单端荧光灯的技术要求有哪些?(集锦8篇)由网友“噫嘻嘻”投稿提供,以下是小编帮大家整理后的单端荧光灯的技术要求有哪些?,供大家参考借鉴,希望可以帮助到您。
篇1:单端荧光灯的技术要求有哪些?
,
2 燃点h 后,其光通维持率不应低于82%。
3 产品中的汞含量小于等于10mg。
4 产品的寿命大于10000 小时。
5 塑料中阻燃剂不得使用多溴联苯(PBB)、多溴二苯酚(PBDE)和氯化酚。
篇2:单光头技术
采用一组镜头和一个激光发射器,利用快门技术来实现焦距的控制,这种技术类似于双透镜模式,只是通过电子的切换来实现焦距的变化,由于完全采用电子控制,因此速度比较快,
单光头技术
,
另外一种单光头技术采用了同一般的透镜不太一样的透镜,是一种不规则的透镜,通过光束照射部委不同样,发射出焦距不同光束来实现DVD和CD盘片的读取,这种技术的优点就是成本低,效率高。不过透镜更容易磨损,使用寿命短。
篇3:机械设计技术要求
1.零件去除氧化皮,
2.零件加工表面上,不应有划痕、擦伤等损伤零件表面的缺陷。
3.去除毛刺飞边。
4.经调质处理,HRC50~55。
5.零件进行高频淬火,350~370℃回火,HRC40~45。
6.渗碳深度0.3mm。
7.进行高温时效处理。
8.未注形状公差应符合GB1184-80的要求。
9.未注长度尺寸允许偏差±0.5mm。
10.铸件公差带对称于毛坯铸件基本尺寸配置。
11.未注圆角半径R5。
12.未注倒角均为2×45°。
13.锐角倒钝。
14.各密封件装配前必须浸透油。
15.装配滚动轴承允许采用机油加热进行热装,油的温度不得超过100℃。
20.齿轮装配后,齿面的接触斑点和侧隙应符合GB10095和GB11365的规定。
21.装配液压系统时允许使用密封填料或密封胶,但应防止进入系统中。
22.进入装配的零件及部件(包括外购件、外协件),均必须具有检验部门的合格证方能进行装配。
23.零件在装配前必须清理和清洗干净,不得有毛刺、飞边、氧化皮、锈蚀、切屑、油污、着色剂和灰尘等。
24.装配前应对零、部件的主要配合尺寸,特别是过盈配合尺寸及相关精度进行复查。
25.装配过程中零件不允许磕、碰、划伤和锈蚀。
26.螺钉、螺栓和螺母紧固时,严禁打击或使用不合适的旋具和扳手。紧固后螺钉槽、螺母和螺钉、螺栓头部不得损坏。
27.规定拧紧力矩要求的紧固件,必须采用力矩扳手,并按规定的拧紧力矩紧固。
28.同一零件用多件螺钉(螺栓)紧固时,各螺钉(螺栓)需交叉、对称、逐步、均匀拧紧。
29.圆锥销装配时应与孔应进行涂色检查,其接触率不应小于配合长度的60%,并应均匀分布。
30.平键与轴上键槽两侧面应均匀接触,其配合面不得有间隙。
31.花键装配同时接触的齿面数不少于2/3,接触率在键齿的长度和高度方向不得低于50%。
32.滑动配合的平键(或花键)装配后,相配件移动自如,不得有松紧不均现象。
33.粘接后应清除流出的多余粘接剂。
34.轴承外圈与开式轴承座及轴承盖的半圆孔不准有卡住现象。
35.轴承外圈与开式轴承座及轴承盖的半圆孔应接触良好,用涂色检查时,与轴承座在对称于中心线120°、与轴承盖在对称于中心线90°的范围内应均匀接触。在上述范围内用塞尺检查时,0.03mm的塞尺不得塞入外圈宽度的1/3。
36.轴承外圈装配后与定位端轴承盖端面应接触均匀。
37.滚动轴承装好后用手转动应灵活、平稳。
38.上下轴瓦的结合面要紧密贴和,用0.05mm塞尺检查不入。
39.用定位销固定轴瓦时,应在保证瓦口面和端面与相关轴承孔的开合面和端面包持平齐状态下钻铰、配销。销打入后不得松动。
40.球面轴承的轴承体与轴承座应均匀接触,用涂色法检查,其接触不应小于70%。
41.合金轴承衬表面成黄色时不准使用,在规定的接触角内不准有离核现象,在接触角外的离核面积不得大于非接触区总面积的10%。
42.齿轮(蜗轮)基准端面与轴肩(或定位套端面)应贴合,用0.05mm塞尺检查不入。并应保证齿轮基准端面与轴线的垂直度要求。
43.齿轮箱与盖的结合面应接触良好。
44.组装前严格检查并清除零件加工时残留的锐角、毛刺和异物。保证密封件装入时不被擦伤。
4
1.零件去除氧化皮。
2.零件加工表面上,不应有划痕、擦伤等损伤零件表面的缺陷。
3.去除毛刺飞边。
4.经调质处理,HRC50~55。
5.零件进行高频淬火,350~370℃回火,HRC40~45。
6.渗碳深度0.3mm。
7.进行高温时效处理。
8.未注形状公差应符合GB1184-80的要求。
9.未注长度尺寸允许偏差±0.5mm。
10.铸件公差带对称于毛坯铸件基本尺寸配置。
11.未注圆角半径R5。
12.未注倒角均为2×45°。
13.锐角倒钝。
14.各密封件装配前必须浸透油。
15.装配滚动轴承允许采用机油加热进行热装,油的温度不得超过100℃。
20.齿轮装配后,齿面的接触斑点和侧隙应符合GB10095和GB11365的规定。
21.装配液压系统时允许使用密封填料或密封胶,但应防止进入系统中。
22.进入装配的零件及部件(包括外购件、外协件),均必须具有检验部门的合格证方能进行装配。
23.零件在装配前必须清理和清洗干净,不得有毛刺、飞边、氧化皮、锈蚀、切屑、油污、着色剂和灰尘等。
24.装配前应对零、部件的主要配合尺寸,特别是过盈配合尺寸及相关精度进行复查。
25.装配过程中零件不允许磕、碰、划伤和锈蚀。
26.螺钉、螺栓和螺母紧固时,严禁打击或使用不合适的旋具和扳手。紧固后螺钉槽、螺母和螺钉、螺栓头部不得损坏。
27.规定拧紧力矩要求的紧固件,必须采用力矩扳手,并按规定的拧紧力矩紧固,
28.同一零件用多件螺钉(螺栓)紧固时,各螺钉(螺栓)需交叉、对称、逐步、均匀拧紧。
29.圆锥销装配时应与孔应进行涂色检查,其接触率不应小于配合长度的60%,并应均匀分布。
30.平键与轴上键槽两侧面应均匀接触,其配合面不得有间隙。
31.花键装配同时接触的齿面数不少于2/3,接触率在键齿的长度和高度方向不得低于50%。
32.滑动配合的平键(或花键)装配后,相配件移动自如,不得有松紧不均现象。
33.粘接后应清除流出的多余粘接剂。
34.轴承外圈与开式轴承座及轴承盖的半圆孔不准有卡住现象。
35.轴承外圈与开式轴承座及轴承盖的半圆孔应接触良好,用涂色检查时,与轴承座在对称于中心线120°、与轴承盖在对称于中心线90°的范围内应均匀接触。在上述范围内用塞尺检查时,0.03mm的塞尺不得塞入外圈宽度的1/3。
36.轴承外圈装配后与定位端轴承盖端面应接触均匀。
37.滚动轴承装好后用手转动应灵活、平稳。
38.上下轴瓦的结合面要紧密贴和,用0.05mm塞尺检查不入。
39.用定位销固定轴瓦时,应在保证瓦口面和端面与相关轴承孔的开合面和端面包持平齐状态下钻铰、配销。销打入后不得松动。
40.球面轴承的轴承体与轴承座应均匀接触,用涂色法检查,其接触不应小于70%。
41.合金轴承衬表面成黄色时不准使用,在规定的接触角内不准有离核现象,在接触角外的离核面积不得大于非接触区总面积的10%。
42.齿轮(蜗轮)基准端面与轴肩(或定位套端面)应贴合,用0.05mm塞尺检查不入。并应保证齿轮基准端面与轴线的垂直度要求。
43.齿轮箱与盖的结合面应接触良好。
44.组装前严格检查并清除零件加工时残留的锐角、毛刺和异物。保证密封件装入时不被擦伤。
4
5.铸件表面上不允许有冷隔、裂纹、缩孔和穿透性缺陷及严重的残缺类缺陷(如欠铸、机械损伤等)。
46.铸件应清理干净,不得有毛刺、飞边,非加工表明上的浇冒口应清理与铸件表面齐平。
47.铸件非加工表面上的铸字和标志应清晰可辨,位置和字体应符合图样要求。
48.铸件非加工表面的粗糙度,砂型铸造R,不大于50μm。
49.铸件应清除浇冒口、飞刺等。非加工表面上的浇冒口残留量要铲平、磨光,达到表面质量要求。
50.铸件上的型砂、芯砂和芯骨应清除干净。
51.铸件有倾斜的部位、其尺寸公差带应沿倾斜面对称配置。
52.铸件上的型砂、芯砂、芯骨、多肉、粘沙等应铲磨平整,清理干净。
53.对错型、凸台铸偏等应予以修正,达到圆滑过渡,一保证外观质量。
54.铸件非加工表面的皱褶,深度小于2mm,间距应大于100mm。
55.机器产品铸件的非加工表面均需喷丸处理或滚筒处理,达到清洁度Sa2 1/2级的要求。
56.铸件必须进行水韧处理。
57.铸件表面应平整,浇口、毛刺、粘砂等应清除干净。
58.铸件不允许存在有损于使用的冷隔、裂纹、孔洞等铸造缺陷。
59.所有需要进行涂装的钢铁制件表面在涂漆前,必须将铁锈、氧化皮、油脂、灰尘、泥土、盐和污物等除去。
60.除锈前,先用有机溶剂、碱液、乳化剂、蒸汽等除去钢铁制件表面的油脂、污垢。
61.经喷丸或手工除锈的待涂表面与涂底漆的时间间隔不得多于6h。
62.铆接件相互接触的表面,在连接前必须涂厚度为30~40μm防锈漆。搭接边缘应用油漆、腻子或粘接剂封闭。由于加工或焊接损坏的底漆,要重新涂装。
63.装配前所有的管子应去除管端飞边、毛刺并倒角。用压缩空气或其他方法清楚管子内壁附着的杂物和浮锈。
64.装配前,所有钢管(包括预制成型管路)都要进行脱脂、酸洗、中和、水洗及防锈处理。
65.装配时,对管夹、支座、法兰及接头等用螺纹连接固定的部位要拧紧,防止松动。
66.预制完成的管子焊接部位都要进行耐压试验。
67.配管接替或转运时,必须将管路分离口用胶布或塑料管堵封口,防止任何杂物进入,并拴标签。
68.补焊前必须将缺陷彻底清除,坡口面应修的平整圆滑,不得有尖角存在。
69.根据铸钢件缺陷情况,对补焊区缺陷可采用铲挖、磨削,炭弧气刨、气割或机械加工等方法清除。
70.补焊区及坡口周围20mm以内的粘砂、油、水、锈等脏物必须彻底清理。
71.在补焊的全过程中,铸钢件预热区的温度不得低于350°C。
72.在条件允许的情况下,尽可能在水平位置施焊。
73.补焊时,焊条不应做过大的横向摆动。
74.铸钢件表面堆焊接时,焊道间的重叠量不得小于焊道宽度的1/3。
75.每个钢锭的水口、冒口应有足够的切除量,一以保证锻件无缩孔和严重的偏折。
76.锻件应在有足够能力的锻压机上锻造成形,以保证锻件内部充分锻透。
77.锻件不允许有肉眼可见的裂纹、折叠和其他影响使用的外观缺陷。局部缺陷可以清除,但清理深度不得超过加工余量的75%,锻件非加工表面上的缺陷应清理干净并圆滑过渡。
78.锻件不允许存在白点、内部裂纹和残余缩孔。
81.精加工后的零件摆放时不得直接放在地面上,应采取必要的支撑、保
护措施。加工面不允许有锈蛀和影响性能、寿命或外观的磕碰、划伤等缺陷。
82.滚压精加工的表面,滚压后不得有脱皮现象。
83.最终工序热处理后的零件,表面不应有氧化皮。经过精加工的配合面、齿面不应有退火
84.加工的螺纹表面不允许有黑皮、磕碰、乱扣和毛刺等缺陷。
85、发蓝、变色的现象
篇4:机械设计技术要求
一、冲压件
1.锐边去毛刺,冲压切口粗糙度6.3.
2.冲件表面氧化处理:H.Y.或(表面镀锌钝彩.Zn8.DC.).
3.未注公差尺寸的极限偏差按GB/T 1804-92 m级.
二、铸件
1.铸件不得有气孔、夹渣、裂纹等缺陷.
2.未注明铸造斜度为1~2.5°.
3.铸造公差按GB6414-86 CT6.
4.未注明铸造圆角为R1~R2.5.
5.未注公差尺寸的极限偏差按GB/T 1804-92 m级.
6.未注形位公差按GB/T1184-96 H级.
7.去毛刺,未注倒角0.5x45°
三、锻件
1.未注锻造圆角半径为R1~R2.
2.未注锻造斜度为1~1.5°,锻造公差为IT15级.
3.锻件组织应致密,不得有折叠、裂纹等缺陷,并去飞边.
4.去锐边毛刺,直角处倒钝.
5.未注公差尺寸的极限偏差按GB/T 1804-92 m级.
6.未注形位公差按GB/T1184-96 H级.
四、活塞件
1.未注公差尺寸的极限偏差按GB/T 1804-92 m级.
2.未注形位公差按GB/T1184-96 H级.
3.去毛刺,未注倒角0.5x45°.
4.表面磷化处理.
五、橡胶件
1.零件表面应光洁.(模具表面粗糙度应在Ra0.4以上)且不允许有气泡.杂质级凸凹等缺陷.
2.合模缝不允许错位,合模飞边的凸起级厚度不得大于0.02mm.
3.邵氏A型硬度65%%P5.
4.去净飞边.
六、塑料件
1.成形前材料应预热干燥.
2.成形后制件应光整不得有扭曲变形现象.
3.未注圆角为R0.5.
4.外表面应光滑,其粗糙度不大于Ra0.4.且不得有划伤,刻痕等缺陷.
5.未注尺寸公差按GB/T 1804-92 m级.
七、弹簧件
1.旋向:左旋.
2.总圈数:no=12
3.工作圈数:no=10
4.钢丝硬度:HRC42~48.
5.表面氧化处理:H.Y.(俗称发黑)
6.单端并紧磨平.
一、冲压件1.锐边去毛刺,冲压切口粗糙度6.3.
2.冲件表面氧化处理:H.Y.或(表面镀锌钝彩.Zn8.DC.).
3.未注公差尺寸的极限偏差按GB/T 1804-92 m级.
二、铸件
1.铸件不得有气孔、夹渣、裂纹等缺陷.
2.未注明铸造斜度为1~2.5°.
3.铸造公差按GB6414-86 CT6.
4.未注明铸造圆角为R1~R2.5.
5.未注公差尺寸的极限偏差按GB/T 1804-92 m级.
6.未注形位公差按GB/T1184-96 H级.
7.去毛刺,未注倒角0.5x45°
三、锻件
1.未注锻造圆角半径为R1~R2.
2.未注锻造斜度为1~1.5°,锻造公差为IT15级.
3.锻件组织应致密,不得有折叠、裂纹等缺陷,并去飞边.
4.去锐边毛刺,直角处倒钝.
5.未注公差尺寸的极限偏差按GB/T 1804-92 m级.
6.未注形位公差按GB/T1184-96 H级.
四、活塞件
1.未注公差尺寸的极限偏差按GB/T 1804-92 m级.
2.未注形位公差按GB/T1184-96 H级.
3.去毛刺,未注倒角0.5x45°.
4.表面磷化处理.
五、橡胶件
1.零件表面应光洁.(模具表面粗糙度应在Ra0.4以上)且不允许有气泡.杂质级凸凹等缺陷.
2.合模缝不允许错位,合模飞边的凸起级厚度不得大于0.02mm.
3.邵氏A型硬度65%%P5.
4.去净飞边.
六、塑料件
1.成形前材料应预热干燥.
2.成形后制件应光整不得有扭曲变形现象.
3.未注圆角为R0.5.
4.外表面应光滑,其粗糙度不大于Ra0.4.且不得有划伤,刻痕等缺陷.
5.未注尺寸公差按GB/T 1804-92 m级.
七、弹簧件
1.旋向:左旋.
2.总圈数:no=12
3.工作圈数:no=10
4.钢丝硬度:HRC42~48.
5.表面氧化处理:H.Y.(俗称发黑)
6.单端并紧磨平.
基本技术要求汇总:一.一般技术要求:1、零件去除氧化皮,2014机械设计技术要求大全
,2、零件加工表面上,不应有划痕、擦伤等损伤零件表面的缺陷。3、去除毛刺飞边。二.热处理要求:1、经调质处理,HRC50~55。2、零件进行高频淬火,350~370℃回火,HRC40~45。3、渗碳深度0.3mm。4、进行高温时效处理。
三.公差要求:1、未注形状公差应符合GB1184-80的要求。2、未注长度尺寸允许偏差±0.5mm。3、铸件公差带对称于毛坯铸件基本尺寸配置。
四.零件棱角:1、未注圆角半径R5。2、未注倒角均为2×45°。3、锐角倒钝。
五.装配要求: 1、各密封件装配前必须浸透油。2、装配滚动轴承允许采用机油加热进行热装,油的温度不得超过100℃。3、齿轮箱装配后应按设计和工艺规定进行空载试验。试验时不应有冲击、噪声,温升和渗漏不得超过有关标准规定。4、齿轮装配后,齿面的接触斑点和侧隙应符合GB10095和GB11365的规定。5、装配液压系统时允许使用密封填料或密封胶,但应防止进入系统中。6、进入装配的零件及部件(包括外购件、外协件),均必须具有检验部门的合格证方能进行装配。7、零件在装配前必须清理和清洗干净,不得有毛刺、飞边、氧化皮、锈蚀、切屑、油污、着色剂和灰尘等。8、装配前应对零、部件的主要配合尺寸,特别是过盈配合尺寸及相关精度进行复查。9、装配过程中零件不允许磕、碰、划伤和锈蚀。10、 螺钉、螺栓和螺母紧固时,严禁打击或使用不合适的旋具和扳手。紧固后螺钉槽、螺母和螺钉、螺栓头部不得损坏。11、规定拧紧力矩要求的紧固件,必须采用力矩扳手,并按规定的拧紧力矩紧固。12、同一零件用多件螺钉(螺栓)紧固时,各螺钉(螺栓)需交叉、对称、逐步、均匀拧紧。13、圆锥销装配时应与孔应进行涂色检查,其接触率不应小于配合长度的60%,并应均匀分布。14、平键与轴上键槽两侧面应均匀接触,其配合面不得有间隙。15、花键装配同时接触的齿面数不少于2/3,接触率在键齿的长度和高度方向不得低于50%。
16、滑动配合的平键(或花键)装配后,相配件移动自如,不得有松紧不均现象。17、粘接后应清除流出的多余粘接剂。18、轴承外圈与开式轴承座及轴承盖的半圆孔不准有卡住现象。19、 轴承外圈与开式轴承座及轴承盖的半圆孔应接触良好,用涂色检查时,与轴承座在对称于中心线120°、与轴承盖在对称于中心线90°的范围内应均匀接触。在上述范围内用塞尺检查时,0.03mm的塞尺不得塞入外圈宽度的1/3。20、轴承外圈装配后与定位端轴承盖端面应接触均匀。21、滚动轴承装好后用手转动应灵活、平稳。22、上下轴瓦的结合面要紧密贴和,用0.05mm塞尺检查不入。23、用定位销固定轴瓦时,应在保证瓦口面和端面与相关轴承孔的开合面和端面包持平齐状态下钻铰、配销。销打入后不得松动。24、球面轴承的轴承体与轴承座应均匀接触,用涂色法检查,其接触不应小于70%。25、合金轴承衬表面成黄色时不准使用,在规定的接触角内不准有离核现象,在接触角外的离核面积不得大于非接触区总面积的10%。26、齿轮(蜗轮)基准端面与轴肩(或定位套端面)应贴合,用0.05mm塞尺检查不入。并应保证齿轮基准端面与轴线的垂直度要求。27、齿轮箱与盖的结合面应接触良好。28、组装前严格检查并清除零件加工时残留的锐角、毛刺和异物。保证密封件装入时不被擦伤。
六.铸件要求:1、铸件表面上不允许有冷隔、裂纹、缩孔和穿透性缺陷及严重的残缺类缺陷(如欠铸、机械损伤等)。2、铸件应清理干净,不得有毛刺、飞边,非加工表明上的浇冒口应清理与铸件表面齐平。3、铸件非加工表面上的铸字和标志应清晰可辨,位置和字体应符合图样要求。4、铸件非加工表面的粗糙度,砂型铸造R,不大于50μm。5、铸件应清除浇冒口、飞刺等。非加工表面上的浇冒口残留量要铲平、磨光,达到表面质量要求。6、铸件上的型砂、芯砂和芯骨应清除干净。7、铸件有倾斜的部位、其尺寸公差带应沿倾斜面对称配置。8、铸件上的型砂、芯砂、芯骨、多肉、粘沙等应铲磨平整,清理干净。9、对错型、凸台铸偏等应予以修正,达到圆滑过渡,一保证外观质量。10、铸件非加工表面的皱褶,深度小于2mm,间距应大于100mm。11、机器产品铸件的非加工表面均需喷丸处理或滚筒处理,达到清洁度Sa2 1/2级的要求。
12、铸件必须进行水韧处理。13、铸件表面应平整,浇口、毛刺、粘砂等应清除干净。14、铸件不允许存在有损于使用的冷隔、裂纹、孔洞等铸造缺陷。
七.涂装要求:1、所有需要进行涂装的钢铁制件表面在涂漆前,必须将铁锈、氧化皮、油脂、灰尘、泥土、盐和污物等除去。2、除锈前,先用有机溶剂、碱液、乳化剂、蒸汽等除去钢铁制件表面的油脂、污垢。3、经喷丸或手工除锈的待涂表面与涂底漆的时间间隔不得多于6h。4、铆接件相互接触的表面,在连接前必须涂厚度为30~40μm防锈漆。搭接边缘应用油漆、腻子或粘接剂封闭。由于加工或焊接损坏的底漆,要重新涂装。 八.配管要求:1、装配前所有的管子应去除管端飞边、毛刺并倒角。用压缩空气或其他方法清楚管子内壁附着的杂物和浮锈。2、装配前,所有钢管(包括预制成型管路)都要进行脱脂、酸洗、中和、水洗及防锈处理。3、装配时,对管夹、支座、法兰及接头等用螺纹连接固定的部位要拧紧,防止松动。4、预制完成的管子焊接部位都要进行耐压试验。5、配管接替或转运时,必须将管路分离口用胶布或塑料管堵封口,防止任何杂物进入,并拴标签。
九.补焊件要求:1、补焊前必须将缺陷彻底清除,坡口面应修的平整圆滑,不得有尖角存在。2、根据铸钢件缺陷情况,对补焊区缺陷可采用铲挖、磨削,炭弧气刨、气割或机械加工等方法清除。3、补焊区及坡口周围20mm以内的粘砂、油、水、锈等脏物必须彻底清理。4、在补焊的全过程中,铸钢件预热区的温度不得低于350°C。5、在条件允许的情况下,尽可能在水平位置施焊。6、补焊时,焊条不应做过大的横向摆动。7、铸钢件表面堆焊接时,焊道间的重叠量不得小于焊道宽度的1/3。
十.锻件要求:1、每个钢锭的水口、冒口应有足够的切除量,以保证锻件无缩孔和严重的偏折。2、锻件应在有足够能力的锻压机上锻造成形,以保证锻件内部充分锻透。3、锻件不允许有肉眼可见的裂纹、折叠和其他影响使用的外观缺陷。局部缺陷可以清除,但清理深度不得超过加工余量的75%,锻件非加工表面上的缺陷应清理干净并圆滑过渡。
4、锻件不允许存在白点、内部裂纹和残余缩孔。
十一.切削加工要求:1、零件应按工序检查、验收,在前道工序检查合格后,方可转入下道工序。2、加工后的零件不允许有毛刺。3、精加工后的零件摆放时不得直接放在地面上,应采取必要的支撑、保护措施。加工面不允许有锈蛀和影响性能、寿命或外观的磕碰、划伤等缺陷。4、滚压精加工的表面,滚压后不得有脱皮现象。5、最终工序热处理后的零件,表面不应有氧化皮。经过精加工的配合面、齿面不应有退火、发蓝、变色的现象。6、加工的螺纹表面不允许有黑皮、磕碰、乱扣和毛刺等缺陷。
篇5:接地线技术要求
接地线技术要求
目 录 List
1 目的和适用范围 ............................................................................................................................................ 2
1.1
1.2
2
3 目的 ........................................................................................................................................................ 2 适用范围 ................................................................................................................................................ 2 引用的相关标准 ............................................................................................................................................ 2 项目编码与建模命名 .................................................................................................................................... 2
3.1
3.2 项目编码 ................................................................................................................................................ 2 建模命名 ................................................................................................................................................ 3 4
5 功能描述 ........................................................................................................................................................ 3 要求 ................................................................................................................................................................ 3
5.1
5.2
5.3
5.4
5.5 结构和外形尺寸 .................................................................................................................................... 3 材料工艺 ................................................................................................................................................ 4 环保要求 ................................................................................................................................................ 5 防霉等级要求 ........................................................................................................................................ 5 其它技术指标 ........................................................................................................................................ 5 6
7 检验规则 ........................................................................................................................................................ 5 说明 ................................................................................................................................................................ 5
图目录 List of Figures
图1 接地线结构尺寸 ............................................................................................................................................ 4
1 目的和适用范围
1.1 目的
结构外购件技术要求是描述公司结构外购件的受控性文件,其作用为:
?
?
?
?
? 供应厂商进行产品设计、生产和检验的依据。 品质部门验货、退货的依据。 物料部门进行采购的依据。 对供应厂商产品质量进行技术认证的依据。 结构设计部门选用结构外购件的依据。
1.2 适用范围
本技术要求适用于接地线的选型、采购与检验。
2 引用的相关标准
下列文件中的条款通过本规范的引用而成为本规范的条款。凡是注日期的引用文件,其
随后所有的修改单(不包括勘误的内容)或修订版均不适用于本规范,然而,鼓励根据本规
范达成协议的各方研究是否可使用这些文件的最新版本。凡是不注日期的引用文件,其最新
版本适用于本规范。
GB2828 计数抽样检验程序
DKBA2332-.6 华为采购物料环保规范
DKBA3295.2- 电缆组件检验标准(第二部分:电缆组件物理机械性能检验标准)
3 项目编码与建模命名
3.1 项目编码
接地线由2个带绝缘套的OT端子和1根黄绿相间的.电力电子线缆组成(例如:6mm2接
地线由2个OT端子和1根电力电子线缆组成),属于外购件,由一级供应商采购,本身无单
独编码。
3.2 建模命名
目前公司使用的接地线有多种,具体的建模命名信息见表1(说明:L-线缆长度)。
表1 建模命名信息
4 功能描述
用于电子设备中各接地体间的连接。
5 要求
5.1 结构和外形尺寸
接地线的规格列表和零部件描述如表2所示,结构主要尺寸如图1所示,其中,接地线
长度L(mm)可根据需要选择。
表2 接地线规格列表及零部件描述
注:“L”为线缆长度,接地线两OT端子的中心距(实际安装长度)为:L+2C。如图1所示。
(a)实物
(b)尺寸要求
图1 接地线结构尺寸
5.2 材料工艺
材料:OT端子导体材质为紫铜(Copper)表面镀锡(Tin),绝缘体材质为PVC;电力电子
线缆导体材质为Stranded bare copper,绝缘体材质为PVC;
颜色:OT端子为银白色,绝缘体为黄色;如果为裸端子,则要求用热缩管包住,不露铜
-04-05 华为机密,未经许可不得扩散 Huawei Confidential 第4页,共
5页Page 4 , Total5
芯。电力电子线缆为黄绿相间,黄色为PANTONE 1235C,绿色为PANTONE 3268C, 黄绿比
例为6:4。
5.3 环保要求
满足“DKBA2332-2009.6 华为采购物料环保规范”的要求。
5.4 防霉等级要求
防霉等级要求满足GB/T 2423.16 1级要求。
5.5 其它技术指标
根据《DKBA3295.2-2003电缆组件检验标准(第二部分:电缆组件物理机械性能检验标
准)》规定,2.5 mm接地线组件的电缆最小拉拔力为225N,6mm接地线组件的电缆最小拉
拔力为350N,10mm接地线组件的电缆最小拉拔力为400N,16mm接地线组件的电缆最小拉拔
力为500N。 2222
6 检验规则
本检验规则适用于华为公司来料检验,其检验应符合华为技术有限公司质量部门的规
定。对于未规定的产品采用批次检验的方式,检验方法采用GB2828.1逐批检验中一次抽样
方案。
7 说明
1、本技术要求的解释权归华为技术有限公司配套产品线固网配套开发部。
2、供求双方有技术上的分歧时,以本技术要求作为仲裁。
2013-04-05 华为机密,未经许可不得扩散 Huawei Confidential 第5页,共5页Page 5 , Total5
篇6:技术要求承诺书
尊敬的xx用户:
xx技术服务部衷心的感谢您选择我公司的产品,并郑重向您承诺:我们将为您提供满意而周到的服务。
为了保证您的机器能够正常使用和得到良好的售后服务,请您仔细阅读本承诺书。
一、我公司对产品从出厂到产品的有效使用年限内实施全程跟踪管理体系,具体措施如下:
1、建立产品技术档案管理体系:
一机一档,具体包括产品组装验收合格登记、产品出厂状态、产品安装调试负责人、客户情况、技术负责人、使用培训及上岗证书、保修期、保质期及维护期的技术、质量状况的记载及分析解决过程记载,以及产品转移追踪记载等内容,以此确保每台已售出产品的质量保障工作。
2、售后服务保障制度体系:
1)设备安装与调试验收:
我公司免费派专业操作工程师负责对设备整体的`安装调试工作。
验收条件:乙方调机完毕,设备正常运转后,甲乙双方代表应对设备质量性能进行验收,验收合格且在验收报告上签字后开始计算保修期。
2)技术培训:
设备运抵后,免费为用户培训操作师2名(为期2天),我公司特编制专业技术培训教材,由专业技术培训工程师负责培训。
3)设立专家热线:
开通(010)60500081专家热线,随时解答用户在实际操作中出现的问题,为操作师正确操作提供可靠保证。
4)定期回访:
安装调试完毕后,三个月内售后技术服务工程师回访一次,听取客户意见,指导操作师正确使用并注意保养模切机;
第四个月至第十二月售后技术服务工程师不定期回访两次。
5)保修服务:乙方提供的保修期为开机调试合格后12个月或货到15个月,以先到者为准。
保修期内任何机组本身故障均由乙方负责维修和更换,费用由乙方负担。
响应时间:设备若发生故障,接到甲方报修电话,乙方应在24小时内提出解决方案,之后48小时内赶到现场(限国内市场)。
乙方在本地区有维修部维修工程师的,应4~6小时内赶到现场。
6)一年保修,三年质保,终身维护:
自购机之日起,我公司一年之内向用户提供免费调试(具体见合同第七款第7条)、维修及配件更换服务,但经专家鉴定属人为操作不当,非机械质量问题造成的事故,我公司将收取主要部件的成本费。
购机一年以后三年以内产品,我公司对发生故障的零部件只收取成本费,免收维修费;
自购机之日起三年以后,用户的设备出现一切故障,我公司将提供无偿的技术援助,并为用户提供有偿的维修服务,包括原厂配件更换。
7)保外服务:公司的维修中心将对用户提供有偿的终身维修,所需更换的部件以最优惠价格提供,用户也可就近与我公司设立的维修中心联系,公司的维修中心将建立用户的维修保养档案,定期向用户提供咨询服务。
8)例行维护:乙方提供一年不少于四次例行巡视,以协助甲方日常维护工作。
9)培训服务:提供现场培训(免费)、使用级培训、维护级培训。
包括:机组使用操作、日常维护保养、简单故障的判断及排除、机组原理等等。
二、本保障具有法律效力,不因本公司发展变更而失效;
三、公司以“胜利”品牌作为售后服务承诺的担保。
如您遇到问题或需要进一步的帮助,请与我们服务热线或传真联系。
xx印刷机械有限公司
技术服务中心
篇7:技术要求承诺书
在各级领导的关心支持下,经我公司积极申请,本公司总投资4000万元的电石炉尾气利用项目(见下表),于6月列入《石嘴山经济技术开发区循环化改造示范试点园区实施方案》(以下简称:《方案》),该《方案》于20XX年11月经国家发改委、财政部联合批准实施。
该项目的成功争取,对于我公司加快项目建设、实现资源高效循环利用、进一步发展壮大是千载难逢的机会。
本篇文章来自资料管理下载。
但由于经济大环境持续低迷、资金制约、发展规划调整等诸多因素的影响,该项目未能如期开工实施。
为了积极配合石嘴山经济技术开发区循环化改造总体工作的顺利进行,我公司郑重承诺:
一、尽快组织开工建设,合理统筹安排项目建设前期各项事宜,保证于20XX年9月1日前开工建设,逾期未开工建设,视为我公司自动退出石嘴山经济技术开发区循环化改造工作,主动放弃中央财政补助机会。
二、坚决维护《方案》的权威性,承诺切实按照《方案》中的项目建设内容进行建设。
如出现实际建设内容与《方案》中批复的建设内容不符的情况,视为我公司自动退出石嘴山经济技术开发区循环化改造工作,一切后果(包括法律责任)由我公司承担。
三、全力维护施工环境和秩序,在项目实施过程中,承诺切实组织好施工,不发生安全事故、拖欠农民工工资、违章施工等现象,由此引发的矛盾、问题及法律责任由我公司承担。
四、保证施工进度,我公司本着顾全大局的原则,承诺项目于6月30日前完工投产,待贵委及相关部门组织验收后,一次性享受国补资金支持,逾期未完工的我公司不要求任何补助。
五、工程开工后,我公司承诺积极配合相关部门搞好日常各项基础工作。
公司法人代表签字:
盖章:
201x年x月x日
篇8:技术要求承诺书
根据《中华人民共和国道路交通安全法》及其实施条例、《中华人民共和国计量法》及其实施细则、国家质检总局令第121号《机动车安全技术检验机构监督管理办法》等有关法律法规规定,为规范机动车安全技术检验活动,确保检测数据准确、可靠,本公司郑重承诺:
一、严格遵守《道路交通安全法》、《计量法》、《机动车安全技术检验机构监督管理办法》等相关法律、法规的规定,依法开展机动车安全技术检验活动,严格执行现行有效的检测标准和规范,保证检测数据准确、可靠,对检验结果负责,并承担因检验工作引发的法律责任。
二、严格执行机动车安全技术检验机构管理体系,完善检验工作各项规章制度,规范机动车安全技术检验行为,保证检验工作质量,提高检验服务水平。
三、加强对机动车安全性能检验设备的管理,配备符合《机动车运行安全技术条件》规定的全部检验设备,依法在用计量器具(检验设备)进行计量周期检定,确保检验设备正常完好。
四、严格在资格许可的检验范围内开展检验工作,不超范围开展检验业务。
五、加强机动车安全技术检验人员培训和内部管理,不断提高检验人员业务能力,保证所有检验人员持证上岗。
六、认真履行机动车安全技术检验机构义务,主动接受质量技术监督部门的检查、管理和社会的监督。
七、坚持诚信为本,牢固树立“质量第一,客户至上”的观念,提供热情、优质的服务。
安检机构名称:
安检机构承诺人:
安检机构监督电话:
监管部门监督电话:
★ 高速6位ADCs MAX155/MAX156的原理及应用
★ 项目节能措施简述
★ 节能措施
★ 书的新一代
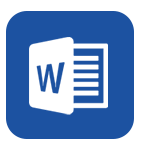
【单端荧光灯的技术要求有哪些?(集锦8篇)】相关文章:
基于TH71101的FSK/ASK数字接收电路设计2022-11-06
汽车开题报告2022-08-22
基于Rocket?I/O模块的高速工I/O设计2023-02-16
大学生数控机床实习报告2023-02-15
数控机床的实习报告2022-11-13
数控机床实习目的2022-08-04
大学数控机床实习报告2022-05-04
汽车销售开题报告2023-04-21
工作产出实训成果范文2022-07-21
工厂数控机床实习报告2022-05-30