精益生产开题报告(共12篇)由网友“kk”投稿提供,下面小编给大家整理后的精益生产开题报告,欢迎阅读!
篇1:精益生产开题报告
一、选题的背景与意义:
目前,国内制造业成本压力越来越大。随着中国经济“高增长,低通胀” vn 黄金时代的结束,高通胀改变了产业层面的成本和价格,进而影响到了企 业的盈利。第三次经济危机爆发以来,国内企业明显感受到各类成本讯 速上升而带来的巨大压力。在企业成本压力增大的同时,企业对产品的要 求也越来越高:产品需求越来越多样性、产品交货期越来越短、产品质量 要求越来越严格,可是产品的价格方面却没有明显提高。而且国内的人工 成本也有大幅度的提升,这使得企业的生存越来越难。在这种大环境下, 越来越多的企业把目光头像了管理层次和车间现场管理方面。总的来说, 目前国内的制造业急需实施精益生产方式来降低成本提高企业竞争力。
自从日本丰田汽车公司打造出丰田汽车生产系统后,历经几十年持续不 断的尝试与努力,从消除企业内部一切浪费MUDA、不合理MURI、不均衡MURA 开始,积极进行改善改进活动,来提高企业竞争力。丰田汽车生产系统使 丰田汽车公司在世界同行的竞争中脱颖而出。因此丰田汽车生产系统广受 全球各界的重视。随后美国麻省理工学院根据其在“国机汽车项目”研究 中基于对日本丰田生产方式的研究总结成精益生产的生产管理系统方法。 精益生产主要用来改善企业体制,提高生产力和企业竞争力。 本篇毕业设计是针对浙江泰德光学有限公司金属 部半成品车间进行精益生产方式的研究。
通过将近一个月的实习生活,我了解到泰德光学目 前的主要问题有如下几个:1、车间加工成产效率较低,2、没有形成一个 良好的流水线作业系统3、搬运浪费、动作浪费、库存浪费等随处可见4、工人不能自觉的努力工作。针对此企业的这些问题,我认为现在急需对泰 德光学实施精益生产管理方式来提高企业竞争力。为了提高泰德光学有限 公司的竞争力,我要运用均衡化生产和现场改善两种方法对泰德光学金属A 部进行改善,最终达到降低成本提高生产效率的目的。
二、研究的基本内容与拟解决的主要问题:
本文首先分析了国内外制造企业的现状,并说明了研究精益生产的重要 意义。然后提出了运用均衡化生产和现场改善两种精益生产方法对泰德光 学金属 部存在的问题并分析原因,然后引入精益生产的两种方法均衡化生产和现场改善对其进行改 善,提出相关的措施。 本文通过理论研究和实地调研相结合的方法,在论文拟写期间我在泰 德光学进行生产实习,在管理部门的支持下,深入生产现场和公司管理部 门,收集相关资料,对生产管理现状有了一定的了解。
通过对在企业收集 的数据分析整理后得到以下主要问题需要解决:
1)整个车间的生产没有形成一个生产线系统 2)车间内各工序生产不平衡 3)因生产不均衡导致的人员、设备、库存浪费问题 4)车间内原材料、半成品、工具等摆放杂乱 5)员工的整体素养低下,不能百分百的投身到工作上
为了解决以上问题我提出了一下要研究的主要内容:
因为泰德光学金属 部的生产没有形成一个生产线系统,这造成了生产效率的低下,因此我要对金属 部车间进行“一个流生产”的研究。主要目的就是使整个车间的生产形成一个流水线系统。 “一个流生产”就是把各个工序、生产线衔接起来,形成整个工厂一 体化生产。
实现“一个流生产”的主要要点如表1: 一个流生产 主要要点 实行单件流动 按加工顺序布置设备 生产同步化 员工的多能工化 站立式走动作业 设备合理布置和设计 制定生产节拍 表1“一个流生产”主要要点 完成“一个流生产”后,就需要进行缩短作业切换时间的研究了。缩 短每次作业切换时间是实现生产流程化的关键,也是实现生产均衡化的前 提。
缩短作业切换时间主要有四个步骤如图1 所示: 在完成缩短作业切换时间之后,就要进行混流生产的研究了。混流生产就是指将工艺流程、生产作业方法基本相同的若干个产品品种,在一条流 水线上科学的编排投产顺序,实行有节奏按比例地混合连续流水生产。
混流生产的主要方法有两种:一种是轮排法,一种是生产比导数法。运用这 两种方法实现混流生产后就基本上实现了均衡化生产。 实现均衡化生产后还需对泰德光学金属A 部车间进行现场改善。现场改 善主要的主要方法包括5S 管理、目视管理两种。通过这两种方法对“车间 内原材料、半成品、工具等摆放杂乱”“员工的整体素养低下,不能百分百 的投身到工作上”这两个问题进行解决,达到现场清洁员工素养提高的目
三、研究的方法与技术路线:3.1 研究的主要方法如下:
运用“一个流生产”、缩短作业切换时间、混流生产三种方法实现均衡 化生产,然后运用5S、目视管理实现对现场的改善。
3.2 技术路线
四、研究的总体安排与进度: 17日:毕业答辩。
五、主要参考文献:
[1]熊卫国,何为红.精益生产模式与全面质量管理[J].江西煤炭科技.(01).
[2]张冬匀.基于精益生产理论的生产现场改善方法的应用[J].机电工程.(10).
[3]王开忠.HL公司精益生产应用与研究[D].华南理工大学,. 基于精益生产的现场改善[J].机电工程, 2011, 28(12). 基于精益生产的SY公司现场改善研究[D].武汉理工大学 工业工程硕士论文, . Engel.Knowledge Management LeanProduction Systems ProcediaCIRP,Volume 2012,Pages 436C441.
[4]Kasra Ferdows,Building factory fitness[J]:Emerald Journal,2011.
[5] Aysun Bozanta. Multi User Virtual Environments SeriousGames TeamBuilding. [J].Procedia Computer Science,2012,15.
[6]王玖河,周荣辅.我国制造业推行精益生产方式的对策研究[J].经济管理学院,.
[7]魏鹏飞.精益生产实施关键因素及评价体系研究[J].管理与经济学部,.
[8]王树贵.经营管理过程中的精益生产方式[J].经营与管理.2011(10).
[11]肖正斌. 精益生产方式下海湾轮毂公司现场改善研究[D]. 燕山大学, 2012. 指导教师审核意见:
篇2:精益生产开题报告
1.选题 :基于精益生产的制造业现场改善研究
2. 论文选题背景和研究意义
2.1论文的选题背景
随着世界经济全球化和多元化的发展,市场也逐渐从卖方市场向买方市场转变。面对着复杂多变的个性化市场需求,各国企业都感受到前所未有的巨大的竞争压力。在“规模经济”向“范围经济”演化的大背景下,目前世界加工制造业也在逐步尝试由传统的大量生产、批量生产方式向多品种小批量生产方式转化。企业之间的竞争也不再是单纯的价格竞争,而是表现为以产品设计、质量、成本、交货时间、对顾客需求的反应速度、售后服务、供应链等为中心的综合实力的竞争。很显然,传统的大规模生产模式下的管理思想和管理手段己不能满足目前生产实际的要求,因此各制造企业纷纷把目光投向了更适用于小批量、多品种、低消耗的生产管理模式――精益生产。
精益生产起源于丰田生产方式。二十世纪中期以后,在对美国汽车大量生产方式进行深入研究的基础上,日本丰田公司逐步创立了一种全新的多品种、小批量、低成本、高效率、低消耗的生产方式―即丰田生产方式(TPS)。凭借这一先进的生产方式,日本汽车在20世纪70年代的石油危机中脱颖而出,迅速占据了美国汽车市场,使日本一度超过美国,成为世界第一汽车制造大国,年产量达到1300万辆,占世界汽车总产量的30%以上。
为了研究日本汽车成功的奥秘,1985年初,在麻省理工学院(MTI)的提议下,以该学院的16名著名教授为核心,成立了“国际汽车计划(lMVP)”。这是一个汇集了14个国家,53名汽车产业研究人员的国际研究网络。他们耗资500万美元,用了5年的时间对近90个汽车生产厂进行了调研,经过对比分析,在1990年他们出版的著作《改变时间的机器》一书中首次提出了“精益生产”的概念,并对其思想和内涵作了全面的描述,认为它能够广泛使用于各个制造行业,将成为未来21世纪制造业的标准生产方式。
现场改善是现场管理的一种延伸,它以增进顾客满意为目标,使用持续改善理论对生产现场的人、机、料、法、环等各生产要素进行持续的改善。实行现场改善活动,可以挖掘资源的潜能,消除各个环节的浪费,以较小的投入、较低的风险换取较大的收益。同时,通过团队合作,增强企业的凝聚力和竞争力,为企业的创新奠定基础。
2.2 论文的研究意义
生产现场是企业直接创造效益的场所,是企业所有信息的原始发源地,也是各种问题萌芽产生的场所。企业向社会和市场提供的商品要通过生产现场制造出来,投入生产的各种要素在生产现场转换成生产力。在生产制造过程中,现场汇集了计划、生产、同时也直接暴露出企业在生产效率、产品质量等各方面的问题。从某种意义上说,生产现场是企业的主要战场之一,要实现现场的高效运转就必须对其进行有效的现场管理。现场改善是现场管理的深化,是对现场管理中发现的问题有计划、分步骤地进行分析和解决,是一个永无止境的优化过程。现场改善给企业带来巨大的效益。
精益生产方式比现有批量生产方式有更多的时间、空间和库存的节省,而且工序越短越减少品质风险且易于管理和控制。而且精益生产方式是靠需求驱动而不是供应。为在激烈的竞争中取胜,不得不把眼光转向了精益生产方式,希望冀此改善目前的竞争劣势,改善目前的工艺及管理状况。因此公司成立专门项目组对此进行研究,并且寻求可行性方案。并且想以此为锲机来推动整个公司的管理和业务上一个台阶,公司上层可谓对此寄以厚望。基于精益生产的制造业现场改善研究具有重要意义。
3. 国内外的基于精益生产的制造业现场改善研究现状及趋势
3.1基于精益生产的制造业现场改善国外研究现状
国外的研究开始比较早。从泰勒的科学管理理论开始,人们就一直致力于生产现场的改善工作。小的改善累积起来,推动人类社会从最早的手工生产发展到现在的柔性生产、大规模定制以至于敏捷制造。在此过程中,现场改善理论也被不断充实完善,出现了一系列有效的改善理念和改善方法。
19世纪末,吉尔布雷斯夫妇对生产过程中工人的动作进行了研究,理论通过对操作动作的分析和改善,去除不合理的、浪费的以及不安全的动作,达到降低作业疲劳度、提高工作效率的目的。其中的“基本动作要素分析”和“动作经济原则”等理论方法一直沿用至今。
20世纪40年代,美国通用电器公司的设计工程师麦尔斯首创了“价值工程(VE)”改善方
法。后来这一方法被融入工作现场,形成了现场改善的VE理念。它以“价值”、“功能”和“成本”为研究对象,强调通过提升功能和降低成本,实现产品和工作价值的提升。
日本学者经过30多年的实践总结,在1986提出了“55”的管理方法,它是通过对现场中“物”这一要素所处的状态不断进行整理、整顿并形成制度习惯的现场管理活动,它的实施在塑造企业形象、降低成本、改善现场条件等方面发挥了重要作用。55的提出冲击了整个现场管理模式,逐渐发展成为企业现场改善必须完成的基础任务。
日本学者清水万里在工业工程(EI)的基础上创立了“定置管理”理论和方法,并在《定置管理入门》一书中对其进行了系统的阐述。它侧重于研究生产现场中人、物、场所之间的位置关系,追求各生产要素的最佳结合,达到提高工作效率的目的。
20世纪80年代末,为了应付来自日本的竞争,摩托罗拉公司的比尔・史密斯和迈克尔・亨瑞等人提出了“六西格玛质量管理”方法。其中六西格玛不单是一条统计术语―代表缺陷率为百万分之3.4―更是一种管理理念。它关注客户的满意度,强调过程思维和基于数据的决策,主张事前预防和主动管理,通过团队合作对产品质量进行持续改善,以达到六西格玛目标。
为了消除“清除瓶颈”、“ 六西格玛”等优化活动局限于局部的弊端,,迈克・鲁斯和约翰・舒克在他们的著作《价值流图析》中提出了价值流图的分析方法。它把价值流定义为“产品通过其基本生产过程所要求的全部活动”,利用直观的图形工具对过程中不增值的活动进行全面的优化改善。
3.2基于精益生产的制造业现场改善在我国国内的研究现状
国内的现场改善研究目前处于起步阶段,还没有形成一个完整的体系,主要是总结和模仿日本的“5S”管理、目视管理以及欧美的“六西格玛”管理等方法,鲜有理论创新。然而中国的国情毕竟与国外不同,因此如何将现场管理理论精髓和我国的实际情况结合起来,实现理论上的突破与创新,就成为眼下我们急需解决的一个问题。
4.论文研究的方法、技术路线和写作计划
4.1本文研究方法、技术路线
本文对对于精益生产的制造业现场改善进行了论述和分析,并结合本人所在的xxx公司现场改善的自身特点,分析了xxx公司在现场改善方面遇到的挑战和难题,并给出了相关的解决方案。
该论文是笔者结合自身的工作实践写作而成,企图为所在行业的现场改善薄弱的之处提供解决方案,参阅了大量的相关论文与专著,并收集了工作实践中大量的数据和资料,并结合所在公司自身的特征,通过理论分析,事例举证,定性和定量分析的方法来进行论述。
4.2本文写作计划和纲要
本文首先对现场改善的方法展开研究,在此基础上,结合精益生产理论和方法,提出了基于精益生产的现场改善方法体系,并论述了各方法的功能和相互之间的联系,然后以企业为例对该方法体系进行了应用研究。本文选择了本人所在的日本企业xxx公司作为研究对象,分析了目前现场改善的现状以及提出了相应的改善与提升措施, 本文主要对现场改善进行了分析,提出了改善建议。
5.主要的参考文献为:
[1] 张广军, 马立宏. GIS技术在物流分析中的应用[J]. 物流技术, ,(03)
[2] 张新敏, 韩天渊. 齿轮车间物流分析与设备布置[J]. 机械设计与制造, ,(04)
[3] 叶慕静, 周根贵. 基于遗传算法的系统布置设计及初步应用[J]. 工业工程,2005,(03)
[4] 张承谦. SLP及其在调整生产布局中的应用[J]. 运筹与管理, 1995,(04)
[5] 张承谦. 物流分析在机械行业技改中的应用[J]. 机械管理开发, ,(03)
[6] 高举红, 陈思宇, 刘晓宇. 基于精益设计的生产能力分析与现场物流改善[J]. 工业工程, ,(01)
[7] 荣朝和, 张广军. 应用于物流分析的GIS技术[J]. 物流科技, 1998,(03)
[8] 程国全. SLP法在化工厂总平面布置中的应用──工业工程专业优秀毕业设计介绍[J]. 物流技术与应用, ,(02)
[9] 杨宝德. 加强企业物流研究是提高效益的重要途径――纪念国际物流专家理查德・缪瑟来华讲授SHA、SLP 20周年[J]. 工程建设与设计, ,(07)
[10] 范俊生. 系统动力学仿真模型参数的选取[J]. 西安工业大学学报, 1990,(Z1)
[11] 黄正夏. 日本的“精益生产方式”[J]. 世界汽车, 1994,(01)
[12] 郝仲敏. 转变思维方式是推行精益生产方式的前提条件[J]. 机械管理开发,1995,(04)
[13] 毛履平. 一汽推行精益生产方式的经验[J]. 机电信息, 1996,(01)
[14] 万侠. 生产方式上的一场变革――精益生产方式在一汽集团公司的推行与实践[J]. 企业研究, 1994,(09)
[15] 赵惠元. 论船舶管理与效益[J]. 航海技术, 1995,(01)
[16] 巴连良, 杜瑞成, 贾玲玲. 关于高校科研管理的思考[J]. 山东工程学院学报,1995,(01)
[17] 刘文志. 推行精益生产方式 振兴黄河汽车事业[J]. 政策与管理, 1996,(05)
[18] 何为精益生产方式[J]. 机电信息, 1996,(01)
[19] 王玖河. 精益生产方式下的质量控制研究[J]. 科技与管理, 2002,(02)
[20] 杨龙琴, 毛振龙, 柴改珍. 与时俱进抓管理 夯实基础保质量[J]. 山西建筑,2003,(12)
篇3:精益生产论文的开题报告
一、选题的背景与意义:
目前,国内制造业成本压力越来越大。随着中国经济“高增长,低通胀” vn 黄金时代的结束,高通胀改变了产业层面的成本和价格,进而影响到了企 业的盈利。第三次经济危机爆发以来,国内企业明显感受到各类成本讯 速上升而带来的巨大压力。在企业成本压力增大的同时,企业对产品的要 求也越来越高:产品需求越来越多样性、产品交货期越来越短、产品质量 要求越来越严格,可是产品的价格方面却没有明显提高。而且国内的人工 成本也有大幅度的提升,这使得企业的生存越来越难。在这种大环境下, 越来越多的企业把目光头像了管理层次和车间现场管理方面。总的来说, 目前国内的制造业急需实施精益生产方式来降低成本提高企业竞争力。
自从日本丰田汽车公司打造出丰田汽车生产系统后,历经几十年持续不 断的尝试与努力,从消除企业内部一切浪费MUDA、不合理MURI、不均衡MURA 开始,积极进行改善改进活动,来提高企业竞争力。丰田汽车生产系统使 丰田汽车公司在世界同行的竞争中脱颖而出。因此丰田汽车生产系统广受 全球各界的重视。随后美国麻省理工学院根据其在“国机汽车项目”研究 中基于对日本丰田生产方式的研究总结成精益生产的生产管理系统方法。 精益生产主要用来改善企业体制,提高生产力和企业竞争力。 本篇毕业设计是针对浙江泰德光学有限公司金属 部半成品车间进行精益生产方式的研究。
通过将近一个月的实习生活,我了解到泰德光学目 前的主要问题有如下几个:1、车间加工成产效率较低,2、没有形成一个 良好的流水线作业系统3、搬运浪费、动作浪费、库存浪费等随处可见4、工人不能自觉的努力工作。针对此企业的这些问题,我认为现在急需对泰 德光学实施精益生产管理方式来提高企业竞争力。为了提高泰德光学有限 公司的竞争力,我要运用均衡化生产和现场改善两种方法对泰德光学金属A 部进行改善,最终达到降低成本提高生产效率的目的。
二、研究的基本内容与拟解决的主要问题:
本文首先分析了国内外制造企业的现状,并说明了研究精益生产的重要 意义。然后提出了运用均衡化生产和现场改善两种精益生产方法对泰德光 学金属 部存在的问题并分析原因,然后引入精益生产的两种方法均衡化生产和现场改善对其进行改 善,提出相关的措施。 本文通过理论研究和实地调研相结合的方法,在论文拟写期间我在泰 德光学进行生产实习,在管理部门的支持下,深入生产现场和公司管理部 门,收集相关资料,对生产管理现状有了一定的了解。
通过对在企业收集 的数据分析整理后得到以下主要问题需要解决:
1)整个车间的生产没有形成一个生产线系统 2)车间内各工序生产不平衡 3)因生产不均衡导致的人员、设备、库存浪费问题 4)车间内原材料、半成品、工具等摆放杂乱 5)员工的整体素养低下,不能百分百的投身到工作上
为了解决以上问题我提出了一下要研究的主要内容:
因为泰德光学金属 部的生产没有形成一个生产线系统,这造成了生产效率的低下,因此我要对金属 部车间进行“一个流生产”的研究。主要目的就是使整个车间的生产形成一个流水线系统。 “一个流生产”就是把各个工序、生产线衔接起来,形成整个工厂一 体化生产。
实现“一个流生产”的主要要点如表1: 一个流生产 主要要点 实行单件流动 按加工顺序布置设备 生产同步化 员工的多能工化 站立式走动作业 设备合理布置和设计 制定生产节拍 表1“一个流生产”主要要点 完成“一个流生产”后,就需要进行缩短作业切换时间的研究了。缩 短每次作业切换时间是实现生产流程化的关键,也是实现生产均衡化的前 提。
缩短作业切换时间主要有四个步骤如图1 所示: 在完成缩短作业切换时间之后,就要进行混流生产的研究了。混流生产就是指将工艺流程、生产作业方法基本相同的若干个产品品种,在一条流 水线上科学的编排投产顺序,实行有节奏按比例地混合连续流水生产。
混流生产的主要方法有两种:一种是轮排法,一种是生产比导数法。运用这 两种方法实现混流生产后就基本上实现了均衡化生产。 实现均衡化生产后还需对泰德光学金属A 部车间进行现场改善。现场改 善主要的主要方法包括5S 管理、目视管理两种。通过这两种方法对“车间 内原材料、半成品、工具等摆放杂乱”“员工的整体素养低下,不能百分百 的投身到工作上”这两个问题进行解决,达到现场清洁员工素养提高的目
三、研究的方法与技术路线:
3.1 研究的主要方法如下:
运用“一个流生产”、缩短作业切换时间、混流生产三种方法实现均衡 化生产,然后运用5S、目视管理实现对现场的改善。
3.2 技术路线
四、研究的总体安排与进度:17日:毕毕业答辩。
五、主要参考文献:
[1]熊卫国,何为红.精益生产模式与全面质量管理[J].江西煤炭科技.(01).
[2]张冬匀.基于精益生产理论的生产现场改善方法的应用[J].机电工程.(10).
[3]王开忠.HL公司精益生产应用与研究[D].华南理工大学,. 基于精益生产的现场改善[J].机电工程, 2011, 28(12). 基于精益生产的SY公司现场改善研究[D].武汉理工大学 工业工程硕士论文, . Engel.Knowledge Management LeanProduction Systems ProcediaCIRP,Volume 2012,Pages 436C441.
[4]Kasra Ferdows,Building factory fitness[J]:Emerald Journal,2011.
[5] Aysun Bozanta. Multi User Virtual Environments SeriousGames TeamBuilding. [J].Procedia Computer Science,2012,15.
[6]王玖河,周荣辅.我国制造业推行精益生产方式的对策研究[J].经济管理学院,.
[7]魏鹏飞.精益生产实施关键因素及评价体系研究[J].管理与经济学部,.
[8]王树贵.经营管理过程中的精益生产方式[J].经营与管理.2011(10).
[11]肖正斌. 精益生产方式下海湾轮毂公司现场改善研究[D]. 燕山大学, 2012. 指导教师审核意见:
1.论文开题报告格式及如何写论文开题报告
2.本科论文开题报告
3.包装论文的开题报告
4.论文开题报告内容
5.论文 开题报告题目
6.论文的开题报告
7.mba论文开题报告
8.日语论文开题报告
9.软件论文开题报告
10.论文开题报告作用
篇4:精益生产心得体会
每个人对于同样一件事情的评价和想法都是不一样的,企业的精益生产也是同样的道理呢,不同的企业对于精益生产的理解也是不一样的,企业要根据企业的实际情况来发展自己的精益生产,这样的精益生产才能取得更好的发展,下面来总结一下我对精益生产的一些理解和体会,分享一下自己的精益生产心得体会,希望对大家的精益生产有帮助。
1. 在没有学习精益生产之前我认为精益生产是以5S工作方法为代表,以减少成本,提高效益满足客户需求的全面的质量管理体系,在生产、生活、管理等多个领域的文化理念。然而在学习之后呢,让我更全面,更深刻的了解精益生产的含义:精益是一个有系统的方法,经由不断的改善以找出及减少浪费,并在追求完美的前提下,在客户需求时才拉动生产线进行生产。最值得我们注意的是不断的改善,持续改善的观念去追求完美!企业的精益管理是个很不错的管理理念,值得运用。
2. 要学习精益生产首先要在思想观念上去改变自己,在价值观上要重塑对事物的看法,在工作中培养,什么是良好的工作习惯,比如看见车间走道上或是推车边有物料没有按要求摆放或乱放了,我们可以主动去纠正,从细微的角落去做,防止大的问题发生。我们每天要做的事情,如果不是要做紧急的事和紧急但不重要的事上,应该把更多的精力应放在重要不紧急的或不重要不紧急的事情上,这些重要的、不紧急的事情做好了就不存在紧急的事情让你工作繁忙,这就形成了工作的一个良性循环。
3. 另一方面就是要知道什么是“价值溪流”,其实就是把整个工艺流程看做是一条溪流的话,哪些是堵住溪流畅通的因素,找到问题所在,然后针对性的去分析,想办法去除最终使整个工艺流程更加合理,更加完善,使整个溪流畅通无阻,这就做到了精益生产的真正含义。要随时去找到可以改进的地方,力求做到完美。
4. 工作中要区分哪些是有价值的工作,哪些是非价值的工作,什么是浪费的工作?
篇5:精益生产心得体会
参加了公司组织的精益生产学习后,我对精益生产的理解更为清晰。作为制造型企业,要想在竞争日益激烈的市场环境中生存,就必须保持良好的竞争力。而竞争力来源于公司的品牌形象、盈利能力、员工素质和高效率的产品供应系统。精益生产正是行之有效提高竞争力的生产方式。所谓精益生产是指合理的安排生产,以最低的制造成本,生产出满足客户需求的产品,并且创造最大利润。 精益生产有以下特点:
一、“均衡化”与“多样化”
多样化也就是多品种及少批量,但多品种少批量如果控制不好会对我们的库存尾数造成压力,也就是说资金的积压。要解决这些问题需要做好均衡化的管理,在库存量及合格率上的有效控制是做好多样化的基础。
二、杜绝各种浪费以提高生产效率
操作的浪费在我们的工作中时刻存在,如可找出这些浪费及改善是关键,要找出我们身边的浪费只有全员参与才能做到更全面。要真正能达到杜绝各种浪费还要做大量的工作,需要大量的人力才能做到,所以我们做好宣传工作,动员全体员工积极参与才能杜绝各种浪费,达到提高生产效率的目的。
三、少人化、自动化
“少人化”是从“省人化”过度得来的,这需要提高员工的操作技能才可实现。而“自动化”除了设备自动化外,我觉得作为生产部门,人的“自动化”由其重要,人的“自动化”指我们每一个人都能自动去做事,自动去寻找问题并寻求解决措施,只有这样才能挖掘第一个人的潜力,使到在少人的情况下能完成预期的工作任务。所以我们在人员的思想教育方面要多下功夫,使员工的意识上提高做到发处内心的自愿去做,只有这样才能达到“自动化”。
四、柔性生产
“柔性生产”实际就是我们常说的“一岗多能”,如果我们每一个员工能够掌握多个岗位的操作技能,那么在生产上人员的调动方面较为灵活,是少人化、自动化及杜绝浪费提高生产效率的基础。要使每一个员工能掌握多个岗位的技能必须多给员工有培训及实践的机会,我们要多关心他们的学习及给予分配不同的工作,让他们在理论及实践中提高操作质能。
篇6:精益生产心得体会
精益生产方式是一种以最大限度地减少企业所占用的资源和降低企业管理和营运成本为主要目标的生产方式。精益生产方式的理论框架包含“一个目标”、“两大支柱”和“一大基础”。“一个目标”是低成本、高效率、高质量地进行生产,最大限度地使顾客满意。“两大支柱”是准时化与人员自主化。“一大基础”是指改善。改善是精益生产的基础,可以说没有改善就没有精益生产。
据麻省理工学院汽车研究小组沃麦克和琼斯统计,在初步实施精益生产方式的企业,通过用户的逆向拉动,把典型的“批量”生产系统转化为连续流动,可使整个系统的劳动生产率翻一番,同时减少完成生产时间的90%,减少整个系统库存量的90%;在用户手中发现错误、生产过程中的废品率下降一半;新产品面市的时间缩短一半;用户只需再增加极少的费用,就可以获得产品系列范围内更多的变型品种。当“精益”生产方式在企业实施两、三年后还能够通过持续的改进将“生产率再翻一番,同时库存量、失误率和供货时间再减少一半”。
现代社会化大生产的不断发展,给企业现场管理提出了更高更新的要求。按精益生产方式的要求,生产现场管理必须合理地组织现场的各种生产要素,做到人流、物流运转有序,信息流及时准确,使生产现场始终处于正常、有序、可控的状态。具体地讲,就是生产上精心组织,管理上精雕细刻,工艺上精益求精,成本上精打细算,操作上精耕细作,精神上精诚团结。
一、“八个零”是企业现场管理的终极目标
按照精益生产方式的要求,企业现场管理的目标是达到“八个零”,即合理定置物品,工作需用时寻找时间为零;合理布局生产现场,物流走向损耗为零;合理安排生产,产品浪费及库存积压为零;严格工艺纪律和工艺操作规程,操作失误和产品质量不合格现象为零;加强现场巡检和设备维护保养,装置“跑、冒、滴、漏”现象为零;准确及时填写各种现场原始记录,规范现场各类信息标识,装置系统程控仪表、电讯、计算机保持有效运转,信息显示、传递误差现象为零;严格安全生产规程和安全生产责任制,安全隐患、事故为零;不断提高现场人员的职业素养,形成良好的职业道德风气,现场人员不良行为为零。管理上的精雕细刻,实际上是确保现场各类问题的发生为零。比如对生产现场的定置管理,就是使各生产要素有机结合,实现生产过程科学化、规范化、标准化,从而达到降低生产成本,提高产品质量、经济效益和现场文明生产水平的目的。
篇7:精益生产心得体会
作为制造型企业, 现在在市场经济的大环境下企业要有竞争力就必须 在精益生产方面下大功夫。通过对精益生产理论学习,我对精益生产 的理解更为深入。 精益生产是从丰田生产方式中总结提炼的先进的管理理念它的核心思想是通过消除企业所有环节上的不增值活动,达到降低成本、缩短生产周期和改善质量的目的。实现精益生产的基础 是稳定的生产运作,及时供货(jit)和稳定的质量保证(自働化)是实 现精益生产两大推动力。
现将本次学习体会到的有关精益生产的内容总结如下:
一、“均衡化”与“多样化”
多样化也就是多品种及少批量, 但多品种少批量如果控制不好会对我 们的库存尾数造成压力,也就是说资金的积压。要解决这些问题需要 做好均衡化的管理, 在库存量及合格率上的有效控制是做好多样化的 基础。 二、杜绝各种浪费以提高生产效率
操作的浪费在我们的工作中时刻存在, 如可找出这些浪费及改善是关 键,要找出我们身边的浪费只有全员参与才能做到更全面。要真正能 达到杜绝各种浪费还要做大量的工作,需要大量的人力才能做到,所 以我们做好宣传工作,动员全体员工积极参与才能杜绝各种浪费,达 到提高生产效率的目的。
三、少人化、自动化
“少人化”是从“省人化”过度得来的,这需要提高员工的操作技能才可 实现。 而“自动化”除了设备自动化外, 我觉得作为生产部门, 人的“自 动化”由其重要,人的“自动化”指我们每一个人都能自动去做事,自 动去寻找问题并寻求解决措施,只有这样才能挖掘第一个人的潜力, 使到在少人的情况下能完成预期的工作任务。 所以我们在人员的思想 教育方面要多下功夫,使员工的意识上提高做到发处内心的自愿去 做,只有这样才能达到“自动化”。
四、柔性生产
“柔性生产”实际就是我们常说的“一岗多能”,如果我们每一个员工能 够掌握多个岗位的操作技能,那么在生产上人员的调动方面较为灵 活,是少人化、自动化及杜绝浪费提高生产效率的基础。要使每一个 员工能掌握多个岗位的技能必须多给员工有培训及实践的机会, 我们 要多关心他们的学习及给予分配不同的工作, 让他们在理论及实践中 提高操作技能。
企业精益生产渗透于企业各个环节,是一个需要全员参与、共同推动 的,要实行精益生产,要关注以下几个环节:
1、设立有关整顿浪费的制度,降低工人提出改进、创新的门槛。工 人只要提出合理、且对生产有益的改进就算一项成果,到年底的时候 评比出优秀的成果, 给予奖励和公布。 这样才能激发工人的创造热情, 将员工的智慧充分加以利用,也就是先将第八大浪费减到最小。
2、生产计划要尽可能的细致和科学。因为粗放的计划,肯定会造成 库存和搬运的浪费, 但是科学的计划还需要在下达计划的先期进行细 致的工作,将各项零部件的生产节拍掌握清楚,然后再制订出科学的 计划,避免不需要的零件堆满现场的弊端。
3、让现场管理真正地为生产服务。现场管理应是生产管理的基石, 而不应是障碍。丰田公司的“5s 管理”就是为整顿现场的浪费而服务 的,只有建立起现场管理为生产服务的理念,才能将现场管理真正地 做好。
4、工艺人员在编制工艺时,对加工余量的大小应科学、适当,避免 不必要的加工和多余的加工,并且在审图时,对图中加严要求的地方 应与设计及时沟通,不必要的加严应放松,以减少加工难度和加工时 间。
5、对产品质量问题的处理不能仅停留在事后管理的层面上。应制定 改善问题的制度,为持续改善创造条件,创造出勇于和乐于面对问题 的氛围,并提供对员工的方法培训,以加强对问题的追溯能力和解决 问题的能力,从而真正做到全员抓质量的目的。 总之,只要能够从一点一滴的小事改起,将精益的理念逐渐地渗透于 日常的生产中,精益总会带来意想不到的收获。我相信总有一天,当 我们面临生产计划跟不上变化的时候,不是改变计划,而是学会控制 变化。
篇8:精益生产口号
精益生产口号推荐
精益从心开始,改善由我做起;
IE is from the heart, improvement is from you.
下一道工序就是客户;
The next position is your customer.
团队的.效率才是真效率;
Team efficiency is the real efficiency.
标准作业,作业标准;
Standard operating, operate standardized.
我的设备我保养,我的品质我保证;
Keep equipments well maintained, let quality be better guaranteed.
坚持改善,天天向上;
Pursue improvement, make progress everyday.
不求一次完善;
Improvement is not for only once.
改善只有更好,没有最好;
There is no best but better for improvement.
今天你提案了吗!今天你改善了吗!
Have you submitted your proposal today? Have you made improvement today?
上联:整理整顿是基础;下联:清洁清扫是保持;横批:素养自然行。
SEIRI, SEITON are the foundation;
SEISO, SETKETSU are for keeping.
SHITSUKE comes naturally.
库存是万恶之源!
Inventory is the resource of all badness.
降低库存,减少浪费;
Reduce inventory, decrease waste.
一针一线,价值体现;
A single needle or piece of thread embodies value.
搬运寻找,尽量减少;
Movement and looking for things should be reduced to the minumum.
多余动作,劳而无获;
No gain for unnecessary movements.
动作优化,有功无过;
It is never wrong to optimize movements.
过量加工,费时费工;
Surplus process is a waste.
浪费资源,金钱去填;
Resources waste needs money to fill.
优化程序,省心省力;
Optimized procedure saves time and money.
一二三四,步调一致;
One, two, three, four, keep the step along the goal.
发现问题,及时报告;
Discover problem, report it in time.
隐藏错误,害人害己;
Hiding mistake is harmful.
篇9:什么是精益生产?
精益生产是一种起源于丰田和汽车制造的流水线制造方法论,也被称为“丰田生产系统”。精益生产的目标被描述为“在适当的时间(或第一时间,thefirsttime)使适当的东西到达适当的地点,同时使浪费最小化和适应变化”。创立了精益生产原则的大野耐一发现他的方法论不但可以减小浪费,还能够增进产品流动和提高质量。
丰田不是把资源放到关于未来制造需要的计划中,而是致力于减少系统反应时间,从而使生产系统能够迅速变化以适应市场的需要。实际上,他们的汽车是按订单生产的。精益生产的原则使这家公司可以按需求交货,使库存最小化,尽可能多使用掌握多门技能的员工,使管理结构扁平化,并把资源集中于需要它们的地方,
在80年代,这套实践被归纳成精益生产的10条准则,并且被美国和欧洲和众多制造企业所采纳。这一管理方法在服务性组织、物流机构和供应链的应用获得了不同程度的成功。在网络热潮之后,人们正在重新对精益生产的原则产生兴趣,特别是精益哲学对库存削减的强调。戴尔电脑和波音公司都从应用精益生产哲学当中获得了巨大的成功。
精益生产的10条准则可以归纳为:
1消除浪费
2使库存最小化
3加速流动
4由顾客需求拉动生产
5满足顾客需要
6把事情一次性做好
7授权给工人
8使设计适应快速的变化
9与供应商结成伙伴
10创造持续改进的文化
篇10: 《精益生产》学习心得
精细化作为现代工业化时代的一个管理概念,最早是由日本的企业在20世纪50年代提出的。“天下大事,必做于细。”精细化管理的理论已经被越来越多的企业管理者所接受,精细化管理就是一种先进的管理文化和管理方式。
管理,从古至今的哲学,也作为一种艺术,被世人研磨。市面上林林总总的管理论著、管理模式,大多一如翩翩的候鸟,从黎明飞至黄昏,从激荡归于静默。勤恳的企业家们(在中国这块被古老文明熏染过的国度里,好像从来就不缺乏勤恳),全面质量管理、ISO9000、流程再造、零库存管理、无边界管理、SCM(现代物流与供应链管理)、CRM(客户关系管理)、
ERP(企业资源管理)……每一种模式基本上都掀起过一阵热潮,热潮过后留下更多的是:无奈的沉寂与渐趋理性的思考。
精细化是一种意识、一种观念、一种认真的态度、一种精益求精的文化。
现代企业对精细化管理的定义是“五精四细”,即精华(文化、技术、智慧)、精髓(管理的精髓、掌握管理精髓的管理者)、精品(质量、品牌)、精通(专家型管理者和员工)、精密(各种管理、生产关系链接有序、精准),以及细分对象、细分职能和岗位、细化分解每一项具体工作、细化管理制度的各个落实环节。“精”可以理解为更好、更优,精益求精;“细”可以解释为更加具体,细针密缕,细大不捐。精细化管理最基本的特征就是重细节、重过程、重基储重具体、重落实、重质量、重效果,讲究专注地做好每一件事,在每一个细节上精益求精、力争最佳。
篇11: 精益生产学习心得
精益生产培训的目的:通过实施精益生产以提高产能稳定性和利用率,产品质量和及时准确的交货表现。
对于生产品质的管理,首先需做到以下几点:
1、工序自检;
2、上工序或供应商来料检验;
3、提升生产制造工艺,如通过设计DOE试验,获取最佳生产制作条件、参数;
QA网络的建设意义在于,品质不仅仅是品质部单一部门进行管理,而是通过工厂内各部门提升品质意识,全员参与,共同提升品质的过程。从事后把关变成事前预防,一旦生产过程处于控制状态,就要维持这种控制状态,才能保证品质。维持控制状态可以采用3种方法:操作者的更多的参与、统计过程控制、防错装置化。QA网络评价活动以制造部门为主,同时物流、品管、生产技术等部门连成一体共同实施。QA是对质量保证程度进行评价的工具之一。管理人员必须有强的质量意识并具备专业知识才能正确使用。管理者高度重视并有效指导是使用QA网络成功的关键。
QC工位表主要用于对重要的品质控制项目进行管理和控制。
品质改善的运作模式为PDCA,即计划、执行、检查、总结。PDCA是环环相扣,必须按步进行,不可逾越。同时每一次循环的结束,代表着品质的提升。其中总结为最重要的阶段,总结就是总结经验、肯定成绩、纠正错误及提出新的问题。
全面质量管理TQM,主要是将过去的事后检验,以把关为主,转变为事前预防改进为主,从管结果到管因素的转变过程。TQM的主要特点为:全面的质量管理、全过程的质量管理、全员参与的质量管理、质量管理的方法是科学的、多种多样的。
6σ品质管理,是生产品质的最终保证,在生产过程中降低产品及流程的缺陷次数,防止产品变异,提升品质。6σ是一个目标,这个质量水平意味的是所有的过程和结果中,99.99966%是无缺陷的,也就是说,做100万件事情,其中只有3、4件是有缺陷的,这几乎趋近到人类能够达到的最为完美的境界。
通过对精益生产中品质管理的学习,结合自身工作岗位实际情况,本人对工序的品质改善提出以下几点建议:
1、上工序来板时,收板人员必须先进行抽检,确保没有重大品质问题的状况下才能收板过数;
2、加强对各岗位员工的品质质量管理方面的培训,提升品质意识及判定缺陷的能力,如此可增加员工在检验或生产过程中的自检能力,将问题解决在萌芽阶段,做到事前预防;
3、对于本工序检验出来的问题,需及时反馈至责任工序,督促责任工序进行相应改善。对于重特大品质问题,需上报工厂管理层,同时迅速组建相应的改善小组,小组成员由各部门人员组成,形成完整的QA网络体系,最终达成改善品质的目的;
4、通过对PDCA模式的认知,是需将后续的品质改善按此方式进行,先有周密的改善计划,彻底的执行力,真实的检验结果,认真的总结改善过程中的得与失。
5、6σ为本工序改善品质的终极目标,目前工序仍存在许多问题,但是相信通过统计分析问题,最终一定能达成99.99966%的目标。
篇12: 精益生产学习心得
1973年爆发了第二次世界大战之后最严重的世界性经济危机――第一次石油危机。日本经济出现了零增长的局面,几乎所有的企业都被逼到了亏损的境地,惟有丰田汽车公司例外。这说明了丰田公司有一种抗拒风险的强有力的方法,这就是丰田生产方式――精益生产。精益生产是一种以最大限度地减少企业生产所占用的资源和降低企业管理和运营成本为主要目标的生产方式,又是一种理念、一种文化。实施精益生产方式JIT就是决心追求完美、追求卓越,就是精益求精、尽善尽美,为实现七个零的终极目标而不断努力。它是支撑个人与企业生命的一种精神力量,也是在永无止境的学习过程中获得自我满足的一种境界。
为全面深入开展精益生产管理工作,把精益生产管理工作扎实有效地落实到每一个岗位,让每一个员工都能建立精益生产的新理念,并将这一理念形成一种习惯融入到具体工作之中,为公司创造更大的经济效益,我厂积极的响应并参加了公司举办的为期两个月的精益生产管理培训学习。通过学习,使我厂人员深层次的了解了集团公司精益生产管理体系的基本概念、各项条款及体系中的各个模块的具体实施办法和要求,并且使我们掌握了精益生产管理的新理念,并将这一理念应用到工作当中,实现了低成本高效率。
同时为全面开展精益生产活动,将精益理念深入贯彻到工作当中,公司人员努力查找不精益问题,研究思考如何改善落实精益生产,我们从以下几个方面做出了一定的精益改革:
一、技术方面
1、重新对木制产品铸件重量进行核算、称重,减少损失。
2、编制合理的产品工艺卡,杜绝工序间的不良衔接,提高生产效率。
3、对原有的木制产品设备进行设计改造,提高产品的使用性能,满足客户要求,增加销售额,提高设备的市场占有率。
4、精确合理的预算材料,降低材料消耗。
二、质量方面
1、开展为期百日的“消除八害,制造精品”质量整顿活动,提高产品质量,降低废次品率,节约生产成本。
2、严格执行收件检验制度,避免产品的批量废次品。
3、加强对检验人员的业务、素质培训,提高检验员的业务能力,减少产品漏检、错检,降低不必要的生产浪费。
4、严把材料入厂检验关,未经复验合格的材料禁止使用,并且标识清晰,严防混料现象发生,避免不必要的材料。
三、采购方面
1、坚持每天对钢材等主要材料市场聚格进行了解,时时掌握主要材料市场聚格动态。
2、坚持对重要的原材料价格和性能等信息进行管理汇总。
3、采购前进行市场比价,同等质量产品选择价格最低厂家。
4、对于不常用的板料采用成型下料进行定货减少库存。
5、对于价格比较高的合金钢原料采用减小尺寸规格和倍尺定料。
6、对于一部分锻件改用圆钢代用。
四、物料管理
1、标准件发放改变以前的领用方式,设备标准件的领用,库房按照标准件领用单进行发放。
2、普通刀头改变以前的换取方式,由材料员根据当月完成工时定数量,按片旧换新的方式。
3、刀具管理,数控刀具磨损后,修复以后在粗加工中使用。
4、工量具管理报废由专业人员鉴定,由人为原因的进行经济处罚。
5、工具由修理人员开展工具的定期检查和修复工作。
6、晒图和复印采用副总经理审批的手续。
五、设备、设施管理方面
1、每天对现场设备进行检查,重点设备每周专人检查,发现问题及时处理。
六、能源管理方面
1、水、电方面加强宣传教育,落实考核制度,对水、电设施每天检查是否正常,发现问题及时处理,每月对总的水、电消耗进行对比,对不合理高出的消耗查找原因,解决处理。
2、油类发放由过去的随意发放,改成每天定量发放,查看每周平均消耗。
通过这些方面的整改,我厂初步实现了低成本高效率的生产目标。
同时,我厂近期更是开展了“双百工程”的活动,号召每一位员工从点滴做起,在一年之内,完成节约百万的目标。在领导的大力倡导下,公司员工积极响应,目前已经完成了一半以上的任务。喜人的成果,使我们坚定了精益生产的理念。
小试牛刀,成绩斐然。可见,精益生产确实是一种降低生产成本、提高企业利润和提高企业竞争力的行之有效的方法。因此,在日趋激烈的市场竞争体系下,我们就必须在精益生产方面下大功夫。而现在对于精益生产我们只是迈出万里长征的第一步,所以摆在我们面前的将会是一段难及慢长的历程,是一段持续改进的过程。但是我们相信,只要我们坚持不懈的做下去,企业的精益之路将不会遥远,我们的公司必将会有一个美好的发展,必将会为强企富民做出更加突出的贡献!
★ 顶益实习报告
★ 硕士论文标准格式
★ 工程硕士论文
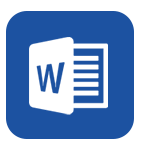
【精益生产开题报告(共12篇)】相关文章:
参考文献学位论文的格式怎么写2023-01-13
读书报告2023-11-04
工程验收意见评语2024-02-03
工学开题报告范文2023-04-02
医学类开题报告范文2023-09-13
毕业论文工作总结2023-09-12
家教意见评语2023-10-08
技术中心工作总结2024-05-08
UI材料大学毕业设计实习报告2022-07-21
诗歌研究类论文开题报告范文2023-02-10