机械制图与检验技术教程-1.3形状与位置公差(精选6篇)由网友“你的希伯来书”投稿提供,以下是小编精心整理的机械制图与检验技术教程-1.3形状与位置公差,希望对大家有所帮助。
篇1:机械制图与检验技术教程-1.3形状与位置公差
第三节、形状与位置公差
一、公差与配合术语、代号及其含义尺寸:用特定单位表示长度值的数字,机械制图与检验技术教程-1.3形状与位置公差
。孔:主要指圆柱形的内表面,也包括其他内表面中由单一尺寸确定的部分。轴:主要指圆柱形的外表面,也包括其他外表面中由单一尺寸确定的部分。基本尺寸:设计给定的尺寸。实际尺寸:通过测量所得的尺寸。由于存在测量误差,所以实际尺寸并非尺寸的真值。极限尺寸:允许尺寸变化的两个界限值,它以基本尺寸为基数来确定。最大极限尺寸:两个界限值中较大的一个称为最大极限尺寸。最小极限尺寸:两个界限值中较小的一个称为最小极限尺寸。尺寸偏差(简称偏差):某一尺寸减其基本尺寸所得的代数差。上偏差:最大极限尺寸减其基本尺寸所得的代数差称为上偏差。下偏差:最小极限尺寸减其基本尺寸所得的代数差称为下偏差。极限偏差:上偏差与下偏差统称为极限偏差。实际偏差:实际尺寸减其基本尺寸所得的代数差称为实际偏差。尺寸公差(简称公差):允许尺寸的变动量,公差等于最大极限尺寸与最小极限尺寸之代数差的绝对值;也等于上偏差与下偏差之代数差的绝对值。零线:在公差与配合图解(简称公差带图)中,确定偏差的一条基准直线,即零偏差线。通常,零线表示基本尺寸。尺寸公差带(简称公差带):在公差带图中,由代表上、下偏差的两条直线所限定的一个区域。标准公差:用以确定公差带大小的任一公差。公差单位:计算标准公差的基本单位,它是基本尺寸的函数。公差等级:确定尺寸精确程度的等级。属于同一公差等级的公差,对所有基本尺寸,虽数值不同,但被认为具有同等的精确程度。基本偏差:用以确定公差带相对于零线位置的上偏差或下偏差,一般为靠近零线的那个偏差。配合:基本尺寸相同的,相互结合的孔和轴公差带之间的关系。间隙:孔的尺寸减去相配合的轴的尺寸所得的代数差。此差值为正时是间隙。过盈:孔的尺寸减去相配合的轴的尺寸所得的代数差。此差值为负时是过盈。间隙配合:具有间隙(包括最小间隙等于零)的配合。此时,孔的公差带在轴的公差带之上。过盈配合;具有过盈(包括最小过盈等于零)的配合。此时,孔的公差带在轴的公差带之下。过渡配合:可能具有间隙或过盈的配合。此时,孔的公差带与轴的公差带相互交叠。最小间隙:对间隙配合,孔的最小极限尺寸减轴的最大极限尺寸所得的代数差。最大间隙:对间隙配合或过渡配合,孔的最大极限尺寸减轴的最小极限尺寸所得的代数差。最小过盈:对过盈配合,孔的最大极限尺寸减轴的最小极限尺寸所得的代数差。最大过盈:对过盈配合或过渡配合,孔的最小极限尺寸减轴的最大极限尺寸所得的代数差。配合公差:允许间隙或过盈的变动量。配合公差对间隙配合,等于最大间隙与最小间隙之代数差的绝对值;对过盈配合,等于最小过盈与最大过盈之代数差的绝对值;对过渡配合,等于最大间隙与最大过盈之代数差的绝对值。配合公差又等于相互配合的孔公关与轴公差之和。最大实体状态(MMC):孔或轴具有允许的材料量为最多时的状态,称为最大实体状态(MMC)最大实体尺寸:在最大实体状态下的尺寸称为最大实体尺寸,它是孔的最小极限尺寸和轴的最大极限尺寸的统称。最小实体状态(LMC):孔或轴具有允许的材料量为最少时的状态,称为最小实体状态(LMC)。最小实体尺寸:在最小实体状态下的尺寸称为最小实体尺寸,它是孔的最大极限尺寸和轴的最小极限尺寸的统称。孔的作用尺寸:在配合面的全长上,与实际孔内接的最大理想轴的尺寸,称为孔的作用尺寸。。轴的作用尺寸:在配合面的全长上,与实际轴承外接的最小理想孔的尺寸称为轴的作用尺寸。要素:构成零件几何特征的点、线、面。理想要素:具有几何学意义的要素。例如:点、球心、轴线、素线、直线、圆、圆柱面、圆锥面、球面、平面等。理想要素是指没有误差的要素,例如直线是绝对直的,圆是绝对圆的,平面是绝对平的等。实际要素:零件上实际存在要素。指可能有误差的要素,例如实际直线不怎么直,实际圆不怎么圆,实际平面不怎么平等。实际要素通过测量获得,由测量要素来代替,由于存在测量误差,测得要素,并非该要素的真实状况。被测要素:给出了形状或(和)位置公差的要素。指图样上规定的要素,制造时要求检测者。基准要求:用来确定被测要素方向或(和)位置的要素。理想基准要素简称基准。单一要素:仅对其本身给出形状公差要求的要素。关联要素:对其他要素有功能关系的要素。形状公差:单一实际要素的形状所允许的变动全量。形状误差:被测实际要素对其理想要素的变动量,理想要素的位置应符合最小条件。最小条件:被测实际要素对其理想要素的最大变动量为最小。位置公差:关联实际要素的位置对基准所允许的变动全量。位置公差分为定向公差、定位公差和跳动公差三大类。定向公差:关联实际要素对基准在方向上允许的变动全量。定向公差是位置公差之一。有:平行度、垂直度、倾斜度。定向误差:被测实际要素对一具有确定方向的理想要素的变动量,理想要素的方向由基准确定。定向误差是位置误差之一。第三节、形状与位置公差
一、公差与配合术语、代号及其含义尺寸:用特定单位表示长度值的数字。孔:主要指圆柱形的内表面,也包括其他内表面中由单一尺寸确定的部分。轴:主要指圆柱形的外表面,也包括其他外表面中由单一尺寸确定的部分。基本尺寸:设计给定的尺寸。实际尺寸:通过测量所得的尺寸。由于存在测量误差,所以实际尺寸并非尺寸的真值。极限尺寸:允许尺寸变化的两个界限值,它以基本尺寸为基数来确定。最大极限尺寸:两个界限值中较大的一个称为最大极限尺寸。最小极限尺寸:两个界限值中较小的一个称为最小极限尺寸。尺寸偏差(简称偏差):某一尺寸减其基本尺寸所得的代数差。上偏差:最大极限尺寸减其基本尺寸所得的代数差称为上偏差。下偏差:最小极限尺寸减其基本尺寸所得的代数差称为下偏差。极限偏差:上偏差与下偏差统称为极限偏差。实际偏差:实际尺寸减其基本尺寸所得的代数差称为实际偏差。尺寸公差(简称公差):允许尺寸的变动量,公差等于最大极限尺寸与最小极限尺寸之代数差的绝对值;也等于上偏差与下偏差之代数差的绝对值。零线:在公差与配合图解(简称公差带图)中,确定偏差的一条基准直线,即零偏差线。通常,零线表示基本尺寸。尺寸公差带(简称公差带):在公差带图中,由代表上、下偏差的两条直线所限定的一个区域。标准公差:用以确定公差带大小的任一公差。公差单位:计算标准公差的基本单位,它是基本尺寸的函数。公差等级:确定尺寸精确程度的等级。属于同一公差等级的公差,对所有基本尺寸,虽数值不同,但被认为具有同等的精确程度。基本偏差:用以确定公差带相对于零线位置的上偏差或下偏差,一般为靠近零线的那个偏差。配合:基本尺寸相同的,相互结合的孔和轴公差带之间的关系。间隙:孔的尺寸减去相配合的轴的尺寸所得的代数差。此差值为正时是间隙。过盈:孔的尺寸减去相配合的轴的尺寸所得的代数差。此差值为负时是过盈。间隙配合:具有间隙(包括最小间隙等于零)的配合。此时,孔的公差带在轴的公差带之上。过盈配合;具有过盈(包括最小过盈等于零)的配合。此时,孔的公差带在轴的公差带之下。过渡配合:可能具有间隙或过盈的配合。此时,孔的公差带与轴的公差带相互交叠。最小间隙:对间隙配合,孔的最小极限尺寸减轴的最大极限尺寸所得的代数差。最大间隙:对间隙配合或过渡配合,孔的最大极限尺寸减轴的最小极限尺寸所得的代数差。最小过盈:对过盈配合,孔的最大极限尺寸减轴的最小极限尺寸所得的代数差。最大过盈:对过盈配合或过渡配合,孔的最小极限尺寸减轴的最大极限尺寸所得的代数差。配合公差:允许间隙或过盈的变动量。配合公差对间隙配合,等于最大间隙与最小间隙之代数差的绝对值;对过盈配合,等于最小过盈与最大过盈之代数差的绝对值;对过渡配合,等于最大间隙与最大过盈之代数差的绝对值。配合公差又等于相互配合的孔公关与轴公差之和。最大实体状态(MMC):孔或轴具有允许的材料量为最多时的状态,称为最大实体状态(MMC)最大实体尺寸:在最大实体状态下的尺寸称为最大实体尺寸,它是孔的最小极限尺寸和轴的最大极限尺寸的统称。最小实体状态(LMC):孔或轴具有允许的材料量为最少时的状态,称为最小实体状态(LMC)。最小实体尺寸:在最小实体状态下的尺寸称为最小实体尺寸,它是孔的最大极限尺寸和轴的最小极限尺寸的统称。孔的作用尺寸:在配合面的全长上,与实际孔内接的最大理想轴的尺寸,称为孔的作用尺寸。。轴的作用尺寸:在配合面的全长上,与实际轴承外接的最小理想孔的尺寸称为轴的作用尺寸。要素:构成零件几何特征的点、线、面。理想要素:具有几何学意义的要素。例如:点、球心、轴线、素线、直线、圆、圆柱面、圆锥面、球面、平面等。理想要素是指没有误差的要素,例如直线是绝对直的,圆是绝对圆的,平面是绝对平的等。实际要素:零件上实际存在要素。指可能有误差的要素,例如实际直线不怎么直,实际圆不怎么圆,实际平面不怎么平等。实际要素通过测量获得,由测量要素来代替,由于存在测量误差,测得要素,并非该要素的真实状况。被测要素:给出了形状或(和)位置公差的要素。指图样上规定的要素,制造时要求检测者。基准要求:用来确定被测要素方向或(和)位置的要素。理想基准要素简称基准。单一要素:仅对其本身给出形状公差要求的要素。关联要素:对其他要素有功能关系的要素。形状公差:单一实际要素的形状所允许的变动全量。形状误差:被测实际要素对其理想要素的变动量,理想要素的位置应符合最小条件。最小条件:被测实际要素对其理想要素的最大变动量为最小。位置公差:关联实际要素的位置对基准所允许的变动全量。位置公差分为定向公差、定位公差和跳动公差三大类。定向公差:关联实际要素对基准在方向上允许的变动全量。定向公差是位置公差之一。有:平行度、垂直度、倾斜度。定向误差:被测实际要素对一具有确定方向的理想要素的变动量,理想要素的方向由基准确定。定向误差是位置误差之一。定位公差:关联实际要素对基准在位置上允许的变动全量。定位公差有:同轴度、对称度、位置度。定位误差:被测实际要素对一具有确定位置的理想要素的变动量,理想要素的位置由基准和理论正确尺寸确定。对于同轴度和对称度,理论正确尺寸为零。理论正确尺寸:确定被测要素的理想形状、方向、位置的尺寸。该尺寸不附带公差。理论正确尺寸是绝对准确 的尺寸,在图样上用方框围住。几何图形:确定一组理想要素之间和(或)它们与基准之间正确几何关系的图形。公差原则:处理尺寸公差、形状公差和位置公差之间关系的原则。公差原则包括独立原则和相关原则。独立原则:图样上给定的形状公差与尺寸公差相互无关,分别满足要求的公差原则。在尺寸公差后无符号E 、在形状公差中无符号“0M ”或“ M ”时,即按独立原则处理形位公差与尺寸公差之间的关系。相关原则:图样上给定的形位公差与尺寸公差相互有关的公差原则。相关原则分为包容原则和最大实体原则两类。包容原则E 0M :要求实际要素处处位于具有理想形状的包容面内的一种公差原则,而该理想形状的尺寸应为最大实体尺寸。尺寸公差后带符号E 、形位公差中带符号“0M ”时,即按包容原则处理。最大实体原则M:被测要素或(和)基准要素偏离最大实体状态,而形状、定向、定位公差获得补偿值的一种公差原则。形位公差中带符号“M”时,即按最大实体原则处理。局部实际尺寸:在实际要素的任意正截面上,两测量点之间测得的距离。作用尺寸:在轴和孔配合时真正起作用的尺寸,即考虑了形位误差后真正起作用的尺寸。单一要素的作用尺寸:在结合面的全长上,与实际孔内接的最大理想轴的尺寸,称为孔的作用尺寸。在结合面的全长上,与实际轴外接最小理想孔的尺寸,称为轴的作用尺寸。关联要素的作用尺寸:在结合面的全长上,与实际孔内接的最大理想轴的尺寸,称为孔的关联作用尺寸,而该理想轴必须与基准要素保持图样上给定的几何关系。在结合面的全长上,与实际轴外接的最小理想孔的尺寸,称为轴的关联作用尺寸,而该理想孔必须与基准保持图样上给定的几何关系。最大实体状态(MMC):实际要素在尺寸公差范围内具有材料量最多的状态。最大实体尺寸:实际要素在最大实际状态时的尺寸。对于孔类,最大实体尺寸是指最小极限尺寸,对于轴类,最大实体尺寸是指最大极限尺寸。最小实体状态(LMC):实际要素在尺寸公差范围内具有材料量最少的状态。最小实体尺寸:实际要素在最小实体状态时的尺寸。对于孔类,最小实体尺寸是指最大极限尺寸。对于轴类,最小实体尺寸是指最小极限尺寸。实效状态(VC):在尺寸公差和形位公差范围内实际要素的综合极限状态。单一要素的实效状态:由图样上给定的被测要素最大实体尺寸和该要素轴线或中心平面的形状公差所形成的综合极限边界,该边界应具有理想状态。关联要素的实效状态:由图样上给定的被测要素最大实体尺寸和该要素的定向或定位公差所形成的综合极限边界,该极限边界应具有理想形状并应符合图样上给定的几何关系。实效尺寸:实效状态时的边界尺寸。实效尺寸是综合考虑尺寸公差和形状(位置)公差后的综合边界尺寸,是一个给定值。基准:即理想基准要素,它是确定要素几何关系的依据,分别称为基准点,基准直线(轴线)和基准平面(中心平面)单一基准要素:作为单一基准使用的单个要素。组合基准要素:作为单一基准使用的一组要素。三基面体系:由三个互相垂直的基准平面组成的基准体系,它的三个平面是确定和测量零件上各要素几何关系的起点。基准目标:为构成基准体系的各基准平面而在要素上指定的点、线、面。延伸公差带P:根据零件的功能要求,位置度和对称度公差带需延伸到被测要素的长度界限之外时,该公差带称延伸公差带。在尺寸前标符号P 。二、公差原则 零件上的尺寸、形状和位置误差,均会影响零件的互换性和使用质量,都要分别给出一个经济合理的允许变动范围,即由相应的公差加以限制。我们在实际工作中往往会发现,尺寸公差、形状公差和位置公差三者在某些场合下有一定联系。例如一个圆柱轴,虽然各个剖面的直径尺寸合格,但如果存在形状误差(例如不圆、轴线不直等),也可能装不进一个基本尺寸相同的孔中,即不能保证互换性。为了解决尺寸公差、形状公差和位置公差之间的关系,需要明确处理相互关系的基本原则。处理各项公差关系的原则称为公差原则。1、基本概念(1)局部实际尺寸和作用尺寸局部实际尺寸在实际要素的任意正截面上,两测量点之间测得的距离,称为局部实际尺寸。由于存在测量误差,所以局部实际尺寸并非该尺寸的真值。同时由于形状误差的影响,同一实际要素不同部位的局部实际尺寸亦不相等。作用尺寸由于实际要素都存在形位误差,因此不能单从局部实际尺寸来判断两相互配合的孔和轴实际起作用的尺寸,因而引入“作用尺寸”这一概念。简单来说,“作用尺寸”就是在配合时,考虑了形位误差后真正起作用的尺寸。这里又分单一要素和关联要素两种情况。A、单一要素的作用尺寸(简称作用尺寸)在结合面的全长上,与实际孔内接的最大理想轴的尺寸,称为孔的作用尺寸(图1-1a)。在结合面的全长上,与实际轴外接的最小理想孔的尺寸,称为轴的作用尺寸(图1-1b)。图1-1B、关联要素的作用尺寸(简称关联作用尺寸)在结合面的全长上,与实际孔内接的最大理想轴的尺寸,称为孔的关联作用尺寸,该理想轴应与基准要素保持图样上给定的几何关系(图1-2a)。在结合面的全长上,与实际轴外接的最小理想孔的尺寸,称为轴的关联作用尺寸,该理想孔应与基准要素保持图样上给定的几何关系(图1-2b)。从以上作用尺寸的定义可以看出:所谓作用尺寸是考虑了局部实际尺寸和形位误差两方面的因素,在装配时真正起作用的尺寸。对于单一要素来说:孔的作用尺寸=孔的局部实际尺寸一形位误差;轴的作用尺寸=轴的局部实际尺寸+形状误差。对于关联要素来说:孔的关联作用尺寸=孔的局部实际尺寸-形状和位置误差;轴的关联作用尺寸=轴的局部实际尺寸+形状和位置误差,当不存在位置误差时,关联作用尺寸等于单一要素作用尺寸。当存在位置误差时,孔的关联作用尺寸小于孔的作用尺寸;轴的关联作用尺寸大于轴的作用尺寸。作用尺寸是一个实际值,对于不同的零件,由于局部实际尺寸和形位误差可能不相同,因而其作用尺寸也可能不相同。(a) (b)图1-2 关联作用尺寸(a)孔的关联作用尺寸;(b)轴的关联作用尺寸(2)实体状态和实效状态为了限制零件的局部实际尺寸和作用尺寸在某一允许的范围内,确保互换性,需要确定某一理想尺寸,因而引入“实体尺寸”和“实效尺寸”以及相应的“实体状态”和“实效状态”等名词。最大、最小实体状态A、最大实体状态(英文缩写MMC)实际要素在尺寸公差范围内具有材料量最多的状态。最大实体尺寸:实际要素在最大实体状态时的尺寸。孔的最大实体尺寸=孔的最小极限尺寸;
轴的最大实体尺寸=轴的最大极限尺寸。
例如;孔Ø22
其最大实体尺寸为Ø 22.01. 轴Ø22其最大实体尺寸为Ø22.02.
B、最小实体状态(英文缩写为LMC)实际要素在尺寸公差范围内具有材料量最少的状态.最小实体尺寸:实际要素在最小实体状态时的尺寸.孔的最小实体尺寸=孔的最大极限尺寸;轴的最小实体尺寸=轴的最小极限尺寸.例如:孔Ø22其最小实体尺寸为Ø22.02;
轴Ø22其最小实体尺寸为Ø22.01.
由此可见,零件规定了尺寸公差后,其最大、最小实体尺寸也就确定了。实体尺寸是指某一极限尺寸,是给定值。实效状态(英文缩写为VC)在尺寸公差和形位公差范围内实际要素的综合极限状态,称为实效状态.又分为单一要素和关联要素两种实效状态:A、单一要素的实效状态(简称单一实效状态):是指由图样上给定的被测要素最大实体尺寸和该要素轴线或中心平面的形状公差所形成的综合极限边界;该极限边界应具有理想状态.单一要素的实效尺寸为处于单一实效状态时的尺寸,如图1-3所示.孔的单一实效尺寸=孔的最小极限尺寸-形状公差;轴的单一实效尺寸=轴的最大极限尺寸+形状公差;(a)(b) 图1-3 单一实效状态和单一实效尺寸 B、关联要素的实效状态(简称关联实效状态):是指由图样上给定的被测要素最大实体尺寸和该要素的定向或定位公差所形成的综合极限边界,该极限边界应具有理想形状并应符合图样上给出定的几合关系。关联要素的实际尺寸为处于关联实效状态时的尺寸,如图1-4所示。孔的关联实效尺寸=孔的最小极限尺寸-位置公差值;轴的关联实效尺寸=轴的最大极限尺寸+位置公差值。由于可见,实效尺寸是综合考虑尺寸公差和形状(或位置)公差后的综合边界尺寸,是一个给定值。3、理想边界根据图纸上给定的尺寸公差和形位公差,理想边界是实际要素几何偶件(即与实际孔内接或与实际轴外接,且具有理想形状的要素)的极限。常用的理想边界有最大实体边界(MMC边界)和实效边界(VC边界)。理想边界的特点是:1、最大实体边界(MMC边界)和实效边界(VC边界)为实际要素全长范围内几何偶件的极限,其尺寸分别最大实体尺寸和实效尺寸。2、单一要素的理想边界不必考虑与基准的关系,因此这种边界的位置与方向将随着要素的实际状态而变化。(a)(b) 图1-4 单一实效状态和单一实效尺寸3、关联要素的理想边界必须与基准成图纸上给定的正确几何关系,因此这种边界的位置与方向是确定的。4、理想边界存在于要素之外,是设计综合量规的依据。4、独立原则根据设计要求,形位公差与尺寸公差可以相互独立地规定,分别满足要求,它们之间相互无关,这种公差原则称为独立原则。独立原则是标注形位公差和尺寸公差相互关系的基本公差原则。为了简化,在尺寸公差后无符号E、在形位公差中无符号“0M”或M时,即按独立原则处理形位公差和尺寸公差之间的关系。即图样上所规定的尺寸公差和形位公差互不相关,尺寸误差由尺寸公差控制,形位误差由形位公差控制,尺寸公差与形位公差之间不存在补偿关系。独立原则主要用于满足功能要求。检测时通常不采用综合量规而用通用量仪进行测量,对检验员的技术水平要求较高。三、采用独立原则时对尺寸公差的解释这里又分线性尺寸公差和角度公差两种情况。1.线性尺寸公差线性尺寸公差仅控制要素局部实际尺寸的变动量,不控制要素本身的形状误差(如圆柱要素的圆度和直线度误差或平行表面的平面度误差)。线性尺寸公差用线性量表示。
如图1-5所示,一圆柱直径为Ø50h7,尺寸公差后无符号E,即表示按独立原则。这时,实际轴的局部实际尺寸必须在49.975至50之间;线性尺寸公差(0.025)不控制要素本身的形状误差。图1-6所示零件的直线度和圆度(包括奇数棱圆)误差由相应的未注形状公差控制。图1-5 线性尺寸遵循独立原则A1、A2、A3……An局部实际尺寸:在49.975至50之间 图1-62.角度公差角度公差仅控制被测要素的理想要素之间的角度变动量,不控制被测要素的形状误差,且理想要素的位置应符合最小条件。角度公差用相应的角度量表示。图1-7 角度尺寸遵循独立原则 图1-8如图1-7所示,角度45±2º遵循独立原则。这时,要求A、B两被测实际要素分别按最小条件确定其理想要素,该两理想要素间的夹角应在给定的两极限角度之间,角度公差不控制实际要素的形状误差(图1-8),实际要素的形状误差由相应的未注形状公差控制。四、采用独立原则时,对形位公差的解释采用独立原则时,图样上给定的形位公差与被测要素的局部实际尺寸无并。不论要素的局部实际尺寸大小如何,被测要素均应在给定的形位公差带内,并且其形位误差允许达到最大值。如图1-9所示,轴的局部实际尺寸应在最大极限尺寸与最小极限尺寸之间:轴的形状误差应在给定的相应形状公差之内。不论轴的局部实际尺寸如何,其形状误差(轴线直线度误差和横截面奇数棱圆误差)允许达到给定的最大值(图1-10)。图1-9 独立原则示例(a)(b) 图1-101、相关原则根据设计要求,形状公差与尺寸公差可以相互关联地规定,这种公差原则称为相关原则。相关原则又分为包容原则和最大实体原则两种情况。五、包容原则包容原则是要求被测要素处处均位于最大实体边界之内的一种公差原则,它是在保证配合性能和装配互换性的前提下建立的。1.包容原则应用于单一要素单一要素遵守包容原则时,要求实际单一要素处处不得超越最大实体边界。实际要素的局部实际尺寸不得超越最小实体尺寸。对遵守包容原则的单一要素,应在其尺寸极限偏差或公差带代号之后加注符号“E”。图1-11如图1-11所示,外圆柱面应遵守包容原则。此时,圆柱表面必须在最大实体边界内,该边界的尺寸为最大实体尺寸Ø50。其局部实际尺寸不得小于49.975(图1-12),由此可见,包容原则应用于单一要素时,能综合控制圆柱表面的纵、横截面的各种形状误差,如圆度误差、轴线直线度误差、圆柱度误差等。图1-122.包容原则应用于关联要素关联要素遵守包容原则时,要求其实际轮廓处处不得超越最大实体边界,而该边界应与基准保持图样上给定的几何关系。要素实际轮廓的局部实际尺寸不得超越最小实体尺寸。对遵守包容原则的关联要素,在图样的形位公差框格中用“0M”形状标注。如图1-13所示,与端面A保持垂直的外圆柱面要求遵守包容原则。此时,圆柱表面必须在最大实体边界内,该边界的尺寸为最大实体尺寸Ø50,且与基准平面A垂直。实际圆柱的局部实际尺寸不得小于49.975(图1-14)。图1-13 图1-14五、大实体原则最大实体原则是当被要素或(和)基准要素偏离最大实体状态时,形状、定向、定位公差获得补偿值的一种公差原则。它是在主要用于保证装配互换性的前提下建立的,其主要内容包括:1图纸上给出的形位公差值是在被测要素或(和)基准要素处于最大实体状态(或实效状态)时给定的。2被测要素的实际状态必须遵守VC边界。当被测实际要素偏离最大实体状态时,形位公差可从尺寸公差获得补偿,当要素处于最小实体状态时,所获得的补偿为最大。3当基准实际要素偏离其最大实体状态时,允许基准轴线与基准要素理想边界产生偏离。4要素的局部实际尺寸由最大、最小极限尺寸限制。对遵守最大实体原则的有关要素,应在相应的形位公差框格中加注符号“M”。应用最大实体原则的实效尺寸按以下公式计算:轴的实效尺寸=轴的最大极限尺寸+形状或位置公差(图1-15);孔的实效尺寸=孔的最小极限尺寸-形状或位置公差(图1-16)。(a)单一要素的实效尺寸为:Ø45+ Ø0.03= Ø45.03 (b)关联要素的实效尺寸:Ø45+ Ø0.03= Ø45.03 图1-15 轴的实效尺寸(a)单一要素的实效尺寸为:Ø50- Ø0.03= Ø49.97 (b)关联要素的实效尺寸:Ø50- Ø0.03= Ø49.97 图1-16 孔的实效尺寸说明:1、包容原则与最大实体原则的关系1包容原则与最大实体原则都是形位公差和尺寸公差相互关联的公差原则。包容原则是从尺寸公差控制形位误差这一角度来定义的;而最大实体原则是从尺寸公差补偿形位公关芝一角度来定义的。2这两种原则要求被测实际要素遵守的理想边界不同,包容原则要求遵守最大实体(MMC)边界;最大实体原则要求遵守实效(VC)边界。2、公差原则小结表1-1列出了三项公差原则的应用与标注;表1-2列出了三项公差原则的应用示例比较。2、形位公差标注的内容及有关符号的含义3、有关符号的含义6、公差数值的识读图6-1是对”中间凸起”的解释,即两端向中间材料不断增加。图中(a)是平面中间凸起的解释;(b)是内孔中间凸起的解释。(a) (b) 图6-1“中间凸起”的解释 (a)平面;(b)内孔 6、本公司常用形状和位置公差的标注示例篇2:形状与位置公差概述
一、零件的形位误差及对其使用性能的影响
1.形位误差的产生 刀具运动方向与工件旋转轴线不平行、内应力;夹紧力;温度;刀具磨损;切削中的振动;热处理变形等等,
2.形位误差对使用性能的影响 影响产品质量、零件的互换性,也影响产品之间的配合性质,工作精度,运动平稳性,耐磨、密封性等。是衡量产品质量的一项重要指标。如:间隙配合时,会使间隙分布不均匀,加快局部磨损,使使用寿命降低。过盈配合时则造成各处过盈量不一致而影响连接强度。机床导轨的直线度和平面度将影响刀架的运动精度。齿轮箱上各轴承孔的位置误差将影响齿面的接触均匀性和齿侧间隙等。形状与位置公差及检测概述
刀具运动方向与工件旋转轴线不平行
钻头移动方向与机床工作台面不垂直
在车削由三爪卡盘夹紧的环形工件的内孔时,会因夹紧力使工件变形而形成棱圆形
二、零件的几何要素与形位误差 零件不论其结构特征如何,都是由一些简单的点、线、面组成,这些点、线、面统称为几何要素。形状是一个要素本身所处的状态,位置则是指两个以上要素之间所形成的方位关系。
篇3:形状与位置公差概述
1.按结构特征分:
1)轮廓要素:平面,圆柱
2)中心要素:抽象的,但存在
2.按存在的状态分:
1)实际要素:实际存在的
2)理想要素:几何的点、线、面
3.在形位公差中所处的地位分:
1)被测要素:图样上给出形位公差要求的检测对象
2)基准要素:确定被测要素方向和位置的要素,图纸上用基准符号标出
4.按结构的性能分:
1)单一要素:具有形状公差的要求
2)关联要素:与其他要素具有功能关系的要素,位置公差三、相关的标准: GB/T1182-《形状和位置公差、通则、定义、符号和图样标注》 GB/T1184-1996《形状和位置公差未注公差值》 GB4249-1996《公差原则》 GB/T16671-1996《形状和位置公差 最大实体要求 最小实体要求和可逆要求》 GB13319-91《位置度公差》形状与位置公差概述四、形位公差项目(略)形状公差
一、定义 单一实际要素的形状所允许的变动全量,
二、形状公差带:限制实际要素变动的区域,零件的实际要素在该区域内为合格。
三、形状公差带的形状
形状公差带有形状、方向、位置和大小四要素
篇4:机械制图与检验技术教程-2常用术语
第二章、常用术语
一、公差与配合术语、尺寸:用特定单位表示长度值的数字,机械制图与检验技术教程-2常用术语
。孔:主要指圆柱形的内表面,也包括其他内表面中由单一尺寸确定的部分。轴:主要指圆柱形的外表面,也包括其他外表面中由单一尺寸确定的部分。基本尺寸:设计给定的尺寸。实际尺寸:通过测量所得的尺寸。由于存在测量误差,所以实际尺寸并非尺寸的真值。极限尺寸:允许尺寸变化的两个界限值,它以基本尺寸为基数来确定。最大极限尺寸:两个界限值中较大的一个称为最大极限尺寸。最小极限尺寸:两个界限值中较小的一个称为最小极限尺寸。尺寸偏差(简称偏差):某一尺寸减其基本尺寸所得的代数差。上偏差:最大极限尺寸减其基本尺寸所得的代数差称为上偏差。下偏差:最小极限尺寸减其基本尺寸所得的代数差称为下偏差。极限偏差:上偏差与下偏差统称为极限偏差。实际偏差:实际尺寸减其基本尺寸所得的代数差称为实际偏差。尺寸公差(简称公差):允许尺寸的变动量,公差等于最大极限尺寸与最小极限尺寸之代数差的绝对值;也等于上偏差与下偏差之代数差的绝对值。零线:在公差与配合图解(简称公差带图)中,确定偏差的一条基准直线,即零偏差线。通常,零线表示基本尺寸。尺寸公差带(简称公差带):在公差带图中,由代表上、下偏差的两条直线所限定的一个区域。标准公差:用以确定公差带大小的任一公差。公差单位:计算标准公差的基本单位,它是基本尺寸的函数。公差等级:确定尺寸精确程度的等级。属于同一公差等级的公差,对所有基本尺寸,虽数值不同,但被认为具有同等的精确程度。基本偏差:用以确定公差带相对于零线位置的上偏差或下偏差,一般为靠近零线的那个偏差。配合:基本尺寸相同的,相互结合的孔和轴公差带之间的关系。间隙:孔的尺寸减去相配合的轴的尺寸所得的代数差。此差值为正时是间隙。过盈:孔的尺寸减去相配合的轴的尺寸所得的代数差。此差值为负时是过盈。间隙配合:具有间隙(包括最小间隙等于零)的配合。此时,孔的公差带在轴的公差带之上。过盈配合:具有过盈(包括最小过盈等于零)的配合。此时,孔的公差带在轴的公差带之下。过渡配合:可能具有间隙或过盈的配合。此时,孔的公差带与轴的公差带相互交叠。最小间隙:对间隙配合,孔的最小极限尺寸减轴的最大极限尺寸所得的代数差。最大间隙:对间隙配合或过渡配合,孔的最大极限尺寸减轴的最小极限尺寸所得的代数差。最小过盈:对过盈配合,孔的最大极限尺寸减轴的最小极限尺寸所得的代数差。最大过盈:对过盈配合或过渡配合,孔的最小极限尺寸减轴的最大极限尺寸所得的代数差。配合公差:允许间隙或过盈的变动量。配合公差对间隙配合,等于最大间隙与最小间隙之代数差的绝对值:绝对过盈配合,等于最小过盈与最大过盈之代数差的绝对值;绝对过渡配合,等于最大间 隙与最大过盈之代数差的绝对值。配合公差又等于相互配合的孔公关与轴公差之和。最大实体状态(MMC):孔或轴具有允许的材料量为最多时的状态,称为最大实体状态(MMC)最大实体尺寸:在最大实体状态下的尺寸称为最大实体尺寸,它是孔的最小极限尺寸和轴的最大极限尺寸的统称。最小实体状态(LMC):孔或轴具有允许的材料量为最少时的状态,称为最小实体状态(LMC)。最小实体尺寸:在最小实体状态下的尺寸称为最小实体尺寸,它是孔的最大极限尺寸和轴的最小极限尺寸的统称。孔的作用尺寸:在配合面的全长上,与实际孔内接的最大理想轴的尺寸,称为孔的作用尺寸。。轴的作用尺寸:在配合面的全长上,与实际轴承外接的最小理想孔的尺寸称为轴的作用尺寸。二、形位公差术语、要素:构成零件几何特征的点、线、面。理想要素:具有几何学意义的要素。例如:点、球心、轴线、素线、直线、圆、圆柱面、圆锥面、球面、平面等。理想要素是指没有误差的要素,例如直线是绝对直的,圆是绝对圆的,平面是绝对平的等。实际要素:零件上实际存在要素。指可能有误差的要素,例如实际直线不怎么直,实际圆不怎么圆,实际平面不怎么平等。实际要素通过测量获得,由测量要素来代替,由于存在测量误差,测得要素,并非该要素的真实状况。被测要素:给出了形状或(和)位置公差的要素。指图样上规定的要素,制造时要求检测者。基准要求:用来确定被测要素方向或(和)位置的要素。理想基准要素简称基准。单一要素:仅对其本身给出形状公差要求的要素。关联要素:对其他要素有功能关系的要素。形状公差:单一实际要素的形状所允许的变动全量。形状误差:被测实际要素对其理想要素的变动量,理想要素的位置应符合最小条件。最小条件:被测实际要素对其理想要素的最大变动量为最小。位置公差:关联实际要素的位置对基准所允许的变动全量。位置公差分为定向公差、定位公差和跳动公差三大类。定向公差:关联实际要素对基准在方向上允许的变动全量。定向公差是位置公差之一。有:平行度、垂直度、倾斜度。第二章、常用术语
一、公差与配合术语、尺寸:用特定单位表示长度值的数字。孔:主要指圆柱形的内表面,也包括其他内表面中由单一尺寸确定的部分。轴:主要指圆柱形的外表面,也包括其他外表面中由单一尺寸确定的部分。基本尺寸:设计给定的尺寸。实际尺寸:通过测量所得的尺寸。由于存在测量误差,所以实际尺寸并非尺寸的真值。极限尺寸:允许尺寸变化的两个界限值,它以基本尺寸为基数来确定。最大极限尺寸:两个界限值中较大的一个称为最大极限尺寸。最小极限尺寸:两个界限值中较小的一个称为最小极限尺寸。尺寸偏差(简称偏差):某一尺寸减其基本尺寸所得的代数差。上偏差:最大极限尺寸减其基本尺寸所得的代数差称为上偏差。下偏差:最小极限尺寸减其基本尺寸所得的代数差称为下偏差。极限偏差:上偏差与下偏差统称为极限偏差。实际偏差:实际尺寸减其基本尺寸所得的代数差称为实际偏差。尺寸公差(简称公差):允许尺寸的变动量,公差等于最大极限尺寸与最小极限尺寸之代数差的绝对值;也等于上偏差与下偏差之代数差的绝对值。零线:在公差与配合图解(简称公差带图)中,确定偏差的一条基准直线,即零偏差线。通常,零线表示基本尺寸。尺寸公差带(简称公差带):在公差带图中,由代表上、下偏差的两条直线所限定的一个区域。标准公差:用以确定公差带大小的任一公差。公差单位:计算标准公差的基本单位,它是基本尺寸的函数。公差等级:确定尺寸精确程度的等级。属于同一公差等级的公差,对所有基本尺寸,虽数值不同,但被认为具有同等的精确程度。基本偏差:用以确定公差带相对于零线位置的上偏差或下偏差,一般为靠近零线的那个偏差。配合:基本尺寸相同的,相互结合的孔和轴公差带之间的关系。间隙:孔的尺寸减去相配合的轴的尺寸所得的代数差。此差值为正时是间隙。过盈:孔的尺寸减去相配合的轴的尺寸所得的代数差。此差值为负时是过盈。间隙配合:具有间隙(包括最小间隙等于零)的配合。此时,孔的公差带在轴的公差带之上。过盈配合:具有过盈(包括最小过盈等于零)的配合。此时,孔的公差带在轴的公差带之下。过渡配合:可能具有间隙或过盈的配合。此时,孔的公差带与轴的公差带相互交叠。最小间隙:对间隙配合,孔的最小极限尺寸减轴的最大极限尺寸所得的代数差,最大间隙:对间隙配合或过渡配合,孔的最大极限尺寸减轴的最小极限尺寸所得的代数差。最小过盈:对过盈配合,孔的最大极限尺寸减轴的最小极限尺寸所得的代数差。最大过盈:对过盈配合或过渡配合,孔的最小极限尺寸减轴的最大极限尺寸所得的代数差。配合公差:允许间隙或过盈的变动量。配合公差对间隙配合,等于最大间隙与最小间隙之代数差的绝对值:绝对过盈配合,等于最小过盈与最大过盈之代数差的绝对值;绝对过渡配合,等于最大间 隙与最大过盈之代数差的绝对值。配合公差又等于相互配合的孔公关与轴公差之和。最大实体状态(MMC):孔或轴具有允许的材料量为最多时的状态,称为最大实体状态(MMC)最大实体尺寸:在最大实体状态下的尺寸称为最大实体尺寸,它是孔的最小极限尺寸和轴的最大极限尺寸的统称。最小实体状态(LMC):孔或轴具有允许的材料量为最少时的状态,称为最小实体状态(LMC)。最小实体尺寸:在最小实体状态下的尺寸称为最小实体尺寸,它是孔的最大极限尺寸和轴的最小极限尺寸的统称。孔的作用尺寸:在配合面的全长上,与实际孔内接的最大理想轴的尺寸,称为孔的作用尺寸。。轴的作用尺寸:在配合面的全长上,与实际轴承外接的最小理想孔的尺寸称为轴的作用尺寸。二、形位公差术语、要素:构成零件几何特征的点、线、面。理想要素:具有几何学意义的要素。例如:点、球心、轴线、素线、直线、圆、圆柱面、圆锥面、球面、平面等。理想要素是指没有误差的要素,例如直线是绝对直的,圆是绝对圆的,平面是绝对平的等。实际要素:零件上实际存在要素。指可能有误差的要素,例如实际直线不怎么直,实际圆不怎么圆,实际平面不怎么平等。实际要素通过测量获得,由测量要素来代替,由于存在测量误差,测得要素,并非该要素的真实状况。被测要素:给出了形状或(和)位置公差的要素。指图样上规定的要素,制造时要求检测者。基准要求:用来确定被测要素方向或(和)位置的要素。理想基准要素简称基准。单一要素:仅对其本身给出形状公差要求的要素。关联要素:对其他要素有功能关系的要素。形状公差:单一实际要素的形状所允许的变动全量。形状误差:被测实际要素对其理想要素的变动量,理想要素的位置应符合最小条件。最小条件:被测实际要素对其理想要素的最大变动量为最小。位置公差:关联实际要素的位置对基准所允许的变动全量。位置公差分为定向公差、定位公差和跳动公差三大类。定向公差:关联实际要素对基准在方向上允许的变动全量。定向公差是位置公差之一。有:平行度、垂直度、倾斜度。定向误差:被测实际要素对一具有确定方向的理想要素的变动量,理想要素的方向由基准确定。定向误差是位置误差之一。定位公差:关联实际要素对基准在位置上允许的变动全量。定位公差有:同轴度、对称度、位置度。定位误差:被测实际要素对一具有确定位置的理想要素的变动量,理想要素的位置由基准和理论正确尺寸确定。对于同轴度和对称度,理论正确尺寸为零。理论正确尺寸:确定被测要素的理想形状、方向、位置的尺寸。该尺寸不附带公差。理论正确尺寸是绝对准确 的尺寸,在图样上用方框围住。跳动公差:关联实际要素绕基准轴线回转一周或连续回转时所允许的最大跳动量。圆跳动:被测实际要素,绕基准轴线作无轴向移动回转一周时,由位置固定的指示器在给定方向上测得的最大与最小读数之差。圆跳动实质上是形状和位置误差在某一横截面上的综合反映。全跳动:被测实际要素绕基准作无轴向移动回转,同时指示器沿理想素线连续移动(或被测实际要素每回转一周,指示器沿理想素线作间断移动),由指示器在给定方向上测得的最大与最小读数之差。全跳动实质上是圆柱表面上形状和位置误差的综合反映。公差带:限制实际要素变动的区域。公差带包括形状、方向、位置和大小(公差值)四要素。公差带的主要形式有10种:①两平行直线;②两等距曲线;③两同心圆;④一个圆;⑤一个球;⑥一个圆柱;⑦一个四棱柱;⑧两同轴圆柱;⑨两平行平面;⑩两等距曲面几何图形:确定一组理想要素之间和(或)它们与基准之间正确几何关系的图形。公差原则:处理尺寸公差、形状公差和位置公差之间关系的原则。公差原则包括独立原则和相关原则。独立原则:图样上给定的形状公差与尺寸公差相互无关,分别满足要求的公差原则。在尺寸公差后无符号E 、在形状公差中无符号“0 M ”或“M ”时,即按独立原则处理形位公差与尺寸公差之间的关系。相关原则:图样上给定的形位公差与尺寸公差相互有关的公差原则。相关原则分为包容原则和最大实体原则两类。包容原则E0M:要求实际要素处处位于具有理想形状的包容面内的一种公差原则,而该理想形状的尺寸应为最大实体尺寸。尺寸公差后带符号E 、形位公差中带符号“0 M ”时,即按包容原则处理。最大实体原则M:被测要素或(和)基准要素偏离最大实体状态,而形状、定向、定位公差获得补偿值的一种公差原则。形位公差中带符号“M”时,即按最大实体原则处理。局部实际尺寸:在实际要素的任意正截面上,两测量点之间测得的距离。作用尺寸:在轴和孔配合时真正起作用的尺寸,即考虑了形位误差后真正起作用的尺寸。单一要素的作用尺寸:在结合面的全长上,与实际孔内接的最大理想轴的尺寸,称为孔的作用尺寸。在结合面的全长上,与实际轴外接最小理想孔的尺寸,称为轴的作用尺寸。关联要素的作用尺寸:在结合面的全长上,与实际孔内接的最大理想轴的尺寸,称为孔的关联作用尺寸,而该理想轴承必须与基准要素保持图样上给定的几何关系。在结合面的全长上,与实际轴外接的最小理想孔的尺寸,称为轴的关联作用尺寸,而该理想孔必须与基准保持图样上给定的几何关系。最大实体状态(MMC):实际要素在尺寸公差范围内具有材料量最多的状态。最大实体尺寸:实际要素在最大实际状态时的尺寸。对于孔类,最大实体尺寸是指最小极限尺寸,对于轴类,最大实体尺寸是指最大极限尺寸。最小实体状态(LMC):实际要素在尺寸公差范围内具有材料量最少的状态。最小实体尺寸:实际要素在最小实体状态时的尺寸。对于孔类,最小实体尺寸是指最大极限尺寸。对于轴类,最小实体尺寸是指最小极限尺寸。实效状态(VC):在尺寸公差和形位公差范围内实际要素的综合极限状态。单一要素的实效状态:由图样上给定的被测要素最大实体尺寸和该要素轴承线或中心平面的形状公差所形成的综合极限边界,该边界应具有理想状态。关联要素的实效状态:由图样上给定的被测要素最大实体尺寸和该要素的定向或定位公差所形成的综合极限边界,该极限边界应具有理想形状并应符合图样上给定的几何关系。实效尺寸:实效状态时的边界尺寸。实效尺寸是综合考虑尺寸公差和形状(位置)公差后的综合边界尺寸,是一个给定值。基准:即理想基准要素,它是确定要素几何关系的依据,分别称为基准点,基准直线(轴线)和基准平面(中心平面)单一基准要素:作为单一基准使用的单个要素。组合基准要素:作为单一基准使用的一组要素。三基面体系:由三个互相垂直的基准平面组成的基准体系,它的三个平面是确定和测量零件上各要素几何关系的起点。基准目标:为构成基准体系的各基准平面而在要素上指定的点、线、面。延伸公差带P:根据零件的功能要求,位置度和对称度公差带需延伸到被测要素的长度界限之外时,该公差带称延伸公差带。在尺寸前标符号P 。篇5:机械制图与检验技术教程-4.1检验方法
第四章、检验标准
第一节、检验方法
1、参考资料: MIL-STD-105E 使用说明. 2、本检验标准的相关品质标准,使用者可依项目,选定适当类别 : (1)金属件及其加工组成品质标准 . (2)喷油品质标准 . (3)包装材料品质标准 .3、注意事项 (1)本规范如与客户要求不同时,原则上以客户之检验标准,如客户提供之 检验规范或备注在客户注意事项内. (2)对模棱两可的缺失,虽经检验员初次误判为允收,但第二次检验发现属 缺失时,可判为定为不合格. (3)如各项品质标准所列为缺点时,后制程加工(如点焊,电镀等),完工后品 质缺点降低者,该缺点项目列为允收.4、作业规范 : (1)检验条件 : A、将待验品置于以下条件,作检验判定 . B、检验角度 : 成45度目视检试之 . C、检验距离 : 距物品30CM . D、检验光源 : 正常日光灯60W光源下检验 . E、检查半成品、成品之前应核对相关检验资料 . (2)抽样依据 A、“MIL-STD-105E”使用说明 . B、 一般检验水准为“Ⅱ”,机械制图与检验技术教程-4.1检验方法
, C、抽样计划 : 重缺点依 AQL : 1.0% 轻缺点依 AQL : 1.5%篇6:机械制图与检验技术教程-5.1检验方法
第五章、检验方法
第一节、披锋的检验方法
1、披锋的判定标准★ 机械制图教案
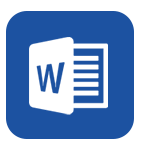
【机械制图与检验技术教程-1.3形状与位置公差(精选6篇)】相关文章:
浩辰CAD教程_CAD制图快速倒角2022-12-05
模具设计cad自荐信2023-01-25
《塑料制品》教案设计2023-06-15
绘制蚂蚱详解教程2022-05-04
简述网络教学的设计原则2022-09-20
机械制图标准-技术制图-明细栏2022-09-09
车工实习总结2023-01-19
机械设计基础课程设计心得体会2023-07-26
教学设计原则2023-05-19
教学设计的依据和原则探析2022-08-15