PLC控制牵引机变频器启动停止的实现的论文(精选6篇)由网友“两肩霜月”投稿提供,下面是小编整理过的PLC控制牵引机变频器启动停止的实现的论文,欢迎您能喜欢,也请多多分享。
篇1:PLC控制牵引机变频器启动停止的实现的论文
PLC控制牵引机变频器启动停止的实现的论文
[摘要]本文首先分析牵引机的功能及动作循环过程,采用plc和伺服电动机作为控制方案;然后做出部件的电气原理图,分析需要控制的部件,根据需要控制的部件具体分析控制的相关部位,并确定出控制所需的输入、输出点数,由输入、输出点数选择plc的型号,分配输入、输出通道;接着设计系统的控制方式,由系统的控制方案设计出控制流程图;最后,完成程序设计的硬件连接和程序设计。
[关键词]控制水平连铸机 牵引机 变频器 伺服电动机 压轮 选型 预置
正文
在铸铜水平连铸生产线中,牵引机是水平连铸驱动系统的被控对象,其性能的好坏直接关系到整个连铸系统能否正常运转。本文将pcl应用于控制水平连铸机牵引机系统,以完成铸铜棒生产中最关键的一环――拉坯。
一、牵引机控制系统概述
牵引机是水平连铸技术的关键设备之一,必须实现精确并 可重复的运动,而且将这些运动丝毫不走样地传递给铸坯,因此它的工作特性直接影响着连铸的工艺水平,并影响着连铸坯的产品质量。
水平连铸牵引机控制系统由系统的控制装置、电动机、减速机、压轮、牵引轮和机座等组成。
水平连铸对牵引系统有两个方面的要求:工艺要求和设备要求。
二、牵引机控制系统功能说明
水平连铸牵引机控制系统的工作原理是:在开始时牵引机引锭杆堵住结晶器的出口,使铜水在结晶器内与引锭杆前端的引锭头凝结在一起。上牵引轮是被动轮,也叫压轮,起到压紧作用;下牵引轮作为主动轮与联轴器相连接,起到牵引作用。在保温炉结晶器中凝固成形的铸铜帮材,通过牵引轮的转动,靠摩擦力拉拔出来,铸坯向前运行。然后通过对下牵引轮的反推和牵引,以及反推牵引停顿凝固,制造出表面光滑、直径均匀的金属棒。根据水平连铸拉坯理论,牵引系统采用非连续的拉坯方式,具体的拉坯方式动作为推―停―拉―停。其中,设定每次反推时间为t1,推停时间为t2,引拉时间为t3,引停时间为t4。
根据铸铜凝固的特点及连铸生产的过程要求,牵引机拖动控制系统的功能可以归纳为以下两个方面。
1.速度给定控制
2.拉停比及周期控制
三、omron plc控制变频器控制系统的设计
水平连铸牵引机驱动控制系统采用的是开环控制方案。水平连铸牵引机伺服驱动控制系统的设备主要包括:plc、变频器、电动机、减速机和牵引辊等。
1.plc控制部分的设计
(1)plc型号的选择
plc、信号输入元件、输出执行器件和显示器件构成一个plc控制系统,其中输入/输出接口电路依据其电气性质的`不同又分为开关量、模拟量和数字量。plc控制系统的设计包括这些器件的选取和连接等。一个输入信号进入plc后在plc内部可以被多处使用,而且还可以获得其常开、常闭和延时等各种形式的触点,因此,信号输入器件只要有一个触点即可。对于输出器件而言,应尽量选取相同电源电压且工作电流较小的器件。
因此,该系统共有9个输入点,7个输出点,逻辑关系较为清楚,且输入/输出信号只有正转频率和反转频率输出为模拟量。应选用plc中的小型机,同时考虑留有一定的裕量。选用ormon cp1h型小型plc,它可以通过usb接口与上位机通信,采用梯形图配功能块的结构文本语言编程,多任务的编程模式,易于连网,拥有多路高速计数与多轴脉冲输出。选用cp1h-xa40dr-a。此plc输入/输出单元的具体规格是:输入点包括0通道0.00-0.11位共12点,1通道1.00-1.11位共12点;输出点包括100通道100.00-100.07位共8点,101通道101.00-101.07位共8点。此外,对于xa型的cp1h类型plc,其模拟量输出单元的主要功能是将指定的数字量转化为标准的电压信号或电流信号。
(2)plc编程软件
本设计使用7.3版本的cx-p作为开发软件,在离线状态下进行编程。
(3)plc的程序设计
铸铜水平连铸是一个典型的顺序控制系统,牵引机的两对相互平行的辊筒将型材以一定的牵引周期从保温炉中拉出,然后按照设定的牵引力方式进行循环牵引。
首先将自动/手动转换开关切换到自动运行状态,接着按下启动按钮置输入节点0.01为on,反转继电器w1.01动作,电动机启动,开始反推牵引,持续时间为t1,当达到设定的反推
间后,反推停止,继电器w3.01动作,电动机停止且持续时间t2;反推停止时间满足要求后,正转继电器w4.00动作,电动机开始正转牵引,时间为t3,当达到t3时,正转停止,继电器w4.01动作,电动机停止t4。引停阶段结束后,下一个循环继电器w2.05动作,进入新的牵引周期。如果牵引过程中按下暂停按钮,则牵引机直接停止工作;如果牵引过程中出现事故报警,则声光报警器报警,牵引机亦停止工作。
2.变频器的设计
(1)变频器的选型和预置
所选变频器为艾默生td3000系列变频器,输入端的标志为r、s、t,接电源进线;输出端的标志为u、v、w,接电动机;外接频率给定端ai1、ai3为0-+10伏的电压信号给定端;ai2为0-10v电压信号或0-20ma电流信号给定端;fwd为正转控制端,rev为反转控制端。
为了使变频器按照预先设计的方式进行工作,要对其进行控制方式预置,升降速功能预置,电动机铭牌数据输入及电动机自动测试功能预置。
(2)plc与变频器的连线
因为变频器在运行中会产生较强的电磁干扰,为保证plc不因为变频器主电路断路器及开关器件等产生的噪声而出现故障,将变频器与plc相连接时应该注意以下几个方面。
①同一操作柜中同时安装有变频器和plc时,应尽可能隔离开与变频器有关的电线和与plc有关的电线。
②当提供的电源稳定性不佳时,在plc的电源模块及输入/输出模块的电源线上接入噪声滤波器和降低噪声的专用变压器等,以保证plc获得可靠、稳定的供电电源。另外,为确保系统的稳健性,在变频器一侧有必要采取相应的措施。
③按规定的接线标准和接地条件对plc进行接地屏蔽处理,同时应注意避免使用使plc和变频器使用共同的接地线,且接地时对二者进行隔离处理。
④对提高抗噪声干扰的水平,建议在电气连接复杂的环境中使用屏蔽线和双绞线。
在此,只对plc和变频器进行简单的连线,完成本文中系统要求的基本功能,参照部分以上的原则,将选用cp1h-xa40dr-a和td3000变频器进行连接。
篇2:PLC实现变频调速器多电机控制论文
PLC实现变频调速器多电机控制论文
[摘要] 本文介绍了一种PLC与变频调速器构成的多分支通讯网络,阐明了该网络控制调速系统与一般模拟量控制调速系统相比的优越性,给出了系统框图及PLC程序。
[关键词] PLC 变频调速器 多电机控制 网络 通讯协议
一、引言
以变频调速器为调速控制器的同步控制系统、比例控制系统和同速系统等已广泛应用于冶金、机械、纺织、化工等行业。以比例控制系统为例,一般的系统构成如图1 所示。
600)this.width=600“ border=0>
工作时操作人员通过控制机(可为PLC或工业PC)设定比例运行参数,然后控制机通过D/A转换模件发出控制变频调速器的速度指令使各个变频调速器带动电机按一定的速度比例运转。此方案对电机数目不多,电机分布比较集中的应用系统较合适。但对于大规模生产自动线,一方面电机数目较多,另一方面电机分布距离较远。采用此控制方案时由于速度指令信号在长距离传输中的衰减和外界的干扰,使整个系统的工作稳定性和可靠性降低;同时大量D/A转换模件使系统成本增加。为此我们提出了PLC与变频调速器构成多分支通讯控制网络。该系统成本较低、信号传输距离远、抗干扰能力强,尤其适合远距离,多电机控制。
二、系统硬件构成
系统硬件结构如图2 所示,主要由下列组件构成;
600)this.width=600” border=0>
1、FX0N―24MR为PLC基本单元,执行系统及用户软件,是系统的核心。
2、FX0N―485ADP为FX0N系统PLC的通讯适配器,该模块的主要作用是在计算机―PLC通讯系统中作为子站接受计算机发给PLC的'信息或在多PLC构成n:n网络时作为网络适配器,一般只作为规定协议的收信单元使用。本文作者在分析其结构的基础上,将其作为通讯主站使用,完成变频调速器控制信号的发送。
3、FR―CU03为FR―A044系列比例调速器的计算机连接单元,符合RS―422/RS―485通讯规范,用于实现计算机与多台变频调速器的连网。通过该单元能够在网络上实现变频调速器的运行控制(如启动、停止、运行频率设定)、参数设定和状态监控等功能,是变频器的网络接口。
4、FR―A044变频调查器,实现电机调速。
在1:n(本文中为1:3)多分支通讯网络中,每个变频器为一个子站,每个子站均有一个站号,事先由参数设定单元设定。工作过程中,PLC通过FX0N―485ADP发有关命令信息后,各个子站均收到该信息,然后每个子站判断该信息的站号地址是否与本站站号一致。若一致则处理该信息并返回应答信息;若不一致则放弃该信息的处理,这样就保证了在网络上同时只有一个子站与主站交换信息。
三、软件设计
1、通讯协议
FR―CU03规定计算机与变频器的通讯过程如图3 所示,
600)this.width=600“ border=0>
该过程最多分5个阶段、计算机发出通讯请求;?、变频器处理等待;?、变频器作出应答;?、计算机处理等待;?、计算机作出应答。根据不同的通讯要求完成相应的过程,如写变频器启停控制命令时完成?~?三个过程;监视变频器运行频率时完成?~?五个过程。不论是写数据还是读数据,均有计算机发出请求,变频器只是被动接受请求并作出应答。每个阶段的数据格式均有差别。图4 分别为写变频器控制命令和变频器运行频率的数据格式。
600)this.width=600” border=0>
2、PLC编程
要实现对变频器的控制,必须对PLC进行编程,通过程序实现PLC与变频器信息交换的控制。PLC程序应完成FX0N―485ADP通讯适配器的初始化、控制命令字的组合、代码转换及变频器应答信息的处理等工作。PLC梯形图程序(部分程序)如图5 所示。
600)this.width=600" border=0>
程序中通讯发送缓冲区为D127~D149;接受缓冲区为D150~D160。电机1启动、停止分别由X0的上升、下降沿控制;电机2启动、停止分别由X1的上升、下降沿控制;电机3启动、停止分别由X2的上升、下降沿控制。程序由系统起始脉冲M8002初始化FX0N―485ADP的通讯协议;然后进行启动、停止信号的处理。以电机1启动为例,X0的上升沿M50吸合,变频器1的站号送入D130,运行命令字送入D135,ENQ、写运行命令的控制字和等待时间等由编程器事先写入D131、D132、D133;接着求校验和并送入D136、D137;最后置M8122允许RS指令发送控制信息到。变频器受到信号后立刻返回应答信息,此信息FX0N―485ADP收到后置M8132,PLC根据情况作出相应处理后结束程序。
四、结语
1、实际使用表明,该方案能够实现PLC通过网络对变频调速器的运行控制、参数设定和运行状态监控。
2、该系统最多可控制变频调速器32台,最大距离500m。
3、控制多台变频器,成本明显低于D/A控制方式。
4、随着变频器的增加,通讯延迟加大,系统响应速度低于D/A控制方式。
篇3:板坯连铸系统中PLC控制功能与技术实现论文
1 板坯连铸系统简介
以板坯连铸机生产工艺的特点为分级依据,可以把板坯连铸系统分为基础自动化系统以及过程控制计算机系统两级系统,其中一级为自动化系统,是运行基础;二级带有部分管理功能。基础自动化系统是一套完整的电/仪一体化系统,在系统运行中起着非常重要的作用,它能够完成各工艺装置的顺序控制以及相关操作,可以对工艺参数进行设置,还可以对工艺参数与设备状态进行显示与预警,对工艺流程进行监控。另外,其还有通信功能。过程控制计算机系统有质量跟踪、参数设定以及铸机的模型计算的功能。除此之外,对于网络的相关配置问题,通过 PLC 与上位机之间的信息转换与以太网相连接,利用 TCP/IP 协议完成数据转换。
篇4:板坯连铸系统中PLC控制功能与技术实现论文
2.1 大包回转台及中间罐车控制
一方面,对装有合格钢水的钢水包,一般要通过行车的吊运运至大包回转台的钢包臂上,此时包臂会运转到浇注位置等待浇铸。
另一方面,提前预热好的中间罐通过中间罐车运送至结晶器的上方,此时中间罐会下降以完成对中就位;在准备工作完成后,钢水罐开始下降,到达指定位置后就要手动开启滑动水口,随之钢水就会通过长水口流入中间罐,等到中间罐内的钢水质量达到指定要求后就需要人工开启中间罐塞棒,这时钢水就会通过侵入式水口流入结晶器内,从而完成这一工序。
2.2 送引锭、脱引锭控制
(1)送引锭:当送引锭指令发出后,引锭杆存放小车会向下反转运行,当引锭杆到达切割后辊道位置时四个对中缸将开始进行对中,随之切割前、切割下、切割后辊道自动运行,将引锭杆送至水平扇形段内。当引锭杆尾部离开 2# 光电管时,切割后辊道就会停止运行,当其到达 1# 光电管时,切割下及切割前辊道就会停止运行,随之辊道就会以 5 米/分的速度在扇形段内运行,与此同时解码器也开始对其进行跟踪记录,最后将引锭杆送入结晶器下口。(2)脱引锭:当引锭杆从扇形段出来达到 1# 光电管时,引锭头就会与铸坯分离,当引锭杆到达 2# 光电管时切割后辊道就会停止,随之引锭杆被移出。
2.3 火焰切割机自动切割控制
在自动状态下,红外定尺系统会给火焰切割机的 PLC 发出信号,火焰切割机只有在接收到信号时才会进行工作。首先,火焰切割机会先进行预压紧,与此同时切割枪开始运动,当切割枪运转至铸坯边缘时,预煤气阀以及热氧阀就会自动打开;当其运转到之前红外定尺系统所检测的定尺距离后,火焰切割机的压头开始下压随之切割氧与粒化水打开,进行切割工作。当切割枪到达切割下辊道边缘时,切下辊就会开始向下方摆动,一直等到切割枪离开切下辊,其才能够向上摆回到原位。
2.4 输送辊道及推钢机控制
输送辊道系统是由移载下线辊道、切割后辊道、切割下辊道以及切割前辊道这四道工序组成。在输送辊道系统运行过程中主要有五个具体步骤:(1) 火焰切割机在对钢坯切割完毕后发出切割完毕信号,随之切割后辊道开始正转;(2)在 2# 光电管检测到铸坯的情况下,移载下线辊道开始运作;(3)当铸坯尾部离开 2# 光电管时,之前运转的切割后辊道停止运作;(4)在 3# 光电管检测到铸坯的情况下,之前运行的移载下线辊道就会停止运作;(5)下线辊道运行停止时说明铸坯已成型,再利用推钢机把铸坯转移到冷床上进行冷却。
这样就可以科学的对铸坯进行生产。
篇5:板坯连铸系统中PLC控制功能与技术实现论文
3.1 变频调速控制技术
在现代板坯连铸系统中,变频调速控制技术已在各个设备中广泛应用;主要包括推钢机、火焰切割机、输送辊道、扇形段辊道、结晶器振动、中间罐车以及大包回转台等。一般来说,PLC 是通过 Re-mote I/O Scanner 通讯方式来把控制命令传输给变频器的,与此同时,变频器也将其实时状态反馈给 PLC 系统。另外,控制程序主要借助 MOV 指令来把速度、正反转以及启动停止命令以信息的形式传送给变频器,然后利用变频器的变频调速功能对整个系统进行自动控制。
3.2 铸流自动跟踪技术
铸流自动跟踪系统主要是利用物理上的光电转换原理进行工作的,通过增量式编码器来完成自动跟踪。增量式编码器可以直接利用光电转换原理来输出 A、B 以及 Z 相三组方波脉冲;其中,A、B两组方波脉冲的相位差为 90°,所以能够比较方便的判断出旋转方向;与此不同的 Z 相每转一个脉冲,所以其常应用与对基准点的科学准确定位。增量式编码器的技术含量较高,其平均寿命可达几万小时以上,而且其构造原理较为简单,抗干扰的能力较强,有较高的可靠性,比较适用于长距离的传输。一般来说,A-B 增量型编码器多安装在扇行段驱动辊的电机上,铸流 PLC 依据增量式编码器发送的脉冲数来自动计算并完成浇注模式、送引锭模式下的铸坯测长、电力测速以及二冷区配水等全自动控制。
3.3 大包下渣检测技术
大包下渣检测技术是用于检测包内钢水含渣量的.一项技术。这个系统主要通过高度自动化、智能化的平衡补偿技术并比较钢渣与钢水导电率来检测钢渣在钢水中的含量,其中还要用到电磁感应的物理原理来对含量进行检测,然后会通过声光报警的方式提醒相关操作者及时发出大包水口关闭信号或自己手动关闭大包滑动水口,以此来控制大中包中钢水的钢渣含量,进而提高钢水的清洁度,提升其质量;除此之外,还有效避免了繁琐的除渣工作,也可以提高钢坯质量。
3.4 液面自动控制技术
液面自动控制是通过涡流传感器来对拉坯及浇钢的速度进行调节的一项技术。一般来说,涡流传感器具有连续测量结晶器钢水液面的功能,它可以输出一系列模拟数据,一般包括随液面高度线性变化的电压以及电流,再把信息传送给液面调节系统,以此完成对拉坯以及浇钢速度的自动控制,使钢水液面得以稳定在预定高度。这样一来,就可以有效的提高连铸机的工作效率,提升其工作质量,防止溢钢及漏钢事故的发生,对钢坯的质量进行有效的保证。
3.5 红外定尺技术
所谓的红外定尺即是通过红外摄像的方式对钢坯进行相关数据识别。利用红外摄像设备对红热钢坯进行远距离实时成像,将所成图像转化为数字化信息,然后传送给 CPU,再利用 CPU 的计算与模糊识别功能对数字化信息进行相关计算与识别处理,再按照提前设定的定尺长度向 PLC 传送切割切割信号,使 PLC 控制火焰切割机对钢坯进行切割。这个系统的技术含量较高,一般具备操作维护简单、控制精度高以及检测可靠的特点,在钢坯处理中发挥非常重要的作用。
4 结束语
综上所述,在板坯连铸系统之中 PLC 控制的应用,对于准确、快速控制的实现,连铸自动化水平、铸坯质量与产量的提高具有非常重要的作用,而且能够降低能源消耗,降低机械故障的停机率,使得铸机的作业率得以有效提高,除此之外,还大大改善了工作环境,提高了工人的工作效率。因此,PLC 控制系统在板坯连铸系统之中值得推广应用。
参考文献
[1]黎华.PLC 在 4 号板坯连铸系统中的应用[J].柳钢科技,(1):23-24.
[2]冯科,韩志伟,毛敬华.连铸板坯质量控制的系统技术[J].钢铁技术,(5):7-9.
[3]杨立安,李涛.板坯连铸控制系统改造[J].科技传播,(1):134-135.
篇6:PLC实现高炉料流阀自修正控制的研究与应用的论文
关于PLC实现高炉料流阀自修正控制的研究与应用的论文
摘 要:高炉炉顶布料操作是现代高炉生产中重要的操作技术之一,根据现代化高炉生产的要求,高炉布料自动控制系统需要实现设备连锁控制、溜槽旋转类型控制、溜槽倾动角度控制、料溜阀开度控制、探尺升降控制等多项精确控制功能。本文主要介绍了高炉料流阀在多环布料时如何通过自修正程序实现炉内合理布料的研究与应用。
关键词:料流阀 多环布料 自修正
1 概述
目前,世界上大型高炉多采用无料钟炉顶,布料方式采用多环布料,通过溜槽调整炉料在炉喉的分布,达到煤气流分布合理,稳定炉况,提高煤气利用率,进而实现高炉稳产顺行。
实现合理的布料控制主要是对炉顶三个角度的稳定控制,布料溜槽倾动角α、布料溜槽旋转角β、料流阀开度γ,其中α、β可通过编码器检测、PLC程序及变频器控制实现角度的精确定位,因此,通过料流阀开度γ控制的布料圈数便成为了制约整个布料系统稳定性的关键因素。
2 料流阀开度控制原理
某钢厂1080m3高炉炉顶料流阀料流调节阀的打开和定位是由液压驱动的。通过电磁阀控制液压缸,料流调节阀的`开度由一个线性位置变送器检测。另外,设2个限位开关用来检测料流调节阀的打开和关闭位置。料流阀有三种控制模式,手动、手动定位、自动。
在自动模式下,PLC根据炉顶料单和槽下传送来的布料代号给出料流调节阀的设定开度,控制料流调节阀打开到设定开度开始布料,当接受到料罐清空信号,料流调节阀首先完全打开才能关闭。清空信号由γ射线检测和PLC的定时器共同完成;手动模式下,操作员直接通过监控画面按钮操作料流调节阀的打开,同样在关闭料流阀之前应将其完全打开;手动定位模式下,操作员首先将所需开度设定在监控画面的角度手动设定对话框中,然后点击监控画面中的手动设定按钮,则料流阀便会执行该设定角度,同样在关闭料流阀之前应将其完全打开。
料流调节阀的位置检测由一个内置在液压缸中的线性位置变送器来实现,输出4~20mA信号对应液压缸行程。为了使料流阀的定位精度达到±1mm的要求,在程序中对料流阀的开关速度进行处理,料流阀开始以最大速度30mm/s运动,当与目标位置相差较小时,以10mm/s速度运动,这样可以精确的定位到目标位置。
3 料流阀开度自修正控制
目前的高炉布料,特别是在大型无料钟炉顶高炉,主要的布料方式是多环布料。它实现了等面积布料,对稳定炉况、提高煤气利用、降低焦比起到了明显作用。合理布料能提高产量,有利于高炉顺行,降低燃料消耗。但是由于高炉布料的原料配比、质量、粒度变化频繁,难以保证布料圈数稳定[1]。
设定料批重为W吨,要求布料溜槽旋转N 圈后炉内矿石正好布料完成,炉内料线断面上沿高炉直径方向设定多个环位。布料操作时,根据不同料种、不同炉况要求,在高炉布料设定图(图1)中设定若干个环位布料。每个环位布满要求的圈数后,自动转到另一个环位上,直到N圈全部布完为止。为实现上述过程,对下料流量提出了较严格的控制要,不仅要求下料流量均匀,而且对应不同批重,不同料种要确定不同的下料流量,使溜槽转N圈后,料头、料尾相接,因此实现自动控制料流调节阀的开度是实现多环布料的关键[2]。
图1 高炉布料设定图
料流阀开度设定值的准确与否是能否保证多环布料圈数准确的重要前提。因此,在全自动布料时,根据料种、料重及前次布料的相关因素,合理地修正料流阀开度的设定值是非常必要的。
通过高炉开炉布料测试以及正常生产时得出的大量数据,得到料流阀自修正公式如下:
γ=γ0+(W-W0)*k/Wf
其中γ为本次布料料流阀开度目标值,
γ0为料流阀开度设定值,
W为本次布料矿石/焦炭实际称量值,
W0为工长料单设定矿石/焦炭理论称量值,
Wf为高炉理论允许最大称量值,
k为修正系数。
当本次布料圈数大于理想圈数时,则应增大料流阀开度目标值达到布料边缘修正,当本次布料圈数小于理想圈数时,则应减小料流阀开度目标值达到布料中心修正的目的。
公式中,γ为计算所得,γ0及W0为工长设定值,Wf在高炉设计完成后基本固定,如何得出k值则为本公式关键。
当高炉实际称量值W在理论允许最大称量值Wf范围内时,k值计算如下:
k=k0+(C-C0)/α
其中k为本次布料自修正系数,
k0为上次布料自修正系数,
C为上次布料实际圈数,
C0为布料理想圈数(一般是10),
α为布料料单中选定的倾动角度数量(一般是5)。
通过PLC编程实现以上自修正程序功能计算,在布料控制画面中将k值及γ目标值做成可人为修改,并增加自修正程序屏蔽按钮,可根据炉况随时转到人为干预,避免出现较大修正误差。
根据高炉开炉布料测试数据(表1),以及矿石、焦炭密度不同的原因,矿石及焦炭的自修正程序需分开运算。
表1 高炉布料测试记录
4 结语
高炉料流阀自修正程序投入使用后,能够基本满足
★ 电梯更换报告范文
★ 电梯实习证明
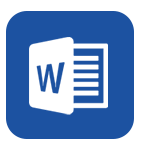
【PLC控制牵引机变频器启动停止的实现的论文(精选6篇)】相关文章:
基于ABCM的成本控制系统的设计论文2023-05-06
浅谈起重机变频控制系统的设计工学论文2023-05-27
维修电工技师论文2023-12-01
PLC教学论文2022-10-08
机械机电设备维护论文2023-09-13
PLC的普通机床数控化控制系统改造2023-04-11
电气自动化论文2022-11-09
汽车维修技师年度个人工作总结2023-08-04
浅谈PLC的特点及应用领域论文2023-03-18
关于自动化技术在消防工程中的运用论文2022-04-30