象的传递函数之后,对于调节器WT(s)的参数?和Ti应按等效对象W0*(s)来整定(按一般单回路系统的整定方法),其原理框图如图2-9所示。
图2-9 补偿法整定框图
补偿法是整定双回路系统的一种很实用的方法,用该方法整定系统时,可以不考虑内外回路之间的相互影响。
2、按等效为串级控制系统的整定方法来整定
采用导前汽温微分信号的控制系统等效为串级控制系统方框图见图2-9。整定步骤和前面已讨论过的串级控制系统相同。 当WT(s)?1?1????KDTDs1?和时,等效副调节器WT*2(s)为W(s)??d1?TDsTis?PI
调节器,传递函数为:
WT*2?s??1?1?1??? TDs?KD?
而等效主调节器WT*1?s?也是PI 调节器,传递函数为
1?1?W(s)??1?? KD?TDs?*T1
此时可根据对象导前区特性和主汽温特性,按串级控制系统的整定方法,分别求得等效副调节器WT*2(s)和等效主调节器WT*1(s)的各个参数,从而求得?、Ti、KD、TD 。
2.3 两种汽温自动控制系统的比较
前面讨论了串级过热汽温控制系统和导前汽温微分信号的双回路过热汽温控制系统,他们在实际应用中一般都能满足生产上的要求,但这两种控制系统在控制质量、系统构成、整定调试等方面各有特点。
1、把采用导前汽温微分信号的双回路控制系统转化为串级
控制系统来看待 时,其等效主、副调节器均为PI调节器。但对于实际的串级汽温控制系统,为了提高副回路的快速跟踪性能,副调节器应采用P或PD调节器,而主调节器应采用PI或PID调节器。因此,采用导前汽温微分信号的双回路系统的副回路,其快速跟踪和消除干扰的性能不如串级系统;在主回路中,串级系统的主调节器可具有微分作用,故控制品质也比双回路系统好,特别对于惯性、延迟较大的系统,双回路系统的控制质量不如串级系统。
2、串级控制系统主、副两个控制回路的工作相对比较独立,因此系统投运时 的整定、调试直观、方便。而有导前汽温微分信号的双回路控制系统的两个回路在参数整定时相互影响,不容易掌握
3、从仪表硬件结构上看,采用导前汽温微分信号的双回路系统较为简单。一般情况下,双回路汽温控制系统已能够满足生产上的要求,因此得到了广泛的应用。若被控对象的迟延较大,外扰频繁,而且要求有较高的控制质量,则应采用串级控制系统。
第三章 大迟延控制系统
在热工过程控制中,有的过程控制(对象特性)具有较大
的纯延迟,使得被调量不能及时反映系统所承受的扰动,且当过程控制通道或测量环节存在延迟时候,会降低系统的稳定性;另外纯迟延会导致被控制量的最大动态偏差增大,系统的动态质量下降,而且t/Tc之比越大越不容易控制。
解决具有纯迟延的过程控制是一个比较棘手的问题,对于闭环系统内的纯迟延若单单采用上述的串级控制等方案是无法保证其控制质量,且响应速度也和很慢,如果在控制精度很高的场合,则须采取其他控制手段,例如补偿控制,采样控制等等。本章仅就预估控制方法进行详细介绍。
3.1 Smith预估补偿器
对于有纯迟延过程的控制系统,调节器采用PID控制规律时,系统的静态和动态品质均下降,纯迟延愈大,其性能指标下降的愈大。Smith针对具有纯迟延的过程,提出在PID反馈控制的基础上引入一个预补偿环节,使控制品质大大提高。下面就对Smith预估补偿的原理进行更详细地介绍。
当采用简单回路控制时,如图3-1所示
图3-1 单回路控制系统
控制器的传递函数为WT(s),对象的传递函数为
W0(s)=W0'(s)e-ts时,从设定值作用至被控变量的闭环传递函数是:
Y(s)WT(s)W0'(s)e-ts
=R(s)1+WT(s)W0'(s)e-ts
(3-1)
扰动作用至被控变量的闭环传递函数是:
Y(s)W0'(s)e-ts
=Fs1+WT(s)W0'(s)e-ts
(3-2)
如果分母中的e-ts项可以除去,情况就大有改善,迟延对闭环极点的不利影响将不复存在。
-tsSmith预估补偿方案主题思想就是消去分母中的e项,实
现的方法是把对象的数字模型引入到控制回路之内,设法取得更为及时的反馈信息,以改进控制品质,这种方案可按不同的角度进行解释说明,下面从内模(模型置于回路之内)的角度来介绍。Smith预估器补偿原理图如图3-2所示。
图3-2 Smith预估补偿控制原理图
在图3-2中W0'(s)是对象除去纯迟延环节e-ts以后的传递函数,Ws'(s)是Smith预估补偿器的传递函数,假若系统中无此补偿器,则由调节器输出m(s)到被调量Y(s)之间的传递函数为:
Y(s)=W0'(s)e-ts m(s)
上式表明,受到控制作用之后的被调量要经过纯迟延t之后才能返回到调节器。若系统采用预估补偿器,则调节器m(s)与反馈到调节器的Y'(s)之间传递函数是两个并联通道之和,即
Y'(s)=W0'(s)e-tst+Ws'(s)m(s)
(3-3)
为使调节器采集的信号Y'(s)不至迟延t,则要求式(3-3)为
Y'(s)=W0'(s)e-tst+Ws'(s)=W0'(s) m(s)
从上式便可得到预估补偿器的传递函数为:
Ws'(s)=W0'(s)(1-e-ts)
(3-4)
一般称式(4-4)表示的预估器为Smith预估器。其实施框图如图4-3所示,只要一个与对象除去纯迟延环节后的传递函数Ws'(s)相同的环节和一个迟延时间等于t的纯迟延环节就可以组成Smith预估模型,它将消除大迟延对系统过度过程的影响,使调节过程的品质与过程无迟延环节时的情况一样,只是在时间坐标上向后推迟的一个时间t。
图3-3 Smith补偿系统方框图
从图3-3可以推出系统的闭环传递函数为
''??s??Y(s)'??s1?WT(s)W0?s??WT(s)W0(s)e?W(s)e R(s)0??1?WT(s)W0'(s)??
=W
(3-5) '0(s)e??s?WT(s)W0'(s)e??s??1?? '?1?WT(s)W0(s)?=W0'(s)e-ts[1-W1(s)e-ts]
WT(s)W0'(s) W1(s)='()()1+WTsW0s
式中W1(s)为无延迟环节时系统闭环传递函数。
Y(s)WT(s)W0'(s)e-ts
==W1(s)e-ts
'R(s)1+WT(s)W0(s)
(3-6)
由式(3-6)可见,对于随动控制经预估补偿,其特征方程中已消去了e-ts项,即消除了纯迟延对系统控制品质的不利影响。至于分之中的e-ts仅仅将系统控制过程曲线在时间轴上推迟了一个t,所以预补偿完全补偿了纯迟延对过程的不利影响。控制品质与被控过程无纯迟延完全相同。
对于定值控制,由式(3-5)可知,闭环传递函数由两项组成。第一项为扰动对象只有t>2t时才产生控制作用,当t?2?时无控制作用。所以Smith预估补偿控制应用于定值控制其效果不如随动控制。不过,从系统特征方程看,预估补偿方案对定值控制系统品质的改善还是有好处的。
下面以传递函数 W01?2e?50s为对象进行仿真研究: 1?90s
其调节器为PI调节器,即WT?s??1?1?1???。用衰减曲线法整??Tis?
定参数得??4.1;Ti?55, 加上Smith预估器用MATLAB进行仿真,其结构图如图3-4所示,其仿真曲线如图3-5所示。
图3-4 史密斯预估器控制的系统Simulink结构图
把对象传递函数中的迟延时间由50s改为40s,再次进行仿真得到的仿真曲线如图3-6所示。
由仿真图3-5与图3-6相比较得到,由图3-5可以看出Smith预估器使控制品质大大提高,系统的特性非常好。但是它对模型的误差十分敏感,当系统参数变化时,由于控制参数不能随之而变化,不能对受控过程参数做出适时调整,从而时过程的品质指标恶化。适应性不强,也就是鲁棒性非常差。
由于主蒸汽温度被控对象的参数会随着时间的变化而产生变化,所以我们需要的是鲁棒性好的控制系统,要进一步探讨别的方法。
3.2 史密斯预估补偿器的改进
由于Smith预估器对模型的误差十分敏感,因而难于在热工过程控制中广泛应用,如何克服Smith预估器的这个不足至今仍使研究的课题之一。
图3-5 在对象参数准确情况下史密斯预估器控制阶跃响应的
曲线
图3-6 改变对象参数后的仿真图
3.2.1 抗干扰的Smith预估器
如果在史密斯补偿回路中增加一个反馈环节Wf(s)如图3-7
所示,则系统可以达到完全抗干扰的目的。由图3-7可看出被调量Y(s)对干扰F(s)的闭环传递函数为:
''??s??1?W(s)W(s)?W(s)W(s)1?eY(s)f00T'??s ?W0(S)e?''??s'??s?F(s)1?W(s)W(s)?W(s)W(s)1?e?W(s)W(s)e??f00TT0??
?W(S)e'
0??s?1?Wf(s)W0'(s)?W0'(s)WT?''1?W(s)W(s)?W(s)WT(s)?f00?(s)?1?e????s?????
(3-7)
图3-7 实现完全抗干扰的史密斯补偿器
若要完全不受干扰F(s)的影响,则只要上式中分子为零,即
1+Wf(s)W0'(s)+W0'(s)WT(s)(1-e-ts)=0
由此可以得到新增反馈环节Wf(s)为
1+W0'(s)WT(s)(1-e-ts)Wf(s)=-W0'(s)
(3-8)
再写出上述系统中被调量Y
Y(s)WT(s)W0'(s)e-ts
=R(s)1+Wf(s)W0'(s)+W0'(s)WT(s)(1-e-ts)+WT(s)W0'(s)e-ts
(s)对设定值R(s)的闭环传递函数为
WT(s)W0'(s)e-ts
=1+Wf(s)W0'(s)W0'(s)WT(s)
(3-9)
将(3-8)式代入(3-9)式后可以得到一个很有意义的结论,即
Y(s)WT(s)W0'(s)e-ts
==1'-ts()()()RsWTsW0se
(3-10)
这就是说如果Wf(s)完全满足式(3-8),则系统可完全跟踪设定值。而且对干扰F(s) 还可以无差的进行补偿。只是Wf(s)完全实现不是很容易的,尤其在对象用高阶微分方程来描述时更是如此。但是这个结论对改善史密斯补偿器的抗干扰能力还是有指导意义的。
3.2.2 增益自适应补偿方案
图3-8 增益自适应补偿方案
Smith预估补偿控制实质上是PID调节器连续地向补偿器传
送信号,作为输入而产生补偿器输出。补偿器与过程特性有关,而过程的数学模型与实际过程特性之间又有误差,所以这种控制方法的缺点是模型的误差会随时间积累起来,也就是对过程特性变化的灵敏度很高。为了克服这一缺点,可采用增益自适应预估补偿控制。
增益自适应补偿方案方框图如图3-8所示。它在Smith补偿模型之外加了一个除法器,一个导前微分环节和一个乘法器。除法器是将过程的输出值除以模型的输出值。导前微分环节的Td=t,它将使过程与模型输出之比提前进入乘法器。乘法妻是将预估器的输出乘以导前微分环节的输出,然后送到调节器。这三个环节的作用量要根据模型和过程输出信号之间的比值来提供一个自动校正预估器增益的信号。由图3-8所得
Y(s)=[R(s)-D4(s)]WT(s)W0'(s)e-ts
A(s)=Y(s)
B(s)=m(s)Wc(s)e-tms
D4(s)=D1(s)D3(s)
A(s)=m(s)Wc(s)(1+Tds)B(s)
(1+Tds)Y(s) =m(s)Wc(s)m(s)Wc(s)e-tms
=(1+Tds)Y(s)
e-tms
D4(s)1+Tds所以 Y(s)=e-tms
Y(s)?R(s)WT(s)W0`(s)e?ts
`?ts1?Tds1?WT(s)W0(s)ee?tms
若t=tm,则有
Y(s)WT(s)W0'(s)e-ts
=R(s)1+(1+Tds)WT(s)W0'(s)
(3-11)
从以上分析可以看出增益自适应补偿器与Smith补偿器具有同样改善控制性能的效果。
3.2.3 观测补偿器控制方案
图3-9 能观测补偿时控制方案
观测补偿器控制方案如图3-9所示,由图可以得
WT(s)Wo(s)Y(s)?R(s)1?W(s)W(s)KoCT1?WK(s)WC(s)
WC(s)?Wo'(s)Ym
(3-12)
闭环特征方程可由下式求得
1+WC(s)WT(s)1+WK(s)W0(s)=0()()1+WKsWCs
(3-13)
不管对象的时滞有多大,只要WC(s)的模足够小,就有
1+WK(s)W0(s)=11+WK(s)WC(s)
(3-14)
从而闭环特征方程为
1+WC(s)WT(s)=0
(3-15)
这表明系统的稳定性只与观测器WC(s)有关,而与时滞大小无关。若WC(s)=W0'(s),则式(3-12)与Smith预估补偿控制方式(3-6)相同,表明其控制效果与Smith预估补偿控制的相同。但本方案对于对象参数的变化不敏感,且不需要时滞环节。因此,实施起来方便,适应性强。
对于随动控制系统,本方案可看作由两个随动系统组成。由主控制器WT(s)与W0(s)、WC(s)、WK(s)组成的主随动控制系统,用于使观测器输出值跟踪设定值。由副控制器WK(s) 与WC(s)组成副随动控制系统用于使观测器输出值与系统的输出保持同步。当设定值发生变化时,由于观测器输出Ym尚未变化,所以主控
制器输出一个较强的控制信号,通过前馈作用,使观测器输出较快的跟踪,以减少控制器的偏差,起到超前的控制作用。同时,该控制信号对过程本身也起调节作用,使输出Y较快变化。由于副控制器的控制作用,使观测器输出Ym适应系统输出Y的变化。当主副控制器均为比例积分作用时,整个系统可以达到稳态无余差。
观测补偿器控制方案仅适用于随动控制系统,不适用于定值控制系统;当WK?s?的模很大时,本控制方案与单回路控制系统相同。
3.2.4 改进型Smith预估器
由Hang等提出的改进型预估器,它比原方案多了一个调节器,其方框图如图3-10所示。
图中设过程特性的比例增益K0?1,从图3-10中可以看到,它与Smith补偿器方案的区别在于主反馈回路,其它反馈通道传递函数不是1而是Wf(s),即
Wf(s)?WT2Ws(s) 1?WT2Ws(s)
图3-10 改进型Smith预估器方框图
改进型Smith预估器方案比原Smith补偿方案多了一个调节器WT2(s),但其参数整定还比较简单。为了保证系统输出相应无余差,要求两个调节器均PI为动作调节器。其中主调节器WT1(s)只需按模型完全准确的情况下进行整定。至于辅助调节器WT2(s)的整定似乎要复杂一些,但经分析发现,辅助调节器是在反馈通道上,且与模型传递函数Ws(s)一起构成Wf(s)。如果假设Ws(s)是一阶环节。且设Ti2?Ts,即使调节器的积分时间等于模型的时间
常数,则Wf(s)可简化为:
Wf(s)?1
Ts
KT2Ks1? Ts?1fs?1
这样,反馈回路上出现了一个一阶滤波器,其中只有一个整定参数Tf,实质上只有WT2(s)中的比例增益KT2需要整定。
下面我们同样以传递函数 W01?2e?50s为对象对改进型1?90s
Smith预估器进行仿真研究,其Simulink结构图如图3-11所示,仿真图如图3-12所示。
篇3:毕业论文锅炉
毕业论文锅炉
基于PLC工业锅炉汽包水位控制系统的设计
The Design of the Boiler Drum Water
Level Control System with PLC
摘 要
锅炉是众多工业部门必不可少的重要动力设备。因此,锅炉往往成了不少工厂不可缺少的一部分。因而,对锅炉设备中的自动控制系统进行分析研究是必要的。锅炉水位控制系统是锅炉生产控制系统中最重要的环节。对锅炉生产操作如果不合理,管理不善,处理不当,往往会引起事故。这些事故中的大部分是由于锅炉水位控制不当引起的,可见锅炉汽包水位控制在锅炉设备控制系统中的重要性。
锅炉汽包水位是一个非常重要的被控变量。由于锅炉的水位调节过程难以建立数学模型,具有非线形、不稳定性、时滞等特点。传统的锅炉水位三冲量控制系统大都采用PID控制,其控制效果还可以进一步提高。而模糊控制不要求知道被控对象的精确模型,只需要操作人员的经验知识及操作数据,鲁棒性强,非常适合于非线性、滞后系统的控制。
关键词: 汽包水位; 模糊PID; 三冲量
Abstract
The boiler is numerous essential important power equipment of industrial department. So, the boiler has often become an indispensable part of many factories. Therefore, it is essential for automatic control system in the boiler equipment to research. The water level control system of the boiler is that the boiler produces the most important link in the control system. If the production operation of the boiler is unreasonable, it is improper to deal with, and will often cause the accident. The majority in these accidents is caused because of improper in control the water level of the boiler. That can see the importance in the equipment control system of the boiler of control of water level of steam dome of the boiler.
The auto-control of the drum water level is very important. The drum water level is an important variable to be controlled, it is hard to get the mathematic model of the water level with adjust process. It is characteristic of nonlinearity, instability and time lag. The traditional control mode of three-variable in the drum water level most use PID, the effect of it can be improved. The fuzzy control does not need precise mathematic model of the controlled object, it only needs the experience of operator and the date of operating it has good robustness and it fit to control the system with nonlinearity and lag.
Keywords: Drum water level, Fuzzy-PID, Three-variable
目 录
摘 要 .............................................. I ABSTRACT ......................................... I
1.引言 ............................................... 1
2.工业锅炉的理论基础.................................. 1
2.1工业锅炉的控制要求与工艺流程 ............................................................1
2.2锅炉设备控制系统 ..................................................................................2
2.3锅炉水位控制系统在锅炉生产控制系统中的重要性 ..............................3
3锅炉汽包水位的基本特性和汽包水位控制系统方案选择 ..... 3
3.1锅炉汽包水位控制对象的基本特性 ........................................................3
3.1.1汽包水位在给水流量扰动下的动态特性 .............................................4
3.1.2汽包水位在蒸汽负荷扰动下的动态特性 .............................................5
3.1.3燃料量扰动下汽包水位的动态特性 ....................................................6
3.2锅炉汽包水位控制系统及控制方案选择.................................................7
3.2.1单冲量水位控制系统 ...........................................................................7
3.2.2双冲量水位控制系统 ...........................................................................8
3.2.3三冲量水位控制系统 ...........................................................................8
3.2.4三冲量模糊水位控制系统 ...................................................................9
3.2.5汽包水位控制系统方案的选择 ..........................................................10
4.锅炉汽包水位模糊控制系统的设计 .................... 11
4.1主回路模糊控制器的设计 ..................................................................... 11
4.1.1确定模糊控制器的结构及输入、输出语言变量................................ 11
4.1.2确定各变量的隶属度函数和赋值表 .................................................. 11
4.1.3模糊控制规则的确定 .........................................................................14
4.1.4模糊控制响应表的生成 .....................................................................14
4.2模糊动态前馈控制器的设计 .................................................................16
4.3 PID控制的设计 ....................................................................................16
4.3.1PID控制的基本公式...........................................................................16
4.3.2 PID的参数设置 ................................................................................16
5. PLC选型及资源分配 ................................ 17
5.1 PLC电气图和I/O分配表 .....................................................................17
5.2 PLC选型................................................................................................18
5.3 传感器选型 ...........................................................................................18
5.4特殊模块功能........................................................................................18
6.控制系统程序设计 .................................. 18
6.1编程软件 ...............................................................................................19
6.2控制系统流程图 ....................................................................................19
6.2.1控制系统总流程图设计 .....................................................................19
6.2.2模糊控制流程图 ................................................................................19
6.2.3PID控制流程图 ..................................................................................20
6.2.4动态前馈流程图 ................................................................................20
6.3系统的程序设计 ....................................................................................21
6.3.1水位控制 ...........................................................................................21
6.3.2模糊控制算法的PLC实现 .................................................................21
6.3.3 PID控制的PLC实现 .........................................................................22
7 结束语 ............................................ 23
致谢 ................................................ 24
参考文献: .......................................... 25
附录: .............................................. 26
1. 引言
在锅炉运行中,水位是一个很重要的参数。若水位过高,则会影响汽水分离的效果,使用电气设备发生故障;而水位过低,则会破坏汽水循环,严重时导致锅炉爆炸。同时高性能的锅炉产生的蒸汽流量很大,而汽包的体积相对来说较小,所以锅炉水位控制显得非常重要。锅炉水位自动控制的任务,就是控制给水流量,使其与蒸发量保持平衡,维持汽包内水位在允许的范围内变化。
目前我国有各类锅炉几十万台,其中相当大的部分还在使用常规仪表控制。由于锅炉水位存在一定的反向特性即“假水位”现象,而常规仪表所常用的PID算法对“假水位”现象的控制效果并不理想,若要较好的控制“假水位”现象,采用常规仪表所构成的控制器,其结构复杂性又会增加,造成成本较高。因此研究新型的水位控制系统,使其能进一步提高水位控制的效果,同时又具有结构简单、容易实现的特点,还是非常必要的。
模糊控制是以模糊集合理论为基础的一种新兴的控制手段,它是模糊系统理论和模糊技术与自动控制技术相结合的产物。模糊控制的核心就是利用模糊集合理论,把人的控制策略的自然语言转化为计算机能够接受的算法语言所描述的控制算法,这种方法不仅能实现控制,而且能模拟人的思维方式对一些无法构造数学模型的被控对象进行有效的控制。三冲量锅炉水位控制系统中的主回路控制部分与蒸汽前馈控制部分正是属于这种情况:由于虚假液位的影响和各种参数存在的时变性而导致无法确定这一过程的数学模型,这样就不能设计常规的控制器进行控制[1]。
2.工业锅炉的理论基础
2.1工业锅炉的控制要求与工艺流程
锅炉是化工、炼油、发电、造纸和制糖等工业生产过程必不可少的重要动力设备。尤其是在现代化的石油化工企业里,热力站的设立可以使工艺生产过程中的物料和能量得到更加合理的充分利用,它不仅能为反映器、蒸馏塔、换热器以及其他设备、管道保温伴热提供热源,而且还可以为生产过程中的风机、压缩机、泵类驱动透平提供动力来源。工业蒸汽锅炉汽包水位控制的任务是控制给水流量与蒸发量保持动态平衡,维持汽包水位在工艺允许的范围内,是保证锅炉安全生产运行的必要条件,也是锅炉正常生产运行的主要指标之一。
所有各种锅炉,虽然燃料种类各不相同,但蒸汽发生系统和蒸汽处理系统是基本相同的。常见的锅炉设备的主要工艺流程图如图2-1所示。
图2-1工业锅炉工艺流程
首先除氧水通过给水泵进入给水调节阀,通过给水调节阀进入省煤器,冷水在经过省煤器的过程中被由炉膛排出的烟气预热,变成温水进入汽包,在汽包内加热至沸腾产生蒸汽,为了保证有最大的蒸发面因此水位要保持在锅炉上汽包的中线位置,蒸汽通过主蒸汽阀输出。空气经过鼓风机进入空气预热器,在经过空气预热器的过程中被由炉膛排出的烟气预热,变成热空气进入炉膛。煤经过煤斗落在炉排上,在炉排的缓慢转动下煤进入炉膛被前面的火点燃,在燃烧过程中发出热量加热汽包中的水,同时产生热烟气。在引风机的抽吸作用下经过省煤气和空气预热器,把预热传导给进入锅炉的水和空气。通过这种方式使锅炉的热能得到节约。降温后的烟气经过除尘器除尘,去硫等一系列净化工艺通过烟囱排出。
2.2锅炉设备控制系统
锅炉生产控制系统,是指锅炉生产过程的自动化系统。即通过各种检测仪表,调节仪表,控制装置(运算器,监控器,执行器)等自动化技术工具,对锅炉生产过程中的温度,压力,流量,液位等热工变量进行自动控制的系统。自动控制的目的是实现各种最优的技术经济指标,减轻劳动强度,提高经济效益和生产率,节约能源,改善劳动环境条件。
锅炉设备控制划分为若干个控制系统。主要控制系统如下。
1)锅炉汽包水位的控制
被控变量是汽包水位,操纵变量是给水流量。他主要考虑汽包内部的物料平衡,使
给水量适应锅炉的蒸汽量,维持汽包水位在工艺允许范围内。维持汽包水位在给定范围内是保证锅炉、气轮机安全运行的必要条件之一,是锅炉正常运行的指标。
2)锅炉燃烧系统的控制
其控制目的是使燃料燃烧所产生的热量适应蒸汽负荷的需要(常以蒸汽压力为被控变量);使燃料与空气量之间保持一定的比例,以保证最经济燃烧,提高锅炉的燃烧效率;使引风量与送风量相适应,以保持炉膛负压在一定范围内。为达到上述三个控制目的,控制手段也有三个,即燃料量、送风量和引风量[2]。
3)过热蒸汽系统的控制
维持过热器出口温度在允许范围内,并保证管壁温度不超过允许的工作温度。被控变量一般是过热器出口温度,操纵变量是减温器的喷水量。
2.3锅炉水位控制系统在锅炉生产控制系统中的重要性
锅炉是一种受压又直接受火的特种设备,是工业生产中的常用设备。对锅炉生产如果操作不合理,管理不善,处理不当,往往会引起事故,轻则停炉影响生产,重则造成爆炸,造成人身伤亡,损坏厂房、设备,后果十分严重。因此,锅炉的安全问题是一项非常重要的问题,必须引起高度重视。
工业锅炉中最常见的事故有:锅内缺水,锅炉超压,锅内满水,汽水共腾,炉管爆破,炉膛爆破,二次燃烧,锅炉灭火等。其中以锅炉缺水事故比例最高。这些事故中的大部分是由于锅炉水位控制不当引起的,可见锅炉汽包水位控制在锅炉设备控制系统中的重要性。
3锅炉汽包水位的基本特性和汽包水位控制系统方案选择
3.1锅炉汽包水位控制对象的基本特性
工业锅炉的汽水系统结构如图3-1所示。
2
1 3 4 7 8
5
6
图3-1工业锅炉汽水结构
1― 给水母管;2―调节阀;3―省煤器;4―汽包;
5―下水管;6―上升管;7―过热器;8―蒸汽母管
贮藏量的多少是以被控制量水位表征的,汽包的流入量是给水量,流出量是蒸汽量,当给水量等于蒸汽量时,汽包水位就恒定不变。引起水位变化的主要扰动就是蒸汽流量的变化和给水流量的变化。如果只考虑主要扰动 那么,汽包水位对象的动态特性可用方程式表示为:
T1T2dkdt22?Tdk1dt?(Twdvwdt?kwvw)?T(ddvddt?kdvd ) (公式1)
式中 T1、T2 时间常数,Tw 给水流量项时间常数,Td 蒸汽流量项时间常数,Kw 给水流量项放大系数,KD 蒸汽流量项放大系数。
3.1.1汽包水位在给水流量扰动下的动态特性
给水流量对水位的影响,即控制通道的动态特性。把汽包和给水看作单容无自衡对象,水位响应曲线应为一条直线。但由于给水温度比汽包内饱和水的温度低,所以给水量变化后,使汽包内气泡含量减少,导致水位下降。即当突然加大给水量后,汽包水位一开始并不增加而要呈现一段起始惯性段[3]。
图3-1-1所示是给水流量作用下,水位的阶跃响应曲线。把汽包和给水看作单容量无自衡过程,水位阶跃响应曲线如图中H1线。
图3-1-1 汽包水位在给水流量扰动下的阶跃响应曲线
但是由于给水温度比汽包内饱和水的温度低,所以给水流量增加后,从原有饱和水中吸取部分热量。这使得水位下汽包容积有所减少,使水位下降,单考虑这个因数,水位的变化如图中曲线H2,相当于一个惯性环节,实际上水位H的响应为H1与H2的和。当水位下汽包容积的变化过程逐渐平衡时,水位变化就完全反映了由于汽包中储水量的增加而逐渐上升。最后当水位下汽包容积不再变化时,水位变化就完全反映了由于储水量的增加而直线上升。因此,实际水位曲线如图2中H线。即当给水量作阶跃变化后,汽包水位一开始不立即增加,而是呈现出一段起始惯性段。用传递函数来描述时,它近似于一个积分环节和时滞环节的串联。可表示为:
Wow(s)?H(s)W(s)??
s???
1??s??
s(1??s)
式中 ?:迟延时间(s); ?:响应速度,即给水流量改变一个单位流量时。
3.1.2汽包水位在蒸汽负荷扰动下的动态特性
蒸汽负荷(蒸汽流量)对水位的影响,即干扰通道的动态特性
在蒸汽流量扰动下,水位响应曲线如图3-1-2。从图上可以看出,在燃烧不变的情况下,蒸汽用量突然增加,瞬时间必然导致汽包压力下降,汽包内水的沸腾突然加剧,水中气泡迅速增加,将整个水位抬高,形成虚假的水位上升现象,即所谓 “虚假水位”现象。 “虚假水位”是由两个原因造成的:
(1) 由于锅炉蒸汽负荷增加,使炉管和汽包中汽水混合物的汽、水比例发生变化(汽
容积增加)而引起汽包水位上升,这是引起汽包“虚假水位”的主要原因。
(2) 蒸汽流量增加,汽包气压下降,炉水沸点下降,由于炉水为饱和水的汽化,使汽
包水位随压力下降而升高。
图3-1-2汽包水位在蒸汽负荷扰动下的阶跃响应曲线
当蒸汽流量D突然增加时,从锅炉的物料平衡关系来看,蒸汽量D大于给水量W,水位应下降,如图中直线H1所示。但实际情况并非这样,由于蒸汽用量的增加,瞬间必然导致汽包压力的下降。汽包内的水沸腾突然加剧,水中汽包迅速增加,由于汽包容积增加而使水位变化的曲线如图3-1-2中H2所示。而实际显示的水位响应曲线H为H1+H2。从图上可以看出,当蒸汽负荷增加时,虽然锅炉的给水量小于蒸发量,但在一开始时,水位不仅不下降,反而迅速上升,然后在下降(反之,蒸汽流量突然减少时,则水位先下降,然后上升)这种现象称之为“虚假水位”。
应该指出:当负荷变化时,水位下汽包容积变化而引起水位的变化速度是很快的,图中H2的时间常数只有10~20S。蒸汽流量扰动时,水位变化的动态特性可用函数表示为:
WOD(s)?
H(s)D(s)
?
k21?T2s
?
?
s
式中, T2:曲线2的时间常数 k2:曲线2的放大系数 ?:曲线1的响应速度 “虚假水位”变化的幅度与锅炉的工作压力和蒸发量有关。例如,一般100~200t/h的中高压锅炉,当负荷变化10%时,“虚假水位”可达30~40mm。“虚假水位”现象属于反向特性,其变化与锅炉的气压和蒸发量的变化的大小有关,而与给水流量无关[4]。
3.1.3燃料量扰动下汽包水位的动态特性
汽包水位在燃料量B扰动下的响应曲线如图3-1-3所示,当燃料量增加时,锅炉的吸热量增加,蒸发强度增大。如果气轮机侧的用汽量不加调节,则随着汽包压力的增高,汽包输出蒸汽量也将增加,于是蒸发量大于给水量,暂时产生了汽包进出口工质流量的不平衡。由于水面下的蒸汽容积增大,此时也会出现虚假水位现象,但由于燃烧率的增
加也将气量D缓慢增加,故虚假水位现象要比D扰动下缓和得多[5]。
图3-1-3 汽包水位在燃烧率扰动下的阶跃响应曲线
3.2锅炉汽包水位控制系统及控制方案选择
3.2.1单冲量水位控制系统
单冲量水位控制系统是以汽包水位测量信号为唯一的控制信号,即水位测量信号经变送器送到水位调节器,调节器根据汽包水位测量值与给定值的偏差去控制给水调节阀,改变给水量以保持汽包水位在允许范围内。单冲量水位控制系统,是汽包水位控制系统中最简单最基本的一种形式[6]。
图3-2-1单冲量水位控制系统
如图3-2-1所示是单冲量变量水位控制系统。单冲量即汽包水位。这种控制结构简单,是单回路定制控制系统,在汽包内水的停留时间较长,负荷又比较稳定的场合下再配上一些锁报警装置就可以安全操作。
然而,在停留时间较短,负荷变化较大时,采用单冲量水位控制系统就不能适用。这是由于:①负荷变化时产生的“虚假水位“将使调节器反向错误动作,负荷增大时反向关小给水调节阀,一到闪急汽化平息下来,将使水位严重下降,波动厉害,动态品质很差。②负荷变化时,控制作用缓慢。即使”虚假水位“现象不严重,从负荷变化到水位下降要有一个过程,再有水位变化到阀动作已滞后一段时间。如果水位过程时间常数很小,偏差必然相当显著。 3.2.2双冲量水位控制系统
双冲量水位控制系统是在单冲量水位控制系统的基础上加入了以蒸汽流量信号为前馈信号的锅炉汽包水位控制系统。如图3-2-2,由于引入了蒸汽流量前馈信号,当蒸汽量变化时,就有一个与蒸汽量同方向变化的给水流量信号,可以减少或抵消由于“虚假液位”现象而使给水量与蒸汽量相反方向变化的错误动作。使调节阀一开始就向正确的方向动作。因而能极大的减小给水量和水位的波动,缩短过度过程时间。
图3-2-2 双冲量控制系统
双冲量控制由于有以上特点,所以能在负荷频繁变化的工程下较好的完成水位控制任务。在给水流量比较平稳时,采用双冲量控制是能够达到控制要求的。
双冲量水位控制系统存在的问题是:控制作用不能及时的反映给水方面的扰动,当给水量发生扰动时,要等到汽包水位变化时才通过调节器作用执行器进行调节,滞后时间长,水位波动较大。因此,如果给水母管压力经常有波动,给水调节阀前后压差不能保持正常时,不宜采用双冲量控制。 3.2.3三冲量水位控制系统
三冲量控制系统,以汽包水位为主控制信号,蒸汽流量为前馈控制信号,给水流量
为反馈控制信号组成的控制系统。三冲量水位控制系统组成原理图如图3-2-3。
图3-2-3三冲量控制系统
现代工业锅炉都向着大容量高参数的方向发展,一般锅炉容量越大,汽包的容水量就相对越小,允许波动的蓄水量就更少。如果给水中断,可能在很短的时间内就会发生危险水位;如果仅是给水量和蒸汽量不相适应,也可能在几分钟呢出现缺水和满水事故,这样对汽包水位要求就更高了。三冲量控制系统,采用蒸汽流量信号对给水流量进行前馈控制,当蒸汽负荷忽然变化时,蒸汽流量信号使给水调节阀一开始就向正确方向移动,即蒸汽流量增加,给水调节阀开大,抵消了“虚假水位”引起的反向动作,因而减小了水位和给水流量的波动幅度。当由于水压干扰使给水流量改变时,调节器能迅速消除干扰。如给水流量减少,调节器立即根据给水流量减小的信号,开大给水阀门,使给水流量保持不变。
3.2.4三冲量模糊水位控制系统
由常规控制理论的局限性和模糊控制理论的特点可以看出,对于存在精确数学模型的自动控制系统,常规控制理论发挥了巨大的作用,并取得了令人满意的控制效果。但在实际系统中,工业生产过程是极其复杂的,无法得到描述这些过程的数学模型,尽管通过各种测试手段及数据处理方法获得数学模型,但也很难得到确切描述这些过程的传递函数或状态方程。这样常规控制理论就无法胜任,必须寻求新的控制理论来取代常规控制理论进行控制。
三冲量系统可以克服“虚假液位”引起的反向动作,并且可以克服给水流量信号变化而引起调节器动作做不及时而引起的水位波动。但是各种参数又存在不同程度的时变性,且过程具有非线性,强耦合的特点,特别是蒸汽负荷变化对水位的影响,当蒸汽负荷增加和减小时,汽包水位在蒸汽作用下的动态特性不一致,这样很难确定三冲量控制
系统中蒸汽前馈系统的精确数学模型,这就使得三冲量控制系统的控制规律很难找到,即使找到控制规律也很难作的精确。这样想采用三冲量水位控制系统来实现锅炉水位的自动控制而又达到规定的工艺要求异常困难。
对于大型锅炉,汽包的容量相对较小,则对锅炉汽包水位的要求更高,汽包水位就必须实现全自动控制才能满足。因而,汽包水位控制就采用比较复杂而投资比较大的控制系统。对于中小型锅炉,汽包的容量相对较大,则对汽包水位的控制要求就没那么高,又由于常规三冲量控制系统很难实现汽包水位的自动控制,所以中小型锅炉允许适当的采用手动控制。这样对于中小型锅炉就可以考虑用模糊控制系统来取代常规的三冲量PID控制系统。
模糊控制是以模糊集合理论为基础的一种新兴的控制手段,它是模糊系统理论和模糊技术与自动控制技术相结合的产物。模糊控制的核心就是利用模糊集合理论,把人的控制策略的自然语言转化为计算机能够接受的算法语言所描述的控制算法,这种方法不仅能实现控制,而且能模拟人的思维方式对一些无法构造数学模型的被控对象进行有效的控制。将模糊集合理论运用于自动控制而形成的模糊控制理论,在近年来得到了迅速的发展,其原因在于对那些时变的非线性的复杂系统,当无法获得精确的数学模型的时候,利用具有智能的模糊控制器能给出有效的控制。
3.2.5汽包水位控制系统方案的选择
通过以上方案的比较,常规的三冲量控制系统中,由于“虚假液位”的原因使得蒸汽负荷上升和下降时的动态特性曲线不对称,且系统参数具有时变性,不能求出准确的数学模型,也就不能设计出准确的前馈控制器,能实现静态前馈,但对动态性能控制不好。考虑到模糊控制器的设计不需要知道该过程的数学模型以及它的其他特点都适合于这种水位控制,所以选择了汽包水位模糊控制系统。
4.锅炉汽包水位模糊控制系统的设计
图 4-1 汽包锅炉水位模糊控制系统的结构图
设计一个模糊控制器以实现语言控制,必须解决以下称为模糊控制器结构的3方面问题:
(1) 精确量的模糊化,把语言变量的语言值化为某适当论域上的模糊子集; (2) 模糊控制算法的设计,通过一组模糊条件语句构成模糊控制规则,并计算模糊控制规则决定的模糊关系;
(3)输出信息的模糊判决,并完成由模糊量到精确量的转化。
4.1主回路模糊控制器的设计
4.1.1确定模糊控制器的结构及输入、输出语言变量
根据控制对象――汽包及控制精度,模糊控制器的结构选为二输入单输出结构,输入语言变量选为汽包液位偏差e和偏差变化率ec,e=AV-SV,AV为液位测量值,SV为液位设定值。这样就为该汽包液位控制系统选定了一个双输入单输出的模糊控制器。输入和输出模糊集合的隶属函数选为三角形的[7]。 4.1.2确定各变量的隶属度函数和赋值表
工业锅炉在正常运行时,偏差变化范围为[-50cm,+50cm],所以,设偏差e的基本论域为[-50cm,+50cm],选定E的离散论域X为{-6,-5,-4,-3,-2,-1,0,+1,+2,+3,+4,+5,+6}。则得偏差e的量化因子ke=6/50=3/25=0.12,为语言变量选取7个语言值:PB,PM,PS,Z,NS,NM和NB。
确定偏差e的基本论域在离散域X上的隶属函数?(x) 如下:
图4-1-2偏差e的隶属函数
根据上面隶属函数建立语言变量E的赋值表如下:
表4-1-2 语言变量E的赋值表
设偏差变化率ec的基本论域为[-15,+15],选定EC的离散论域Y={-6,-5,-4,-3,-2,-1,0,+1,+2,+3,+4,+5,+6},得偏差变化率ec的.量化因子kec=6/15=0.4。为语言变量EC选取PB,PM,PS,Z,NS,NM和NB共7个语言值。 确定偏差ec的基本论域在离散域Y上的隶属函数?(y) 如下:
图4-1-3 偏差ec的隶属函数
建立偏差变化率ec的语言变量EC的赋值表:
表4-1-3 语言变量EC的赋值表
设控制量变化?的基本论域为[-10,+10],选定U的离散论域为Z={-6,-5,-4,-3,-2,-1,0,+1,+2,+3,+4,+5,+6},则得控制量变化?的量化因子ku=6/10=0.6。同样,为语言变量U选取PB,PM,PS,Z,NS,NM和NB共7个语言值。确定出控制量U的隶属函数,再建立语言变量U赋值表如下:
图4-1-4控制量u的隶属函数
表4-1-4 语言变量U赋值表
4.1.3模糊控制规则的确定
对于双输入单输出模糊控制器,规则选用“if e and ec then u”的形式[8]。根据控制经验,列出控制规则表如下:
表4-1-5 控制规则表
4.1.4模糊控制响应表的生成
模糊控制器在线计算推理模糊关系时,需要耗费大量时间,占用大量内存。而工业锅炉在运行时,需要提高安全性,就必须对控制系统的实时性有较高的要求。所以,离线算出模糊控制表,通过查询方式找到控制量。
要算出模糊控制响应表,必须选择一种模糊推理算法。当模糊控制器采用查表法实现时,用来离线设计查询表,当模糊控制器采用软件推理法实现时,用来在线进行模糊推理。该模糊控制系统采用Mamdani模糊推理算法。对求得的输出模糊集合用加权平均法解模糊,得到精确量,即模糊控制响应表。
当输入偏差E=-6,EC=3时,根据隶属函数,查得对应两条规则: ① if E=NB and EC=PS then U=PM ② if E=NB and EC=PM then U=Z 应用Mamdani模糊推理算法如下图4-1-5:
4-1-5 Mamdani模糊推理算法
应用重心法(加权平均法)解模糊,得到控制器输出的精确量。同理,应用上述算法算出169个离散点的输出。以下不再赘述。现将最后算出的模糊控制响应表列出如下
表4-1-6
4.2模糊动态前馈控制器的设计
该模糊控制器是解决锅炉汽包控制系统在运行时,蒸汽负荷变化对汽包造成虚假液位问题的主要控制器。原始的PID控制系统不能实现动态前馈,且静态前馈控制效果也不尽如人意。而模糊控制不需要了解蒸汽负荷变化时,汽包的外扰特性,即数学模型,且鲁棒性好,对于非线性和参数时变系统有较好的控制能力[9]。所以前馈控制器采用模糊控制器。
在图4-1中,模糊动态前馈控制器采用单输入单输出结构,输入变量为:正常工况下蒸汽母管流量与扰动后蒸汽母管流量之差e,输出语言变量为阀门开度变化量u,模糊动态前馈控制器的设计步骤如下:
(1)输入变量e、输出变量u的论域均取为[-4 4],输入变量e的语言值取为{PB,PM,PS,Z,NS,NM,NB},输出变量e、输出变量u的语言值的隶属函数都选择三角形的隶属度函数。
(2)此控制器仍是离线算出控制表,通过查询方式找到对应的控制量。应用Mamdani模糊推理算法,加权平均法解模糊。 (3)规则选用“if e then u”的形式。
控制规则表如表4-2所示:
4.3 PID控制的设计
4.3.1PID控制的基本公式
PID是比例(P)、积分(I)、微分(D)的缩写,PID控制器是目前应用最为广泛的闭环控制器。标准PID的控制值与偏差(实际值与设定值之差)、偏差对时间的积分、偏差对时间的微分,三者之和成正比。模拟量PID控制器的输出表达式为
u(t)?Kp[e(t)?
1Ti
?
t0
e(t)dt?
TDde(t)dt
]?M
,式中u(t)为控制值 e(t)为偏差值,Kp为比例系
数,Ti为积分常数,TD为微分常数,M为积分部分的初始值。 4.3.2 PID的参数设置
P增益: 设定范围:0.01~10.0倍
这是操作量和偏差之间有比例关系的动作。增益取大时,响应快,但过大将产生振
荡。增益取小时,响应迟后。实际中本设计取0.5。 积分时间:
设定范围:0.1~3600s
操作量(输出频率)的变化速度和偏差成比例关系的动作,即输出按偏差积分的动作。积分时间大时,响应迟后,另外,对外部扰动的控制能力变差。积分时间小时,响应速度快,但过小将产生振荡[10]。实际中本设计取50s。
5. PLC选型及资源分配
5.1 PLC电气图和I/O分配表
图5-1 PLC I/0口分配图
根据上述关于PLC控制系统的基本单元输入和输出信号统计,制定I/O分配表,具体对应关系如下表5-1所示。模拟量模块输入地址分配表如表5-2所示。
表5-1 PLC I/O 分配表
表5-2模拟量模块输入地址分配表
5.2 PLC选型
根据系统的I/O点数,并考虑富裕量及今后系统的扩展升级和工艺控制等问题,本系统设计采用三菱公司的FX2N-16MR型作为主机,FX2N-48MR型是三菱公司的典型产品,具有功能强大,处理速度快、容量大等优点,属于高性能小型机,系统I/O总点数为16点,输入、输出均为8点,配置扩展单元后可增加I/O点数。
5.3 传感器选型
各传感器主要用于水位、蒸汽流量、给水流量等测量。
(1) 应力式涡街流量传感器: 一种既可以测蒸汽、气体又可以测液体的传感器 流速: 气(汽)体:3 m/s ~ 90 m/s 液体: 0.27 m/s ~ 9 m/s
(2)连杆浮球式液位开关(IL-140-2):一种基于自重原理工作的液位开关。当浮球受液体浮力作用而随液位上升时,浮球向上移动后压缩弹簧,并快速启动微型开关,输出相应触点。
5.4特殊模块功能
系统同时配有FX2N-4AD特殊功能模块作为模拟量控制的输入接口。其中FX2N-4AD模拟量输入模块接到FX2N-16MR基本单元的最近位置,模块编号为0,CH1,CH2,CH3通道分别与应力式涡街流量传感器、应力式涡街流量传感器、连杆浮球式液位开关。
6.控制系统程序设计
6.1编程软件
编程软件采用三菱公司为其生产的SWOPC-FXGP/WIN-CVERSINON2.11。
PLC
开发的编程软件
6.2控制系统流程图
6.2.1控制系统总流程图设计
图6-2-1 控制系统总流程图
6.2.2模糊控制流程图
图6-2-2 模糊控制流程图
6.2.3PID控制流程图
图6-2-3 PID 流程图
6.2.4动态前馈流程图
图6-2-4 动态前馈流程图
6.3系统的程序设计
6.3.1水位控制
当输入起动的指令时(X0= 1) , 辅助继电器Y0 被激励, 给出系统运行指示(Y0=
1) , 并且工作指示灯亮。为锅炉水位双位控制。当水位到最低位(X2= 1) , 辅助继电器M 0 被激励(M 0= 1) , 同时给水泵电动机起动运行(Y1= 1)。当水位到最高位(X3= 1) , 水泵电动机停止; 当水位到最低位(X2= 1) 时重复上述过程, 实现锅炉水位双位控制。当双位式控制失灵, 锅炉内水位低至过低限后(X4= 1) , 辅助继电器M 1 被激励(M 1= 1) 实现声光报警, 警铃声音应报警(Y2= 1) , 答后(X5= 1) 消音; 报警灯仍以1s (T1、T2) 为周期闪烁, 直至故障消除[11]。具体梯形图如6-3-1。
图6-3-1
6.3.2模糊控制算法的PLC实现
首先将模糊化过程的量化因子
ke
、
kec
、u存入PLC的保持继电器中,然后利用A/D
k
模块将输入量采集到PLC的D数据区,根据它们所对应的的输入模糊论域中的相应元素,查模糊控制量表求出模糊输出量U,再乘以输出量化因子即可得实际输出量u,由D/A模块输出对阀门度进行控制。在模糊控制算法的实现中,模糊控制量表的查询是程序设计的关键,图6-3-2给出了实现模糊控制量表查表功能的梯形图。为了简化程序设计,程序设计中将输入模糊论域的元素有[-6,-5,-4,-3,-2,-1,0,+1,+2,+3,+4,+5,+6]转化为[0,1,2,3,4,5,6,7,8,9,10,11,12],将模糊控制量表中的U的
控制结果按由上到下、由左到右的顺序依次存入D100~D268中,控制量的基址为100,偏移地址为Ec*13+E。图中,D0和D1分别为E和Ec在模糊论域中所对应的元素[12]。
图6-3-2
6.3.3 PID控制的PLC实现
7 结束语
由于本系统设计采用可编程控制器批plc作为锅炉控制系统的控制核心,使该控制系统具有操作方便,运行可靠,便于修改,扩充等优点。主回路我们设计的是PI控制器和模糊控制器并联的混合控制器,减小了静态误差,改变对象参数后,模糊控制系统仍能使偏差在工艺允许范围内。副回路用模糊控制器取代了常规控制器,解决了因为“虚假液位”造成的不能确定精确的数学模型而无法采用常规控制器进行自动控制的问题并且实现了动态前馈[13]。
鉴于学校实验设备有限,未能将本系统设计的plc梯形图进行模拟调试,所以系统软件设计的可行性未能得到实践证明;鉴于系统建设资金庞大,本系统设计还停留于理论上的方案设计和验证,本次设计尚待检测、实践。
致谢
首先要感谢我的导师朱笑花老师。朱老师平日里工作繁多,但在我做毕业设计的每个阶段,从外出实习到查阅资料,设计草案的确定和修改,中期检查,后期详细设计,装配草图等整个过程中都给予了我悉心的指导。我的设计较为复杂烦琐,但是朱老师仍然细心地纠正图纸中的错误。除了敬佩朱老师的专业水平外,他的治学严谨和科学研究的精神也是我永远学习的榜样,并将积极影响我今后的学习和工作。
其次,我还要感谢一起做PLC论文的各位同学,正是他们的帮助,让我克服了一个个困难。
最后,向我的父母,及所有的老师致谢,感谢他们的栽培与支持!
参考文献:
[1]任向民.工业锅炉控制系统的设计与实现[J].中国科技信息,,第12期 [2]丁鹏飞.工业锅炉集中监视与监控系统[J].中国科技信息,20,第16期 [3]肖大雏.控制设备及系统[M] 北京:中国电力出版社,.252-254
[4]周美兰,周封,王岳宇.plc电气控制与组态设计[M] 北京:科学出版社,.105-109 [5]柴瑞娟 ,陈海霞.西门子PLC编程技术及工程应用[M] 北京:机械工业出版社, 2006.294-300 [6]马育锋,吴汉松,郭颈东.锅炉水位系统的计算机控制[J].自动化仪表第二十卷第四期, [7]唐涛.锅炉汽包三冲量调节系统的设计[J].化工技术与开发, 第32卷第六期12月 [8]文群英,潘汪杰等.热工自动控制系统[M] 北京: 中国电力出版社, 2006.59-65 [9]潘祥亮,罗利文.模糊PID控制在工业锅炉系统中的应用[J].控制系统
[10]甄立常,高欣,锅炉水位控制系统中不完全微分PID 控制器的研究[J].锅炉技术第38卷第四期,
[11]李玲玲.工业锅炉水位三冲量控制系统的改进[J].河北工业大学学报
[12]孙欣.PLC在锅炉控制系统中的应用[J].节能环保 :中国设备工程,6期
[13]高钦和,可编程控制器应用技术与设计实例[M] 北京:人民邮电出版社,. 252-257
附录:
26
27
28
29
30
篇4:锅炉毕业论文的致谢
在本论文的完成过程中,我获得了许多人的帮助。比如:我的老师,我的朋友及我的家人。我很高兴能够借此机会表达我最诚挚的谢意。
首先,我想向我的导师杜云副教授表达我的感谢。本文是在导师杜云老师的悉心指导下完成的。在三年的硕士研究生涯中,杜老师提供了一个气氛宽松而又严谨的科研环境,在我的学业和论文的研究中无不倾注着导师辛勤的汗水和心血。正是因为导师全力支持,课题的研究才得以顺利进行。导师渊博的知识、高尚的人品、积极的工作态度都是我学习的榜样。从敬爱的导师身上,我不仅学到了科学研究的方法,也学到了做人的道理。
其次,我想对在研究生学习阶段,给予我帮助的河北科技大学电气学院的老师及同学们致以衷心的感谢。正是有了你们的包容和帮助,才使我不断成长,不断进步。
同时,我也深深地感谢我的家人。家人对我的殷切希望和爱护是我学习的力量的源泉,家人的鼓励是我坚持的动力。我取得的进步和成绩都离不开他们的无私付出与支持。
最后,向所有老师及百忙之中评阅本论文的专家和教授们,真诚地说一声谢谢!
篇5:锅炉毕业论文的致谢
北建大三年的硕士生活转瞬即逝,提及毕业内心充满了期待与不舍:期待于未来,不舍于现在。回想起这三年的点点滴滴,让我感触的事情太多太多,让我感谢的人也很多很多。
首先,必须感谢我的导师张群力教授,感谢张老师把我引进学术的大门,并在我的科研道路上给予的精心指导,没有张老师的言传身教和悉心教导就不可能有我学术论文的顺利完成,张老师对科研严谨的态度永远是我学习的榜样。除此之外,张老师的人生阅历非常丰富,经常跟我们分享人生感悟,尤记得在我感到山穷水尽的时候,是张老师的一席话,给了我“柳暗花明又一村”
的希望和动力。其次,感谢课题组的刘芳老师在学习方法上给予的指导和择业道路上给予的帮助。感谢环境与能源工程学院的杨晖老师在学习上给予的指导,她对科研的专一态度值得我学习。感谢师兄师姐,在科学研究上为我解惑,在生活中为我解忧。感谢我的同门,让我的学习和生活充满快乐。感谢师弟师妹,在我的科研道路上给予的热情帮助和支持。感谢赵金姊同学,在我学术文论撰写时给予的无私帮助。感谢我的舍友,让我有一个轻松愉快的研究生生活。感谢我的家人,对我的理解与支持。最后,感谢评阅本论文的专家老师,谢谢老师在百忙之中抽出时间评阅此论文。
本课题是北京市自然基金重点项目“喷淋式烟气冷凝余热回收过程热质交换与净化协同强化机理研究”(00351911032)基金资助,特此一并致谢。
篇6:锅炉工作总结
新家园制砖锅炉房,现有司炉工及维修人员5人,平均年龄45岁,负责砖厂生产线锅炉正常工作及维修保养工作。几年来我们始终牢固树立“安全第一”的思想,时时刻刻不忘安全工作,坚持标准“学标、对标、达标”,作为锅炉房班长,在厂里领导正确领导下,出色地完成各项任务。现将我个人所做的工作总结如下。
一、统筹兼顾、突出重点狠抓安全
首先抓好班组的劳动安全工作,把劳动纪律作为整治重点,对班组内存在的违纪现象,认真组织分析讨论,落实整改措施,及时整改。保证安全有序可控。二是抓好设备质量检查,对于需要更换设备的及时向厂里汇报要求更换,确保设备安全可靠。三是严格锅里我班组工作人员按规定穿戴和使用防护服装和用品,有个别工作人员在焚火时不穿戴防护装备,造成不安全因素。每天都严格要求我班组锅炉工焚火时必须穿着厂部发工作服和用品保证职工劳动安全。为保证安全工作,重在日常抓安全,为班组制定“每日工作安排”,结合厂里对锅炉房的工作标准,特别制定的其内容:周一,安全阀试喷(车间领导监控)。周二,高低水警报试验(车间领导监控)。周三,机械各传动部位加油。周四,注水器上水试验。周五,除尘器清灰,打扫卫生。周六,煤,灰场清整。周日,环境卫生清扫。每月1号捅烟火管,每月1—3日,16—18日各冲洗一次压力表存水弯管(车间领导监控)。几年来,我们始终坚持执行,保证了安全生产的顺利进行。
二、认真学习,提高班组人员素质
厂里出台的一系列制度,打破了平均主义的分配方式,真正起到奖勤罚懒的作用,激发职工的积极性和奋斗精神。实施竞争上岗,使职工人人竞岗,促进职工技术和思想素质不断提高,使比较差的职工有压力,比较好的职工有动力,更好地调动职工的积极性,激励职工奋发学习业务,钻研业务技术,提高技术水平。每周坚持学习业务知识,不断提高班组人员的业务技能。结合我厂开展安全生产大检查、大反思和安全生产专项整治活动,根据现状查找隐患和不足。及时制定措施、整改。严格岗位卡死制度,使每个职工做到上标准岗,干标准活,不违章不违纪。向先进学习,向标兵学习,苦练本领,形成个个有绝招,人人有绝活,都不甘落后的好局面。
三、严格管理、落实工作标准
为更好的为制砖生产服务,为厂里服务,要求班组锅炉工有更高的标准,我们制定相关制度上墙,并与经济考核挂钩,锅炉房内使用的工具、用具、备品等都定置摆放,使锅炉房内整齐、美观,当班人员搞好自检自修,杜绝“跑、冒、滴、漏”现象。机械设备每班擦拭,做到铜铁分明,无油灰等,定期打扫卫生,做到文明生产,加强日常设备保养与维修工作,定期按规程、规定搞好锅炉洗炉保养工作。及时送验压力表、安全阀,当班人员
严格遵守操作规程,不简化作业程序,把经营责任制落实到岗、到人,加强检查考核,使每个人都有压力,目的是把规章制度执行好,更好地完成任务。
四、加强养修,保持设备良好状态
我们严格执行自检自修规定,要求当班人员做到小活不出班,大活不出车间,不带病交接班,同时要求杜绝“跑、冒、滴、漏”现象,强调锅炉本体和附机设备等班班擦拭,做到铜铁分明,班组长及时检查,加大考核。严格执行设备巡视制度,加大关键部位巡视,发现问题及时排除,对锅炉换季保养,严格按有关规章制度。按规定洗炉、及时整修及时调倒锅炉保障供气。认真做好锅炉本体和辅机的维护保养,保持锅炉各部件的整洁,油路畅通,保证设备处于完好状态。
五、存在不足和下一步打算
在领导的关怀下,我们班组虽然取得了一点成绩,但我们也清醒地认识到不足。1、进一步认真学习安全知识,强化安全事前控制水平。2、进一步加强责任心,更好地干好本职工作。
我们始终严格按照《安全合格锅炉房检查评比标准》进行对标检查,找差距,落实措施抓整改,狠抓锅炉人员业务技术水平的提高。我们有信心,有能力,在上级主管部门的领导下,按照锅炉安全操作规程标准化作业,提高自身的业务素质,严格作业程序,保证锅炉及设备的安全,不负重望,为跨越时发展作出贡献。
篇7:锅炉工作总结
20xx年即将过去,一年来,我做为一名锅炉运行人员,以饱满的工作热情,努力学习专业技术知识,严格遵守各项运行规程,虚心求教,团结同事,不断提高工作能力,干好本职工作,现将一年来的工作加以总结:
一 、在技术上用心钻研,理论上熟记操作规程,在现代的互联网及可得到学习资料的各种途径中寻找相关运行方面的资料;实践工作中严格遵守运行规程,培养个人独立操作能力,保证不发生误操事故,把工作中遇到的问题和取得的经验、注意的事项随时记下来,虚心向老员工和领导请教,个人能达到独立上岗,但深知要想锅炉专业学透学精,还需要时间的磨练、知识的运行要求。迎难而进,积极调整自己的工作思路,抓住重点,积极进行运行高运调整,取得了可喜的成绩,并得到了厂里领导的肯定。
二、能力包括协调能力和处理事故能力,若说“技术”比作“智商”的话,那么“能力”就可比作“情商”,锅炉专业亦是如此,智商高就不见得情商高,因为技术是死的,能力是活的。在各种突发事故中能够果断处理,将事故消灭在萌芽状态,使实发事件最小化。所以判断能力快速准确,活学活用,才能更好地干好工作。
三、积累工作经验,贯彻厂里“节能降耗”。在耗煤、耗水、耗电方面,节约每一斤煤,每一滴水,每一度电。本着安全运行为首要,兼顾经济运行。
四、在安全生产工作中,加大巡检设备力度、提高设备可靠性,合理调整锅炉运行方式,确保完成厂里下达的各项生产指标。避免人身伤亡、设备损坏、火灾事故、人为责任造成重大事故。
新的一年有新的开始,也有新的压力,制定新的合理目标才有新的突破。 所以我制定了的个人工作方向:
1、继续钻研锅炉专业技术,提高事故处理能力,争取锅炉运行更平稳,使锅炉负荷在安全、稳定、经济的情况下再上新高。
2、干好本职工作的同时,了解其他专业知识,争取早日达到 “全能操作”目标。
3、继续发挥团结协作精神,强化理念,鞭策自己有更高的认识和发展 。
在201x年的工作中我取得了一定的成绩,在技术方面有了新的突破,在工作中以主人翁的思想态度工作,全身心的投入到了厂里的工作中,不懈的努力取得了骄人的成绩。但我不会因为有了成绩而会放弃求新的步伐。我会继续努力工作,鞭策自己,为新家园贡献自己的一份力量!
篇8:锅炉申请书
xxxx监督局
我(单位)现向(你局)申请 锅炉使用登记 行政许可,并提交如下申请材料:
1、《锅炉登记卡》一式2份;
2、锅炉总图(加盖设计审核印章,验原件);产品质量证明书(复印件1份,验原件);制造过程监督检验证明(复印件1份,验原件);
3、进口锅炉安全性能监督检验报告(复印件1份,验原件,仅适用于进口锅炉);
4、锅炉安装质量证明书(复印件1份,验原件);
5、锅炉安装过程监督检验证明(复印件1份,验原件);
6、锅炉水质指标化验报告(复印件1份,验原件;有机热载体炉不需提供);
7、锅炉使用安全管理的'有关规章制度;
8、安全阀及压力表校验证明(复印件1份,验原件);
9、锅炉过户或异地移装证明(适用于移装的旧锅炉,提供原件存档);
10、检验结论为合格的锅炉定期检验报告(复印件1份,验原件;超过检验有效期或过户及异地移装锅炉需提供此报告); 11、营业执照或组织机构代码证。
申请人承诺:以上提交材料真实合法有效。 请依法审查并予以批准。
申请人签字(盖章)
年 月 日
篇9:锅炉申请书
xx村党委、村委:
xx小学教学楼后侧锅炉为xx小学、和xx村办公楼供暖。由于xx村办公楼、xx幼儿园采暖为地暖,地暖所需供暖水温为40℃既可,水温过高采暖管会有爆裂的可能;xx小学采暖为铸铁暖气片,供暖水温应在80℃以上。三个单位同用一个锅炉使我校采暖温度无法达到标准采暖温度。
自20xx年11月15日正式取暖开始,今年冬季又比往年寒冷而且时间比较长,我校今年学生因教室采暖温度无法达到标准采暖温度,导致手脚冻伤情况比往年人数有所增加。特向xx村党委、村委申请对xx小学采暖问题进行整改。整改措施:
1、为xx小学安装独立卧式锅炉1个。
2、将原有管道进行改造,使其与新锅炉对接,管道通畅。
请xx村两委对整改措施尽快作出整改意见。
此致!
xx小学
20xx.4.7
篇10:锅炉申请书
xx技术监督局:
由于我校后勤服务方式调整,现将我校一台锅炉申请报停使用,该锅炉信息为:型号:LSG0.1-0.04-AⅢH,单位内部编号:1#,设备名称为:承压蒸汽生活锅炉。
特此申请
xx中学
20xx年3月28日
篇11: 锅炉年终工作总结
回顾过去的一年,锅炉分厂在厂部的正确领导下,圆满地完成了厂部下达的各项生产任务,下面对锅炉分厂全面工作做如下总结:
一、加强安全管理,坚持安全第一,重在安全措施的落实
20xx年我们完成了一次大修、四次小修和部分电除尘改造工程,共完成机组非标和技术改造 48项。20xx年是锅炉分厂检修任务较繁重的一年,在全分厂职工的共同努力下,我们实现了全面无轻伤及重大设备损坏事故,为实现这一目标我重点做了如下工作:
1.年初围绕全年无轻伤和重大设备损坏,实现安全年这一目标,认真贯彻省公司安全生产一号文件精神,根据我分厂的具体情况进行分解,制定了以分厂主任为第一责任者的安全保证体系,完善了各项安全管理制度及考核办法。
2.充分利用“两个”安全大检查,突出两个重点,重点提高全体工作人员的安全意识,牢固树立“安全第一,预防为主”的指导方针,重点落实安全措施的落实,通过二次安全大检查,查出设备重大隐患26项,生产隐患164项,不安全因素24项,发现问题制定措施,落实责任,限期完成,收到良好效果,隐患消除率100%,从而保证了机组的安全运行。
3.加强对职工的安全教育,充分利用好每周一的安全活动时间,对每期上级及我厂的安全通报都进行复印,分厂主任签署学习要求,各班认真组织学习讨论,使每个职工都受到教育,举一反三,避免类似事故的发生。
4.加强规范化管理,使安全活动经常化和制度化,管理规范化,分厂今年按要求对204名职工进行了全员通考,合格率100%,做到了持证上岗。对大修期间使用的短期临时工进行安全教育和安规考试,合格后上岗。
5.加强对外包队伍的管理,对于外包队伍进入现场前进行安全教育,用安全事故实例对他们进行教育,并对进入现场应注意事项提出要求,实行安全措施学习并签字制度。
6.加强“两票”管理,狠反习惯性违章。安全生产是完成各项生产任务的必要条件之一,安全生产应放在各项工作之首,针对今年锅炉分厂重大非标项目多、工作量大等特点,强化工作人员的安全意识,重点从班组长抓起,尤其是大小修检修集中、交叉作业多的特点,制定切实可行的安全措施,重点做好安全措施的落实,坚持重大检修班长到位制度,分厂人员责任分工,重点部位更是加强管理,分厂主任、书记、安全员对检修现场不定期进行安全检查,发现问题及时纠正,对一些习惯性违章进行处罚,从而提高了全员的安全意识和自我防护意识,使习惯违章现象基本杜绝。
二、加大改造力度,使设备健康水平上一新台阶
年初,组织各班班长、技术员、生产骨干以班为单位就目前设备存在的问题及20xx年工作目标征集方案,分厂组织专工针对目前设备存在问题进行研究,确定工作目标,并进行可行论证,为厂部决策提供依据,如何采用新技术、新工艺解决生产难题。在厂部的正确决策下,锅炉设备健康水平上了新的台阶。
1.继续投入对锅炉受热面进行改造,通过几年的努力锅炉受热面状态逐步改善,我们在改造的同时加强对受热面的检查,重点对尾部受热面磨损的防治和过热部位的治理,辛勤的劳动必然结出丰硕之果,20xx年“四管”漏泄的次数比XX年显著减少,XX年“四管”漏泄13次,20xx年(到目前)漏泄5次。
2.制粉系统的综合治理已收到明显的效果,设备的可靠性和文明生产有了显著的提高。
3.空气预热器的改造,使改造前的漏风率从20%降到7%以下,使机组的效率得到很大的提高,为CCS的投入奠定了基础。
4.加强对重要辅机的检查工作,尤其对轴流风机加强检查,不放过每一次的检查机会,同类型电厂的经验和教训鞭策了我们,在检查中曾发现了两次轴流风机叶片裂纹,得到及时的处理,从而避免重大设备损坏事故的发生。
5.对燃油系统的管理和炉前油系统的口焊进行了彻底处理,使油系统的可靠性大大提高。
6.对#2炉电磁泄放阀进行了改造,解决困扰我们多年的电磁泄放漏泄问题。
7.对高压阀门的检修,今年我提出了阀门的检修、小修按大修管理,解决由于小修时间短使阀门失修的问题。今年未发生一起阀门外泄事故,提高了机组的可靠性。
另外,我们还完成了三号炉燃烧器反切风改造工作、燃烧器喷咀体的防磨处理和磨煤机润滑油加热器改造论证工作,为锅炉设备的安全稳定运行奠定了基础。
三、提高职工的综合素质,检修做到规范化
随着我厂提出创国际一流火电厂的目标步伐,我们提出管理逐步和国际接轨,检修做到“标准化作业,规范化管理”的目标,检修项目落实到人,层层落实责任制,作业负责人为所负责的项目,从安全生产、文明生产、检修质量、检修工期全面负责,班组进程管理,分厂把关,落实三级验收自检为主的方针,检修质量和业绩考核与奖金挂钩,继续推行“工序卡”制度,并试行了作业指导书制度,从而使工作人员在检修工作中有法可依、有章可循。通过近两年的宣传、教育和实践,从职工逐步认识到,规范管理重要性,俗话说“没有规矩不成方圆”,通过规范化管理的逐步运作,使锅炉分厂总体检修水平有了进一步的提高,今年的一次大修、四次小修没发生过较大检修失误,为以后的检修工作起到指导性工作。
一、安全生产方面
1.坚持“安全第一,预防为主”的方针,加强对职工进行安全教育,提高职工安全意识,真正做到不伤害自己,不伤害他人,不被他人伤害。
2.建立健全分厂安全管理机制,加大安全考核力度,认真学习安全规程,让安全生产管理人员在工作中能够有章可循,有法可依,并严格执行安全管理制度。
3.认真做好各项安全措施,尤其是重点班组、重点工程、重点施工场所安全措施的落实,如锅炉炉膛内作业、大件的吊装、制粉系统煤粉管道大修、磨煤机大修、燃烧器改造等。
4.提高检修质量,搞好技术培训工作,及时消除重大设备隐患,不出人为责任设备损坏事故,提高设备健康水平,确保机组安全稳定运行。
5.加大反习惯性违章力度,树立“违章就是事故”的观念,坚持预防为主的方针,把各类违章消灭在萌芽状态,实现全年无轻伤。
6.控制火灾事故的发生,重点加强炉前油系统的防火和制粉系统漏泄治理工作。
在油系统上作业,必须办理明火工作票,要求工作责任人及每个作业人员熟知作业范围和安全措施,在工作过程中加强检查,实现火灾事故为零。
另外,对分厂负责的安全设施做好日常维护,进行定期检验,保证随时好用。
7.认真做所辖设备的安全性评价工作,从中找出设备的问题点,并做好改进、防治措施。
二、培训与管理工作
1.完善分厂各项管理制度,把我们的管理水平逐步向国际一流的管理标准靠近,对我们已有的管理制度进行重新修订,对不合理的部分进行讨论、修改,对于不完善的部分予以补充,对应进行规范而没有现成制度的,要制定新的规章制度,真正做到分厂内部的每项工作都有一个统一的标准、模式,主要表现在分厂内部的公文的格式、运行方式、技术记录的格式、设备档案的格式、会议记录的内容、格式等。
2.在检修作业中,继续完善和执行“工序卡”和“检修作业指导书”制度,力争在20xx年#2机组大修中所有标准项目均执行检修作业指导书,所有非标项目均有为保证进度和质量的工艺卡做指导。
3.在厂部领导下,建立ISO9000质量管理体系
一个企业只有建立并完善了ISO9000质量体系并通过认证,可能证明这个企业在质量管理上达到了国际标准,我厂要想创建国际一流火力发电厂,通过ISO9000质量体系的认证是必须的,我们分厂一定全力支持厂部这项工作。
4.重视科学技术人才的培养,充分发挥工程技术人员的作用,为工程技术人员创造条件,调动他们的积极性,使他们有机会了解和掌握先进的技术信息,大力提供采用新产品、新材料、新工艺和新技术。
5.抓好生产培训工作,严格按照《电力工人技术等级标准》进行培训和考核,并以此做为竞聘上岗、提岗的重要依据。
6.加强对特殊工种的培训,尤其是焊工的培训工作,争取在二季度使异种钢合格焊工达到8~9人,以适应受热面改造以及企业走向市场的需要。
7.完成工程技术人员班组之间的交流,拓宽他们的知识面,培养技术多面手和技术尖子,以适应走向电力市场的需要。
三、生产任务
20xx年锅炉分厂将完成#2炉大修、#2炉电除尘改造部分安装和质检工作,#1炉小修、#3炉小修、#4炉小修以及四台机组维护工作。
#2炉大修是锅炉分厂20xx年工作的重中之重,我们将针对#2炉运行情况,存在的缺陷和今年小修检查结果,根据厂年度检修计划的要求,确定检修重点项目,制定符合实际情况的对策和措施,做好大修工程开工前的各项准备工作。
大修施工阶段是检修工作最紧张的阶段,在此阶段我们应做到:
1.贯彻安全工作规程,检查各项安全措施,确保人身和设备安全;
2.检查落实岗位责任制,严格执行各项质量标准、工艺措施,保证检修质量;
3.随时掌握施工进度,加强组织协调,确保如期竣工;
4.贯彻勤俭节约原则,爱护工具、器械,节约原材料;
5.搞好文明检修,培养踏踏实实、一丝不苟的工作作风;
6.关心检修人员生活,注意职工健康。
在大修中力争实现质量好、工期短、检修费用低、安全好和检修管理好的目标,为确保检修质量,我们将大力提倡、推广、完善检修作业指导书,大修后积极主动地配合运行人员做好修后试验工作,并制定切实可行的维护措施,以进一步确保大修能够创全优。
#1炉小修、#3炉小修和#4炉小修是机组全年唯一次计划检修,是难得的消除设备缺陷的机会,也是检查设备健康状况的良机,所以,在明年三台炉的小修中,锅炉分厂要抓住机会,以大修的管理标准去做好小修的修前准备。施工中的管理以及修后试验工作,杜绝麻痹思想,保证小修质量,并为以后大修项目的确定寻找依据。
#2炉电除尘改造是我厂四台炉中改造的第三台,工期安排恰好与#2炉大修同步,从工期上看是不利因素,但我们仍将抽出部分技术力量,总结前两次改造工作中的经验教训,力争做好质检工作,杜绝前两次改造过程中出现的问题重现。
结合目前机组运行情况,总结以往检修经验,为保证机组继续维持一个较为健康的状态,减少故障的发生,本着提高设备可靠性的目的,在明年的大小修及维护中,我们计划完成以下几项重要项目:
1.#2炉受热面的改造工作;
2.磨煤机润滑油加热器改造;
3.风机入口暖风器改造;
4.#3、#4炉电磁泄放阀改造;
5.#2炉一次风机叶片的更换;
7.原煤斗防棚煤装置的完善;
8.#2炉电除尘改造部分项目施工;
9.#2炉煤粉管道防磨及大修等等。
四、挖潜降耗,降低生产成本
1.加强职工思想教育,在职工心中树立勤俭节约的思想,使降低检修费用在分厂每位职工的心中占重要位置,营造一个节约光荣、浪费耻辱的良好氛围。
2.针对勤俭节约、降低费用制定有关的规章制度,健全材料领用管理制度,从管理上杜绝浪费的发生。
3.大力提倡修旧利废工作,备件工具等损坏可修复的,决不批准领用新的,减少不必要的支出。
4.在资金密集的项目上多下功夫,比如磨煤机易磨损件,严格控制磨辊使用周期,保证不发生磨辊磨穿的事件,力争多修复,少购买,节约材料费用支出。
5.加强设备巡回检查,做好设备维护工作,尤其是今年磨煤机减速机损坏频繁,减速机修理费用巨大,为减少此项开支,一方面要严格监视润滑油系统,从系统上予以改造;另方面,要下力量对润滑油质量进行研究,提高减速机轴承、齿轮等使用寿命。
五、为厂创国际一流火力发电厂做贡献
开展阶建国际一流火力发电厂工作是深化改革、建立现代企业制度、发展电力工作的需要,是实现管理科学化、规范化、现代化与国际先进水平接轨的需要,是提高经济效益、增强企业凝聚力、促进企业自身发展的需要。 我们分厂已经制定了《锅炉分厂创建国际一流电厂规划》,在《规划》中,我们对照《国家电力公司创建国际一流火力发电厂考核标准》查找自身存在的问题,找出我们和一流标准的差距,从安全、质量、技术、管理、员工素质、企业文化等几方面制定了切实可行的措施规划,争取在铁岭发电厂创国际一流火力发电厂的工作中,为全厂起一个带头作用。
20xx年即将过去,新的世纪即将到来,锅炉分厂一定会在新的一年里,以新的姿态做好每一项工作。
篇12: 锅炉年终工作总结
回顾已经过去的XX年里,车间严格按照公司“质量是企业生存的根本”和“安全重于泰山”基本原则。在公司的正确领导和各部门积极协助下,紧紧围绕以安全生产为中心,确保产品质量的前提下,积极克服诸多不利因素,不断完善强化车间基础管理工作,狠抓落实生产过程控制,强化产品质量,经过公司全体干部职工的共同努力,车间的综合管理工作逐步提高,保证了公司销售工作的正常进行。
一、自XX年3月至12月底,经过车间全体职工齐心努力及公司其他部门密切配合。特别是6--9月份,全体职工积极克服操作人员紧张、车间工作环境高温、锅炉及变压器等设备在超负荷运行的不利因素下,根据销售人员的要求及时调整产品品牌,满足客户的需求。在保证产品质量和安全生产的前提下,精心操作,共生产优质产品3600余吨,保证了公司销售和市场进一步的拓展。
二、与化验室主任、经理制订完善了操作规程及设备运行记录表,特别是设备运行记录表为提高产品质量和设备安全运行,打下了良好的基础。生产过程中根据化验室产品化验结果,及时对生产过程中的设备运行参数及时进行调整,确保产品质量,为公司销售提供了有利保障。
三、根据公司生产规模的扩大和销售市场的拓展,结合车间的生产实际情况,调整生产人员班次,聘用了部分新员工,对新、老员工进行合理搭配,采取了由班组长牵头,老员工具体负责的方式,及时加强新员工的培训,对新员工的工作业务技能、安全生产知识等进行传、帮、带。新员工积极认真的学习岗位操作技能、安全生产和自我安全防护意识,已经能完全胜任车间安排的岗位工作。实现了XX年全年生产无重大安全生产责任事故。
四、并积极组织协调车间人员参与公司第三、四期产能扩建工程(含厂房及设备、锅炉改造等),为明年的公司生产和销售工作夯实了基础。
五、XXX公司工多次来我公司进行技术指导,调整产品液配方并进行生产,产品已通过了严格的检测,优化确定了产品生产配方,为以后的公司产品质量提高提供了有利保障。并于XX公司XX工和XX公司XX工进行交流,确定了聚乙烯醇厂家及品种。
六、根据公司的发展要求和实际情况,9月份与董经理共同到青岛、淄博等地学习考察,借鉴其他厂家真石漆、岩片漆先进生产经验,多次调整试验真石漆、岩片漆及配套底、面漆配方,并进行了试生产,为明年公司真石漆、岩片漆生产销售提供了充分保证。
七、3―10月份,在XXX集团新建XX车间和XX扩建工程中,克服高温酷暑天气,积极组织协调人员进行压型瓦加工,产值20余万元。施工人员克服人员少、维修工程临时性、突发性的特点,经过施工队全体员工积极努力下,在保证施工安全的前提下,全年共计完成产值130余万元。管理机构,是承上启下、沟通内外、协调左右、联系四面八方的枢纽,是推动各项工作朝着既定目标前进的中心。提高管理及操作人员加强内部管理对长远发展至关重要观念。要树立“任何小的改进都是进步,任何小的误差都有可能导致意想不到的后果”思想观念和“追求、沟通、改进、创新”的意识。按照“高标准严要求”的原则,深刻的反思与检讨,急需改进和提高的地方。提高综合管理水平,跟上生产发展的需要。为了总结经验,发扬成绩,克服不足,扬长避短。针对当前工作现状,调整今后的工作思路,加强安全生产和产品质量的控制管理。在明年的工作中积极采取以下几项措施:
篇13:锅炉年终总结
供暖公司自成立之日起,积极响应一个声音、十分努力、百般维护、千万珍惜的精神以及供暖公司提倡的融瑞丽治业精神、暖社区四季如春的服务理念,结合甲方工作的指导方针与瑞丽物业的服务宗旨,认真贯彻执行上级交予的供暖任务,接受任务后能够迅速做出安排,在甲方及物业各部门的支持与配合下,基本能够圆满完成赋予的各项供暖工作任务,保障供暖工作的正常运行。
通过近段时间来的供暖工作,我们取得经验的同时也发现了存在的问题,针对以往的工作及今后工作的顺利进行,我们从以下几个方面进行了总结:
一、前期工作
1、签收供暖协议;制订执行融合供暖结构组合方案;制订、制作锅炉房各项规章制度、锅炉房各种标牌、交接班记录表、维修工具等;到×××供暖办办理锅炉房供暖形式的证明;司炉、维修人员定位(10月8日赤城人员到位)进行岗前培训及熟悉锅炉供暖系统和附属设备情况;成立供暖公司技术组;巡视、检查锅炉房各供暖系统等前期准备工作。
2、在甲方的主导和锅炉安装队及施工方有效的配合与支持下,小区于10月22日、23日进行了锅炉注水试压工作。总体来讲,没有出现较大的问题基本顺利(南区板楼试验完成54,家中无人28。北区塔楼试验完成47,家中无人30)。但是通过打压检查发现:北区塔楼存在主要问题有管道井、调节阀漏水、法兰盘垫漏水、过滤阀接口处漏水、采暖计量表接口处漏水、住户三通阀漏水和住户室内地埋管漏水,以及塔楼末端图纸没有设计安装压力表,不便于锅炉房人员观测了解末端压力,造成锅炉房无法准确定压;南区试压情况较好,个别存在滴、漏水现象。以上问题发现后在本部门人员与施工方及各部门配合下已全部解决。
3、小区于11月5、6日进行供暖系统低温调试运行,11月15日开始正常供暖,供暖面积南区69557。33㎡,北区118888。90㎡。这期间出现的问题基本得以解决。如:南、北区锅炉房补水泵电磁阀和压力传感器未装、保温未做、热交换器在使用过程中后固定压紧板处漏水、二次循环泵的起动电流超出主进线电缆额定功率等等;土建方面卫生间马桶缺马桶盖、卫生间顶子缺吸音板、锅炉房内吸音板部分损坏并且有脏物、污水井盖、下水箅子应刷漆、排污管、自来水进水管周边未封堵严向锅炉房内漏水、烟道生锈有杂物、门窗需刷漆等外观方面;13#塔楼(04、05、0xxxx型)、13#1004室高低区供回水供暖系统管道井接反等现象。
4、维修供暖系统中出现的问题:暖气不热、供暖系统噪音、采暖系统跑、冒、滴、漏水,并成立维修监察回访组,监察回访对出现的问题维修工是否予以彻底解决以及室内测温、水质化验等工作。
二、能源耗损供热锅炉房年终总结
南区锅炉房至今购买天燃气270000m3,北区锅炉房至今购买天燃气264000m3,共计96120xxxx。在确保锅炉房设备安全运行的情况下,司炉人员应根据天气变化,调整锅炉出水温度。保证业主居室内温度不得低于16°c。根据南北区锅炉房供暖面积,制定了节约能源的基本标准)。
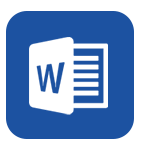
【锅炉毕业论文(精选13篇)】相关文章:
护理类毕业论文开题报告范文2023-08-11
太原电厂实习报告2023-04-01
电厂实习报告2022-08-11
扬州二电厂实习报告2023-03-03
电气自动化毕业实习报告2023-02-07
发电厂实习总结2022-09-10
跨栏开题报告范文2023-09-16
水电厂实习报告2022-11-29
电厂实习报告8000字2023-09-28
酒店锅炉房员工个人工作总结2023-06-19