飞机制造工装协同工艺设计(集锦8篇)由网友“其实我是小狗勾”投稿提供,下面是小编整理过的飞机制造工装协同工艺设计,欢迎大家阅读分享借鉴,欢迎大家分享。
篇1:飞机制造工装协同工艺设计
飞机制造工装协同工艺设计
从飞机制造工装工艺设计入手,结合计算机支持的协同工作方法,分析并论述了飞机工装协同工艺设计系统的框架模型,工作流管理机制.提出一种以工艺知识为支撑,基于网络的'工装协同工艺设计系统的实现方案.
作 者:刘野 王自军 郑国磊 LIU Ye WANG Zi-jun ZHENG Guo-lei 作者单位:北京航空航天大学机械工程及自动化学院,北京,100083 刊 名:航空精密制造技术 ISTIC英文刊名:AVIATION PRECISION MANUFACTURING TECHNOLOGY 年,卷(期): 43(6) 分类号:V262.4 TP391 关键词:协同工作 CAPP 工作流篇2:变速拨叉加工工艺及工装设计
摘 要
本论文设计的是变速拨叉的加工工序、设计方案、计算过程以及钻孔的夹具设计,变速拨叉加工工艺及工装设计
。拨叉表面加工方法的选择、加工顺序的安排、工序集中与分散的处理、加工阶段的划分、机床和工艺装备的选择、加工余量与工序尺寸及公差的确定等都是编制工艺规程的主要问题。而夹具设计所面临的是设计方案的确定、定位元件的选择、定位误差的分析与计算、夹紧力的计算、夹具体毛坯结构及夹具元件配合的确定。还有拨叉毛坯图、零件图和夹具装配图的绘制,如何保证用拨叉的技术条件是加工过程最为重要的问题,而夹具也起着至关重要的作用。拨叉的合理结构设计、加工工艺性设计,保证拨叉的加工质量,对提高生产效率有着重要意义,它是保证产品质量的关键所在。通过对拨叉加工过程的设计,可以发现一个产品的设计需要各个加工过程很好的配合才能成功。 关键词:拨叉;工艺; 夹具; 夹紧; 定位 AbstractIn this paper, the design of the fork processing speed, design, calculation and design of drilling jig. Fork the surface of the choice of processing methods, processing sequence of the arrangement, process centralization and decentralization of treatment, the division stage of processing, machine tools and process equipment selection, allowance and processes determine the size and tolerance of the preparation process are the main point of order problem. Fixture Design and facing the program is designed to identify, locate component selection, positioning errors of analysis and calculation, the calculation of clamping force, the specific folder structure and the rough with the determination of fixture elements. There are fork blank map, fixture assembly parts diagram and mapping how to ensure the technical conditions fork is the most important process, and fixture also plays a vital role.
Fork reasonable structural design, design process to ensure quality processing fork, to improve the productivity of great significance, it is to ensure that the key to product quality. Fork through the design process can be found in a product design process requires a good co-ordination to succeed.
Keywords: fork; technology; fixture; clamping; positioning目录第一章 拨叉零件的分析………………………11.1零件的作用 …………………....11.2零件的技术要求. …………………1.3工艺分析…………………………第二章 工艺规程的设计..............................2.1确定毛坯的制造形式……………….32.2基面的选择…………………....32.3表面加工方法的确定制定工艺路………..32.4工序顺序安排的确定…………....32.5确定工艺路线……....42.6机械加工余量 工序尺寸及毛坯尺寸的确定..52.7确立切削用量及基本工时…………..5第三章夹具设计……………………...…...93.1问题的提出……………………93.2夹具设计…………………….9
参考文献………………………….17
序言机械制造工业是为现代化建设提供各种机械装备的部门,在国民经济的发展中具有十分重要的地位。机械制造工业的发展规模和水平是反映国民经济实力和科学技术水平的重要标志,因此,我国一贯都把发展机械制造工业作为发展国民经济的战略重点之一。我国机械制造工业虽然取得了很大的进步,但与工业发达的国家相比,在生产能力、技术水平、管理水平和劳动生产率等方面,还有很大的差距。因此,我国的机械制造工业今后的发展,除了不断提高常规机械生产的工艺装备和工艺水平外,还必须研究开发优质高效精密工艺,为高新技术产品的生产提供新工艺、新装备,加强基础技术研究,强化和掌握引进技术,提高自主开发能力,形成常规制造技术与先进制造技术并进的机械制造工业结构。制造自动化及其发展是机械制造行业中的最新技术进步的又一个标志,但随着数控加工的应用的推广,CAD和CAM逐步进入实用阶段,特别是柔性制造系统(FMS)的出现,提高生产效率,降低成本,同时也保证了产品的质量和改善了劳动条件。目前,计算机集成制造系统(CIMS)正在研究和开发,也即将投入使用,它的出现将会更大程度的改变现代世界的机械行业。摘 要
本论文设计的是变速拨叉的加工工序、设计方案、计算过程以及钻孔的夹具设计。拨叉表面加工方法的选择、加工顺序的安排、工序集中与分散的处理、加工阶段的划分、机床和工艺装备的选择、加工余量与工序尺寸及公差的确定等都是编制工艺规程的主要问题。而夹具设计所面临的是设计方案的确定、定位元件的选择、定位误差的分析与计算、夹紧力的计算、夹具体毛坯结构及夹具元件配合的确定。还有拨叉毛坯图、零件图和夹具装配图的绘制,如何保证用拨叉的技术条件是加工过程最为重要的问题,而夹具也起着至关重要的作用。拨叉的合理结构设计、加工工艺性设计,保证拨叉的加工质量,对提高生产效率有着重要意义,它是保证产品质量的关键所在。通过对拨叉加工过程的设计,可以发现一个产品的设计需要各个加工过程很好的配合才能成功。 关键词:拨叉;工艺; 夹具; 夹紧; 定位 AbstractIn this paper, the design of the fork processing speed, design, calculation and design of drilling jig. Fork the surface of the choice of processing methods, processing sequence of the arrangement, process centralization and decentralization of treatment, the division stage of processing, machine tools and process equipment selection, allowance and processes determine the size and tolerance of the preparation process are the main point of order problem. Fixture Design and facing the program is designed to identify, locate component selection, positioning errors of analysis and calculation, the calculation of clamping force, the specific folder structure and the rough with the determination of fixture elements. There are fork blank map, fixture assembly parts diagram and mapping how to ensure the technical conditions fork is the most important process, and fixture also plays a vital role.
Fork reasonable structural design, design process to ensure quality processing fork, to improve the productivity of great significance, it is to ensure that the key to product quality. Fork through the design process can be found in a product design process requires a good co-ordination to succeed.
Keywords: fork; technology; fixture; clamping; positioning目录第一章 拨叉零件的分析………………………11.1零件的作用 …………………....11.2零件的技术要求. …………………1.3工艺分析…………………………第二章 工艺规程的设计..............................2.1确定毛坯的制造形式……………….32.2基面的选择…………………....32.3表面加工方法的确定制定工艺路………..32.4工序顺序安排的确定…………....32.5确定工艺路线……....42.6机械加工余量 工序尺寸及毛坯尺寸的确定..52.7确立切削用量及基本工时…………..5第三章夹具设计……………………...…...93.1问题的提出……………………93.2夹具设计…………………….9
参考文献………………………….17
序言机械制造工业是为现代化建设提供各种机械装备的部门,在国民经济的发展中具有十分重要的地位。机械制造工业的发展规模和水平是反映国民经济实力和科学技术水平的重要标志,因此,我国一贯都把发展机械制造工业作为发展国民经济的战略重点之一。我国机械制造工业虽然取得了很大的进步,但与工业发达的国家相比,在生产能力、技术水平、管理水平和劳动生产率等方面,还有很大的差距。因此,我国的机械制造工业今后的发展,除了不断提高常规机械生产的工艺装备和工艺水平外,还必须研究开发优质高效精密工艺,为高新技术产品的生产提供新工艺、新装备,加强基础技术研究,强化和掌握引进技术,提高自主开发能力,形成常规制造技术与先进制造技术并进的机械制造工业结构。制造自动化及其发展是机械制造行业中的最新技术进步的又一个标志,但随着数控加工的应用的推广,CAD和CAM逐步进入实用阶段,特别是柔性制造系统(FMS)的出现,提高生产效率,降低成本,同时也保证了产品的质量和改善了劳动条件。目前,计算机集成制造系统(CIMS)正在研究和开发,也即将投入使用,它的出现将会更大程度的改变现代世界的机械行业。我研究的课题是拨叉。拨叉应用在变速箱的换档机构中,拨叉头孔套早变速叉轴上。拨叉脚则夹在双联变换齿轮的槽中。当需要变速时,操纵变速杆,变换操纵机构就通过拨叉头部的操纵槽带动拨叉与变速叉轴一起在变速箱中滑移,拨插脚拨动双联变换齿轮在花键上滑动一改变档位,从而改变速度。该拨叉在改换档位是要承受弯曲应力和冲击载荷的作用,因此该零件具有足够的强度和刚度以及韧性,以适应拨叉的工作条件。该拨叉形状特殊,结构简单。为实现换档变速的功能,其叉轴空与变速叉轴有配合要求,因此加工精度要求较高。叉脚两端面在工作中需要承受冲击载荷,为增强起耐磨性,该表面要求高频淬火处理,硬度为48—58HRC。拨叉头两端面和叉脚两端面均要求切削加工。并在轴方向上均高于相邻表面,这样既减少了加工表面又提高了换档是叉脚端面的接触刚度。该零件除了主加工表面外,其余的表面加工精度均较低,不需要高精度的机床加工,通过铣削、钻床的粗加工就可以达到加工要求毕业设计是本专业培养我们的最后一个综合性的实践教学环节,通过完成一定的生成设计或科研试制任务,获得运用基本理论的工程技术训练达到综合素质和能力的提高。其目的的培养我们独立分析和处理专业问题的能力。 第一章 拨叉零件的分析1.1零件的作用拨叉应用在变速箱的换档机构中,拨叉头孔套早变速叉轴上。拨叉脚则夹在双联变换齿轮的槽中。当需要变速时,操纵变速杆,变换操纵机构就通过拨叉头部的操纵槽带动拨叉与变速叉轴一起在变速箱中滑移,拨插脚拨动双联变换齿轮在花键上滑动一改变档位,从而改变速度。该拨叉在改换档位是要承受弯曲应力和冲击载荷的作用,因此该零件具有足够的强度和刚度以及韧性,以适应拨叉的工作条件。该拨叉形状特殊,结构简单。为实现换档变速的功能,其叉轴空与变速叉轴有配合要求,因此加工精度要求较高。叉脚两端面在工作中需要承受冲击载荷,为增强起耐磨性,该表面要求高频淬火处理,硬度为48—58HRC。拨叉头两端面和叉脚两端面均要求切削加工。并在轴方向上均高于相邻表面,这样既减少了加工表面又提高了换档是叉脚端面的接触刚度。该零件除了主加工表面外,其余的表面加工精度均较低,不需要高精度的机床加工,通过铣削、钻床的粗加工就可以达到加工要求1.2零件的技术要求零件的技术要求表加工表面尺寸及偏差mm表面粗糙度Ra 公差精及度等级形位公差/mm 拨叉头左端面83.53.2IT12 拨叉头右端面83.53.2IT12 拨叉脚内表面R4012.5IT13 拨叉脚两端面2.5IT9 φ12孔φ5IT7┻0.1A Φ8孔φ20IT7 操纵槽内侧面13.55IT12 操纵槽底面111013
该拨叉形状特殊,结构简单,属典型的叉杆类零件。为实现换档变速的功能,其叉轴孔与变速叉轴有配合要求,因此加工精度要求较高。叉脚两端面杂工作中需承受冲击载荷,为增加强起耐磨性,该表面要求高频淬火处理,硬度为48~58HRC。 1.3拨叉的工艺分析 分析零件图可知,拨叉头两端面和叉脚两端面均要求切削加工,并在轴向方向上均高于相邻表面,这样既减少了加工面积,又提高了换档时叉脚端面的接触刚度。φmm孔的的端面为平面,可以防止钻头偏钻,可以保证加工精度;另外,该零件除了主要工作表面外,其余的表面加工精度均较低,不需要高精度机床加工,通过铣床钻床的粗加工就可以达到加工要求;而主要的饿表面虽然加工精度要求较高,但也可以在正常的生产条件下,采用较经济的方法保证质量的加工出来.由此可见,该零件的工艺性能较好.第二章 工艺规程的设计2.1 确定毛坯的制造形式 零件材料为ZG45。考虑零件在机床运行过程中要承受的载荷较大,为增强拨叉的强度和冲击韧度,零件结构又比较简单,故选择铸件毛坯。该零件的轮廓尺寸不大,且生产类型为大批量的生产,为提高生产率和锻件的精度,宜采用模锻方法制造毛坯。2.2 基面的选择基面选择是工艺规程设计中的重要工作之一。定位基准有粗基准和精基准之分。通常先确定精基准然后确定粗基准。基面选择得正确与合理可以使加工质量得到保证,生产率得以提高。否则,加工工艺过程中回问题百出,更有甚者,还会造成零件的大批报废,是生产无法正常进行。(1)精基准的选择。根据零件的技术要求和装配要求选择拨叉的端面和叉轴孔φ12mm作为精基准。零件上的很多表面都是可以采用它们作为精基准进行加工,即遵循“基准统一”的原则。叉轴孔φ12mm的轴线是设计基准。选择基准定位加工拨叉脚两端面和锁销孔φ8mm。实现设计基准和工艺基准的重合,保证被加工表面的垂直度要求。选择拨叉头左端面作为精基准同样遵循了基准重合的原则。因为该拨叉在轴向方向上的尺寸多以该端面作为设计基准。另外由于拨叉件的刚性较差受力容易产生弯曲变形,为了避免在机械加工中产生夹紧变形。根据夹紧力应垂直于主要定位基面,并应作用在刚度较大部位的原则。夹紧力作用点不能作用在叉杆上。选择拨叉头左端面作进进精基准。夹紧可作用在拨叉头的右端面上夹紧稳定可靠。(2)精基准的选择。 作为粗基准的表面平整,没有飞边毛刺或其他表面缺欠。拨叉轴孔φ12mm的外圆和右端面作为粗基准。采用φ12mm外圆面定位加工内孔可保证孔的内壁厚度均匀。采用拨叉右端面做粗基准加工左端面可以为后续工序准备精基准。2.3 表面加工方法的确定 根据拨叉零件图上各个加工表面的尺寸精度和表面粗糙度,确定加工件表面的加工方法如下表加工表面尺寸精度等级表面粗糙度Ra 加工方案备注 拨叉头左端面IT123.2粗铣 拨叉头右端面IT123.2粗铣 拨叉脚内表面IT1312.5粗铣—磨 拨叉脚两端面IT92.5粗铣—粗磨—精磨 φ12孔IT75钻—铰—拉 Φ8孔IT720钻 操纵槽内侧面IT125粗铣 操纵槽底面1310粗铣
2.4 工序顺序的安排 1 机械加工工序(1)遵循“先基准后其他”的原则,首先加工精基准——拨叉头左端面和φ12mm(2)遵循“先粗后精”的原则,先安排粗加工工序,后安排精加工工序,(3)遵循“先主后次”的原则,先加工主要表面——拨叉头左端面和叉轴孔φ12mm和拨叉脚的两端面,后加工次要表面——操纵槽底面和内侧面(4)遵循“先面后孔”的原则,先加工拨叉头的端面,在加工叉轴孔φ12mm孔;先铣操纵槽,在钻φ8mm孔2热处理工序 锻成型后切边,进性调质,调质的硬度为241—285HBS,叉脚精加工之前进行局部高频淬火,提高其耐磨性和在工作中承受的冲击载荷的能力。3辅助工序 粗加工拨叉两端面和热处理后,安排校正工序;在半精加工后,安排去毛刺和中间检验工序;精加工后,安排去毛刺清洗和钟检工序 2.5 确定工艺路线 工序一 铸钢工序二 清砂工序三 热处理 正火工序四 校正 整形工序五 检验毛坯工序六 铣拨叉两端面工序七 1钻φ12mm孔 铰孔 工序八 第一拉孔 第二次拉孔工序九 检验工序十 1锪端面 2孔口倒角工序十一 1 锪另端面取总长 2孔口倒角工序十二 校正叉脚高低工序十三 校正叉脚开挡工序十四 1铣叉口面 2 铣5.5mm平面 3铣平面至尺寸4 铣槽工序十五 倒角去毛刺工序十六 钻锁销孔,去内孔毛刺 1钻φ8mm孔 2 去内孔毛刺工序十七 1钻通气孔φ3mm 2 去内孔毛刺工序十八 叉槽两侧面处高频淬火工序十九 校正叉脚高低工序二十 1磨叉脚上端面至锁销孔中心尺寸为2磨叉脚下端面至上端面尺寸为工序二十一 镀铬工序二十二 校正叉脚高低工序二十三 磨叉交两端面 1磨上端面至尺寸2 磨下端面至尺寸工序二十四 磨叉脚开挡面工序二十五 按检验卡要求检验工序二十六 清洗,涂防锈油,入库 2.6 加工余量,工序尺寸的确定2.6.1叉头两端面:粗铣——锪平面 查《课程设计》表2-35,粗铣端面的余量为3mm,锪端面的余量为0.5mm;查《课程设计》表1-20可知,粗铣的精度为IT12,锪端面为IT11;由此可知单边余量为2..5mm;工序尺寸偏差按“入体原则”标注为:粗铣——86.5,锪端面——84.5。2.6.2叉脚两端面:铣——粗磨——精磨查《课程设计》表2-35可知,粗铣余量为3mm,查《课程设计》表2-36可知,粗磨余量为0.3mm,精磨余量为0.2mm;查《课程设计》表1-20可知,粗铣的精度为IT12,粗磨为IT10,精磨为IT9;由此可知端面单边余量为3.5mm;查《课程设计》表2-40可得各公差为:T铣=0.09mm,T粗磨=0.058mm,T精磨=0.036mm;工序尺寸偏差按“入体原则”标注为:铣——14,粗磨——8,精磨——7.4。2.6.3叉脚内表面:铣——磨查《课程设计》表2-35可知,铣削余量为3mm,查《课程设计》表2-36可知磨削余量为0.3mm;查《课程设计》表1-20可知,粗铣的精度为IT12,粗磨为IT10;由此可知单边余量为3.3mm;查《课程设计》表2-40可得,T铣=0.3mm,T磨=0.12mm;工序尺寸偏差按“入体原则”标注:铣削——69.8;磨削——75.8。2.6.4叉口两侧面:铣查《课程设计》表2-35可知,铣削余量为3mm;查《课程设计》表1-20可知,铣的精度为IT12;由此可知,单边余量为3mm;查《课程设计》表2-40得,T铣=0.18mm;工序尺寸偏差按“入体原则”标注:铣——7.5,39.65;2.6.5铣5.5mm平面查《课程设计》表2-35可得铣削余量为1mm;查《课程设计》表1-20可得,铣的精度为IT12;由此可知单边余量为1mm;查《课程设计》表2-40得T=0.12mm;工序尺寸偏差按“入体原则”标注:铣——7.5 2.7 切削用量的计算 工序六 粗铣拨叉头两端面该工序分两工步,分别粗铣拨叉头两个端面。由于这两个 工步在同一台机床上经过一次走刀加工完成,因此它们所选用的切削速度v和进给量f是一样的。(1)背吃刀量的确定=2mm=2mm。 (2) 进给量的确定 《课程设计》表5-7,按机床的功率5-10KW,工件—夹具系统刚度为中等条件选取,该工序的每齿进给量取为0.08mm/z。(3)铣削速度的计算 查《课程设计》表5-9,按镶齿铣刀d/Z=80/10,的条件选取,铣削速度v可取44.9m/min。由公式n=1000v/d可得该工序铣刀转速,n=1000*44.9m/min/*80mm=178.65r/min,参照《课程设计》表4-15所列X-51型立式铣床的主轴转速,取n=160,在将该转速代入该公式可求出该工序的实际铣削速度v=40.2m/min。 工序七 钻φ12mm孔 铰孔(1) 钻φ12mm孔工步1)背吃刀量的确定=11.5mm。2)进给量的确定 参照《课程设计》表5-22,选取该工步的每转进给量f=0.1mm/r。3)切削速度的计算 参照《课程设计》表5-22,按工件材料为ZG45的条件选取,切削速度v可取为22m/min。由公式n=1000v/d可求得钻头的钻速n=897.6r/min, 参《课程设计》表4-9所列Z525型立式钻床的主轴转速,取转速n=960r/min。在将此转速代入公式n=1000v/d中可求的实际的切削速度v=23.5m/min。 (2) 粗铰孔1)背吃刀量的确定=0.1mm。2)进给量的确定 参照《课程设计》表5-31,选取该工步的每转进给量f=0.4mm/r。3)切削速度的计算 参照《课程设计》表5-31,切削速度v可取为22m/min。由公式n=1000v/d可求得钻头的钻速n=80r/min, 参照《课程设计》表4-9所列Z525型立式钻床的主轴转速,取转速n=97r/min。在将此转速代入公式n=1000v/d中可求的实际的切削速度v=2.4m/min。
工序八 拉孔(1)第一次拉孔工步1) 背吃刀量的确定=0.2mm。2)进给量的确定 参照《课程设计》表5-33选取该工步的每转进给量f=0.01mm/r(单齿面升量)。3)切削速度的确定 参照《课程设计》表5-34,选取该工步的拉刀的速度为5m/min。(2)第二次拉孔工步1)背吃刀量的确定=0.2mm。2)进给量的确定 参照《课程设计》表5-33选取该工步的每转进给量f=0.01mm/r(单齿面升量)。3)切削速度的确定 参照《课程设计》表5-34,选取该工步的拉刀的速度为5m/min。工序十 锪端面1) 背吃刀量的确定=0.5mm。2) 进给量的确定 参照《课程设计》表5-31,选取该工步的每转进给量f=0.10mm/r。3) 切削速度的确定参照《课程设计》表5-32,切削速度v可取为10m/min。由公式n=1000v/d可求得铰刀转速n=159.2r/min, 参照《课程设计》表4-9所列Z525型立式钻床的主轴转速,取转速n=195r/min。在将此转速代如公式n=1000v/d中可求的实际的切削速度v=12.4/min。 工序十一 锪另一端面取总长1) 背吃刀量的确定=0.5mm。2) 进给量的确定 参照《课程设计》表5-31,选取该工步的每转进给量f=0.10mm/r。3)切削速度的确定参照《课程设计》表5-32,切削速度v可取为10m/min。由公式n=1000v/d可求得铰刀转速n=159.2r/min, 参照《课程设计》表4-9所列Z525型立式钻床的主轴转速,取转速n=195r/min。在将此转速代如公式n=1000v/d中可求的实际的切削速度v=12.4/min。 工序十四 铣各部平面,槽及叉口(1)铣叉口面工步1)背吃刀量的确定=3mm。2) 进给量的确定 《课程设计》表5-7,按机床的功率5-10KW,工件—夹具系统刚度为中等条件选取,该工序的每齿进给量取为0.08mm/z。3)铣削速度的计算 查《课程设计》表5-9,按镶齿铣刀d/Z=80/10的条件选取,铣削速度v可取44.9m/min。由公式n=1000v/d可得该工序铣刀转速,n=1000*44.9m/min/*80mm=178.65r/min,参照《课程设计》表4-15所列X-51型立式铣床的主轴转速,取n=160,在将该转速代入该公式可求出该工序的实际铣削速度v=40.2m/min。(2)铣5.5mm平面工步1)背吃刀量的确定=1.5mm。2) 进给量的确定 《课程设计》表5-7,按机床的功率5-10KW,工件—夹具系统刚度为中等条件选取,该工序的每齿进给量取为0.08mm/z。3)铣削速度的计算 查《课程设计》表5-9,按镶齿铣刀d/Z=80/10的条件选取,铣削速度v可取44.9m/min。由公式n=1000v/d可得该工序铣刀转速,n=1000*44.9m/min/*80mm=178.65r/min,参照《课程设计》表4-15所列X-51型立式铣床的主轴转速,取n=160,在将该转速代入该公式可求出该工序的实际铣削速度v=40.2m/min。(3)铣平面至尺寸工步1)背吃刀量的确定=1.5mm。2) 进给量的确定 《课程设计》表5-7,按机床的功率5-10KW,工件—夹具系统刚度为中等条件选取,该工序的每齿进给量取为0.08mm/z。3)铣削速度的计算 查《课程设计》表5-9,按镶齿铣刀d/Z=80/10的条件选取,铣削速度v可取44.9m/min。由公式n=1000v/d可得该工序铣刀转速,n=1000*44.9m/min/*80mm=178.65r/min,参照《课程设计》表4-15所列X-51型立式铣床的主轴转速,取n=160,在将该转速代入该公式可求出该工序的实际铣削速度v=40.2m/min。 (4) 铣槽工步1)背吃刀量的确定=1.0mm。2) 进给量的确定 《课程设计》表5-7,按机床的功率5-10KW,工件—夹具系统刚度为中等条件选取,该工序的每齿进给量取为0.08mm/z。3)铣削速度的计算 查《课程设计》表5-9,按镶齿铣刀d/Z=80/10的条件选取,铣削速度v可取44.9m/min。由公式n=1000v/d可得该工序铣刀转速,n=1000*44.9m/min/*80mm=178.65r/min,参照《课程设计》表4-15所列X-51型立式铣床的主轴转速,取n=160,在将该转速代入该公式可求出该工序的实际铣削速度v=40.2m/min。 工序十六 钻φ8mm孔1)背吃刀量的确定=8mm。2)进给量的确定 参照《课程设计》表5-22,选取该工步的每转进给量f=0.1mm/r。3)切削速度的计算 参照《课程设计》表5-22,按工件材料为ZG45的条件选取,切削速度v可取为22m/min。由公式n=1000v/d可求得钻头的钻速n=897.6r/min, 参照《课程设计》表4-9所列Z525型立式钻床的主轴转速,取转速n=960r/min。在将此转速代入公式n=1000v/d中可求的实际的切削速度v=23.5m/min。工序十七 钻通气孔φ3mm1)背吃刀量的确定=3mm。2)进给量的确定 参照《课程设计》表5-22,选取该工步的每转进给量f=0.1mm/r。3)切削速度的计算 参照《课程设计》表5-22,切削速度v可取为20m/min。由公式n=1000v/d可求得钻头的钻速n=2123.4r/min, 参照《课程设计》表4-9所列Z4006型台式钻床的主轴转速,取转速n=2900r/min。在将此转速代入公式n=1000v/d中可求的实际的切削速度v=27.3m/min。 工序二十 粗磨脚叉两端面 (1)粗磨叉脚上端面至锁销孔中心尺寸为工步 1)背吃刀量的确定=0.4mm。 2)进给量的确定 参照《课程设计》表5-35,选取该工步的进给量f=0.0068mm/r。 3)切削速度的确定 参照《课程设计》表5-35,选取工件的运动速度为v=25m/min。由公式n=1000v/d可求的该工序的砂轮转速为99.5r/min。再将此转速代入公式中,可以求的该工序的实际磨削速度为v=25m/min 。(2)粗磨叉脚下端面至上端面尺寸为1)背吃刀量的确定=0.3mm。 2)进给量的确定 参照《课程设计》表5-35,选取该工步的进给量f=0.0068mm/r。 3)切削速度的确定 参照《课程设计》表5-35,选取工件的运动速度为v=25m/min由公式n=1000v/d可求的该工序的砂轮转速为99.5r/min。再将此转速代入公式中,可以求的该工序的实际磨削速度为v=25m/min 。工序二十三 磨叉交两端面(1)精磨上端面至尺寸工步1)背吃刀量的确定=0.2mm。 2)进给量的确定 参照《课程设计》表5-36,选取该工步的进给量f=0.0040mm/r。 3)切削速度的确定 参照《课程设计》表5-36,选取工件的运动速度为v=30m/min由公式n=1000v/d可求的该工序的砂轮转速为119.4r/min。再将此转速代入公式中,可以求的该工序的实际磨削速度为v=29.9m/min 。(2) 精磨下端面至尺寸工步1)背吃刀量的确定=0.2mm。 2)进给量的确定 参照《课程设计》表5-36,选取该工步的进给量f=0.0040mm/r。 3)切削速度的确定 参照《课程设计》表5-36,选取工件的运动速度为v=30m/min由公式n=1000v/d可求的该工序的砂轮转速为119.4r/min。再将此转速代入公式中,可以求的该工序的实际磨削速度为v=29.9m/min 。 工序二十三 磨叉脚的开挡面1)背吃刀量的确定=0.3mm。 2)进给量的确定 参照《课程设计》表5-36,选取该工步的进给量f=0.0016mm/r。3)切削速度的确定 参照《课程设计》表5-36,选取工件的运动速度为v=15m/min公式n=1000v/d可求的该工序的砂轮转速为238.8r/min。再将此转速代入公式中,可以求的该工序的实际磨削速度为v=14.9m/min。 第三章 夹具的设计 决定设计第十七道工序——钻M3孔的钻床卡具。本卡具将用于Z4006立式钻床。刀具为φ3的高速钢麻花钻。 3.1问题的提出在给定的零件中,对本步加工的定位并未提出具体的要求,是自由公差,定位要求较低。因此,本步的重点应在卡紧的方便与快速性上。 3.2 夹具的设计 3.2.1基准的选择出于定位简单和快速的考虑,选择φ12孔为基准,即以一面上一长销(自由度限制数:5)配合以一挡销(自由度限制数:1)使工件完全定位。再使用快速螺旋卡紧机构进行卡紧。 3.2.2切削力和卡紧力计算本步加工可按钻削估算卡紧力。实际效果可以保证可靠的卡紧。轴向力扭矩由于扭矩很小,计算时可忽略。卡紧力为取系数 S1=1.5 S2=S3=S4=1.1则实际卡紧力为 F’=S1*S2*S3*S4*F=10.06N使用快速螺旋定位机构快速人工卡紧,调节卡紧力调节装置,即可指定可靠的卡紧力。 3.2.3误差的分析本工序采用一定位销,一挡销定位,工件始终靠近定位销的一面,而挡销的偏角会使工件自重带来一定的平行于卡具体底版的水平力,因此,工件不在在定位销正上方,进而使加工位置有一定转角误差。但是,由于加工是自由公差,故应当能满足定位要求。 3.2.4卡具操作的简要说明卡具的卡紧力不大,故使用手动卡紧。为了提高生产力,使用快速螺旋卡紧机构。钻模套上设置有钻套,用于确定的钻头位置。 参考文献(1) 机械加工工艺手册。 李洪主编。北京:北京出版社。1990(2) 机械加工工艺手册第一卷。孟少农主编。北京:机械工业出版色 1991(3) 机械夹具设计手册(第二册)。东北重型机械学院,洛阳工学院,第一汽车制造厂职工大学编。上海:上海科学技术出版,1990(4) 金属机械加工工艺人员手册。赵如福主编。上海:上海科学技术出版社,1990(5) 简明机械加工工艺手册。徐圣群主编。上海:上海科学技术出版,1991(6) 机床夹具图册。大连理工大学。王小华主编。北京:机械工业出版社1990(7) 机床夹具图册。上海机械专科学校。孟宪栋。哈尔滨机电专科学校 刘彤安主编。北京:机械工业出版社 1992(8) 机械制造工艺学。 江南大学 郑修本,上海机械专科学校 冯冠大主编。北京:机械工业出版社,1992(9) 机床夹具设计。湘潭机电科学校 刘友才,江南大学 肖继德 主编。北京:机械工业出版社,1992(10) 机械零件设计手册 互换性与技术测量教材和金属切削原理与刀具教材篇3:数控车床的工艺与工装
数控车床加工的工艺与普通车床的加工工艺类似,但由于数控车床是一次装夹,连续自动加工完成所有车削工序,因而应注意以下几个方面:
一、合理选择切削用量
对于高效率的金属切削加工来说,被加工材料、切削工具、切削条件是三大要素,这些决定着加工时间、刀具寿命和加工质量。经济有效的加工方式必然是合理的选择了切削条件。
切削条件的三要素:切削速度、进给量和切深直接引起刀具的损伤。伴随着切削速度的提高,刀尖温度会上升,会产生机械的、化学的、热的磨损。切削速度提高20%,刀具寿命会减少1/2。
进给条件与刀具后面磨损关系在极小的范围内产生。但进给量大,切削温度上升,后面磨损大。它比切削速度对刀具的影响小。切深对刀具的影响虽然没有切削速度和进给量大,但在微小切深切削时,被切削材料产生硬化层,同样会影响刀具的寿命。
用户要根据被加工的材料、硬度、切削状态、材料种类、进给量、切深等选择使用的切削速度。
最适合的加工条件的选定是在这些因素的基础上选定的。有规则的、稳定的磨损达到寿命才是理想的条件。
然而,在实际作业中,刀具寿命的选择与刀具磨损、被加工尺寸变化、表面质量、切削噪声、加工热量等有关。在确定加工条件时,需要根据实际情况进行研究。对于不锈钢和耐热合金等难加工材料来说,可以采用冷却剂或选用刚性好的刀刃,
二、合理选择刀具
1、粗车时,要选强度高、耐用度好的刀具,以便满足粗车时大背吃刀量、大进给量的要求。
2、精车时,要选精度高、耐用度好的刀具,以保证加工精度的要求。
3、为减少换刀时间和方便对刀,应尽量采用机夹刀和机夹刀片。
三、合理选择夹具
1、尽量选用通用夹具装夹工件,避免采用专用夹具;
2、零件定位基准重合,以减少定位误差。
四、确定加工路线
加工路线是指数控机床加工过程中,刀具相对零件的运动轨迹和方向。
1、应能保证加工精度和表面粗糙要求;
2、应尽量缩短加工路线,减少刀具空行程时间。
五、加工路线与加工余量的联系
目前,在数控车床还未达到普及使用的条件下,一般应把毛坯上过多的余量,特别是含有锻、铸硬皮层的余量安排在普通车床上加工。如必须用数控车床加工时,则需注意程序的灵活安排。
六、夹具安装要点
目前液压卡盘和液压夹紧油缸的连接是靠拉杆实现的,如图1。液压卡盘夹紧要点如下:首先用搬手卸下液压油缸上的螺帽,卸下拉管,并从主轴后端抽出,再用搬手卸下卡盘固定螺钉,即可卸下卡盘。
刀具上的修光刃指的是在刀具刀刃后面副偏角方向磨出的一小段与刀尖平行的刀刃,主要用于刀刃切削后进行一次二次切削,相当于精加工过程,去处毛刺等伤痕,目的是提高工件的表面粗糙度。多应用于进行精加工的刀具上。
篇4:工艺文件编制及工装设计工作中的评语
工艺文件编制及工装设计工作中的评语 -评语
该同志悟性较好,在工艺文件编制及工装设计这两方面理解能力与接受能力均较强,因此对安排的工作做得较满意.本人认为,该同志发展潜力较大,只要坚持不懈的努力,今后一定会为公司的`发展做出较大的贡献.寥寥数语,勾勒出我在工作方面的特点.
六月份公司要新进员工找一位师傅,跟着学习,跟着工作.本人师父是一位60多岁退休的老高工,如爷爷般慈祥,我们亲切的称其为许嗲嗲,无私的教授我们实际知识和经验.
一年一度的年终自我总结,交给师父写评语,以上就是本人师父的年终评语,记下来,勉励自己在以后的工作和学习中发挥优点,改正缺点.更上一层楼.不负许嗲嗲的厚望.
篇5:空气压缩机曲轴零件的机械加工工艺及工装设计
内容摘要
此次毕业设计任务是对3L-10/8空气压缩机曲轴零件的机械加工工艺、夹具的设计,在曲轴零件的加工工艺过程中轴与轴中心线之间要有位置要求, 以毛坯轴两端定位先加工两中心孔,以两端中心孔定位再粗、精加工各轴的表面,然后以粗、精后的两轴径定位钻螺纹、铣键槽和铣曲拐端面,采用专用夹具加工两斜油孔,最后粗、精磨各轴。
在夹具的设计过程中,主要以V形块和支承板来定位,靠直压板和弹簧来夹紧,钻拐径两孔应采用长型快换钻套,在钻拐径倾斜30的孔时采用平面倾斜的夹具体,在钻拐径倾斜40的孔时使用的是卧式钻床,铣面时2个V形块与铣刀不能干涉,因此V形块高度要降低,夹具设计要方便、简单。
关键词:曲轴;加工工艺;夹具设计
目 录
内容摘要 ........................................................................................................................ I 1 绪 论 ................................................................................... 错误!未定义书签。 2 零件分析 ............................................................................... 错误!未定义书签。
2.1 零件的作用 ................................................................. 错误!未定义书签。
2.2 零件的工艺分析 ......................................................... 错误!未定义书签。
2.2.1 以拐径为?95mm为中心的加工表面 ............ 错误!未定义书签。
2.2.2 以轴心线两端轴为中心的加工表面 ............... 错误!未定义书签。
2.3 零件加工的主要问题和工艺过程设计分析 ............. 错误!未定义书签。 3 工艺规程设计 ....................................................................... 错误!未定义书签。
3.1 确定毛坯的制造形式 ................................................. 错误!未定义书签。
3.2 基面的选择 ................................................................. 错误!未定义书签。
3.2.1 粗基准选择 ....................................................... 错误!未定义书签。
3.2.2 精基准的选择 ................................................... 错误!未定义书签。
3.3 制定工艺路线 ............................................................. 错误!未定义书签。
3.3.1 工艺路线方案一 ............................................... 错误!未定义书签。
3.3.2 工艺路线方案二 ............................................... 错误!未定义书签。
3.4 机械加工余量、工序尺寸及毛坯尺寸的确定 ......... 错误!未定义书签。
3.4.1 加工两端中心线上的外圆表面。 ................... 错误!未定义书签。
3.4.2 粗车?86 mm 与?93 mm外圆端面,及M12深24mm螺孔错误!未定义书签。
3.4.3 攻M12深24mm螺孔,及攻4―M20螺纹 .. 错误!未定义书签。
3.4.4 钻轴径?86 mm的`端面钻左端?6的锥行孔 错误!未定义书签。
3.4.5 铣右端轴径?93mm的上的槽 ........................ 错误!未定义书签。
3.4.6 铣?86处键槽 .................................................. 错误!未定义书签。
3.4.7 钻右端轴径?95 mm的孔(?30mm) .......... 错误!未定义书签。
3.4.8 铣115mm左右两侧面 ..................................... 错误!未定义书签。
3.4.9 铣60mm×115 mm平面 .................................... 错误!未定义书签。
3.4.10 钻拐径?95处的两个油孔(?8) ............... 错误!未定义书签。
3.4.11 车磨拐径为?95 mm ...................................... 错误!未定义书签。
3.5 确定切削用量及基本工时 ......................................... 错误!未定义书签。
3.6 时间定额计算及生产安排 ......................................... 错误!未定义书签。
3.6.1 粗车左端外圆?95 mm ...................................... 错误!未定义书签。
3.6.2 粗车左端轴径?90mm ..................................... 错误!未定义书签。
3.6.3 粗车左端轴径?86 mm .................................... 错误!未定义书签。
3.6.4 粗车拐径外侧左、右端面并粗车台肩 ........... 错误!未定义书签。
3.6.5 粗车拐径?95 mm ............................................ 错误!未定义书签。
3.6.6 精车拐径?95mm尺寸 .................................... 错误!未定义书签。
3.6.7 精车右端轴径?95 mm .................................... 错误!未定义书签。
3.6.8 精车右端轴径?93 mm .................................... 错误!未定义书签。
3.6.9 精车左端轴径?95+0.025
+0.003 mm ........................... 错误!未定义书签。
3.6.10 精铣底面60mm×115mm ................................ 错误!未定义书签。
3.6.11 钻、攻4―M20螺纹 ...................................... 错误!未定义书签。
3.6.12 铣键槽24mm×110mm .................................... 错误!未定义书签。
3.6.13 铣右端轴径?93mm的槽44+0.5
+0.2mm.............. 错误!未定义书签。
3.6.14 粗镗、精镗右端?30mm孔 .......................... 错误!未定义书签。
3.6.15 钻拐径?95-0.036
-0.071 mm斜油孔?8mm ............ 错误!未定义书签。
3.6.16 钻曲拐左侧孔?8mm ..................................... 错误!未定义书签。
3.6.17 粗磨左端轴径?95+0.025
+0.003 mm ......................... 错误!未定义书签。
3.6.18 磨左端轴径?90mm ....................................... 错误!未定义书签。
3.6.19 磨右端轴径?95 mm ...................................... 错误!未定义书签。
3.6.20 精磨拐径?95mm至规定尺寸 ...................... 错误!未定义书签。
3.6.21 精磨左右两轴径?95mm至规定尺寸 .......... 错误!未定义书签。
3.6.22 精磨?90mm至规定尺寸 .............................. 错误!未定义书签。
3.6.23 车1:10圆锥 ................................................. 错误!未定义书签。
3.6.24 磨1:10圆锥?86长124mm ....................... 错误!未定义书签。
4 专用夹具设计 ....................................................................... 错误!未定义书签。
4.1 加工曲拐上端面油孔夹具设计 ................................. 错误!未定义书签。
4.1.1 定位基准的选择 ............................................... 错误!未定义书签。
4.1.2 切削力的计算与夹紧力分析 ........................... 错误!未定义书签。
4.1.3 夹紧元件及动力装置确定 ............................... 错误!未定义书签。
4.1.4 钻套、衬套及夹具体设计 ............................... 错误!未定义书签。
4.1.5 夹具精度分析 ................................................... 错误!未定义书签。
4.2 加工曲拐上侧面油孔夹具设计 ................................. 错误!未定义书签。
4.2.1 定位基准的选择 ............................................... 错误!未定义书签。
4.2.2 切削力的计算与夹紧力分析 ........................... 错误!未定义书签。
4.2.3 夹紧元件及动力装置确定 ............................... 错误!未定义书签。
4.2.4 钻套、衬套及夹具体设计 ............................... 错误!未定义书签。
4.2.5 夹具精度分析 ................................................... 错误!未定义书签。
4.3 铣曲拐端面夹具设计 ................................................. 错误!未定义书签。
4.3.1 定位基准的选择 ............................................... 错误!未定义书签。
4.3.2 定位元件的设计 ............................................... 错误!未定义书签。
4.3.3 铣削力与夹紧力计算 ....................................... 错误!未定义书签。
4.3.4 对刀块和塞尺设计 ........................................... 错误!未定义书签。 5 结 论 ................................................................................... 错误!未定义书签。 参考文献 ..................................................................................... 错误!未定义书签。
篇6:《飞机制造工艺》课程教学实践与探索
《飞机制造工艺》课程教学实践与探索
本文针对飞行器制造工程、飞机设计等专业高年级本科生开设的飞机制造工艺课程教学实践,从该学科的独特性、目前教学内容和教学方式中存在的'问题,结合具体教学实践探讨了本课程教学中的一些心得、问题的解决方法及未来的教学思路等内容.
作 者:王志国 作者单位:南京航空航天大学机电学院航空宇航制造工程系,210016 刊 名:中国科技信息 英文刊名:CHINA SCIENCE AND TECHNOLOGY INFORMATION 年,卷(期): “”(5) 分类号: 关键词:飞机 制造 教学篇7:飞机工装设计制造技术探讨
飞机工装设计制造技术探讨
“十一五”期间,我国主要航空主机厂将承担多种型号飞机的研制和批量生产任务.按现有的工装研制模式,研制过程中需制造大量工艺装备,生产准备周期长,成本高,并需要大量的'生产用地,根本无法满足新型号研制和批生产的要求.
作 者:刘洪 作者单位:成都飞机工业(集团)有限责任公司技术装备公司 刊 名:航空制造技术 ISTIC英文刊名:AERONAUTICAL MANUFACTURING TECHNOLOGY 年,卷(期): “”(12) 分类号:V2 关键词:篇8:工装夹具设计的基本知识
1.夹具设计的基本要求 (1)工装夹具应具备足够的强度和刚度 (2)夹紧的可靠性 (3)焊接操作的灵活性 (4)便于焊件的装卸 (5)良好的工艺性 2.工装夹具设计的基本方法与步骤 (1)设计前的准备 夹具设计的原始资料包括以下内容: 1)夹具设计任务单; 2)工件图样及技术条件; 3)工件的装配工艺规程; 4)夹具设计的技术条件; 5)夹具的标准化和规格化资料,包括国家标准、工厂标准和规格化结构图册等, (2)设计的步骤 1)确定夹具结构方案 2)绘制夹具工作总图阶段 3)绘制装配焊接夹具零件图阶段 4)编写装配焊接夹具设计说明书 5)必要时,还需要编写装配焊接夹具使用说明书,包括机具的性能、使用注意事项等内容。 3.工装夹具制造的精度要求 夹具的制造公差,根据夹具元件的功用及装配要求不同可将夹具元件分为四类: 1)第一类是直接与工件接触,并严格确定工件的位置和形状的,主要包括接头定位件、V形块、定位销等定位元件,
2)第二类是各种导向件,此类元件虽不与定位工件直接接触,但它确定第一类元件的位置。 3)第三类属于夹具内部结构零件相互配合的夹具元件,如夹紧装置各组成零件之间的配合尺寸公差。 4)第四类是不影响工件位置,也不与其它元件相配合,如夹具的主体骨架等。 4.夹具结构工艺性 (1)对夹具良好工艺性的基本要求 1)整体夹具结构的组成,应尽量采用各种标准件和通用件,制造专用件的比例应尽量少,减少制造劳动量和降低费用。 2)各种专用零件和部件结构形状应容易制造和测量,装配和调试方便。 3)便于夹具的维护和修理。 (2)合理选择装配基准 1)装配基准应该是夹具上一个独立的基准表面或线,其它元件的位置只对此表面或线进行调整和修配。 2)装配基准一经加工完毕,其位置和尺寸就不应再变动。因此,那些在装配过程中自身的位置和尺寸尚须调整或修配的表面或线不能作为装配基准。 (3)结构的可调性 经常采用的是依靠螺栓紧固、销钉定位的方式,调整和装配夹具时,可对某一元件尺寸较方便地修磨。还可采用在元件与部件之间设置调整垫圈、调整垫片或调整套等来控制装配尺寸,补偿其它元件的误差,提高夹具精度。 (4)维修工艺性 进行夹具设计时,应考虑到维修方便的问题。
★ 上海书展实习报告
★ 工业工程应聘范文
★ 扶梯车间实习报告
★ 研制报告
★ 新年述职报告
★ 数控机床论文示例
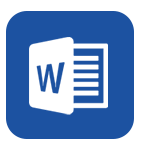
【飞机制造工装协同工艺设计(集锦8篇)】相关文章:
飞机数字化装配若干问题的思考2022-04-29
精益生产策略下车间生产准备管理技术2022-12-13
工艺工程师工作职责2022-09-09
机械工程及自动化专业就业前景薪酬排名等分析2022-10-11
公司技术部门的承诺书范本2024-03-04
先进制造技术课程教学方法研究2023-04-05
电子工艺员实习报告2022-12-16
精益专员个人简历2022-10-20
机械论文范文2022-11-28
钳工实习工作总结2023-02-07