浅谈刀具涂层技术发展及应用(整理10篇)由网友“Baekhyun”投稿提供,下面是小编整理过的浅谈刀具涂层技术发展及应用,希望对大家有所帮助。
篇1:浅谈刀具涂层技术发展及应用
近30余年来,刀具涂层技术迅速发展,涂层刀具得到了广泛应用,1969年德国克虏伯(Krupp)公司和瑞典山特维克(Sandvik)公司研发成功了化学气相沉积(CVD)涂层技术,并向市场推出了CVDTiC涂层硬质合金刀片产品。20世纪70年代初,美国本夏(R.Runshan)和拉格胡南(A.Raghuran)研发了物理气相沉积(PVD)工艺,并于1981年将PVDTiN高速钢刀具产品推向市场。当时CVD涂层工艺温度约 1000℃,主要用于硬质合金刀具(刀片)的表面涂层;PVD涂层工艺温度为500℃和500℃以下,主要用于高速钢刀具的表面涂层。
后来,CVD和PVD涂层技术不断迅速发展,在涂层材料、涂层设备和工艺等方面都有了很大进步,而且发展了多层材料的涂覆技术,使涂层刀具(刀片)的使用性能有了很大的提高。PVD涂层技术过去主要用于高速钢刀具,而近年来随着PVD涂层技术飞跃发展,也成功用于硬质合金刀具(刀片),占领了硬质合金涂层刀具(刀片)的一半阵地。现在,涂层高速钢刀具和涂层硬质合金刀具(刀片)广泛应用,已占全部刀具使用总量的50%以上。
涂层刀具的优越性
在韧性较好的刀具(刀片)基体上进行表面涂层,涂覆具有高硬度、高耐磨性、耐高温材料的薄层(如TiN、TiC等),使刀具(刀片)具有全面、良好的综合性能。未涂层高速钢的硬度仅为62~68HRC(760~960HV),硬质合金的硬度仅为89~93.5HRA(1300~1850HV);而涂层后的表面硬度可达~3000HV以上。
①由于表面涂层材料具有很高的硬度和耐磨性,且耐高温。故与未涂层的刀具(刀片)相比,涂层刀具允许采用较高的切削速度,从而提高了切削加工效率;或能在相同的切削速度下,提高刀具寿命。
②由于涂层材料与被加工材料之间的摩擦系数较小,故涂层刀具(刀片)的切削力小于未涂层刀具(刀片)。
③用涂层刀具(刀片)加工,零件的已加工表面质量较好。
④由于涂层刀具(刀片)的综合性能良好,故涂层硬质合金刀片有较好的通用性,一种涂层硬质合金牌号的刀片具有较宽的使用范围。
刀具涂层技术的发展和进步
笔者多次参观了国际机床工具展览会,收集到很多资料,并听取了各大工具公司的技术报告,从而了解到刀具产品表面涂层技术的发展和进步。
CVD涂层技术的进展
过去,硬质合金刀具表面涂层采用高温化学气相沉积(HTCVD)工艺。在常压或负压的沉积系统中,将纯净的H2、CH4、N2、TiCl4、AlCl3、CO2等气体根据沉积物的成分,按一定配比均匀混和,依次涂到具备一定温度(一般为1000~1050℃)的硬质合金刀片表面,即在刀片表面沉积TiC、TiN、TiCN、Al2O3或者它们的复合涂层。直到现在,HTCVD仍是使用最多的工艺方法,除HTCVD外,还有等离子体化学气相沉积(PCVD)工艺,它是在硬质合金刀具(刀片)表面涂层的另一种方法,因这种涂层工艺温度较低(700~800℃),故刀片的抗弯强度降低。因为TiC与基体材料的线膨胀系数最接近,通常用TiC 薄层先涂在基体表面上,外面再涂TiN、Al2O3,如TiC/TiN、TiC/Al2O3、TiC/TiCN/TiN等。
后来,发展了各种不同组合的多层涂层。笔者在多次展览会上调查和统计了瑞典、德国、美国、日本、韩国、以色列和中国各公司的CVD涂层硬质合金刀片产品,涂层材料有以下组合:TiCN/Al2O3、TiCN/TiC/TiN、TiCN/TiC/Al2O3、TiCN/Al2O3/TiN、TiCN/TiC/Al2O3/TiN、TiCN/Al2O3/TiCN、 TiN,TiC/TiCN/TiN、TiN/TiCN/TiN等。可以看出,近年多用TiCN或TiN作底层,这是因为基体硬质合金有了改进,例如采用了梯度结构,才有可能用TiCN或TiN垫底。此外,TiN涂层不宜单独使用,因为与硬质合金相比,TiN的硬度提高不多,TiN必须与TiC、TiCN、 Al2O3等组合使用。
PVD涂层技术的进展
早期,PVD涂层均采用“真空蒸镀法”,膜层往往不均匀,与基体的结合不够牢固,后发展了“真空磁控溅射法”和“真空等离子镀工艺”,效果很好,
现在刀具表面涂层主要用后两种方法。
早年,PVD涂层只用于高速钢刀具,涂层材料几乎只用TiN一种。后来,改进了涂层工艺,发展了多种涂层材料和多层涂层,在硬质合金刀具上也得到了大量的应用。涂层效果比以往大有进步。TiN涂层材料仍在使用,新兴的涂层材料是TiAlN和AlTiN,其使用效果优于TiN。
欧洲的PVD涂层技术水平最高,领先于其他国家和地区。知名的厂商有欧瑞康巴尔查斯(OerlkonBalzers)公司、德国PVT等离子真空技术公司和丹麦尤尼莫克(Unimerco)公司等。他们的PVD涂层设备和工艺先进,涂层材料品种多,涂层刀具和其他产品使用性能好。
国外一些知名的高速钢和硬质合金工具厂,都有涂层刀具(刀片)产品,但涂层设备和工艺多购自涂层技术的专业公司,或与之合作,而不是自行研制。据悉,瑞典山特维克公司和以色列伊斯卡公司的PVD涂层设备都是从欧瑞康巴尔查斯公司购进的。中国也应当这样做,这是一条既好又快的道路。例如,中国哈尔滨第一工具厂和德国PVT公司合作,成立了哈一工普威特镀膜合资股份公司。欧瑞康巴尔查斯公司在全球设有77个涂层中心,在中国苏州、天津和汉江各设有一个中心,中国邻近城市和地区的工具厂家,其涂层产品多在上述中心进行涂层。湖南株洲硬质合金厂和四川自贡长城硬质合金厂的涂层设备都是从国外引进的。
CVD涂层新技术在超硬材料涂层方面的应用
利用“热丝CVD法”、“等离子体喷射CVD法”、“火焰燃烧法”等工艺能在硬质合金或高速钢刀具表面沉积金刚石薄膜(10μm)。CVD金刚石膜的力学、物理性能介于天然金刚石和热压聚晶PCD金刚石之间,能够有效地加工有色金属。
如增加沉积时间,可在基体或衬底(一般用硅片)上沉积出厚度大于0.5mm的厚膜。将厚膜从基体上剥离,并切割成一定形状的小块,再将小块钎焊在基体刀片(一般为硬质合金刀具)上使用。CVD厚膜金刚石刀具应用范围大于薄膜涂层刀具。在CIMT上,很多国内外刀具公司都有CVD薄膜金刚石涂层刀具产品,但只有少数厂家有厚膜产品。北京东方天地超硬材料工具公司能生产金刚石厚膜刀具产品,并且已有多年的经验。厚膜刀具应用范围较广,能加工各种有色金属、非金属硬材料及颗粒增强的复合材料等。
PVD涂层新技术在超硬材料涂层方面的应用
武汉大学物理系用直流反应磁控溅射法在刀具表面沉积出氮化碳(CxNy)超硬涂层薄膜,厚度只有几个微米,硬度可达40~50GPa.CxNy涂层刀具能切削黑色和有色金属。
实验数据
笔者对涂层高速钢和硬质合金刀具(刀片)的切削性能进行了长期的研究,进行了很多科学实验。兹介绍部分实验数据如下:
①在相同的切削条件下,涂层刀具刀片的使用寿命比未涂层刀具(刀片)提高3~5倍。在相同的切削条件下,相同刀具寿命时,涂层刀具的切削速度比未涂层刀具提高20~30%.
②在相同的切削条件下,涂层刀具(刀片)的切削力小于未涂层者。笔者用涂覆TiC硬质合金刀片车削钢材与未涂层刀片对比,主切削力Fc可减小3%~4%,TiN或TiC/TiN涂层刀片的Fc约可减小6%,进给力Ff与切深力Fp的减小尤为显着。Al2O3涂层刀片与切削力的减小效果与TiN涂层刀片接近。
③笔者曾用CVD涂层金刚石厚膜刀具,加工过硅铝合金、各种硬铝、铅黄铜、无氧铜、碘化钛以及纤维增强和颗粒增强的复合材料等,均取得较好效果。但用作超精密切削的刀具,其效果不如天然金刚石刀具。
④笔者曾用CxNy涂层高速钢钻头在高强度钢上钻孔,与未涂层钻头相比,涂层钻头的使用寿命提高7~9倍。在其他高速钢刀具上涂覆CxNy,亦有显着效果。又曾在硬质合金刀片上涂覆CxNy,用以车削钢料,效果尚不够理想,其使用寿命不超过普通TiC涂层硬质合金刀片。
中国的刀具涂层技术与工业发达国家相比尚有很大差距,涂层刀具的数量也差得很远,大致只占全部刀具的20%.其中数控机床和加工中心上使用得多一些,在普通的非数控机床上则少得可怜,原因是认识问题和价格等因素。我们应该努力提高刀具涂层技术和应用技术的水平,大力推广应用涂层刀具,促进切削加工和机械制造水平的提高。
篇2:刀具涂层技术的进展和应用
刀具涂层技术的进展和应用
切削刀具材料不仅需要有很高的硬度和耐磨性,而且需要有较好的抗弯强度和冲击韧性.这两方面的性能相互矛盾,难以兼顾.在刀具表面敷以涂层,是解决这一矛盾的'有效方法.
作 者:于启勋 张京英 作者单位:北京理工大学机械与车辆工程学院 刊 名:航空制造技术 ISTIC英文刊名:AERONAUTICAL MANUFACTURING TECHNOLOGY 年,卷(期):2007 “”(7) 分类号:V2 关键词:篇3:特种加工技术发展及其应用
关键词:技术特点;技术种类;发展趋势
一、概述
传统的机械加工技术对推动人类的进步和社会的发展起到了重大的作用。随着科学技术的迅速发展,新型工程材料不断涌现和被采用,工件的复杂程度以及加工精度的要求越来越高,对机械制造工艺技术提出了更高的要求。
二、特种加工技术的特点
(一)加工范围上不受材料强度、硬度等限制。特种加工技术主要不依靠机械力和机械能去除材料,而是主要用其他能量(如电、化学、光、声、热等)去除金属和非金属材料,完成工件的加工。故可以加工各种超强硬材料、高脆性及热敏材料以及特殊的金属和非金属材料。
(二)以柔克刚。特种加工不一定需要工具,有的虽使用工具,但与工件不接触,加工过程中工具和工件间不存在明显的强大机械切削力,所以加工时不受工件的强度和硬度的制约,在加工超硬脆材料和精密微细零件、薄壁元件、弹性元件时,工具硬度可以低于被加工材料的硬度。
(三)加工方法日新月异,向精密加工方向发展。当前已出现了精密特种加工,许多特种加工方法同时又是精密加工方法、微细加工方法,如电子束加工、离子束加工、激光束加工等就是精密特种加工:精密电火花加工的加工精密度可达微米级0.5~1u m,表面粗糙度可达镜面Ra0.021.1m。
(四)容易获得良好的表面质量。由于在加工过程中不产生宏观切屑,工件表面不会产生强烈的弹、塑性变形,故可以获得良好的表面粗糙度。残余应力、热应力、冷作硬化、热影响区及毛刺等表面缺陷均比机械切割表面小,尺寸稳定性好,不存在加工中的机械应变或大面积的热应变。特种加工的主要应用范围有
1.加工各种难切削材料。如硬质合金、钛、合金、耐热钢、不锈钢、淬硬钢、金刚石、红宝石、石英以及锗、硅等各种高硬度、高强度、高韧性、高熔点的金属及非金属材料。
2.加工各种特殊复杂零件的三维型腔、型孔、群孔和窄缝等。如发动机机匣、整体锅轮、锻压模和注射模的立体成型表面,各种冲模、冷拔模上特殊断面的型孔,炮管内膛线,喷油嘴、栅网、喷丝头上的小孔、窄缝等。
3.加工各种超精、光整或具有特殊要求的零件。如对表面质量和精度要求很高的航天航空陀螺仪、阀,以及细长轴、薄壁零件、弹性元件等低刚度零件的加工,有些方法还可用于纳米级加工。
4.以高能量密度束流实现焊接、切割、制孔、喷涂、表面改性、刻蚀和精细。
三、特种加工技术的种类
特种加工技术所包含的范围非常广,随着科学技术的发展,特种加工技术的内容也不断丰富。
(一)电火花加工
电火花加工又称作电蚀加工或放电加工,是将工具电极和工件置于绝缘的工作液中,工件和工具分别接直流脉冲电源正极和负极,加上电压,利用工具电极和工件电极间脉冲放电时产生的电蚀现象对材料毛坯进行加工。
(二)电化学加工
电化学加工是通过电化学反应去除工件材料或在其上镀覆金属材料等的特种加工。该方法主要包括电解、电镀、电铸、电化学抛光等工艺方法。
(三)高能束流加工
高能束流加工也称为三束流加工,是利用能量密度很高的激光束、电子束或离子束等去除工件材料的特种加工方法的总称。其中电子束加工技术改变了原有的设计思想,可将原有的`高精度复杂难加工型面或无法加工的大型整体零件分成若干个易加工的单元,精加工和热处理以后,用电子束将其焊接成整体零件。
(四)物料切蚀加工
物料切蚀加工包括超声波加工与水喷射加工、磨料喷射加工、磨料流动加工。是指利用流体、磨料,流体与磨料的混合液等动能,去冲击、抛磨、浸蚀工件被加工部位而实现去除工件材料的方法。
(五)复合加工
复合加工是指用多种能源组合进行材料去除的工艺方法,大多是在机械加工的同时应用流体力学、化学、光学、电磁学和声波等能源进行综合加工,这些加工方法能够提高加工效率或获得很高的尺寸精度、形状精度和完整的表面。
四、特种加工技术的发展趋势
(一)采用自动化技术充分利用计算机技术对特种加工设备的控制系统、电源系统进行优化,建立综合参数自适应系统、数据库等,进而建立特种加工的cAD/cAM和FMS系统,这是当前特种加工技术的主要发展趋势。
(二)向工程化和产业化方向发展不断改进、提高高能束源品质,对大功率、高可靠性、多功能、智能化加工设备的研发是今后的重点发展方向。
(三)着力开展精密化研究高新技术的发展促使高新技术产品向超精密化与小型化方向发展,正向亚微米级和纳米级迈进,对产品零件的精度与表面粗糙度提出更严格的要求。
(四)污染问题是影Ⅱ自和限制某些特种加工应用、发展的严重障碍,加工过程中产生的废渣、废气如果排放不当,会造成环境污染,影响工人健康。必须花大力气处理并利用废气、废渣、废液,向“绿色”加工的方向发展。
五、结束语
现代特种加工技术主要是伴着高硬度、高强度、高韧性、高脆性等难切削材料的额出现,以及制造精密细小、形状复杂和结构特殊的零件的需要而产生的,具有其他常规加工技术无法比拟的优点,已成为航空航天、汽车、仪器仪表、微型机械、轻工、模具等行业的支撑技术和关键技术。
随着科学技术和现代工业的发展,特种加工技术必将不断完善和迅速发展,反过来又必将推动科学技术和现代工业的发展,并发挥越来越重要的作用。
参考文献:
[1]刘振辉,杨嘉楷.特种加工[M].重庆:重庆大学出版社,.
[2]刘晋春,赵家齐,赵万生.特种加工[M].北京:机械工业出版社,.
[3]孔庆华.特种加工[M].上海:同济大学出版社,.
[4]白基成,郭永丰,刘晋春.特种加工技术[M].哈尔滨:哈尔滨工业大学出版社,.
[5]张纹,蒋维波.特种加工技术的应用与发展趋势[J].农业装备技术,2006,(3).
篇4:卫星通信的技术发展及应用
一、卫星通信技术的概述
卫星通信简单地说就是地球上的无线电通信站利用卫星作为中继而进行的通信。
卫星通信体统包括两部分,分别是卫星以及地球站。
使用卫星通信的特点就是通讯的范围较大,只要是卫星发射的电波覆盖的地方就可以进行任意两点的通信;还有就是可靠性较高,不容易受到陆地灾害的影响;电路开通迅速,只要设置一个地面接收装置就可以进行卫星通信;以及卫星通信的电路设置灵活,可以随时的分散过于集中的信息等等。
目前,卫星通信系统中主要有移动业务的卫星系统、固定业务的卫星系统以及广播业务的通信系统,它们的组成是不完全相同的。
固定卫星又称静止地球轨道卫星,轨道高度大约在36000km,呈圆形分布,只需要三颗就可以达到覆盖全球的效果,且这三颗相隔的角度在120度,在这一种卫星系统中发展最好的就是intelsat 1-1X代卫星,该卫星已经发展到了第九代,在全球覆盖性能上表现得最突出;移动卫星通信它既有全球性也有地域性的,在全球性中采用的是中、低轨道,区域性的采用的是静止轨道通信。
二、卫星通信技术的发展
(一)通信技术的发展。
人类是一个群居性的物种,所以,人类之间存在着一定的联系,这样就需要采取一定的措施进行通信,人类的通信历史是悠久的。
在远古的时候,人们可以通过一些简单的壁画或者语言等方式进行信息的交换。
然后当人类文明发展到一定阶段后,人们开始利用烽火、飞鸽、驿马邮递、语言、竹简、书纸等进行简单地通讯,这些通讯一般都是通过视觉和听觉来传给人们的。
直到19世纪中期的时候,人们发现了电磁理论,人们的通讯开始发生了重大的改变,实现了利用金属导线就可以进行远距离的传输信息,甚至于到后来利用电磁波进行无线通讯。
人们首先发明了电报机、电话机等,但是随着科学技术的进步,以及在这些通讯中遇到的问题就又发展出了卫星通讯技术。
(二)卫星通信技术在国外的发展。
在最近的十几年间,由于经济以及科学技术的快速发展,国外的卫星通信技术无论是在军事领域还是在商业上都有了很大的进步,大量的新型的质量较高的、寿命较长的以及功率更大的卫星不断升空。
目前世界上比较先进的卫星通信技术仍然被洛马、波音、休斯等欧美实力雄厚的卫星制造商所掌握。
目前在通信卫星领域中最发达的还属美国,它的卫星发展计划已经经过了长时间的发展,已经在商业以及军事上都有了一些列的卫星产品,目前其通信卫星计划主要有美国国防部的转型卫星通信系统计划,先进极高频的卫星计划等等。
欧洲的国家也为了积极的提高自己在卫星通信领域中的分量,不断的公布新的卫星通讯计划,欧空局计划要不断地提高大功率卫星的占有率,这标志着欧洲通信卫星向着大功率方向不断发展。
(三)国内卫星通信技术的发展。
近年来,随着我国改革开放不断深入,经济与科技快速的发展,现代的小卫星技术取得了长足的发展,这就对卫星技术有了进一步更高的要求,国内的一些科技公司以及一些大中院校都加入到了对卫星技术研究的行列,并且取得了明显的成果,例如,编队卫星的跟踪切换技术以及激光终端机等等都已经得到了很好的解决,但是还有很多方面还是与国外发达国家有很大的差距。
三、卫星通信技术的应用
(一)卫星通信技术在广播电视领域中的应用。
我国是一个人口众多的国家,由于人口的基数较大,这就导致我国电视机拥有量达到3.5亿台,并且我国还有数千家各种各样的电视媒体机构,有线电视的用户量也已经达到9000万户。
我国的电视节目虽然数量众多,但是规模偏小,是处于发展的前期,潜力巨大。
我国各类电视数目虽然较多,但是供于村村通的节目也就44套,而且我国单收设备也就才百万多台,和美国相比,虽然他们人口基数只有两亿但是人家的有线电视用户量已经达到了6000万户,卫星电视直播的用户也有近2000万。
虽然我国现在处于发展阶段,和一些发达国家相比有很大的差距,但是随着我国发展的不断深入,我国一定也会达到、甚至超过这样的水平,所以我国卫星通信技术在电视广播领域中的应用的前景是巨大的。
目前,我国政府以及一些电视领域中的专家普遍表示我国发展卫星电视直播的业务已经成熟,我国已经获得了发展DBs的轨位和频道,而且我国在发展村村通的时候又有了一定的卫星广播的经验,并且得到了广大人民的支持,现在我国自行研制的RD已经进入市场。
在不久的将来我国将通过卫星传输和广播的电视会进一步的覆盖更多的人,数百套的电视节目可以任由普通民众来选择。
(二)卫星通信技术在计算机网络领域中的应用。
卫星通讯技术在计算机网络中的应用主要就是提供宽带网络。
而提供网络宽带属于卫星固定通信业务。
目前国际上卫星宽带业务发展主要体现在两个方面,第一就是在原有的VSAT技术的基础上研发新的产品并利用现有的频段卫星资源,快速的建立起宽带连接,以满足用户的需求,这一种是在和地面宽带业务的竞争中来获得自己的生存空间;而另外一种是积极的发展高频段的新型卫星宽带通信系统,来适应新业务的要求,这一种是和地面相辅相成的。
我国目前的状况,就是首先要积极的发展卫星宽带通信业务,国内的电信经营商应该根据不同客户的需求提供不同的业务;其次就是跟踪国外再见的新型的卫星宽带通信系统;最后建立起自己的卫星宽带通信系统。
四、结语:
综上所述,随着时代的发展,经济与科学技术得到了长足的发展,人们为了享受更加舒适的环境,对通信领域提出了更高的要求,原有的通信慢慢的不能满足人们的要求,而新出现的卫星通信技术由于具有良好的特性得到了人们的亲睐,世界各国都在积极的发展卫星通信技术。
本文就主要的讲述了卫星通信技术的'发展以及在一些领域中的应用,希望能够推动卫星通信技术知识的普及,为卫星通信发展奠定知识基础。
参考文献:
【1】熊群力,姜康林.航天编队飞行星座的星间通信[J].无线电通信技术. (01)
【2】林来兴.发展我国小卫星星座和测控技术.飞行器测控学报[J].才智.(10)
篇5:卫星通信的技术发展及应用
摘 要:本文介绍了卫星通信的基本概念及相关技术,重点介绍卫星通信技术在中海油应用领域上的发展以及小站卫星通信方式的应用。
关键词:卫星通信;海上石油卫星;VSAT;自动跟踪
0 引言
20世纪90年代初,从中海油开始建立第一个卫星端站至今,已经有超过的卫星通信技术应用。
目前,已经形成了以湛江、天津、深圳、上海这4个中心站点为核心的网状网络,且已经具备了链路相互备份功能。
1 卫星通信在中海油的发展
1.1 TES卫星系统
TES(TelephonyEarthStation)是基于卫星的全数字话音和数据通信的网状网,它在多个地球站之间提供网状连接,支持系统内任意地点远端站之间的电话、同步、异步数据通信,TES系统在中海油的应用主要用于话音与数据传输。
运用的是C波段卫星的频分多址方式FDMA实现与地面站间的通信,使用四相相移键控QPSK或二相相移键控BPSK调制方式,信道编码采用编码效率为1/2或3/4的前向纠错FEC。
TES是中海油海上平台初期使用的一种主要的卫星通信方式,主要承载的业务为话音业务,所使用的卫星资源前期以亚洲3号卫星为主,后来转至鑫诺1号卫星。
1.2 VSAT卫星系统
篇6:软件工程技术发展及应用论文
软件工程技术发展及应用论文
【摘 要】软件工程是一门研究用工程化方法构建和维护有效的、实用的和高质量的软件的新兴学科。它涉及程序设计语言、数据库、软件开发工具、系统平台、标准、设计模式等方面。随着现代信息化不断的发展与进步,软件工作作为一门新兴学科已经广泛渗透到各个领域,在现代社会中,软件应用于多个方面,这些应用促进了经济和社会的发展,也提高了工作效率和生活效率 。这门学科在计算机技术的发展与应用中起到了关键的作用,为现如今强大的计算机信息技术奠定了夯实的基础。
【关键词】软件工程;程序编写;软件模型
软件工程技术的发展经历了30年的发展时间,经历了多次的改革与发展,每一次改革与发展的着重对象和发展进度都在不断变化中。现如今,计算机基础正朝着高科技、现代化、信息化的层面不断发展,传统的软件工程技术在质量和效率上已经不能满足人们的需求,软件开发局面必须要向更加全面、系统、深刻的方向发展,才能适应现代的计算机软件开发市场。
1.软件工程技术的发展历程
它的发展过程分为了三个阶段,程序设计阶段、软件设计阶段、软件工程阶段,第一个阶段就仅仅是没有软件的概念,只是围绕计算机开发出规模较小的程序内容,只是简单的程序编制。第二个阶段开始出现“软件作坊”,软件开发环境相对成熟,技术开发人员逐渐意识到开发出更加全面、系统、深刻的软件工程才能满足现阶段人们对软件工程技术的需要。第三个阶段中,由于开发软件需要大量的人力和资源,投资的费用巨大,但是其软件技术的实用性却不能得到保证,落后的生产方式无法满足迅速增长的,从而导致与维护过程中出现一系列严重问题的现象,此阶段出现了严重的“软件危机”,开发人员深刻的认识到了得不断的研究和改变开发的技术手段和管理方法,才能开发出统一、规范的软件工程。这个开发阶段成就了现如今软件工程的基础理论思想,为软件工程基础的完善构造了基本框架。
2.软件工程技术的概述
就软件工程而言,主要就是借鉴传统软件工程技术的原则和方法来开发出高质量的软件,软件工程现阶段的要求就是应需而生,其本质就是对物理空间中的行为模式,进行逻辑的抽象。首先要研究软件的元素和结构模型,实现“高层概念”到“低层概念”的映射,其中应用了计算机科学、数学和管理科学。计算机科学和数学用于构造模型与算法,工程科学用于制定规范、设计范型、评估成本及确定权衡,管理科学用于计划、资源、质量和成本的管理。软件开发的模型是软件开发的全过程、活动 、任务的'结构框架 ,早期的瀑布式开发模型的作用就是告诉人们需要做什么,经过不断的发展,到后来的螺旋模型让人们在开发软件时引入了其他模型不具备的风险分析,它兼顾了快速原型的迭代特征以及瀑布模型的系统化与严格监控。每个模式都展示了在不同时代软件产业对软件开发不同的认识,不可否认的是,每个软件模型都有自己的有点,越到成熟时期的软件模型更加趋于完善。但是要根据开发软件的实际情况来使用软件模型。
3.软件工程应用的实施
在实际的开发应用中,主要通过几个步骤来完成应用实施,首先要制定计划,确定软件目标,选择实施方案,弄清项目开发的限制条件;其次进行风险分析,分析评估所选的 方案,考虑如何识别和消除风险;其次是进行实施,实施软件开发和验证;最后提出评估,提出修正建议,指定下一步计划。
3.1软件开发的制定
必须提供一个基本框架,合理的估算出软件开发项目所需的成本,资源和开发进度,并制定软件项目开发的过程,按照过程有序进行,在做计划时,必须就需要的人力、项目持续时间及成本作出估算,此估算需按照历史估算的成本做参考,软件项目计划包括两个任务:研究和估算。即通过研究确定该软件项目的主要功能、性能和系统界面。
3.2需求分析和定义
风险分析对于软件项目管理是决定性的,然而现在还是有很多软件开发者不考虑风险就着手进行,风险是软件开发不可忽视且长期潜在的不利因素,它能不同程度影响软件产品的质量。开发软件者在软件风险的目标还没有造成之前,要及时对软件进行识别和分析,进而减少或消除风险对软件带来的损害。
3.3软件设计
此步骤是软件开发的核心,是把需求变成实质需要的具体方案。首先先搭建一种概念设计,要注重项目计划的层次性。它是把许多事物和问题抽象起来,并且抽象它们不同的层次和角度。将问题或事物分解并模块化使得解决问题变得容易,通常分为总体设计和详细设计两个方面。总体设计是系统通过使得设计陈述逐渐接近源代码,从而导出软件的模块结构。而详细设计主要注重于把框架逐步求精细化为具体的数据结构和软件的算法表达,按照模块的设计准则把设计行为、数据、算法和程序设计通过现代程序的界面设计结合起来。
3.4程序编写
是让为解决某个问题而使用某种编写程序代码,并最终得到相应结果的过程,根据源程序清单写出的程序结构简单、直观、易理解。
3.5软件测试
软件测试时保证软件质量的重要手段。首先要阅读需求,理解需求,与客户、开发、架构多方交流,深入了解需求;其次,根据需求估算测试所需资源(人力、设备等)、所需时间、功能点划分、如何合理分配安排资源等;再次,根据测试用例的详细步骤,执行测试用例,通过不断测试、追踪,直到被测软件达到测试需求要求;最后,通过用户体验来完成软件的发布。
4.总结
软件系统作为计算机系统的核心,随着其运行环境的演变也经历了一系列的变革。在社会信息化不断发展的今天,软件作为一种特别的产品,具有很大的发展前景和目标市场,因为现如今各行各业都需要计算机技术,然而软件就是各类信息带到生产力中,很大程度上为用户带来了便捷,软件系统为了适应这样一种发展趋势,将会逐步呈现出柔性、多目标、连续反应式的网构软件系统的形态。因此,我们必须提高软件的质量,生产出适合用户需求的高质量软件,进一步促使软件生产产业向更高水准发展。 [科]
【参考文献】
[2]朱剑.软件工程系统的发展及其应用[J].商场现代化,(06).
篇7:闪电探测技术发展和资料应用
闪电探测技术发展和资料应用
文中综述了闪电探测技术和方法的发展状况,阐述了闪电监测资料在闪电预警预报、防护以及在灾害性天气监测等方面的应用,探讨了我国闪电探测站网建设的.技术和方法,以及利用闪电探测资料开展雷电预警预报的方法与途径.闪电探测技术对雷电研究和雷电防护技术的发展非常重要,特别是随着科学技术的发展,闪电探测技术得到了快速发展,这为雷电监测和预警提供了重要手段,对减少雷电灾害具有重要作用.
作 者:张义军 孟青 马明 董万胜 吕伟涛 Zhang Yijun Meng Qing Ma Ming Dong Wansheng Lü Weitao 作者单位:中国气象科学研究院雷电物理与防护工程实验室,北京100081 刊 名:应用气象学报 ISTIC PKU英文刊名:JOURNAL OF APPLIED METEOROLOGICAL SCIENCE 年,卷(期): 17(5) 分类号:P4 关键词:闪电定位 闪电监测网 闪电预警篇8:国外航空涡扇发动机涡轮叶片热障涂层技术发展
国外航空涡扇发动机涡轮叶片热障涂层技术发展
介绍了美国等国家开发的`航空发动机涡轮叶片热障涂层技术及其应用情况,并总结了该技术的发展动向,旨在为中国开展相关研究和应用工作提供参考和借鉴.
作 者:徐庆泽 梁春华 孙广华 王志宏 XU Qing-ze LIANG Chun-hua SUN Guang-hua WANG Zhi-hong 作者单位:沈阳发动机设计研究所,沈阳,110015 刊 名:航空发动机 英文刊名:AEROENGINE 年,卷(期): 34(3) 分类号:V2 关键词:涡扇发动机 涡轮叶片 热障涂层篇9:变频调速器在涂层机上的应用
变频调速器在涂层机上的应用
多单元织物涂层机的工艺流程为:织物进给à上胶à焙烘à1轧à刀涂à2轧à锡林à成品卷取,整机由5台电动机拖动。生产要求车速在0 ~ 30m/min范围内连续调节,各单元同步运行,并保持一定张力。该机各单元均为恒转矩负载,要求起动平稳、低速起动力矩较大。通过分析比较,确定各单元均采用FTY系列三相永磁同步电动机驱动,由一台变频器控制,以确保各单元齐速运行。为弥补各单元由于机械磨损而造成的累积线速度误差,则通过装于各电动机轴上的齿链式无级减速器作速度微调。1. 控制系统的组成
根据工艺要求,4个单元的驱动电机均选用3kW、380V;锡林的驱动电机选用7.5kW、380V。变频器选用三垦SAMCO - LF-37K型。
2. 控制系统的工作过程
(1) 工作单元的选择
根据生产品种和工艺条件的.不同,织物涂层时,有些单元不需运转,这可通过选择电路进行选择。选择只能在开车前进行,不允许在运行中投入和切换单元电动机,以防过压、过流保护动作,使变频器停止工作。开车前,继电器KM1的触点11-13为常闭状态,此时按SST1 ~ SST5中的任何一个起动按钮,就可使相应的接触器吸合,使预选的单元电动机投入。若投入有错,可按SSTP1,使电路复位,重新进行选择。当电动机起动后(K吸合后),KM1的触点11-13断开,11-33闭合,保证了在运行中任何单元电动机不能投入,也不能使选择电路复位进行单元切换。
(2) 起动过程
1 工作单元选好后,按下按钮SST6,接触器K吸合并自保,变频器电源接通。
1 按下按钮SST7,继电器KM1吸合并自保,使FR-COM1接通,调节电位器RP,变频器驱动各单元电机正转,外接频率计P,则显示频率,将频率调至工艺车速值,系统开始正常运行。
(3) 停车过程
1 正常停车:按下SSTP3(SSTP4),KM1失电,FR - COM1断开,系统按设定的减速时间降频停车。
1 自由停车:按下SST8(SST9),KM2得电吸合并自保,其触点43 - 45断开、MBS - COM1接通,变频器即停机,输出频率降为零,电机呈空转自由停车状态。
1 紧急停车:当任一电机过载,使其热继电器动作时,触点11-57接通,KM4吸合,ES - COM1接通,变频器则报警停机。
正常停车或自由停车后,再开车时,按下SST7,系统即按设定的升速时间升至工艺车速;紧急停车后,待事故处理完毕再开车时,应先按复位按钮SST10解除报警,再按SST7,系统亦将按设定的升速时间加速到工艺车速。
3. 变频器参数的设定
SAMCO - LF -37K变频器可供设定的参数有215个,根据工艺要求,只对其中的部分参数给于设定,其它参数可采用出厂时的设定值。我们只对下列参数进行设定。
(1) 运转指令选择 以外部信号控制运转。
(2) 频率指令选择 频率设定用电位器操作。
(3) 频率、电压和电流的设定 基准频率和最高频率均设定为50Hz,最高输出电压设定为400V,最大输出电流设定为额定电流的120% 。
(4) 加减速时间的设定 三相永磁电动机的起动
[1] [2]
篇10:刀具干切削技术的应用优势
干切削技术对传统生产方式一个重大创新,种崭新清洁制造技术,世界各国日益严厉环保法规,有利于加速干切削技术推广与应用;各种超硬、耐高温刀具材料及其涂层技术发展,为干切削技术创造了极为有利条件;最小量润滑装置有效应用各种心小孔孔加工标准刀具出现,使准干切削铝合金各种难加工材料孔加工获得了越来越多应用。它一种新兴绿色制造技术.对实施人类可持续发展战略有重要意义,新世纪前沿制造技术。
随着高速机床、加工中心及加工技术迅猛发展,切削速度和切削功率急剧提高,使得单位时间内的金属切除量大量增加,机床加工过程使用切削液用量越来越大,其流量有时高达80~100L/min。但在高速切削时切削液实际上很难到达切削区,切削液很难起到冷却作用。因此,高速切削技术的发展推动了干切削技术的研究。
另外,在某些特殊的加工应用中,例如医学植入领域中为髋部植入一个球形关节,切削液可能弄脏零件或产生污染,因此,切削液在特殊的加工领域中是绝对不允许使用的。
干切削加工技术是一种在加工过程中不用或微量使用切削液的加工技术,是一种对环境污染源头进行控制的清洁环保制造工艺。它作为一种新型的绿色制造技术,不仅环境污染小,而且可以省去与切削液有关的装置,简化生产系统,能大幅度降低产品的生产成本,通时形成的切屑干净清洁,便于回收处理。干切削已成为目前绿色制造工艺研究的一个热点,并已经在实际加工中得到了成功应用,
干切削对刀具必须要有严格的性能要求:瑞士著名FRAISA高速刀具品牌独特的刀具形状和针对性专业涂层,特别能满足干切削对刀具性能的要求,具备以下优点:
①具有优良的热硬性和耐磨性。
干切削是的切削温度通常比湿切削时的高得多,热硬性高的刀具材料才能有效地承受切削过程的高温,保持良好的耐磨性。刀具材质的硬度为工件材料的4倍以上。
②较低的摩擦系数。
降低刀具与切屑、刀具与工件表面之间的摩擦系数,在一定程度上可替代切削液的润滑作用,抑制切削温度上升。
③较高的高温韧性。
干切削时切削力比湿切削要大,并且干切削的切削条件差,因此刀具具有较高的高温韧性。
④较高的热化学稳定性。
在干切削的高温下,刀具仍然保持较高的化学稳定性,减小高温对化学反应的催化作用,从而延长刀具寿命。
⑤具有合理的刀具结构和几何角度。
合理的刀具结构和几何角度,不但可以降低切削力,抑制积屑瘤的产生,降低切削温度,而且还有断屑和控制切屑流向的功能。刀具形状保证了排屑顺畅,易于散热。
★ 模具制造论文
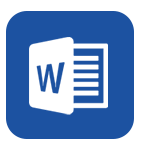
【浅谈刀具涂层技术发展及应用(整理10篇)】相关文章:
数控论文2024-04-20
数控论文参考文献2022-05-08
静电冷却干式切削技术2023-01-15
数控毕业论文2023-02-07
浅谈尾矿干堆技术2023-03-19
数控毕业论文范文2023-02-15
寒假机电专业大学生实习报告2023-11-29
连杆的加工工艺2023-05-25
机电专业实习总结2023-01-04
车工技师论文2023-07-29